Moulage sous pression est similaire au vol d'un bourdon ; les deux sont théoriquement impossibles. Cependant, plus de 150 ans de fonctionnement efficace, avec une productivité et une qualité des composants en constante augmentation, ont démontré que le moulage sous pression est intrinsèquement robuste et capable d'atteindre des niveaux élevés de capacité de traitement. Même dans les ateliers les mieux gérés, il y a des rebuts, et nous discutons ci-dessous du diagnostic, des causes et du traitement des défauts qui peuvent survenir dans les pièces moulées sous pression en zinc, tous ces problèmes étant les mêmes pour les pièces moulées sous pression en aluminium et en magnésium.
Il existe plusieurs façons d'organiser les défauts afin de fournir un traitement cohérent du sujet. Dans cet article, nous adopterons une approche progressive, de la réception du lingot d'alliage à l'expédition du produit fini, et nous présenterons des informations sur chaque type de défaut au moment où il se produit. D'autres méthodes d'identification des défauts et divers systèmes de recherche de défauts seront abordés ultérieurement. Les étapes du processus sont énumérées ci-dessous :
En outre, les pièces de coulées et les déchets seront recyclés à différentes phases, et il faut tenir compte du stockage et de la manipulation entre les processus. Toutes les pièces moulées ne passeront pas par toutes les procédures.
Lingots d'alliage de zinc Spécifications :
Les compositions des alliages de fonderie de zinc ont été développées méthodiquement sur une période de 75 ans. Les gammes d'éléments d'alliage ont été ajustées et les maxima pour les contaminants dangereux ont été soigneusement déterminés. Pour produire des pièces coulées fiables, il faut utiliser des lingots qui répondent aux exigences internationalement reconnues. En outre, la qualité de l'alliage doit être maintenue pendant les opérations de fusion et de coulée afin de garantir que les composants coulés répondent aux critères de composition de la coulée.
Les différences mineures entre les normes pour les lingots (tableau 1) et les normes pour les pièces coulées (tableau 2) pour chaque type d'alliage sont destinées à tenir compte des variations causées par les processus réguliers de traitement et de recyclage. L'utilisation de lingots non conformes, en particulier ceux qui sont chargés d'impuretés hautement toxiques comme le plomb, l'étain ou le cadmium, n'est jamais justifiable.
Les alliages sont répartis en trois familles : les alliages d'aluminium 4% (Zamak 3 et 5, ainsi que nos 2 et 7), les alliages ZA à plus forte teneur en aluminium (nos 8, 12 et 27) et les alliages de cuivre (A cu zinc 5 et 10).
En outre, certains autres alliages n'ont pas été acceptés commercialement. Presque toutes les pièces moulées en alliage de zinc sont fabriquées en Zamak No3 ou No5, les autres alliages n'étant spécifiés que lorsque des qualités particulières sont requises.
Effet de la contamination
Les effets des éléments contaminants, tels que le plomb sur les pièces coulées, sont comparables dans tous les alliages. Les maxima d'impuretés spécifiques indiqués reflètent la gravité variable de l'effet ainsi que la facilité avec laquelle les lingots peuvent être fabriqués avec de faibles niveaux d'éléments à l'état de traces.
Plomb, étain et cadmium
Ces éléments, ainsi que l'indium et le thallium, comparables mais moins courants, peuvent provoquer une défaillance catastrophique par corrosion intergranulaire. Les impuretés s'accumulent aux joints de grains, facilitant la corrosion intergranulaire, en particulier dans les environnements chauds et humides. Les pièces coulées gonflent et se désagrègent, laissant apparaître des monticules de poudre grise (figure 1).
Si les niveaux de magnésium sont maintenus au-dessus des minima, l'effet est insignifiant dans les pièces coulées contenant jusqu'aux maxima prescrits de ces polluants. Les méthodes préventives comprennent l'achat de lingots appropriés et un bon entretien pour éviter la contamination par la refonte ou l'environnement de l'atelier, comme la soudure.
Le fer
Le fer n'est que faiblement soluble dans le zinc, et l'excès de fer se combine avec l'aluminium dans l'alliage pour générer un complexe intermétallique, l'aluminure de fer (FeAl3). Ce composé est extrêmement dur et, s'il pénètre dans la pièce moulée, il peut créer des problèmes d'usinage, une usure excessive des outils et des problèmes de polissage, car des particules se détachent ou se détachent. Des quantités excessives peuvent limiter la fluidité de l'alliage et donc sa capacité à remplir les moules. Enfin, si elles sont concentrées dans des endroits soumis à des contraintes, la résistance et la ductilité peuvent diminuer. Il est prouvé que c'est la taille des particules, plutôt que la quantité totale présente, qui détermine l'usinabilité, car le fer provient du pot de fusion. La protection essentielle consiste à maintenir les températures du métal sous contrôle.
Nickel, chrome, manganèse et silicium
Des niveaux excessifs de ces composants ont le même effet sur le moulage qu'une quantité supplémentaire de fer. Il convient de noter que le nickel n'est pas un contaminant de l'alliage n° 7 ; la faible quantité indiquée (inférieure à la limite de solubilité) est un ajout intentionnel destiné à réduire la corrosion intergranulaire dans cet alliage sans magnésium et à haute fluidité.
Effet des éléments d'alliage
Aluminium
À l'exception des alliages d'acuzinc, l'aluminium est l'élément d'alliage le plus courant. La résistance et la coulabilité des alliages dépendent de la conformité de leur teneur aux spécifications. Les propriétés peuvent changer rapidement en dehors des plages très limitées indiquées, en particulier pour les alliages de zinc 2, 3, 5 et 7.
L'excès d'aluminium dans ces alliages 4%Al réduit considérablement la résistance aux chocs (figure 2), c'est pourquoi aucun aluminium ne doit être récupéré pendant le traitement. Si le niveau d'aluminium tombe en dessous du minimum prescrit, les effets sont moins visibles. Les conséquences possibles sont une tendance à la déchirure à chaud, qui réduit la résistance, une diminution de la fluidité et une tendance accrue de l'alliage à s'accrocher à la matrice (soudure).
