OEM Aluminum Cold Forging, Hot Forging Manufacturer in China
One Stop service for die casting parts from aluminum, magnesium, zinc alloys…
Aluminum Forging Basics – Hot forging and Cold Forging
Aluminum and its alloys are among the most popular non-ferrous metals with the second place in the production after steel. Aluminum is the eighth most abundant element in the earth’s crust by weight and is more abundant than all other non-ferrous metals put together. It is only one third of that of steel (2. 7 g/cm³ for aluminum alloys and approximately 7. 85 g/cm³ for steel). This low density makes aluminum alloys ideal for lightweight applications, with good strength, stiffness and high fatigue life, which makes them ideal for load carrying members.
Aluminum alloys are highly ductile and thus suitable for intricate designs and close tolerance forgings. Aluminum forgings have better characteristics than steel forgings in terms of corrosion resistance, thermal conductivity, and non-magnetic properties. In many aspects, they are superior to steel forgings.
Aluminum forgings have many applications because of their characteristics; they are used in machinery, aviation, automobiles, railways, ships, construction, bridges, chemicals, and power plants. Aluminum can be substituted for steel forgings and this can decrease the weight of mechanical products by 60% while increasing the strength. This has made it to be widely used in aviation, aerospace, and defense industries due to its light weight and high strength. For example, structures of aircrafts contain aluminum forging in the range of 15% to 50%. This article will discuss the aluminum forging process and most commonly forging techniques for aluminum like hot, cold, and drop forging.
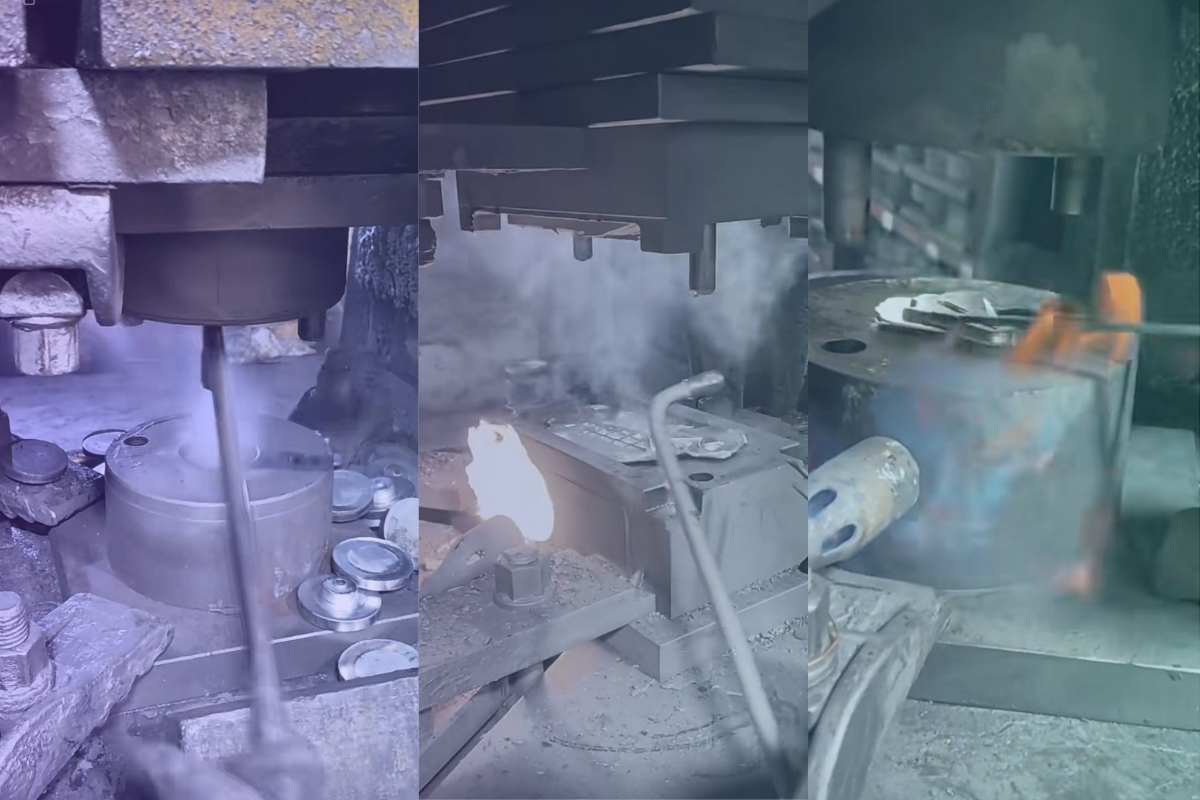
Forgeability Characteristics of Aluminum Metal
In the aspect of forgeability, aluminum alloys are almost the same as carbon steel and low-alloy structural steel.
Variation in Deformation Resistance at High Temperatures
Aluminum alloys exhibit a wide range of deformation resistance (or flow stress) depending on the type of alloy. Low to medium strength Al alloys in the 6000 series are more susceptible to deformation at elevated temperatures. On the other hand, high strength aluminum alloys especially the 7000 series aluminum such as Al-Zn-Mg-Cu alloys have been reported to offer higher resistance to deformation at high temperatures.
