Los remaches son fijaciones mecánicas permanentes. Se utilizan para unir dos o más materiales. Hay tres tipos más comunes de remaches: remaches macizos, remaches ciegos (como los remaches pop) y remaches semitubulares.
Principales conclusiones del artículo:
- Definición de remache
- Tipos de remaches
- Aplicaciones de los remaches
- Técnicas de instalación de remaches
- Comparación del remachado con otros métodos de fijación
¿Qué es un remache?
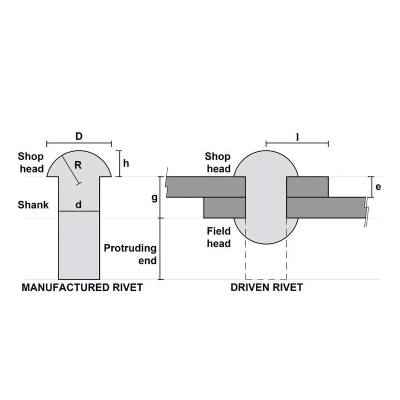
Remaches son las fijaciones semipermanentes. Se utilizan para unir las distintas partes de las aplicaciones. Consiste en una forma cilíndrica con una cabeza en un extremo y una cola en el extremo opuesto.
Antes de su instalación, la parte de la cola de los remaches se introduce en la herramienta. A continuación, se somete al proceso de aplicación de fuerza de compresión. Esta fuerza deforma los remaches en una forma plana, uniendo una parte con la otra.
Estas fijaciones mecánicas se suelen fabricar con acero dulce, latón, cobre y aluminio. Los fabricantes utilizan remaches para diversos proyectos y la fabricación de piezas industriales. Por ejemplo, puentes, operaciones de chapa metálica, armazones estructurales, barcos y sectores aeroespaciales.
Tipos de remaches
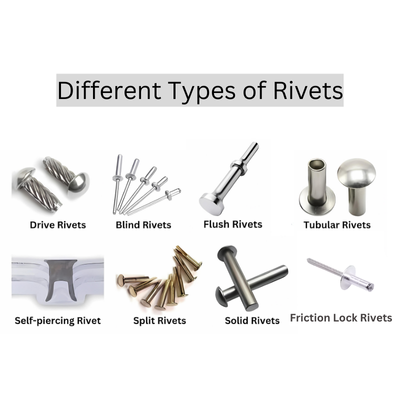
Los remaches están disponibles en varias formas y tipos con diferentes usos. Pero intentaremos hablar de los tipos específicos que se suelen utilizar en todo tipo de trabajos, desde piezas ligeras hasta piezas de alto rendimiento. Vamos a descubrirlos:
- Remaches macizos
- Remaches ciegos
- Remaches de arrastre
- Remaches enrasados
- Remaches autoperforantes
- Remaches partidos
- Remaches tubulares
- Remaches de fricción
Remaches macizos
Los remaches macizos son los métodos clásicos para unir el material. Estos elementos de fijación tienen forma redonda, también conocidos como remaches redondos. La deformación de la cola puede hacerse mediante herramientas de martilleo o engarce. Estos remaches unen las piezas a prueba de manipulaciones y vibraciones.
Los metales acero, aluminio y cobre son materiales adecuados para la construcción de remaches macizos. Estos tipos de elementos de fijación se utilizan en aplicaciones de aeronáutica, aeroespacial, construcción, productos domésticos, electrónica, etc.
Remaches ciegos
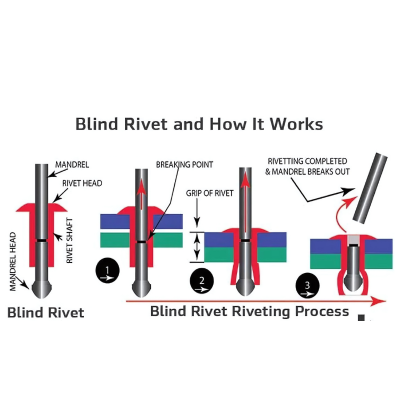
Los remaches ciegos tienen fama de remaches pop, construidos con formas cilíndricas con una cabeza y un vástago que discurren por el centro. Son como remaches tubulares que pueden instalarse en piezas con orificios taladrados.