Les variations de la teneur en aluminium ont un effet moins perceptible sur les caractéristiques des alliages ZA à forte teneur en aluminium, ce qui permet d'élargir les fourchettes autorisées. Cependant, comme pour les alliages 4%, les compositions ont été optimisées pour fournir une combinaison optimale de caractéristiques, et le dépassement des limites entraînera des modifications qui peuvent être délétères.
Magnésium
Bien que l'ajout de magnésium ait un effet renforçant, son but premier est de prévenir la corrosion inter-granulaire dans les alliages contenant du plomb, de l'étain et d'autres métaux à des niveaux allant jusqu'au maximum autorisé. Les pièces coulées contenant moins de magnésium que le minimum autorisé peuvent se corroder en service. Une teneur en magnésium supérieure à la fourchette autorisée peut provoquer une déchirure à chaud, entraînant une perte de résistance ou des difficultés de revêtement. Une teneur élevée en magnésium réduit la fluidité de l'alliage, ce qui peut entraîner des problèmes de remplissage.
Cuivre
L'ajout de cuivre à l'alliage de base 4%Al augmente la résistance et la dureté au détriment de la ductilité et entraîne un changement de dimension plus important des alliages au cours du vieillissement. La résistance à l'impact des alliages à forte teneur en cuivre diminue également avec le vieillissement. Par conséquent, les alliages qui n'entrent pas dans les limites applicables au cuivre auront des qualités intermédiaires à celles des alliages spécifiés.
La teneur en cuivre des alliages ZA a un impact significatif sur leurs propriétés mécaniques. En général, une forte teneur en cuivre réduit la ductilité, tandis qu'une faible teneur en cuivre réduit la résistance à la traction.
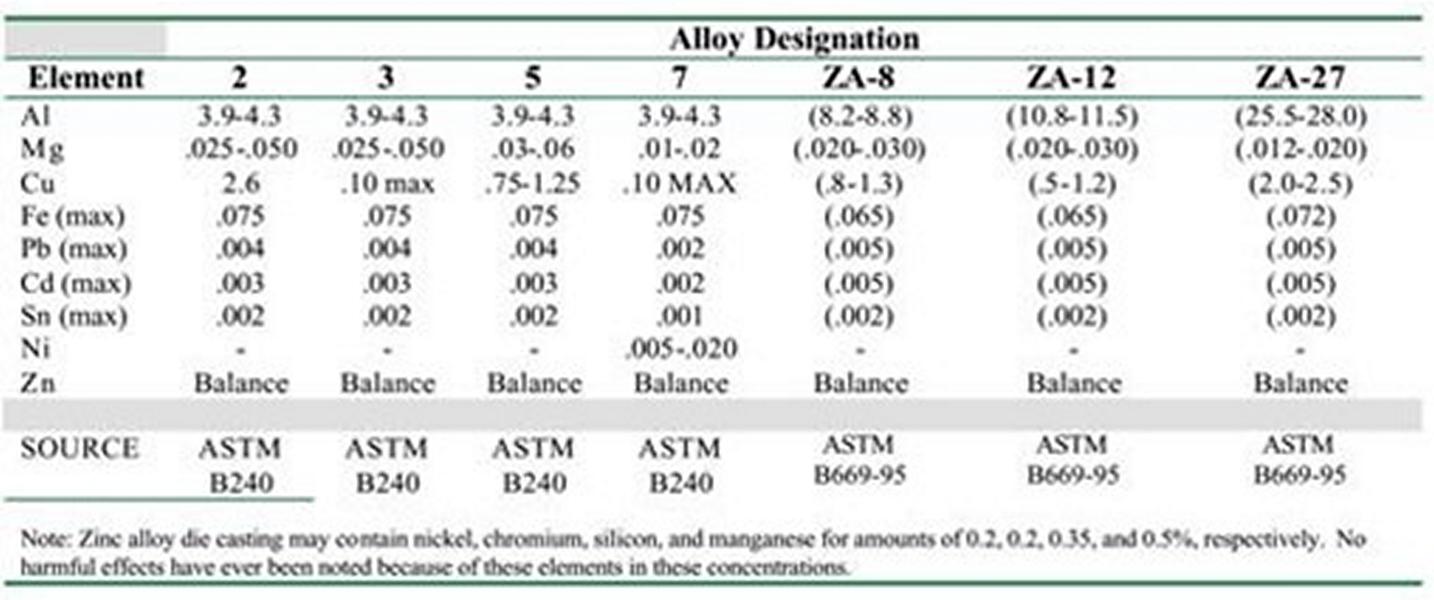
Tableau 1. GOMPOSITION DES ALLIAGES DE COUVERTURE SOUS PRESSION AU ZINC LIMITES DE L'INGOT, EN POIDS.
