Nagynyomású öntés hasonló a dongó repüléséhez; mindkettő elméletileg lehetetlen. A több mint 150 éves hatékony működés azonban - egyre növekvő termelékenységgel és alkatrészminőséggel - bebizonyította, hogy a nyomásos öntés eredendően robusztus és képes a folyamatok magas szintjének elérésére. Még a legjobban működő üzemekben is előfordulnak selejtek, és az alábbiakban a cink nyomásos öntvényeknél felmerülő hibák diagnózisát, okait és kezelését tárgyaljuk, ezek a kérdések mindegyike azonos az alumínium és magnézium nyomásos öntvényeknél is.
A hibákat többféleképpen lehet rendszerezni a téma következetes kezelése érdekében. Ebben a cikkben lépésről lépésre haladva közelítünk az ötvözetből készült ingot átvételétől a késztermék elküldéséig, és minden egyes hibatípusról azon a ponton mutatunk be információkat, ahol az előfordul. A hibák azonosításának egyéb módszereiről és a különböző hibakereső rendszerekről később lesz szó. A folyamat egyes szakaszai az alábbiakban vannak felsorolva:
Ezenkívül a futóelemeket és a törmeléket különböző fázisokban újrahasznosítják, és figyelembe kell venni a folyamatok közötti tárolást és kezelést. Nem minden öntvény megy át minden eljáráson.
Cinkötvözet Ingot specifikációk:
A cinköntött ötvözetek összetételét 75 év alatt módszeresen fejlesztették ki. Az ötvözőelem-tartományokat összehangolták, és gondosan meghatározták a veszélyes szennyezőanyagok maximális értékeit. A megbízható öntvények előállításához olyan ingotokat kell használni, amelyek megfelelnek a nemzetközileg elfogadott követelményeknek. Továbbá az ötvözet minőségét az olvasztási és öntési műveletek során fenn kell tartani, hogy az öntött alkatrészek megfeleljenek az öntési összetételi kritériumoknak.
Az egyes ötvözettípusok esetében az ingot (1. táblázat) és az öntvény (2. táblázat) szabványai közötti kisebb eltérések célja, hogy megfelelően figyelembe vegyék a rendszeres feldolgozási és újrahasznosítási folyamatok által okozott eltéréseket. A nem szabványos, különösen az olyan erősen mérgező szennyeződésekkel, mint az ólom, az ón vagy a kadmium, terhelt rudak használata soha nem igazolható.
Az ötvözeteket három családba sorolják: A 4% alumíniumötvözetek (Zamak 3 és 5, valamint a 2. és 7. számú), a magasabb alumíniumtartalmú ZA ötvözetek (8., 12. és 27. számú), valamint a rézötvözetek (A cu cink 5 és 10).
Ezenkívül bizonyos más ötvözeteket nem fogadtak el a kereskedelemben. Majdnem minden cinkötvözetből készült öntvényt Zamak No3 vagy No5 anyagból gyártanak, más anyagokat csak akkor, ha különleges tulajdonságokra van szükség.
A szennyeződés hatása
A szennyező elemek, például az ólom öntvényekre gyakorolt hatása az összes ötvözet esetében hasonló. A feltüntetett specifikus szennyezőanyag-maximumok tükrözik a hatás változó súlyosságát, valamint azt, hogy milyen könnyen gyárthatók ingotok alacsony nyomelem-szintekkel.
Ólom, ón és kadmium
Ezek az elemek a hasonló, de kevésbé gyakori indiummal és talliummal együtt katasztrofális meghibásodást okozhatnak szemcseközi korrózió révén. "A szennyeződések a szemcsehatárokra szegregálódnak, elősegítve a szemcseközi korróziót, különösen meleg, nedves környezetben. Az öntvények megduzzadnak és felbomlanak, szürke porhalmokat eredményezve (l. ábra).
Ha a magnéziumszintet a minimumok felett tartják, a hatás nem jelentős az olyan öntvények esetében, amelyek az előírt maximumokig tartalmazzák ezeket a szennyező anyagokat. A megelőzési módszerek közé tartozik a megfelelő öntvényvásárlás és a helyes háztartásvezetés az újraolvasztásból vagy az üzemi környezetből, például a forrasztásból származó szennyeződések elkerülése érdekében.