Se eligen remachadoras y herramientas únicas para colocar los remaches en las piezas de trabajo. La fuerza se aplica para empujar el vástago a través del remache. De esta forma, la fuerza expande el tubo entre la herramienta y la pieza del vástago para bloquear la chapa.
Los remaches ciegos son inaccesibles y se utilizan para unir un lado de las piezas. Poseen una gran resistencia al cizallamiento y a la tracción. Las aplicaciones habituales de estos remaches son la construcción naval, la electrónica, la industria militar, la aeroespacial y el hogar.
Remaches de arrastre
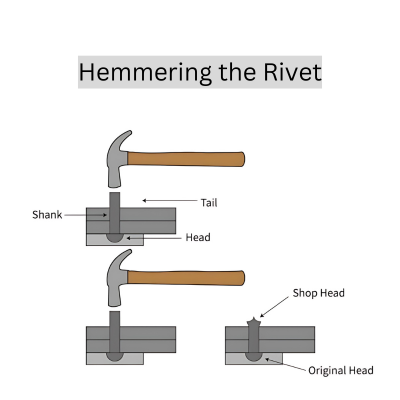
Los remaches de arrastre son similares a los remaches ciegos. Se construyen con un vástago corto que atraviesa el centro de los remaches. Los fabricantes pueden fijar los remaches de arrastre utilizando un martillo o una herramienta de bloqueo de respaldo.
Estos remaches pueden utilizarse para fijar aplicaciones de componentes de automoción, paneles arquitectónicos y trabajos de albañilería. No perforan los orificios de bloques, paneles o chapas durante el proceso de fijación.
Remaches enrasados
Los remaches enrasados están diseñados con cabezas que quedan a ras de las superficies metálicas que se van a fijar. También se conocen como remaches avellanados. Eso minimiza los arrastres aerodinámicos y mantiene las superficies lisas.
Los fabricantes utilizan remaches enrasados para aplicaciones en las que la apariencia es una preocupación. Estos ejes se utilizan habitualmente para fabricar piezas externas de aeronaves y otras aplicaciones industriales, como la automoción y la marina.
Remaches autoperforantes
Los remaches autoperforantes se construyen con extremos de perforación biselados o puntas biseladas. Estas categorías de remaches pueden montarse en piezas sin taladrar ni perforar la superficie.
Los fabricantes colocan ambos componentes en la prensa. Introducen remaches autoperforantes en el soporte de la pieza en bruto. A continuación, este soporte exhibe la fuerza presionando los remaches en la cara superior de la pieza.
Los operarios dejan de perforar el remache hasta que su mitad se incrusta en la segunda parte. Es el procedimiento más rápido para dar uniones estancas o con juntas de gas utilizadas en el sector aeroespacial.
Remaches partidos
Los remaches partidos o bifurcados se fabrican dividiendo el eje o sus extremos opuestos en dos patas separadas. Las piezas con orificios pretaladrados se combinan mediante remaches partidos. Se utiliza un martillo para aplanar las patas partidas de los remaches.
Con estos remaches se pueden unir materiales blandos y ligeros, como plástico, textiles y chapas finas. Sin embargo, no son una buena opción para sujetar artículos de grandes prestaciones.
Remaches tubulares
Los remaches tubulares son básicamente elementos de fijación en forma de tubo. Estos vástagos constan de una cabeza en un extremo, un vástago y un tubo parcialmente hueco en el lado opuesto.
Los remaches tubulares no necesitan una gran fuerza de compresión para deformarse, a diferencia de los macizos. Puede unir cualquier pieza mediante la tecnología de conformado en frío, en la que las paredes del orificio se aplanan hacia fuera para unir las piezas.
Este remache es la opción preferida entre las aplicaciones comerciales de dispositivos eléctricos, conductos de climatización y otras piezas de bajo riesgo.
Remaches de fricción
Los remaches de cierre por fricción son los tipos de remaches ciegos que se fabrican en forma de cúpula o avellanados. Estos remaches también se denominan remaches autoobturadores. Son como pernos que utilizan la presión interna del vástago para expandir el eje. Los vástagos de este remache se encajan en la superficie inferior de las piezas debido a la presencia de altas tensiones. Los fabricantes utilizan remaches de bloqueo por fricción para reparar aplicaciones aeronáuticas como las luces.