For instance, a hard aluminum alloy has a forging strength limit of 40 MPa at 500°C while the 6061 aluminum alloy has a forging strength limit of 20 MPa. This means that the forging deformation load for the latter is approximately half that of the former.
Resistance to Deformation at High and Room Temperatures
At room temperature, most deformation-resistant aluminum alloys offer less deformation resistance than carbon steel. But at high temperatures, their ability to resist deformation may be lower, similar or even better than that of carbon steel.
Sensitivity to Temperature
Aluminum alloys are very sensitive to temperature changes. This is because as the temperature decreases, their ability to resist deformation increases at a very high rate. This increase in hardness is more than that of carbon steel. For carbon steel and low-alloy structural steel, the strength limit is 1. 5 times higher if the temperature is reduced by 100°C. On the other hand, a 50°C temperature drop can lead to a 50% to 300% increase in the strength of aluminum alloys.
Forging Methods of Aluminum Parts
Aluminum is a soft, low-density alloy that is often used in combinations with other metals such as copper, magnesium, tin or zinc to enhance its formability, hardness and strengthening abilities. Aluminum alloys are easily forgeable, and as such, 85% of aluminum parts are forged.
Forged products are relatively stronger than cast aluminum products because they possess the features of two metals. Since aluminum has a low melting temperature and is less expensive than forged products. The most commonly used aluminum alloys for forging applications includes; Al 6061, 6063, 6082, and 7075. These alloys are used in engineering parts and systems where corrosion protection and low density are important. Forged aluminum parts find their extensive use in various industries such as shipbuilding, automotive interior, and exterior parts, engines, aerospace, and other manufacturing industrial products where ability to withstand harsh conditions like in marine ships plays an indispensable role. .
Aluminum Hot Forging
Aluminum hot forging of aluminum involves sawing and heating aluminum bars to high temperatures. This process, called recrystallization, refines the grain structure of the aluminum and improves the forged parts’ toughness, ductility, and yield strength. Hot forging is also highly efficient in its use of material since it generates little material scrap. Hot forging of aluminum parts can be done in our factory to meet the required designs and sizes of our clients.
Aluminum Cold Forging
Aluminum cold forging is particularly suitable for aluminum components because aluminum is highly ductile and easy to manipulate. This technique results in highly accurate parts that require little or no further machining and is best suited for making symmetrical products. Cold forging is more economical than hot forging in most cases. Cold forging process involves bending the bar stock into the required shape and then compressing it between a die to achieve the final shape. However, due to the relatively soft nature of aluminum, heat treatment is advised to increase the hardness of the forged parts. These characteristics make aluminum forgings essential in many industries and applications.
In this process, the upper part of the die is fixed to the hammer and the lower part of the die is fixed to the anvil. The heated aluminum workpiece is placed on the anvil within the lower half of the die. Subsequently, the workpiece is forced into the die cavity with a uniform force until it occupies the die cavity completely. At this stage, any excess aluminum is ejected through the openings between the two halves of the die. This excess material, called flash, is gathered, and then utilized in the production process again.
Aluminum Drop Forging
Drop forging is a method of forging that involves placing an aluminum workpiece between two halves of a die and using a hammer to shape the material, making it ideal for the large-scale production of aluminum parts. Aluminum alloys are preferred for drop forging because of their light weight, and the 6000 and 7000 series alloys are most suitable. After the workpiece is forged, any excess material which is called flash is trimmed off and the parts may be further processed.
Aluminum is known to be strengthened, toughened and have improved fatigue characteristics by the process of drop forging. This controlled deformation process makes it possible to achieve high accuracy and uniformity, which makes it a cheap and non-waste process that can be used to manufacture complex shapes.
The characteristics of aluminum alloy are as follows:
Metals such as aluminum have a characteristic known as plasticity, which is the ability of the material to deshaped under high external forces. Aluminum possesses the ability and to maintain its structural stability. The ductility of aluminum alloys defines their processability and the circumstances under which die forging can be carried out.
While aluminum alloys exhibit a flow rate of 50% that of steel, their friction coefficient on mold surfaces is three times as high. This leads to high bonding, low workability, and low ductility during forging operations.
How to Forge Aluminum: A Comprehensive Guide
Aluminum forging is a process of pressing the aluminum into various design configurations by using a forging press or hammer. This process helps replicate various prototype design patterns for industrial use such as defense, automobile, and aerospace.
Step 1: Preparation
First, the aluminum billet should be properly sourced, meaning that it should be pure, free from any impurities and in the right dimensions for the intended use.
Step 2: Heating
Heat the billet to the right temperature before the forging process. This step makes the aluminum more pliable than steel, thus easier to work on than steel. The temperature depends on the particular type of alloy and the shape of the final product that is to be produced. Typically, aluminum alloys are forged at temperatures ranging from 700 to 950 degrees F, but some alloys may require up to 1100 degrees F.