Vas
A vas csak kis mértékben oldódik a cinkben, és a felesleges vas az ötvözet alumíniumával egyesülve az intermetallikus vasaluminid-komplexet (FeAl3) hozza létre. Ez a vegyület rendkívül kemény, és ha az öntvénybe kerül, megmunkálási problémákat, túlzott szerszámkopást és polírozási problémákat okozhat, mivel a részecskék felállnak vagy kiszakadnak. A túlzott mennyiség korlátozhatja az ötvözet folyékonyságát, és ezáltal a szerszámok kitöltésének képességét. Végül, ha az anyag a terhelt helyeken koncentrálódik, csökkenhet a szilárdság és a képlékenység. Bizonyított, hogy a részecskék mérete, és nem a teljes mennyiség határozza meg a megmunkálhatóságot, mivel a vas az olvasztótégelyből származik. A legfontosabb védelem a fém hőmérsékletének kordában tartása.
Nikkel, króm, mangán és szilícium
Ezeknek az összetevőknek a túlzott mennyisége ugyanolyan hatással van az öntvényre, mint a felesleges vas. Meg kell jegyezni, hogy a nikkel nem szennyező anyag a 7. számú ötvözetben; a megadott kis mennyiség (az oldhatósági határértéknél kevesebb) inkább szándékos hozzáadás, hogy csökkentsék a szemcseközi korróziót ebben a magnéziummentes, nagy folyékonyságú ötvözetben.
Az ötvözőelemek hatása
Alumínium
Az acuzinkötvözetek kivételével az alumínium a leggyakoribb ötvözőelem. Az ötvözetek szilárdsága és önthetősége egyaránt attól függ, hogy az ötvözetek szintje a specifikáción belül van-e. A tulajdonságok gyorsan változhatnak a megadott nagyon korlátozott tartományokon kívül, különösen a 2., 3., 5. és 7. cinkötvözetek esetében.
A 4%Al ötvözetekben a felesleges alumínium jelentősen csökkenti az ütőszilárdságot (2. ábra), ezért a feldolgozás során nem szabad alumíniumot felvenni. Ha az alumíniumszint az előírt minimum alá csökken, a hatások kevésbé észrevehetőek. A lehetséges következmények közé tartozik a forró szakadásra való hajlam, ami csökkenti a szilárdságot, a csökkent folyékonyság és az ötvözet fokozott hajlama a szerszámhoz való tapadásra (forrasztás).
Az alumíniumtartalom változása kevésbé érezhető hatással van a magasabb alumíniumtartalmú ZA ötvözetek jellemzőire, ami szélesebb tartományokat tesz lehetővé. A 4% ötvözetekhez hasonlóan azonban az összetételeket is úgy optimalizálták, hogy a jellemzők optimális kombinációját biztosítsák, és a határértékek túllépése olyan módosításokat eredményez, amelyek károsak lehetnek.
Magnézium
Bár a magnézium hozzáadása erősítő hatású, elsődleges célja az ólmot, ónt és más fémeket tartalmazó ötvözetekben a megengedett maximális szintig terjedő szemcseközi korrózió megakadályozása. A tartományi minimumnál kevesebb magnéziumot tartalmazó öntvények üzem közben korrodálódhatnak. A megengedett tartományt meghaladó magnéziumszint forró szakadást okozhat, ami szilárdságvesztést vagy bevonatolási nehézségeket eredményezhet. A magas magnéziumtartalom csökkenti az ötvözet folyékonyságát, ami töltési problémákat okozhat.
Réz
A réz hozzáadása a 4%Al alapötvözethez növeli a szilárdságot és a keménységet a képlékenység rovására, és az ötvözetek az öregedés során jobban változtatják a méretüket. A magas réztartalmú ötvözetek ütőszilárdsága szintén csökken az öregedéssel. Ennek eredményeképpen a rézzel kapcsolatos korlátozásokon kívül eső ötvözetek tulajdonságai a meghatározott ötvözetekhez képest köztes tulajdonságokkal rendelkeznek.
A ZA ötvözetek rézkomponense jelentős hatással van a mechanikai tulajdonságaikra. Általánosságban elmondható, hogy a magas réztartalom csökkenti a képlékenységet, míg az alacsony réztartalom a szakítószilárdságot.