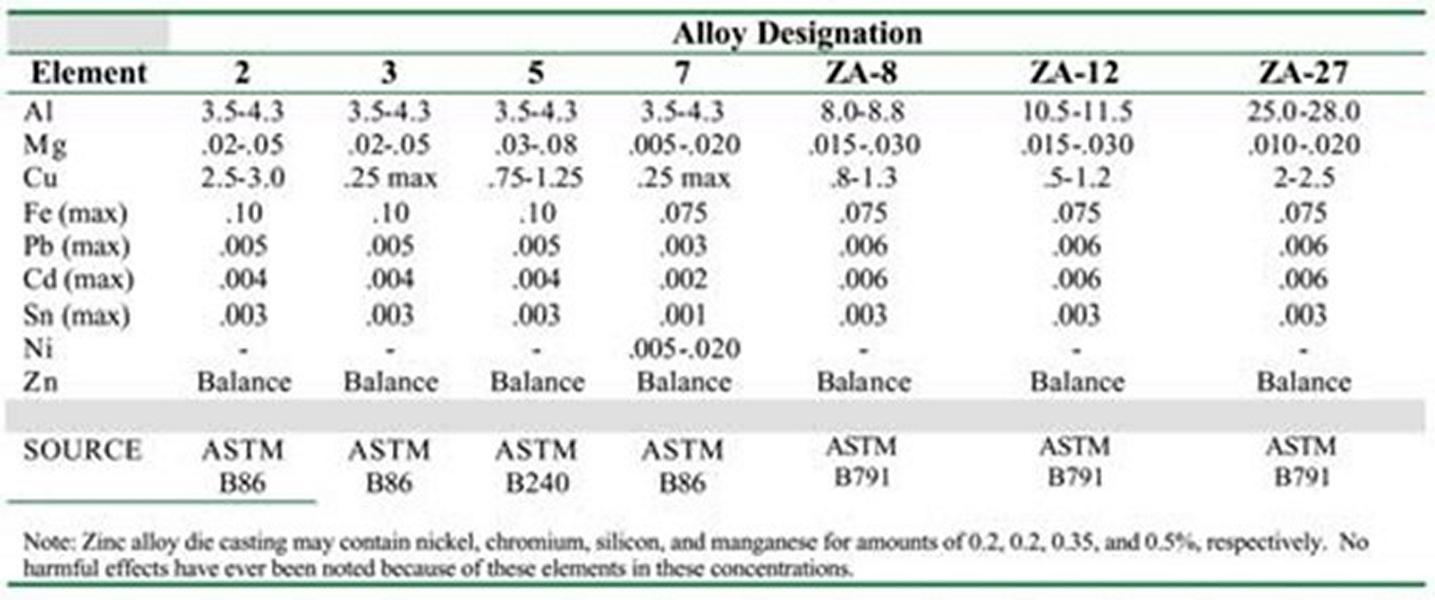
Tableau 2. GOMPOSITION DES ALLIAGES DE COUVERTURE SOUS PRESSION AU ZINC LIMITES DE COUVERTURE, PAR POIDS
Le cuivre est le principal élément d'alliage des alliages d'Acuzinc, ce qui leur confère une plus grande dureté et une plus grande résistance à haute température que les autres alliages à base de zinc. Les teneurs relatives en cuivre et en aluminium des alliages d'Acuzinc ont été optimisées pour équilibrer les caractéristiques et la coulabilité. Comme la teneur élevée en cuivre se produit dans un système de phases distinct, son effet sur le changement de vieillissement dimensionnel peut différer de celui rapporté dans les alliages 4%Al.
Fusion, transfert et maintien des métaux
À l'exception des alliages ZA-12, ZA-27 et Acuzinc10, qui attaquent le fer et l'acier à une vitesse inacceptable, les alliages de zinc peuvent être fondus et stockés dans des conteneurs métalliques. Cette caractéristique leur permet d'être coulés par le procédé de la chambre chaude, qui utilise un système d'injection immergé.
Toutefois, cette caractéristique précieuse n'est possible que grâce à un contrôle strict de la température. En dessous d'environ 450°C, l'alliage de zinc dissout le fer à un rythme suffisamment lent pour permettre l'utilisation de pièces métalliques en contact avec l'alliage. Le taux de réaction augmentant de manière exponentielle avec la température, il est sensible à de légères fluctuations de température.
La réaction se produit entre l'aluminium de l'alliage et le fer du creuset et des pièces de la machine.
Aluminium + Fer > Particules intermétalliques
3Al + Fe > FeAl3
L'intermétallique d'aluminure de fer flotte à la surface et réagit avec la couche d'oxyde pour générer des crasses. Si les crasses sont mélangées au métal, ou si le niveau du pot est si bas que le métal sub-superficiel est aspiré dans le col de cygne, la coulée contiendra des particules dures, ce qui entraînera les défauts indiqués sous le terme "fer" dans la section "contamination".
Une température excessive entraîne également une perte de magnésium, car il s'agit d'un élément volatil qui est cuit. Une faible teneur en magnésium expose la pièce moulée à d'importantes difficultés de corrosion en service.
Il convient de noter que la température globale de fusion n'est pas le seul facteur à prendre en considération. S'il y a un point chaud dans le four, par exemple un brûleur mal calibré, la température élevée provoquera une accumulation de fer. Dans les cas les plus graves, le creuset peut être rongé, ce qui entraîne une coulure.
Recommandé métal coulée températures sont :
Zamak No 2,3,5,7 |
415-4S0°C |
ZA8 |
420-445°C |
ZA12 |
465-495°C |
ZA27 |
550-580°C |
Acuzinc 5 |
~ 480°C |
Acuzinc 10 |
~ 5S0°C |
Lorsque les alliages ZA, en particulier le ZA-27, sont fondus, ils ont tendance à se séparer par gravité en couches riches en aluminium et en zinc. L'agitation verticale permet de mélanger la masse fondue ; une forte agitation doit être évitée, car elle favorise l'oxydation. Une fois mélangée, la matière fondue doit rester stable. Il est essentiel que toute couche d'écume créée ne soit pas présumée séparée et mélangée. Le ZA-27 ne doit pas être stocké à une température inférieure à 540°C, car le fer en solution précipite sous forme de particules intermétalliques massives.
La fusion et la conservation des lingots conformes aux spécifications devraient se dérouler sans problème tant qu'un contrôle adéquat de la température est assuré et qu'aucune contamination involontaire ne se produit. Lors de la refonte des pièces coulées et des déchets, plusieurs aspects doivent être pris en compte.
Les retours doivent être strictement séparés, en particulier dans les ateliers qui fondent également des alliages d'aluminium. Le mélange de certaines coulées d'aluminium avec les alliages de zinc 4% produit des pièces moulées à forte teneur en aluminium, ce qui les rend cassantes. Le même problème se posera si l'alliage ZA est combiné à un alliage normal.
La refonte directe de copeaux, de bavures et d'autres matériaux légers contaminés en surface produit un excès de crasse et risque d'absorber des impuretés. Il est préférable de traiter ces matériaux séparément afin de pouvoir déterminer la composition du lingot refondu. Les crasses doivent être traitées séparément pour des raisons identiques. Le flux a tendance à extraire le magnésium, en particulier lorsque le métal est chauffé. Les pièces coulées électrodéposées requièrent une attention particulière. Pendant la fusion, la peau de la plaque électrolytique reste à la surface et peut être écrémée. La plaque ne doit pas être brisée et mélangée à la fonte, car le nickel, en particulier, peut créer des points durs.
