Le processus de fabrication des motos s'est amélioré ces derniers temps, en particulier lorsqu'il s'agit de fabriquer des pièces plus légères et plus résistantes. L'une des principales méthodes de fabrication de pièces dans ce secteur est le moulage sous pression, qui permet de mouler le métal afin d'obtenir des pièces solides et précises qui sont utilisées dans les motos d'aujourd'hui. Parmi ces pièces, les pièces de moteur de moto, les cadres de moto et les pièces de carrosserie fabriquées par moulage d'aluminium sont populaires parce qu'elles sont robustes, bien fabriquées et peuvent résister à une forte chaleur.
Cet article explique comment le moulage sous pression est utilisé pour fabriquer des pièces de motocycles. Il aborde des questions telles que la température adéquate, la pression nécessaire, la vitesse de réchauffement ou de refroidissement des matériaux et la vérification de l'ajustement et de l'aspect des pièces.
Comprendre la technologie du moulage sous pression
Le moulage sous pression tire son nom du fait que le métal est poussé dans un moule rapidement et sous une forte pression. Cette méthode permet de fabriquer des pièces petites et détaillées qui s'emboîtent très bien et qui ne nécessitent pas beaucoup d'usinage pour obtenir une forme correcte.
L'industrie utilise principalement deux types de méthodes de moulage sous pression.
- Moulage sous pression en chambre chaude
- Moulage sous pression en chambre froide
Le moulage sous pression en chambre froide est souvent utilisé pour fabriquer des pièces de moteur de moto, car les matériaux utilisés pour les fabriquer doivent être fondus à une température assez élevée.
Pourquoi les fabricants de motos choisissent-ils le moulage sous pression ?
Le moulage sous pression est souvent utilisé par les fabricants de motos parce qu'il permet de produire des pièces solides et capables de résister à l'utilisation intensive des motos, tout en permettant de fabriquer des pièces plus rapidement et à moindre coût.
Le moulage sous pression est important parce qu'il nous permet de fabriquer des pièces pour les motos qui doivent être très résistantes.
- Rapport résistance/poids élevé
- Excellente finition de surface
- Conductivité thermique pour les pièces sensibles à la chaleur
- Précision dimensionnelle élevée
Le moulage sous pression de l'aluminium étant à la fois durable et doté d'une excellente résistance à la corrosion, il est utilisé pour produire des carters d'embrayage, des carters de vilebrequin, des culasses et des couvercles d'engrenage.
Pièces moulées sous pression pour motocycles
A. Composants du moteur
- Culasse
- Carter
- Corps de pompe à huile
- Couvercles de transmission
Lorsque la moto est en marche, de nombreuses pièces sont portées à haute température et soumises à une forte pression à l'intérieur du moteur. C'est pourquoi elles sont généralement fabriquées en plaçant du métal dans un moule et en exerçant une forte pression sur celui-ci afin que le métal reste solide et ne présente pas de nombreux trous d'air.
B. Parties structurelles
- Colliers de serrage du guidon
- Supports de repose-pieds
- Moyeux de roue
Elles doivent être précises au dixième de millimètre près et avoir la même résistance que toutes les autres pièces de la structure.
C. Parties esthétiques et de soutien
- Boîtiers de rétroviseurs
- Supports de l'indicateur
- Supports de plaque d'immatriculation
Bien qu'elles n'aient pas à supporter de charge, ces pièces peuvent être fabriquées avec une surface exceptionnelle, ce qui réduit la nécessité d'un traitement supplémentaire.
Matériaux et propriétés thermiques
La plupart des motos moulées sous pression sont fabriquées à partir d'alliages d'aluminium (A380, ADC12 ou LM6).
Propriétés clés de l'alliage d'aluminium A380 :
Propriété | Valeur |
Point de fusion | 555-595°C |
Conductivité thermique | 96-105 W/m-K |
Densité | 2,7 g/cm³ |
Résistance à la traction | 310 MPa |
Limite d'élasticité | 140 MPa |
Température de fonctionnement | Jusqu'à 300°C |
En raison de sa conductivité thermique, la chaleur peut se dissiper librement dans les pièces du moteur des motos, principalement dans les moteurs refroidis par air.