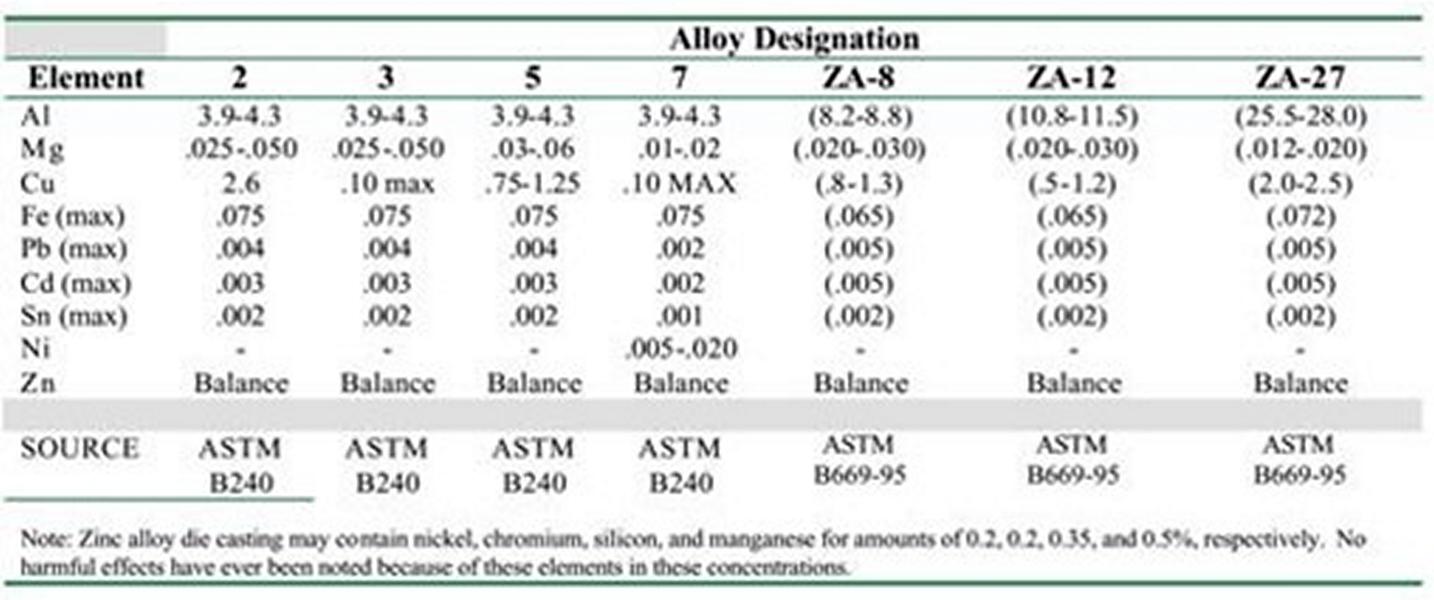
1. táblázat. A CINK NyOMÓSZERŰ ÁTALAKOZÁSI ALKALMAZÁSOK INGOT HATÁRÉRTÉKÉNEK GOMPOSZITÁSA, Súly szerint.
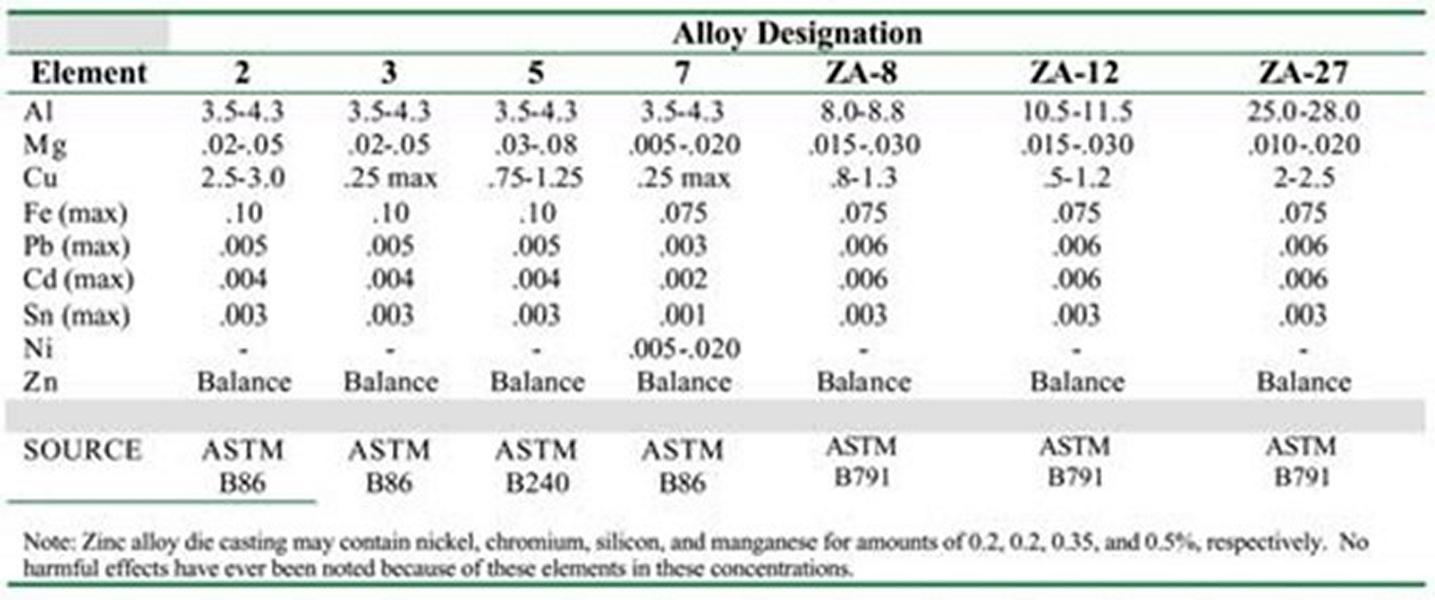
2. táblázat. A CINK NyOMÓSZERŰ ÁTALAKOZÁSI ALKALMAZÁSOK GOMPOSZITÁSA ÁTALAKOZÁSI HATÁRÉRTÉKEK, MÉRLEGESEN
Az acuzinkötvözetekben a fő ötvözőanyag a réz, amely nagyobb keménységet és magas hőmérsékleti szilárdságot biztosít, mint más cinkalapú ötvözetek. Az Acuzinc ötvözetek relatív réz- és alumíniumtartalmát a tulajdonságok és az önthetőség egyensúlya érdekében optimalizálták. Mivel a magas rézszint egy különálló fázisrendszerben fordul elő, annak hatása a méretbeli öregedésre gyakorolt változásra eltérhet a 4%Al ötvözeteknél tapasztaltaktól.
Fémolvasztás, átvitel és tartás
A ZA-12, ZA-27 és Acuzinc10 ötvözetek kivételével, amelyek elfogadhatatlanul nagy mértékben támadják a vasat és az acélt, a cinkötvözetek megolvaszthatók és fémtartályokban tárolhatók. Ez a tulajdonságuk lehetővé teszi, hogy forrókamrás eljárással öntsék őket, amely merített befecskendező rendszert alkalmaz.
Ez az értékes tulajdonság azonban csak szigorú hőmérséklet-szabályozással érhető el. Körülbelül 450 °C alatt a cinkötvözet elég lassan oldja a vasat ahhoz, hogy az ötvözettel érintkező fém alkatrészeket használni lehessen. Mivel a reakció sebessége exponenciálisan nő a hőmérséklettel, ezért érzékeny a szerény hőmérséklet-ingadozásokra.