Aplicaciones de remaches
A lo largo del tiempo, las industrias han aprovechado las fijaciones por remache para fabricar sus múltiples componentes con uniones resistentes. Al asegurar las piezas múltiples, los remaches eliminan los movimientos internos y las vibraciones.
Aplicaciones específicas del sector
- Aplicaciones aeroespaciales
- Automoción
- Sectores de la construcción.
Aplicaciones aeroespaciales
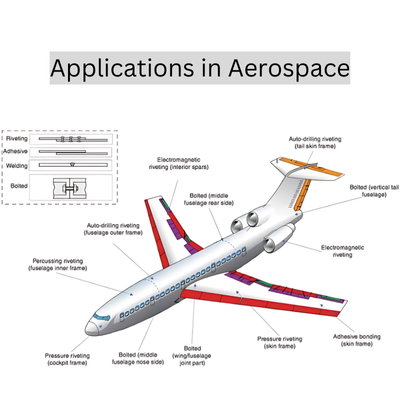
En general, en las aplicaciones aeroespaciales se utilizan materiales fuertes y resistentes a la corrosión, como el aluminio, el cobre y el acero. Los ingenieros ensamblan las piezas de los aviones aplicando remaches. Estos remaches suelen estar fabricados con materiales compuestos de aluminio, lo que permite que las piezas no estructurales sean ligeras. Alinean y forman múltiples piezas, entre ellas:
- Marcos del fuselaje
- marco de la piel de la cola
- Puertas y escotillas
- Largueros interiores
- armazón de la cabina
- Fijaciones del tren de aterrizaje
- Góndolas y soportes de motor
- Estructuras de ala
Automoción
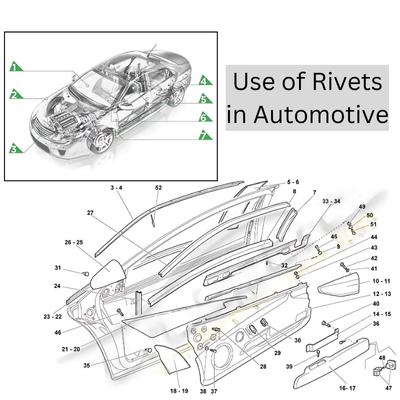
Los remaches de bajo peso fabricados con aleación de aluminio son la opción preferida de los ingenieros para aligerar el peso de las piezas de automoción. Los diversos usos de los remaches incluyen la deformación para unir las piezas de aluminio, acero y cobre. Estas son las partes de los vehículos donde se aplican los remaches:
- Paneles de carrocería
- Chasis y bastidor
- Carcasas para baterías
- Piezas de suspensión
- Estructura de choque, zonas deformables
- Puertas y ventanas
- Sistemas de escape
Sector de la construcción
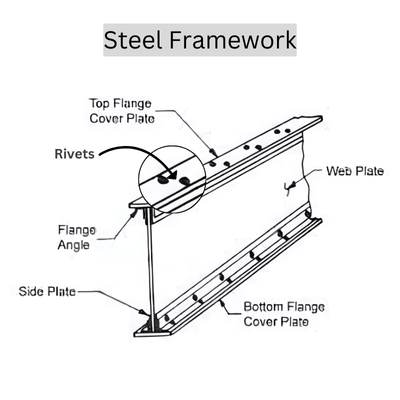
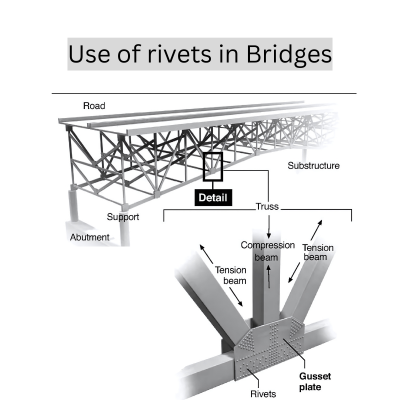
La unión de piezas estructurales y no estructurales puede realizarse con remaches. Proporcionan una gran eficacia para aplicaciones de construcción. La fijación mediante remaches es el paso más sencillo para unir varios componentes. puede aprovecharlo para fabricar las siguientes piezas:
- Estructura y vigas de acero
- Puentes
- Cubiertas metálicas
- Sistemas de fachadas y revestimientos
- Ventanas y muros cortina
- Pasamanos y barandillas
- Escaleras y salidas de incendios
El proceso de remachado
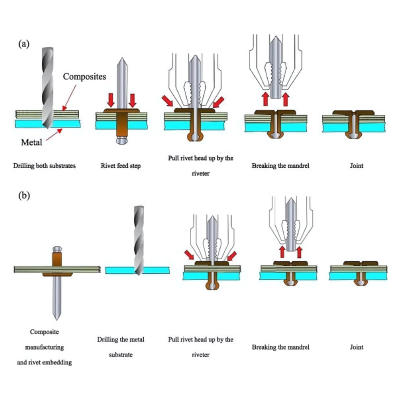
Técnicas de instalación de remaches