Détaillé : Pièces moulées sous pression pour motocycles
Le moulage sous pression est aujourd'hui un élément important de la fabrication des motos, car il permet à l'entreprise de produire rapidement des pièces solides et précises qui sont légères. Le processus fonctionne bien avec des métaux comme l'aluminium, car ces matériaux conviennent aux structures et aux machines parce qu'ils sont à la fois solides et légers, et qu'ils dégagent moins de chaleur lorsqu'ils sont soudés.
Vous trouverez ci-dessous quelques-unes des pièces moulées sous pression les plus couramment utilisées sur les motos, ainsi que leur fonction, les matériaux à partir desquels elles sont généralement fabriquées, la force qu'elles doivent supporter et les types de moules qui conviennent le mieux pour les fabriquer.
1. Carter du moteur
Fonction :
Le carter est l'endroit où se trouvent le vilebrequin, la transmission et, parfois, l'endroit où est stockée l'huile du moteur. C'est l'une des pièces les plus difficiles à traiter, car elle peut devenir très chaude et provoquer des niveaux élevés de stress dans un moteur de moto.
Matériau :
- Alliage d'aluminium (A380 ou ADC12)
- Conductivité thermique : ~96-105 W/m-K
- Point de fusion : ~610°C
- Température de fonctionnement : 80-120°C
Exigences en matière de moulage :
- Une épaisseur de 2,5 à 3 mm permet d'utiliser des matériaux plus légers.
- Passages à l'intérieur du moteur qui permettent à l'huile de circuler et aux pièces de rester froides.
- Il faut utiliser des presses qui travaillent à haute pression, ainsi qu'une machine à vide pour aider à maintenir le métal exempt de trous.
Tolérance dimensionnelle :
- ±0,05 mm pour les surfaces qui relient un roulement et un logement
2. Tête de cylindre
Fonction :
La culasse ferme la partie où le carburant est brûlé et maintient les soupapes, les bougies d'allumage et un arbre à cames en place.
Matériau :
- Aluminium LM6 ou ADC12
- Doit supporter des charges thermiques élevées (200-250°C)
- Bonne usinabilité et résistance à la corrosion
Considérations relatives au moulage :
- Une ventilation précise du moule est nécessaire pour éviter que le gaz ne soit piégé dans l'article moulé.
- L'usinage CNC post-coulée permet de s'assurer que les guides de soupapes et les trous d'arbre à cames des pièces en aluminium sont finis pour obtenir une forme régulière et lisse.
- Le tuyau doit être étanche à la pression (des tests de pression hydrostatique sont effectués jusqu'à 5 bars).
3. Couvercles de moteur (embrayage, magnéto, boîte de vitesses)
Fonction :
Protéger les bougies d'allumage, les soupapes et les pistons du moteur contre l'encrassement, les fuites d'huile et les dommages extérieurs.
Matériau:
- Aluminium A360 ou A380
- Souvent recouvert d'un revêtement en poudre ou anodisé après la coulée
- Épaisseur de la paroi : 2,5-4 mm
Méthode de moulage :
Le moulage sous pression permet souvent d'obtenir des surfaces lisses avec de petites piqûres de surface, ce qui signifie que la surface est vraiment lisse au toucher.
Importance :
Il permet à la voiture de conserver sa pression d'huile et de maintenir un système de refroidissement efficace. Il contribue également à leur donner une belle apparence et à aider les gens à reconnaître la marque.
4. Supports de guidon et triples pinces
Fonction :
Ces pièces relient la colonne de direction aux fourches et contribuent à les soutenir.
Matériau :
- Moulage sous pression d'aluminium (A356 ou A380)
- Limite d'élasticité : ~200-250 MPa
- La durée de vie en fatigue a été testée jusqu'à 100 000 fois sous différentes charges.
Détails du casting :
- Exiger une grande précision dimensionnelle
- Un traitement thermique peut être effectué après la coulée pour améliorer la ductilité de la pièce.
- Les roulements de direction doivent être montés avec des tolérances de 0,02 mm.
5. Boîtiers d'étriers de frein
Fonction :
Le piston de râteau et les canaux de liquide de frein contribuent à l'alimentation des freins.