Au cours de la fusion et de la coulée, l'alliage perd une petite quantité de magnésium (par volatilisation) et d'aluminium (par interaction avec le fer et élimination ultérieure sous forme d'écume). Une refonte continue du même métal finirait par produire des pièces coulées hors normes. Des tests sur l'alliage No3 ont montré qu'il faut sept cycles pour réduire le magnésium à un niveau inférieur à celui spécifié. Pour éviter cette dégradation éventuelle, le processus doit être alimenté en continu en lingots vierges.
Défauts de la coulée sous pression du zinc
Vous trouverez ci-dessous les défauts les plus courants répertoriés dans moulage sous pression du zincDans le cas de la coulée sous pression de l'aluminium ou du magnésium, les problèmes sont à peu près les mêmes que dans le cas de la coulée du zinc,
Interne Défauts dans le moulage sous pression du zinc
Rétrécissement Porosité
Lorsque l'alliage passe de l'état liquide à l'état solide, il se rétracte de plusieurs pour cent de son volume de coulée. Un vide se forme si le métal liquide supplémentaire n'est pas disponible pour alimenter la rétraction. Il s'agit de la porosité de retrait. Elle se produit souvent dans des parties lourdes isolées sous forme d'énormes trous irréguliers (figure S), mais elle peut aussi prendre une forme interdendritique, semblable à une fissure, en particulier dans les alliages à longue plage de congélation tels que le ZA-27 et l'Acuzinc.
La porosité interne peut être révélée si des surfaces telles que des brides ou des alésages doivent être usinées, ce qui entraîne un rejet. La porosité peut également entraîner l'usure des outils et la dérive des forets pendant les processus d'usinage. L'influence sur la résistance sera déterminée à la fois par la distribution et la quantité de porosité. Il est important de rappeler que les résistances nominales indiquées pour les alliages ont été obtenues sur des éprouvettes présentant des niveaux de porosité typiques.
Pour limiter la porosité de retrait, il faut augmenter la pression du métal et s'assurer que l'opercule est suffisamment épais pour être actif pendant la solidification. Le piston ne doit pas se déplacer au point de toucher le fond du col de cygne, ce qui pourrait entraîner un manque de pression sur le métal. Le temps de remplissage doit être suffisant pour permettre une solidification complète ; sinon, le métal sera retiré de la cavité lorsque le piston reviendra. Le refroidissement local peut minimiser les points chauds et donc empêcher la production de plaques isolées de métal liquide qui, lorsqu'elles sont gelées, produisent des pores.
La porosité interdendritique peut entraîner des fuites dans les composants étanches à la pression. Plus la plage de congélation de l'alliage est longue, plus le risque de fuite est élevé. La coulée à basse température épaissit la peau de coulée et réduit le risque de fuite. Toutefois, ce processus peut être entravé par la nécessité d'une température de moule suffisamment élevée pour obtenir un aspect de surface souhaitable. Les températures de la face de la filière sont généralement comprises entre 170°C et 240°C.
Porosité du gaz
Lorsque la matrice se remplit rapidement, d'énormes volumes de gaz peuvent être piégés. Après la solidification à haute pression, le gaz forme des bulles quasi-sphériques, généralement autour de la ligne centrale (figure 4). Le gaz et la porosité de retrait peuvent coexister ; dans ce cas, le gaz a tendance à arrondir la porosité de retrait
La porosité gazeuse provoque les mêmes défauts que la porosité de retrait, mais les fuites sont moins probables car les trous de gaz sont rarement interconnectés. En outre, la porosité gazeuse est la principale cause de formation de cloques dans les pièces moulées. Si l'alliage est faible, à la suite d'un chauffage à haute température, l'énorme pression du gaz dans le pore peut souffler la peau métallique environnante. L'augmentation du temps de refroidissement et/ou la diminution de la température de la matrice peuvent réduire l'apparition de cloques peu après l'éjection.
Idéalement, la quantité de gaz piégée dans la cavité doit être réduite au minimum. Pour ce faire, il faut que la course du premier étage soit la plus grande possible et que le temps de remplissage soit le plus long possible (tout en gardant à l'esprit la nécessité contradictoire de périodes de remplissage courtes pour obtenir un aspect de surface acceptable). Les évents doivent être maximisés et correctement positionnés. Il est avantageux de réduire au minimum les projections sur la matrice. La porosité est souvent moins problématique, et produit certainement moins de cloques, lorsqu'elle se présente sous la forme de nombreux pores microscopiques plutôt que de quelques gros pores. Les petits pores sont favorisés par l'utilisation de vitesses de métal élevées ; des vitesses de porte de 40 m/s devraient être l'objectif. Le moulage sous vide élimine ce type de porosité.
Défauts de microporosité dans le moulage sous pression
Outre la porosité visible, il existe une porosité dont la taille ne peut être observée qu'au microscope. Cette microporosité, si elle est absente de la peau de coulée (comme c'est souvent le cas), n'a pas d'impact négatif, à moins qu'elle ne soit exposée ultérieurement par des processus de polissage avant le revêtement de surface.
Larmes and Fissures
Les déchirures à chaud, comme leur nom l'indique, se produisent à des températures proches de la plage de solidification. La fissure est causée par la rupture de la coulée dans des conditions de forte déformation et de faible contrainte, et elle suit souvent un schéma irrégulier (figure 5). Cela contraste avec les fissures beaucoup plus droites qui peuvent se produire à des températures plus basses dans des conditions de forte contrainte et de faible déformation. En outre, l'aspect des faces de rupture varie entre ces deux types de défauts.
La forme du composant contribue de manière significative à la déchirure à chaud. Ce phénomène se produit lorsque le retrait de solidification est limité à une petite zone, en particulier si cette zone est également une zone chaude. Le ZA-27 et l'Acuzinc sont plus sujets à ce défaut que les autres alliages, sauf si leur teneur en aluminium est inférieure aux spécifications ou s'ils contiennent un excès de magnésium. À l'exception de la distribution de la température de la matrice, les paramètres de coulée n'ont aucun effet sur la déchirure à chaud. Le refroidissement des zones chaudes de la matrice peut aider à résoudre le problème.