Intente siempre seguir cada paso sin saltárselo para conseguir unas uniones duraderas y seguras de las piezas con remaches. Estos pasos pueden incluir:
- Herramientas
- Proceso de instalación paso a paso
Herramientas
- Pistolas remachadoras
- Barras
- Taladros y abrazaderas
Proceso de instalación paso a paso
- Preparación
- Colocación de remaches
- Remachando
- Inspección de calidad
Preparación
Limpie la superficie de las piezas que vayan a ensamblarse mediante remachado. Utilice una mezcla de agua y detergente para eliminar las marcas y manchas pegajosas del metal.
Adelante, marque el metal con los puntos correctos y una dimensión ligeramente mayor que la de los remaches. Para que pueda hacer los agujeros a través de la perforación.
Colocación de remaches
Dé forma a las cabezas de los remaches utilizando barras de remachado. A continuación, coja la pistola remachadora para iniciar el proceso de remachado. Coloque el extremo opuesto del remache en las ranuras de la pistola. Puede ajustar el tamaño de los pernos de la pistola para que coincidan con el tamaño de los remaches.
Remachando
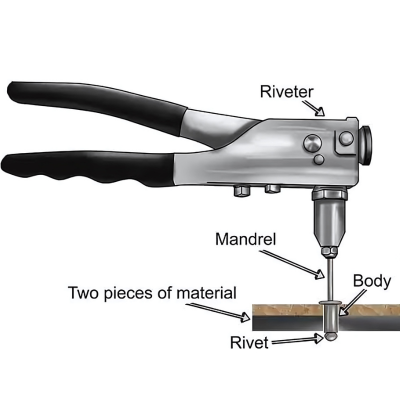
Coloque ambas piezas de fijación juntas, equivalentes a los orificios taladrados. A continuación, coja la pistola remachadora con los remaches insertados para colocarlos en la superficie del orificio. Presione la pistola manualmente para tirar de la cola contra la cabeza del remache hasta que se aplane y la cola se rompa.
Inspección de calidad
Inspeccione las piezas minuciosamente para identificar cualquier grieta o rotura, asegurando el acabado enrasado. Estos pasos adicionales pueden asegurar la garantía de calidad contra fallos estructurales. Esto es necesario por motivos de seguridad.
Métodos de inspección
- Inspecciones visuales
- Pruebas ultrasónicas
- Pruebas de cizallamiento
Inspecciones visuales
El equipo de gestión de la calidad debe examinar a fondo cada pieza. Pueden comprobar los fallos de cabezas de remache agrietadas, mala alineación o daños superficiales sin utilizar ninguna herramienta específica.
Pruebas ultrasónicas
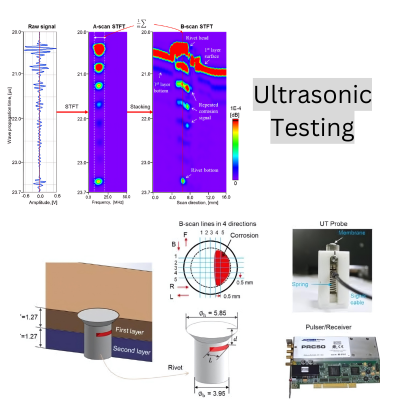
Utilice herramientas ultrasónicas para inspeccionar piezas complejas y detalladas. La técnica de ensayo no destructiva identificará el falso remachado, exhibiendo los rayos a través de los metales unidos.