Matériau :
- Aluminium à haute résistance (A413 ou ADC12 modifié)
- Doit résister à la pression élevée de l'eau (100 à 120 fois plus que la pression normale de l'air).
- Haute résistance à la corrosion car il peut supporter le contact avec les déchets sur la route et l'humidité.
Considérations relatives au moulage :
- Les canaux internes du fluide ne doivent pas présenter de défauts susceptibles d'entraver la circulation du fluide.
- Des tests d'étanchéité doivent être effectués sur chaque lot de produits.
- L'étanchéité des pistons dépend fortement de la finition de la surface.
6. Supports de repose-pieds et supports latéraux
Fonction :
Soutenir le poids du conducteur et stabiliser le motocycle lorsqu'il est garé.
Matériau :
- Alliages combinant l'aluminium et le silicium pour les rendre plus résistants à l'usure
- Résistance à la traction : ~180 MPa
- Dureté : ~80-100 HB
Méthode de moulage :
Le moulage en coquille par gravité ou à basse pression est utilisé lorsque vous avez besoin d'une surface plus belle et moins susceptible de se briser.
7. Composants du bras oscillant (sur certains modèles)
Fonction :
Soutient la roue arrière et l'aide à se déplacer vers le haut et vers le bas.
Matériau :
- Parfois en aluminium résistant, fabriqué à l'aide de matrices (A356-T6).
- Limite d'élasticité après traitement : ~240 MPa
- Épaisseur de la paroi : 4-6 mm, en fonction des chemins de charge
Notes de casting :
- L'analyse par éléments finis est utilisée pour la répartition des contraintes
- Soudage ou usinage post-coulée pour les roulements.
Tableau récapitulatif des principales pièces moulées sous pression
Nom de la pièce | Matériau | Fonction | Tolérance | Température de fonctionnement |
Carter | A380/ADC12 | Maisons vilebrequin et engrenages | ±0,05 mm | 80-120°C |
Culasse | LM6/ADC12 | Joint d'étanchéité de la chambre de combustion | ±0,03 mm | Jusqu'à 250°C |
Couvercles de moteur | A360/A380 | Protège les composants internes | ±0,1 mm | Ambiant-90°C |
Corps d'étrier de frein | A413/ADC12 | Soutient le système de freinage | ±0,02 mm | 0-120°C |
Supports de guidon | A356/A380 | Maintient la structure de direction | ±0,02 mm | Ambiant |
Supports de repose-pieds | LM6/A360 | Soutien aux cavaliers | ±0,1 mm | Ambiant |
Chacune de ces pièces de fonderie est importante car elle contribue au bon fonctionnement des motos, à leur sécurité et à leur résistance aux pannes. Les ingénieurs passent beaucoup de temps à s'assurer que les pièces ont la bonne forme, qu'elles sont très légères mais suffisamment résistantes pour le travail, et cela se fait principalement à l'aide du processus de moulage sous pression de l'aluminium.
Paramètres du processus de moulage sous pression
A. Pression d'injection
Dans le cas du moulage sous pression, la pression utilisée est de l'ordre de 200 à 1000 livres par pouce carré, ce qui permet au métal de se déplacer rapidement dans le moule et de s'assurer qu'il n'y a pas trop de bulles d'air dans la pièce.
B. Température du moule
Les températures typiques des moules se situent généralement entre 180 et 300 degrés Celsius et sont régulées par des canaux de refroidissement afin de s'assurer que le métal refroidit et durcit de manière homogène.
C. Durée de remplissage
Si vous injectez le moule dans les 0,1 secondes pour les petites pièces, vous éviterez les fermetures à froid et lisserez la surface.
D. Post-traitement
Après le moulage, les pièces subissent :
- Coupe des glissières et des évents
- Grenaillage ou tonnelage
- Usinage pour les dimensions critiques
- Les traitements de surface tels que l'anodisation ou le revêtement en poudre permettent de protéger les pièces métalliques et de leur donner un meilleur aspect.
Ces étapes sont importantes car elles permettent de s'assurer que les pièces fonctionnent bien et s'emboîtent parfaitement sur un vélo de course.