La fissuration se produit lors de l'éjection lorsque des forces excessives sont générées en raison de l'encrassement de la pièce moulée dans la matrice. Ce phénomène est souvent dû à des erreurs de fabrication d'outillage qui ont entraîné des contre-dépouilles, un tirage inadéquat ou des bavures. L'allongement de la période de refroidissement pour rendre la pièce moulée plus résistante et mieux à même d'absorber les contraintes d'éjection peut contribuer à prévenir la fissuration. Toutefois, lorsque la force est causée par la contraction de la pièce moulée sur la matrice, des temps de refroidissement prolongés sont inefficaces et une éjection plus rapide peut être bénéfique.
Questions relatives aux inclusions
Ce problème se pose beaucoup moins dans les alliages de zinc que dans ceux qui forment des films d'oxyde plus résistants. En effet, les intermétalliques de fer créés par une gestion inadéquate de la fusion sont souvent les seuls qui posent des problèmes dans la pratique. Le niveau de métal dans le pot ne doit pas baisser au point que le métal de subsurface pénètre dans le col de cygne.
Défauts de surface des pièces moulées sous pression
Tours d'or.
Ce défaut (également connu sous le nom de "flowmarks" ou "cold flow") se développe lorsque les courants de métal qui se sont pré-solidifiés au contact de la matrice ne sont pas refondus dans la masse de la coulée lorsque du métal supplémentaire arrive. La surface se présente sous la forme d'une rainure inégale avec un effet d'écaille de poisson dont la profondeur varie en fonction de la gravité du recouvrement (figure 6). La section transversale présente la caractéristique déterminante d'un recouvrement à froid, à savoir la mesure dans laquelle la fracture superficielle se poursuit horizontalement et génère une discontinuité sous la surface (figure 7).
Les retassures à froid dégradent l'aspect des pièces coulées et posent des problèmes lors des procédures de finition ultérieures, en particulier lors de la galvanoplastie, ce qui entraîne une défaillance du revêtement. S'ils sont importants, les retassures peuvent nuire à la ductilité de la pièce moulée. Le temps de remplissage de la cavité et la température de la filière sont les principaux paramètres de coulée qui influencent la production de retassures à froid. Les caractéristiques moins importantes sont le schéma d'écoulement, la distance d'écoulement, la vitesse du métal, la surface de la filière et la température du métal. L'épaisseur de la pièce coulée est cruciale. Les retassures sont plus fréquentes dans les pièces coulées de faible épaisseur.
Le lien entre l'aspect de la surface, l'épaisseur de la paroi, la température de la matrice et le temps de remplissage a été déterminé. Le prédicteur de surface (figure 8) peut être utilisé pour déterminer le temps de remplissage maximal de la cavité et la température minimale de la matrice qui permettront d'obtenir une surface électrodéposable. Si la pièce est destinée à être peinte, des temps de remplissage plus longs et des températures de matrice plus basses sont acceptables. Une surface texturée sur la matrice peut augmenter le temps de remplissage maximum de 50%.
Il arrive que des décalages apparaissent alors que la matrice est chaude et que le temps de remplissage de la cavité est court. ils sont généralement associés à un écoulement tourbillonnaire qui a piégé du gaz. La contre-pression exercée par le gaz à les fin de cavité remplir ralentit les encerclant métal vapeur et donc produit les conditions nécessaire pour local tour de piste formation. En cette cas, il volonté être nécessaire à réduire les l'air piégé en les mourir (voir section sur la porosité) ou de modifier le schéma de remplissage afin d'éviter la formation de telles lacunes.
Lamination
Les stratifications sont des feuilles de métal qui se chevauchent et s'étendent sur une plus grande surface et de manière plus uniforme que les stratifications à froid. Elles peuvent survenir en cas de problèmes avec le système d'injection de la machine, qui fait que la matrice se remplit en une série d'impulsions. Une stratification se formera également si la course du premier étage est trop longue, ce qui fait que le premier métal entrant dans la cavité se déplace lentement et se fige.
Mauvais fonctionnement
Si la matrice est trop froide et le temps de remplissage trop long, la coulée ne sera pas complète. Le métal se solidifiera complètement avant que la cavité ne soit remplie et il en résultera une erreur de coulée (figure 9). Les petites zones de maquillage incomplet, par exemple à l'extrémité des ailettes ou au centre des tourbillons, peuvent être causées par des gaz emprisonnés qui empêchent le métal de remplir complètement la cavité. Si la capacité de tir de la machine est dépassée, le "tir court" provoquera un raté.
Tir ou éclaboussure
Comme les décalages, ils sont le résultat d'une pré-solidification, mais l'apparence et la cause sont différentes. Le défaut peut être purement superficiel, et produire alors une texture rugueuse, ou peut être incrusté sous la forme d'une couche d'ozone. "inclusion d'alliage" (figure 10). Les "tirs" sont des globules d'alliage qui ont été pulvérisés hors du flux principal de métal et qui n'ont pas été adsorbés par la suite.
Les éclaboussures peuvent provenir de l'impulsion lorsque le premier métal passe à travers la grille ou peuvent être des tourbillons qui s'enroulent sur le bord du flux de métal. C'est pourquoi les éclaboussures se produisent généralement à proximité de la porte. Parfois, les éclaboussures sont si peu liées à la pièce coulée qu'il en reste une partie lors de l'éjection. Ce matériau formera alors des "inclusions" dans la coulée suivante.
L'augmentation de la température de la filière devrait améliorer les choses, mais le principal remède consistera à modifier la porte de manière à obtenir un remplissage frontal plus solide.
Ces dépressions en les coulée surface sont moins commun en le zinc alliage que certains autres métaux et beaucoup Le problème est moins important que pour les pièces moulées en plastique. La cause en est le même retrait de solidification qui est la force motrice de la formation de la porosité. Une section localement lourde présente un puits de surface plutôt qu'un pore interne lorsque la distribution de la température est telle que le centre de chaleur est proche d'une surface. Le retrait final attire alors vers le bas la faible peau de coulée solide pour former une dépression (figure 11).
Dans les alliages tels que le ZA-27, l'aspect peut être différent. Ici, le défaut s'étend sur une zone plus large et semble givré. La longue plage de congélation a modifié le comportement de sorte qu'au lieu d'une coulée définitive, le retrait a drainé la surface du liquide eutectique et l'a laissée rugueuse et semi-poreuse.