Pruebas de cizallamiento
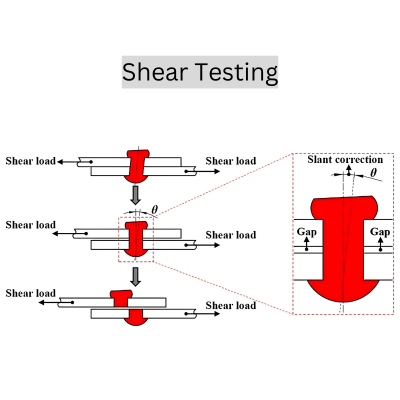
Compruebe la resistencia de las piezas fijadas aplicando la fuerza de cizallamiento. Así se asegurará de que las piezas sujetas soportan o no las presiones de funcionamiento.
Análisis comparativo del remachado frente a otros métodos de fijación
Aspecto | Remachando | Soldadura | Adhesión adhesiva | Pernos |
Método | Fijación mecánica mediante remaches | Proceso de fusión de metales | Unión química con adhesivos | Insertado y apretado con herramientas |
Uso principal | Permanente, para estructuras metálicas, aviones, puentes | Permanente, para juntas estructurales y de alta resistencia | Semipermanente, utilizado para materiales mixtos | Juntas metálicas estructurales y desmontables |
Materiales | Metales, materiales compuestos | Metales (por ejemplo, acero, aluminio) | Metales, plásticos, materiales compuestos | Metales o materiales similares |
Características de resistencia | Buena resistencia al cizallamiento, moderada resistencia a la tracción | Alta resistencia a la tracción y al cizallamiento | Resistencia moderada; buena para no soportar cargas | Alta resistencia a la tracción y al cizallamiento |
Implicación del calor | No requiere calor | Requiere mucho calor para fundirse | Sin calor, curado por tiempo, presión o UV | No requiere calor |
Proceso de instalación | Insertar el remache, utilizar la pistola remachadora/barra de remachar para formar la cabeza | Alinear materiales, soldar bordes con alto calor | Aplicar el adhesivo, presionar las superficies y curar | Inserte el perno, apriételo con una llave u otras herramientas |
Proceso de retirada | Taladre o corte el remache para retirarlo | Requiere corte o esmerilado | Disolvente o calor para debilitar la unión, despegar | Desatornillado con herramientas (llave inglesa, carraca, etc.) |
Requisitos de inspección | Pruebas visuales, ultrasónicas o de cizallamiento | Visual y END (ultrasónico, radiográfico) | Pruebas visuales, a veces de tracción | Inspección visual, prueba de par |
Ventajas | Gran durabilidad, sin distorsión por calor | Junta continua muy resistente | Adecuado para una gran variedad de materiales, unión flexible | Fácil de instalar y desmontar, permite el desmontaje |
Desventajas | Lleva tiempo, requiere una alineación precisa | Potencial de distorsión por calor, irreversible | Sensible al medio ambiente (por ejemplo, humedad) | Propenso a aflojarse con las vibraciones, es necesario reapretarlo |