Défauts de coulée courants et solutions
Malgré ses avantages, le moulage sous pression peut entraîner des problèmes au niveau des pièces coulées si l'on n'y prend pas garde.
Défauts typiques :
Type de défaut | Cause | Solution |
Porosité | Piégeage de l'air ou rétrécissement | Coulée assistée par le vide, gating approprié |
Fermeture à froid | Faible température du métal | Augmenter la température de fusion à 660-700°C |
Flash | Pression excessive ou matrice usée | Maintenir la force de serrage correcte |
Remplissage incomplet | Vitesse d'injection insuffisante | Augmenter la pression ou optimiser les vannes |
Il est important d'assurer le contrôle de la qualité des pièces moulées pour automobiles afin qu'elles puissent être utilisées en toute sécurité.
Avantages du moulage sous pression pour les motos
- La précision des outils et des machines permet d'éviter un traitement ultérieur aussi important.
- Il est possible de fabriquer des milliers de pièces identiques en utilisant une seule matrice pour la production de masse.
- Le moulage sous pression de l'aluminium permet de réduire le poids des composants.
- Une bonne conductivité thermique permet un meilleur refroidissement du moteur.
- Plus rapide et moins coûteux que la production de pièces à partir d'une billette.
Étude de cas : Fabrication de carter
Le carter est important pour toute moto car il protège le vilebrequin et la transmission. En général, on utilise le moulage sous pression pour produire un carter standard.
- Température de fusion : 675°C
- Température du moule : 250°C
- Pression d'injection : 70 MPa
- Durée du cycle : 60 secondes
- Tolérance : ±0,05 mm
- Traitement thermique : T6 pour améliorer les propriétés mécaniques
Les composants de précision augmentent les performances du moteur tout en allégeant sa charge et en économisant du carburant.
Dernières tendances en matière de moulage sous pression de motocycles
- Motos électriques : De plus en plus de personnes demandent des housses légères pour les batteries et les moteurs.
- Alliages de magnésium : Bien qu'il coûte plus cher, le magnésium pèse encore moins lourd.
- Contrôle de qualité automatisé : Les outils d'IA sont utilisés pour identifier les problèmes de moulage en temps réel.
- Matrices imprimées en 3D : Développement plus rapide d'échantillons et réduction du temps de préparation des outils.
La technologie AW déterminera l'efficacité et la conception des composants des motocycles à l'avenir.
Conception de moules pour pièces de motocycles
Les performances et la durée de vie des pièces moulées sous pression dépendent en grande partie de la conception de la matrice. Dans la fabrication des motos, les matrices sont conçues pour répondre aux besoins spécifiques de chaque modèle.
Par exemple, on peut rencontrer des géométries complexes, telles que des carters contenant des canaux d'huile.
- Sections à parois minces (de 1,5 à 3 mm d'épaisseur)
- L'utilisation d'évents et de vannes pour éliminer les défauts de moulage
- Des conduites de refroidissement dans la filière permettent de réguler la température.
La fabrication d'une matrice pour une culasse de moto coûte généralement entre $15 000 et $40 000 et peut produire plus de 100 000 pièces avant que l'usure ne réduise la précision des pièces.
Utilisation d'alliages technologiques dans le moulage sous pression de l'aluminium
Les besoins mécaniques et thermiques des pièces d'un moteur de moto déterminent le choix des alliages d'aluminium utilisés.
Alliages courants :
Alliage | Propriétés principales | Application |
A380 | Haute résistance, bonne fluidité | Carters, couvercles de moteur |
ADC12 | Bonne usinabilité et résistance à la corrosion | Culasses |
LM6 | Excellente coulabilité, non corrosif | Pièces détachées non structurelles pour motocycles |
Ils présentent tous certains avantages, notamment une forte conductivité thermique et une résistance à la fatigue. À titre d'exemple, l'A380 a une conductivité thermique de près de 96 W/m-K, ce qui permet d'évacuer rapidement la chaleur du moteur.