Les remèdes sont les mêmes que ceux indiqués pour la porosité de retrait. Si cela est possible, il convient de revoir la conception de la coulée afin de réduire le point chaud.
Lacs
Un lac est une large marche dans la surface de coulée avec une hauteur de marche de seulement 5 à 0 micromètre. Il devient très visible sur les composants qui sont ensuite polis et plaqués, où il produit un effet d'ondulation insatisfaisant (figure 12).
En dépit de intensif l'enquête, les cause, et donc les remède reste insaisissable. Il y a est preuve que le terme "lac" peut être attribué à deux défauts de même apparence, Lorsqu'ils sont sectionnés, certains lacs présentent une microstructure différente sous le lac que dans la masse de la pièce coulée ou la surface environnante. Les lacs de ce type semblent être associés à une solidification locale précoce et les remèdes pris pour les tours froids peuvent être bénéfiques.
D'autres lacs, en revanche, ne présentent aucun changement microstructurel. En outre, sur les pièces minces, il n'est pas rare que le défaut traverse l'épaisseur, qu'il y ait une dépression d'un côté et une zone surélevée de l'autre. En fait, la pièce coulée s'est pliée de quelques dizaines de microns. Cela indique que le lac s'est formé alors que la pièce était solide et il est tentant de spéculer sur le fait que le retrait limité a produit un lac. "bidon d'huile" distorsion.
Il est assez clair que le défaut est lié à la chaleur et reflète probablement les gradients de température à l'intérieur de l'outil.
Ampoules
En coupant ces protubérances à la surface lisse, on découvre leur centre creux. Les ampoules sont causées par l'expansion du gaz à haute pression piégé dans les pores de gaz qui gonflent la peau superficielle de la pièce moulée (figure 1).3). Les cloques se forment lorsque l'alliage est trop faible pour contenir les forces générées par le gaz interne, lorsque les la coulée est trop chaude. La réduction de la température de la pièce coulée au moment de l'éjection permet d'éviter la formation de cloques.
On y parvient en augmentant le refroidissement de la filière et/ou le temps de refroidissement de la filière. La formation de cloques sera atténuée en réduisant la quantité d'air piégé (voir la section sur la porosité du gaz) et en utilisant une vitesse de grille élevée afin d'affiner la taille des pores du gaz.
Fissures
Les fissures superficielles peuvent avoir deux causes principales. La première forme, que l'on rencontre fréquemment aux changements de section, est la déchirure à chaud, dans laquelle la forte déformation locale induite par la limitation du retrait près du point de fusion a entraîné une fracture intergranulaire. Le second type se produit lorsque la pièce coulée colle dans la matrice, ce qui entraîne des pressions importantes lors de l'éjection. Ces fissures sont généralement moins intergranulaires et plus droites que celles causées par les déchirures à chaud.
La déchirure à chaud est plus visible dans les alliages à longue plage de congélation, tels que le ZA-27, et est principalement due à la forme du composant. Un refroidissement local de la zone concernée peut être bénéfique. (Voir la section sur les lingots pour plus d'informations).
La fissuration par éjection doit être traitée dans un premier temps en éliminant les problèmes liés à la filière, tels que les contre-dépouilles, la conicité inadéquate et les surfaces rugueuses. Si la température de la matrice est réduite et que la période de refroidissement est augmentée, la pièce moulée sera plus solide et donc mieux à même de résister aux forces d'éjection. Toutefois, si le collage est dû à la contraction de la pièce moulée sur la matrice, par exemple un trou dans la tige centrale, une éjection précoce pour réduire la contraction peut s'avérer bénéfique. Pour être efficace en tant qu'agent de séparation, le spray de la filière doit couvrir correctement la face de la filière.
Traînée Marques
Le frottement entre la pièce moulée et la matrice lors de l'éjection du composant provoque des marques le long de la ligne d'étirage (voir figure 14). Les marques de traînée sont dues à un tirage insuffisant, à des contre-dépouilles et à la rugosité de la surface, ainsi qu'à une pulvérisation inadéquate de la matrice. Il est impossible d'éviter toute éraflure lorsque la pièce moulée se rétracte étroitement contre le composant. Dans ce cas, il est nécessaire d'avoir une conicité la plus élevée possible et d'optimiser la durée (température) d'éjection de la pièce moulée.
Distorsion
Les pièces coulées pliées, indentées ou percées par les broches d'éjection, apparaissent lorsque la pièce coulée est trop faible pour résister aux forces d'éjection (figure 15). Il convient tout d'abord de vérifier que la matrice ne présente pas de contre-dépouille, de dépouille insuffisante ou de surface rugueuse. Le problème peut ensuite être résolu en abaissant la température à laquelle la pièce est éjectée. Pour ce faire, il convient d'abaisser la température de la filière et/ou d'augmenter le temps de refroidissement de la filière.
L'érosion
L'érosion produit de l'usure et des cavités dans la surface de la filière, ce qui peut entraîner des marques sur le moulage et des problèmes d'éjection. Elle réduit également la durée de vie de la filière. L'alliage en fusion use physiquement la filière aux endroits où le flux de métal frappe la filière à grande vitesse. L'usure peut également se produire aux endroits où le métal à grande vitesse tourbillonne et produit de la cavitation hydraulique. Dans les deux cas, la réduction de la vitesse du métal permet de réduire l'érosion. L'érosion est également réduite en abaissant la température de la filière. Elle est plus susceptible de se produire dans les matrices qui sont trempées jusqu'au côté mou de la plage de dureté.
Chaleur Vérification
Un motif de pavage fou d'ailettes sur la surface de la pièce moulée est dû à la rupture de la surface de la matrice (contrôle de la chaleur). La cause en est la contrainte superficielle induite par le cycle de température qui se produit à chaque coulée. La gravité de la contrainte dépend de la température de fusion de l'alliage. Les alliages de zinc ayant une faible plage de fusion, ce défaut est rare et n'est observé que dans les matrices ayant produit des millions de pièces.