Step 3: Aluminum Forging
When the billet gets to the required temperature, it is ready for forging. In a forging shop, a large force is used to shape the aluminum through the use of a forging press or hammer. The forging process involves three main steps:The forging process involves three main steps:
- Upsetting: Exert pressure on one end of the billet to elongate it and make it thinner.
- Drawing Out: The billet is then stretched to the required length and shape of the bar.
- Finishing: It helps replicate the final shape and trim off the unnecessary material from the parts’ surface.
Step 4: Cooling
The forged aluminum is then cooled down at an ambient temperature gradually. Quenching at a high rate can lead to formation of cracks or distortion particularly in the large forgings
Step 5: Machining and Surface Finishing
This process involves using tools such as drills or cutting tools to shape the forged parts into the desired final form and size. The final step of the process is to polish or coat the material to improve its surface finish and to ensure that it will not corrode easily in the future.
Aluminum forging is a common process that involves shaping metals through the application of force, and it is used to produce a wide range of products, from small parts to large structures.
Useful Tips For Aluminum Forging
Consider the following tips to ensure successful aluminum forging:
- Select the Correct Aluminum Alloy: Select the appropriate alloy for your product since different alloys have different forging temperatures and properties.
- Manage the Temperature: Ensure that the aluminum billet is within the appropriate temperature for the particular alloy by observing it frequently.
- Use the Right Equipment: Use a forging press or a hammer with the right tonnage and stroke for the job that needs to be done.
- Collaborate with Skilled Aluminum Forging Companies: For those who are new to aluminum forging, it is advisable to approach a company that has been in the business for some time, such as Sincere Tech. They can help you choose the right alloy, temperature, and equipment, as well as provide guidance throughout the forging process.
Benefits of Forged Aluminum Parts
Forged aluminum parts offer numerous benefits, including:Forged aluminum parts offer numerous benefits, including:
Strength
Aluminum forging creates parts that are more robust than those that are created through casting and machining. The grain flow in the material conforms to the shape of the component during forging which increases the strength of the material and thus the life of the component. Forged aluminum is also preferred in applications where the components are subjected to repeated impact loads, cyclic loading, and other stressful conditions.
Cost
Aluminum forging is generally more economical in terms of lead time, material cost and other manufacturing considerations. Compared to aluminum die casting, forging is relatively cheaper in terms of tooling and has a higher production rate.
Mechanical Characteristics
Metal forming changes the microstructure of aluminum alloys in a positive way, improving their mechanical characteristics. This process enhances tensile strength, yield strength, toughness, and fatigue properties.
Durability and Reliability
Other aluminum forming techniques may produce parts that have porosity and voids in them, which may compromise performance. These problems are solved in forging since it involves application of compressive forces which improves the performance, strength and reliability of the forged products.
Dimensional Precision
Aluminum is a shrinkage free alloy in forging since it is heated to its recrystallization temperature, whether slightly below or above. The aluminum billets are processed in solid forms, thereby, the final products possess a high degree of accuracy in terms of dimension.
Property Retention
The forging process does not in any way alter the excellent characteristics of aluminum. The metal is bent, twisted and deformed and none of the positive attributes of the metal are affected.
Material Waste Reduction
Today’s manufacturing sector mainly focuses on minimizing waste to save costs, and innovations are being made to go with techniques with no negative impacts on the environment. During aluminum forging, the flash happens during open and closed die forging ,and that can be easily utilized and recycled after the cycle completion. Therefore the waste material generation is quite low, you can say negligible. Aluminum is among the most recycled metals in the world and this property makes it ideal for applications requiring sustainable parts or products which can adorn harsh environments. .
High Volume Production
Aluminum forging is a fastidious approach of metalworking that can create 1000s of intricate detailed feature components in minimal time leads. The process usually takes less time from transforming design to completion of the product can be as little as two months. Aluminum forging is a process that produces a large amount of aluminum products, but it has minimal scrap production.
Key Takeaways
Aluminum forging has become an adaptable, and one of the most effective and widely used methods of manufacturing in different industries. Adherence to the steps and tips provided in this guide will result in successful aluminum forging and the production of quality products that meet the customers’ requirements. It’s recommended to choose the right aluminum alloy, controlling temperature, using proper tools, and working with an experienced forging firm. It is therefore possible to manufacture aluminum products that meet the highest quality and performance standards by using the right preheating, forging, cooling and finishing methods.
Products Gallery
LED Lamp Heat Sink Components, Marine Components, Architectural Hardware Components, auto components, Mechanical Engineering Components, Automobile Parts, LED lighting enclosure & parts, window and door Hardware, Sports Equipment Components, Automotive Components, Electric Tool Parts.
About Us
Established in 1999, GC Precision Mold Co. ltd (Was Aluminium die casting manufacturer (China) Limited ), is now becoming one of the leading global suppliers of high quality die casting parts and machining of nonferrous metal products.
Our production line include but not limited to aluminium die casting, zinc die casting, bronze sand casting, aluminum gravity casting, CNC precision machining. our products were recognized and certified by ISO 9001, we always ready to be your trusted partner and supplier in China.