Travailler avec les outils et les entretenir dans le domaine de la fonderie sous pression
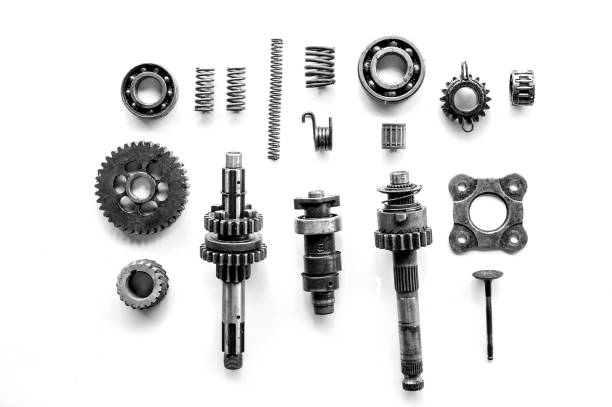
Arrière-plan de vieilles pièces de motocyclettes en noir et blanc. réparation et entretien de vieilles pièces de moteur.
Avec un nombre élevé de pièces automobiles moulées, une attention particulière doit être accordée à la maintenance de l'outillage :
- Polissage de la matrice tous les 10 000 tirs
- Veillez à chauffer les pots à environ 200°C avant de les utiliser afin d'éviter les changements brusques de température.
- Vérifiez régulièrement s'il y a des signes d'endommagement, car ils peuvent entraîner des défauts tels que des bavures et des pièces de moule mal alignées.
Aujourd'hui, les machines gèrent l'application des agents de démoulage et aident à contrôler la température des matrices d'un cycle à l'autre, ce qui permet d'obtenir des produits finis plus homogènes.
Impact environnemental et économique
Avantages pour l'environnement :
- Le moulage sous pression de l'aluminium permet de recycler jusqu'à 95% du matériau, ce qui réduit les émissions de carbone.
- Ils permettent d'économiser environ 30% d'énergie par rapport aux anciens types de systèmes.
Considérations économiques :
- Les outils de moulage sous pression étant coûteux, la quantité de pièces fabriquées permet d'obtenir un coût très faible pour chacune d'entre elles.
- La plupart des pièces de moteur de moto fabriquées par moulage sous pression sont jusqu'à 40% moins chères que celles fabriquées par usinage.
- Grâce au moulage sous pression, la fabrication moderne de motocycles peut être à la fois rentable et respectueuse de l'environnement.
Assurance qualité dans le processus de fabrication
Les fournisseurs de pièces de moto OEM doivent appliquer les normes ISO 9001:2015 et IATF 16949. Les contrôles de qualité courants comprennent :
- La technologie des rayons X permet de vérifier si l'intérieur du métal est poreux
- Confirmer les mesures exactes des pièces à l'aide de machines à mesurer tridimensionnelles (MMT).
- Tester les zones du moteur qui doivent être étanches
- Utilisation de l'eau salée pour vérifier les propriétés de résistance à la corrosion des pièces détachées pour motocycles
L'utilisation de normes permet de s'assurer que les pièces répondent à la fois aux besoins mécaniques requis et aux exigences de sécurité dans les applications à haute performance.
Capacité à travailler avec l'usinage CNC et les traitements de surface
Les pièces moulées sous pression sont presque prêtes, mais à certains endroits (comme les sièges de roulements ou les trous de filetage), l'usinage CNC est encore nécessaire pour garantir une grande précision.
Les étapes de post-traitement comprennent également :
- Revêtement en poudre pour la résistance à l'usure
- Anodisation pour la protection contre la corrosion
- La vibration et le culbutage sont utilisés pour rendre la surface plus attrayante.
Par conséquent, ces pièces sont parfaites pour une utilisation immédiate sur les chaînes de production.
Rôle dans la performance et la sécurité
Le moulage sous pression est essentiel dans de nombreuses industries.
- Réduire le poids : Les composants fabriqués à partir d'aluminium plus léger sont meilleurs pour la consommation de carburant et la maniabilité de la voiture.
- Gestion de la chaleur : En offrant une meilleure conductivité thermique, la chaleur est transférée efficacement de votre moteur, ce qui élimine les risques de surchauffe.
- Sécurité structurelle : Si le moulage automobile est parfait, les supports de guidon et de repose-pieds peuvent être plus résistants en cas de collision.
Même si le boîtier de l'étrier de frein n'est décalé que de 0,1 millimètre, cela peut entraîner une fuite de liquide de frein, ce qui prouve à quel point une bonne qualité est essentielle pour la sécurité des motocycles.