Soudure
Il s'agit de l'accumulation sur la surface de la matrice d'une couche d'alliage qui adhère à la fois physiquement et chimiquement. La pièce coulée est marquée lorsque la peau collée est arrachée lors de l'éjection et la contre-dépouille produite par l'accumulation entraîne également des rayures sur la pièce coulée. La soudure est plus probable lorsque la vitesse de la porte est élevée et que la filière est en contact avec la surface de la pièce. température est élevé. Mourir pulvériser doit être adéquat en commande à produire a de protection couche sur les acier surface.
Les accumulations dues à la soudure sont difficiles à éliminer de la filière. Cela les distingue des accumulations dues à l'excès de spray de la matrice, qui peuvent généralement être essuyées.
Flash
Lorsque le métal pénètre entre les faces de contact des parties de la filière et les moitiés de la filière, de fines couches d'extrane- ous matériel sont gauche sur les coulée (chiffre 16). Vers prévenir cette les meurt doit être fortement construit et parfaitement exclu.
Même dans ce cas, les déviations thermiques peuvent entraîner l'ouverture de fentes à la température de fonctionnement. Si la force de verrouillage de la machine n'est pas adaptée à la taille de la pièce coulée, les matrices se sépareront et des zones étendues de bavures se formeront. La réduction de la pression du métal diminuera la probabilité d'éclatement des matrices. De même, l'augmentation du temps de remplissage, et donc la réduction de la température du métal au moment où il atteint la ligne de séparation, réduira la pénétration entre les faces d'accouplement.
Dimensionnel Cohérence
La question des tolérances dimensionnelles est traitée en détail dans un autre chapitre de ce manuel. Elle est mentionnée ici parce que la non-conformité peut être considérée comme un défaut de coulée.
La reproductibilité d'une dimension telle que coulée, tir après tir, dépend presque exclusivement de la constance de la température. Le facteur qui a le plus d'effet est la température de la pièce coulée au moment où elle est éjectée de la matrice. StabilisLe respect de cette température améliore la reproductibilité des dimensions et facilite le maintien de tolérances étroites.
En raison des effets du vieillissement métallurgique, il y aura un léger retrait avec le temps après la coulée. La quantité est faible et reproductible et ne constitue un problème que pour les composants spécifiés selon les tolérances les plus strictes. Un traitement thermique à basse température, généralement quelques heures à 95°C, peut être utilisé pour stabiliser le moulage si nécessaire.
Trimming et Robeeng
Général problèmes en cette zone de les production fonctionnement sont inacceptable changer de contour due à plus- l'enlèvement de métal et les déformations dues à une manipulation brutale ou à des problèmes d'alignement.
Rupture Défauts
En raison de la minceur des pores que permet la coulée d'alliages de zinc, il est souvent préférable d'opter pour le cassage plutôt que pour l'ébarbage à la presse. Le cassage peut être manuel ou mécanique dans des machines à spirale ou à tambour. Une cassure nette dépend de la forme et de l'épaisseur de la grille.
Earring
Les portes légèrement incurvées peuvent être cassées mais ont tendance à laisser des traces. "oreilles" sur la pièce moulée lorsque des vannes coniques sont utilisées. En fonction de la conception et de la direction de la flexion, même sur un portail droit, la terre peut être laissée en saillie par rapport à la pièce moulée..
Break en
Ici, la forme du portail et la direction de la flexion ont conduit la fracture à pénétrer dans la pièce coulée, laissant ainsi une contre-dépouille dans la pièce coulée.
Ligne de porte Porosité
Même lorsque la porte se brise proprement, un témoin est laissé sur le moulage. Le métal mis à nu est différent de la peau de la coulée qui l'entoure ; il est typique de l'intérieur de la coulée et peut donc contenir des porosités (figure 17). Plus la grille est épaisse, plus cette porosité risque d'être visible. L'épaisseur de la ligne d'obturation porosLa microporosité sera influencée par les facteurs couverts dans la section Porosité de ce chapitre. Même si elle n'est pas visible, la microporosité exposée peut poser un problème après le revêtement.
Appuyer sur Trim Défauts dans le moulage sous pression du zinc
Notation
Un mauvais positionnement du composant et/ou un alignement incorrect de la matrice et des jeux peuvent conduire à ce que la matrice d'ébarbage rase le côté de la pièce moulée.
Pliage
Lorsque la bavure est fine et ne s'étend que sur une courte distance, la ductilité de l'alliage est telle que la bavure peut se plier plutôt que d'être coupée. Il en résulte un mince pli de métal à la surface du composant. Lorsque ce problème se pose, il peut être préférable de procéder délibérément à un flash transversal, plutôt que de l'obturer sans succès, afin que l'outil d'ébarbage puisse couper une épaisseur définie.
Finitiong Défauts dans le moulage sous pression du zinc
Un enlèvement excessif de la surface exposera la microporosité. Celle-ci peut ne pas être visible mais entraînera des problèmes si le moulage est ensuite revêtu.
Barrelling/Vibropolisheng Défauts
Mise à l'échelle
Excessif traitement de fortement décalé moulages peut plomb à les tours levage ou devenir complètement détaché (figure 18).
Polissage Défauts
Un enlèvement excessif de métal expose la microporosité. L'apparition de petites bosses et de queues de comète est due à des particules dures dans la pièce coulée provenant d'une contamination métallique. Comme pour le barattage et le vibro-polissage, te brunissage ne fait que masquer les défauts de surface, tels que les chevauchements. La discontinuité sous-jacente est toujours présente et peut causer des problèmes plus tard.
Usinage et assemblage Défauts dans le moulage sous pression du zinc
Outil Porter
L'usure rapide des outils de coupe peut être due à la présence de particules dures dans l'alliage à la suite d'une contamination de la matière fondue. L'usure et la rupture peuvent également être causées par la pénétration des outils dans de grands pores de gaz ou de retrait. La prévention de la porosité est traitée dans la section sur la coulée.
Exposé Porosité
L'élimination de la peau superficielle saine peut exposer la porosité sur les faces usinées, par exemple sur les brides ou dans les alésages. Le contrôle de la porosité est abordé dans la section sur le moulage.