Comparación de costes de remachado, soldadura, unión adhesiva y atornillado
Método de unión | Coste aproximado por junta |
Remachando | $0.10 – $1.00 |
Soldadura | $0.50 – $5.00 |
Adhesión adhesiva | $0.25 – $2.00 |
Atornillado | $0.20 – $1.50 |
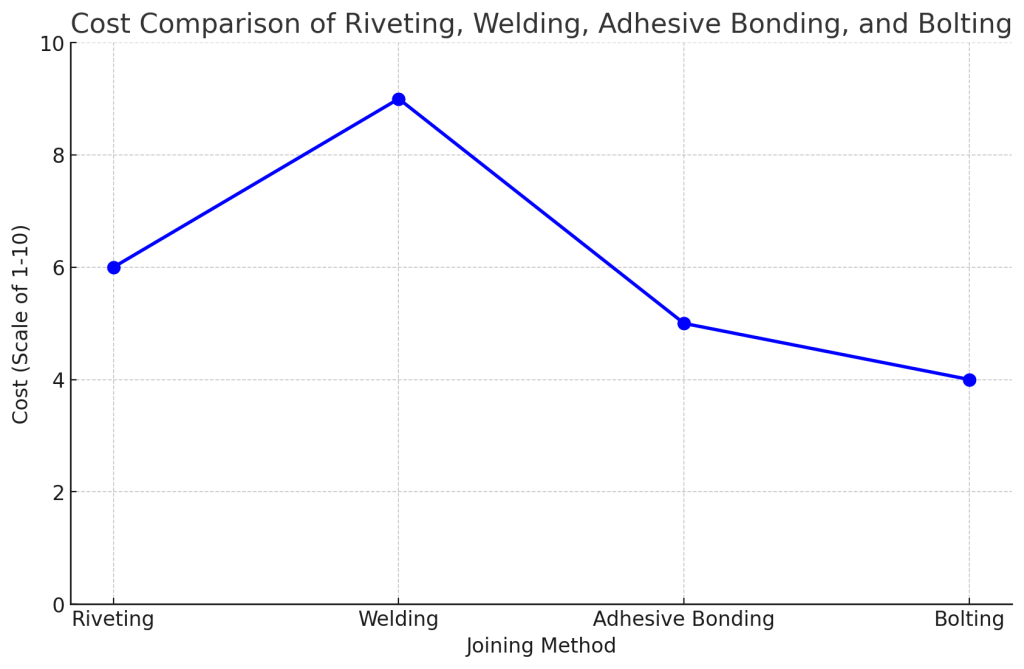
Este gráfico de líneas muestra la fluctuación de precios de los métodos de remachado, soldadura, unión adhesiva y atornillado en una escala del 1 al 10. La fijación por soldadura es el método más caro. Implica una preparación específica, gastos de herramientas y costes de mano de obra. En cambio, el atornillado es una opción económica para todo tipo de sectores. Los precios del remachado y la unión adhesiva indican costes moderados intermedios.
Tecnologías innovadoras de remachado
Avances en las tecnologías de remachado
Sistemas de remachado robotizados y automatizados
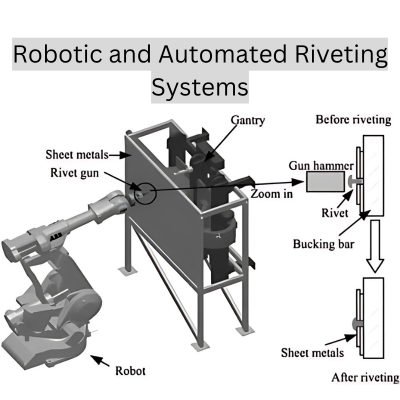
Las técnicas de remachado se han mejorado con la introducción de brazos robóticos y máquinas CNC (control numérico por ordenador). Estas herramientas proporcionan una colocación precisa y exacta con una presión constante en cada remache deformado.
Calculadoras de remaches
Las calculadoras de remaches facilitan la fijación de las distintas piezas. Estas herramientas de medición tienen en cuenta el tamaño exacto, el material de construcción o los valores de espacio. Además, racionalizan las presiones de carga precisas, los grosores y la resistencia de los remaches. La calculadora de remaches permite optimizar las opciones de durabilidad y seguridad.
Impacto en la eficiencia y la calidad:
Los avances en los procesos de fabricación y remachado aportan factores de garantía de calidad. Disminuyen el tiempo de operación y producen piezas de gran calidad. El uso de un brazo robotizado y calculadoras evita problemas de fatiga del metal y permite una producción rápida con precisión.
Conclusión:
Los remaches son las mejores fijaciones que no son más caras que la soldadura. Proporcionan uniones duraderas con acabados suficientes. Estos remaches pueden estar hechos de diversos materiales como acero, aluminio o cobre. Además, los remaches son de múltiples tipos, con su uso específico para aplicaciones. Siguiendo los pasos esenciales de la técnica de remachado y adaptando los sistemas modernos se consigue el resultado deseado.
0 Comentarios