Les défis du moulage sous pression des motocycles
Voici quelques-uns des défis auxquels l'industrie est confrontée :
- Réduction des défauts de moulage dans le processus de prototypage rapide
- La hausse des prix de l'aluminium, due à la demande mondiale, entraîne une raréfaction de l'offre.
- Essayer de maintenir la force tout en gardant le fil léger
- L'épuisement des pièces à cause des températures élevées et des cycles rapides.
Les experts de l'industrie étudient de meilleurs matériaux pour les moules, des revêtements avancés (comme la nitruration) et des simulations de moulage assistées par ordinateur pour résoudre ces problèmes.
L'avenir : Fonderies intelligentes et industrie 4.0
À l'avenir, les amateurs de motos verront probablement ces éléments avec :
- Les jumeaux numériques peuvent être utilisés pour surveiller les conditions de moulage à tout moment.
- Utilisation de capteurs qui repèrent et corrigent automatiquement les problèmes de moulage
- La fabrication additive (impression 3D) peut faciliter et accélérer la production d'inserts de matrices complexes.
- Inclure l'énergie verte dans les usines de moulage de métaux
L'essor des commandes électroniques et des moteurs à batterie dans la conception des motocycles augmentera le besoin de pièces moulées sous pression de pointe dans l'industrie.
Comparaison : Moulage sous pression et autres méthodes de fabrication
Le succès des pièces de moteur de moto dépend en grande partie du choix de la méthode de fabrication appropriée. Voyons comment les pièces moulées sous pression se comparent aux autres procédés :
Nous allons établir une comparaison entre le moulage sous pression et le moulage en sable.
Paramètres | Moulage sous pression | Moulage au sable |
Précision dimensionnelle | ±0,05 mm | ±0,5 mm |
Finition de la surface | Excellent (Ra 1,6-3,2 µm) | Moins bonne (Ra 6,3-25 µm) |
Volume de production | Volume élevé | Faible à moyen |
Coût de l'outillage | Élevé (~$20 000 par jour) | Faible (~$1 000 par moule) |
Défauts de coulée | Plus bas (environnement contrôlé) | Plus élevé (porosité du gaz, inclusions) |
Pour les prototypes et le moulage de grosses pièces, le moulage en sable est moins onéreux ; le moulage sous haute pression est plus adapté à la fabrication de nombreuses pièces pour l'automobile.
Moulage sous pression et forgeage
Bien que les pièces forgées soient solides grâce à leur structure de flux de grains, elles sont moins complexes et offrent une moins bonne finition que le moulage sous pression de l'aluminium. Pour les pièces qui ne supportent qu'une charge moyenne, le moulage sous pression est une option meilleure et moins coûteuse que les autres méthodes.
Optimisation de la conception pour le moulage de pièces de motocycles
Les ingénieurs utilisent l'analyse par éléments finis (FEA) et la dynamique des fluides numérique (CFD) pendant la conception pour s'assurer qu'une pièce est solide, légère et abordable.
Les optimisations comprennent :
- Renforcement de la force grâce aux côtes, mais faible perte de masse musculaire
- Epaisseur uniforme de la paroi (typiquement 2-3 mm)
- Laissez un angle de tirage de 0,5 à 2 degrés pour faciliter le dégagement de la matrice du jeu de matrices.
- Vous aurez également besoin de bossages et de tampons à l'endroit où vos charges rejoignent la remorque.
- Il est très important de concevoir des composants aussi précis, en particulier pour les motos de sport et de course.
Refroidissement des moules de coulée sous pression
Il est important de réguler la conductivité thermique de la matrice pendant la coulée afin de maintenir la précision des dimensions. Pour ce faire, il faut
- La matrice comporte des canaux de refroidissement conformes.
- Dans les zones chaudes, on utilise des chicanes thermiques (baffles).
- Chaque coup est pulvérisé par la machine afin d'uniformiser le chauffage.
Vous devez veiller à ce que la température de la matrice soit comprise entre 180°C et 300°C. Une surchauffe du métal peut provoquer une fatigue thermique et entraîner des défauts lors de la coulée, tels que des déchirures à chaud ou des soudures.