Fracture
Les opérations de rivetage et de pliage sont fréquemment utilisées pour assembler moulage en alliage de zincs. Si les rivets et les pattes ne sont pas bien réalisés, ces éléments peuvent se briser. Les surfaces doivent être exemptes de chevauchements et de fissures excessifs (voir la section sur le moulage). Le processus de vieillissement qui se produit après la coulée affecte la ductilité. Il est au minimum d'environ trois semaines après la coulée. La ductilité de l'alliage est considérablement accrue par la déformation à des températures modérément élevées.
Poudre Coating défauts de la coulée sous pression du zinc
Dans cette section, nous examinerons les défauts qui surviennent pendant le revêtement et qui affectent le revêtement en cours d'utilisation. Seuls les défauts causée par défauts en les coulée sont couverts. A plus complet couverture, qui comprend défauts en le manteau lui-même, est indiqué dans les livrets "Placage de la matrice en zinc moulages" et "Revêtement par poudre de la matrice en zinc moulages" qui ont été publiés par la Zinc Development Association, Londres, Royaume-Uni.
Distorsion
La résistance de l'alliage de zinc diminue avec la température, de sorte qu'aux températures du four à peinture, il est assez faible et même la température du bain de placage a un certain effet. Par conséquent, si les pièces coulées sont mal soutenues ou si les gabarits exercent une force de ressort trop élevée, les pièces coulées seront déformées. Un gauchissement peut également se produire en raison de l'allègement des contraintes de la coulée. Le refroidissement rapide pendant la coulée peut bloquer les tensions causées par le retrait différentiel. Le niveau de contrainte dépend largement de la forme du composant.
Irregular Surface
L'aspect écaillé des lacs froids apparaît à travers la couche de placage et, s'il est important, peut également apparaître à travers la couche de peinture plus épaisse. Les limites des lacs apparaissent sous la forme d'une marque d'ondulation sur la surface plaquée ou peinte. Les causes et les remèdes à ces défauts sont indiqués dans la section sur le moulage.
Plateng Défauts dans le moulage sous pression du zinc
Ampoules
Les boursouflures dans la plaque électrolytique sont un défaut de coulée (les boursouflures et autres défauts peuvent également être causés par des problèmes liés au processus de placage) et sont dues à l'emprisonnement de terre, de gaz et de solutions de placage dans les imperfections de la surface. La formation de gaz derrière le revêtement imperméable entraîne la formation de cloques, voire d'éclats. L'expansion causée par les produits de corrosion issus de la réaction de la fonte et des solutions corrosives piégées aura un effet similaire.
Si le piégeage est causé par des retouches à froid, la surface de coulée et la plaque peuvent se soulever. Il convient de noter que les plis provoqués par le pliage de la bavette sur la surface produiront les mêmes problèmes que les retassures. En cas de mise en service, les dommages causés à la couche plaquée se traduiront par de la corrosion. (Figures 7, 19.)
Les pièces coulées dont la surface contient des retouches à froid ou qui présentent une porosité ou une micro-porosité importante sont susceptibles de produire des boursouflures dans la couche plaquée. Des détails sur ces défauts sont donnés dans les sections Coulée et Dressage.
Paint Défauts dans le moulage sous pression du zinc
Ampoules
Les cloques sur la surface peinte d'une pièce de fonderie peuvent être de deux types. Il est essentiel de les distinguer, car les mesures correctives nécessaires sont différentes.
Les cloques de taille modérée qui peuvent apparaître sur les côtés opposés de la pièce moulée sont générées par la porosité du gaz à l'intérieur de la pièce moulée (figure 13). On peut le vérifier en grattant la couche de peinture ou en découpant la cloque. Il s'agit d'une cloque de gaz si le défaut se trouve dans la fonte et non dans la peinture. Le problème est dû à la faiblesse de l'alliage de zinc à la température du four à peinture, ce qui provoque un gonflement de la pièce coulée en raison de la présence de gaz à haute pression à l'intérieur des pores.
La température de cuisson est cruciale et, si la procédure prévoit diverses circonstances, il convient de choisir l'option d'une cuisson plus longue mais à une température plus basse. Les pièces coulées qui seront cuites à des températures élevées (200°C) doivent contenir une quantité minimale de gaz piégé finement dispersé.
Les petites cloques sont causées par des gaz qui s'échappent de la surface de coulée et qui se coincent dans le film de peinture. Parfois, le gaz s'échappe, mais la peinture qui se solidifie est trop dure pour reconstituer une surface lisse, ce qui provoque une cloque semblable à un volcan miniature (figure 20). Pour éviter ces problèmes, le moulage doit être exempt de discontinuités superficielles susceptibles de piéger les gaz et les salissures, telles que les retombées froides, les plis et les porosités visibles. La cuisson avant l'ajout de la couche organique permet au moulage d'expulser les gaz et de résoudre le problème.
Ébréché Peinture
L'écaillage de la peinture peut parfois être dû à un défaut de moulage ou à une mauvaise manipulation après l'application de la peinture. Si un pli (c'est-à-dire un flash plié) est peint puis soumis à un impact, il peut se briser, révélant la surface sous-jacente non revêtue.
Manipulation, stockage et conditionnement
Une mauvaise manipulation peut entraîner une détérioration de la surface ou une déformation de l'appareil. moulage sous pression. Dans le cas d'outils à plusieurs cavités, le moulage de liens entre des composants fragiles peut s'avérer efficace pour fournir un support. L'ampleur des dommages de surface qui peuvent être acceptés est déterminée par les exigences de qualité et le revêtement utilisé.
Lorsque les pièces de fonte nues doivent être stockées pendant une certaine période, elles doivent être sèches. L'humidité favorise le développement de la rouille blanche et de la corrosion superficielle. Si l'eau de trempe ou de pulvérisation de la matrice s'est dégradée, entraînant le développement de composés acides, la corrosion peut être plus grave. Les pièces moulées doivent être revêtues ou peintes dès que possible après la coulée et le polissage afin de réduire le risque de contamination de la surface.
Les pièces de fonte doivent être emballées dans des matériaux secs, car le carton humide produit des acides qui endommagent et noircissent les pièces de fonte en zinc.
0 commentaires