Les avantages et les inconvénients du moulage sous pression utilisé dans la fabrication des motocyclettes
Voyons maintenant combien coûterait la fabrication d'un composant de moto de taille moyenne tel qu'un capot latéral de moteur (environ 1,2 kg d'aluminium) :
Poste de coût | Valeur approximative (USD) |
Outillage (amorti) | 0.50 |
Matériau en aluminium | 2.70 |
Énergie (four électrique) | 0.45 |
Main-d'œuvre et manutention | 0.40 |
Post-traitement | 0.60 |
Coût total par pièce | ~$4.65 |
Comparez cela à l'usinage de barres ($8.50 par pièce) et vous comprendrez facilement pourquoi le moulage sous pression peut vous faire économiser de l'argent. Pour toute production de plus de 50 000 unités de pièces détachées de motos, le moulage sous pression est le processus le plus abordable.
Assurer les certifications et la traçabilité dans le moulage sous pression des motocycles
Les pièces moulées sous pression doivent être traçables pour tous les lots traités par les fournisseurs OEM. Cela implique
Sérialisation des pièces
- Administration des réactifs (substances, point de fusion et tout ce qui est impur)
- Enregistrement de la température et de la pression (fusion, injection et matrice)
- Essais destructifs et non destructifs
Vous devez utiliser les normes ISO 9001, TS 16949 et, dans certains cas, AS 9100 pour les pièces entrant dans le moteur de la moto, comme les culasses et les couvercles de transmission.
Intégration à d'autres processus de fabrication
Le moulage sous pression ne peut se faire seul. Le processus comprend des initiatives dans la fabrication des motos.
- Soudage (par exemple, pour les supports de montage)
- Usinage (alésage, filetage, dressage)
- Les utilisateurs peuvent traiter les feuilles à la chaleur (exfor ample T6) pour augmenter leur résistance.
- Lignes d'assemblage (robotisées ou manuelles)
Un exemple automatisé pourrait être un carter d'engrenage moulé sous pression :
- Moulage (A380 en aluminium)
- Alésage CNC (siège de roulement)
- Le revêtement par poudre protège les pièces usinées de l'usure et de la corrosion.
- Les roulements à rouleaux et les joints d'huile sont utilisés pour l'assemblage.
Cette méthode met en évidence le rôle que joue la fonderie automobile dans l'ensemble de l'industrie.
Conclusion
Les moteurs de moto et les pièces détachées sont mieux formés par le moulage sous pression que par d'autres méthodes en raison de leur grande précision et de l'aspect superbe du produit final. De l'utilisation de moulage d'aluminium sous pression, les fabricants obtiennent une grande précision des dimensions, une bonne capacité à transférer la chaleur et une grande résistance par rapport à leur poids. Si des défauts de moulage peuvent survenir, ils sont faciles à corriger grâce au contrôle du processus et à des techniques avancées telles que le moulage sous haute pression. L'augmentation de la demande de motos plus performantes et plus économes en carburant rendra encore plus importante l'importance des pièces moulées sous pression dans l'industrie de la moto à travers le monde.
FAQ
Pourquoi les pièces produites par moulage sous pression de l'aluminium sont-elles spéciales pour les motos ?
Les pièces produites par le moulage sous pression de l'aluminium sont légères, résistantes à la chaleur et solides. Elles permettent de créer des pièces compliquées qui doivent s'ajuster étroitement les unes aux autres.
Quelles sont les pièces des motos fabriquées par le procédé de moulage sous pression ?
Les différents produits moulés sous pression comprennent les carters, les culasses, les couvercles de moteur, les étriers de frein et les pièces pour les supports de guidon.
Quelles sont les stratégies utilisées pour garantir la qualité supérieure de certaines pièces de motocycles ?
La température, le moulage sous vide et les inspections comprenant des rayons X et des mesures de pression sont autant d'éléments qui permettent de garantir la qualité.
En quoi le moulage sous pression est-il plus performant que les autres procédés ?
Cette méthode permet d'obtenir une surface plus lisse, une plus grande précision, un travail plus rapide et de réduire le coût unitaire lors de la production de nombreuses pièces similaires.
0 commentaires