A reakció az ötvözetben lévő alumínium és a tégelyben és a gépalkatrészekben lévő vas között játszódik le.
Alumínium + vas > Intermetallikus részecske
3Al + Fe > FeAl3
A vas-aluminid-intermetallikus anyag felúszik a felszínre, és az oxidréteggel reakcióba lépve salakot hoz létre. Ha a korpa bekeveredik a fémbe, vagy ha az edény szintje olyan alacsonyra csökken, hogy a felszín alatti fém beszívódik a libatömlőbe, az öntvény kemény részecskéket tartalmaz, ami a szennyeződéseknél a vas alatt feltüntetett hibákat eredményezi.
A túl magas hőmérséklet szintén magnéziumveszteséget okoz, mivel ez egy illékony elem, amely szétfő. Az alacsony magnéziumtartalom jelentős korróziós nehézségeknek teszi ki az öntvényt a használat során.
Érdemes megjegyezni, hogy az olvadék teljes hőmérséklete nem az egyetlen figyelembe veendő tényező. Ha a kemencében van egy forró pont, például egy rosszul kalibrált égő, a magas hőmérséklet vasfelvételt okoz. Súlyos körülmények között a tégely átrághatja magát, ami kifutáshoz vezethet.
Ajánlott fém casting hőmérsékletek vannak:
Zamak No 2,3,5,7 |
415-4S0°C |
ZA8 |
420-445°C |
ZA12 |
465-495°C |
ZA27 |
550-580°C |
Acuzinc 5 |
~ 480°C |
Acuzinc 10 |
~ 5S0°C |
A ZA ötvözetek, különösen a ZA-27 olvasztásakor a gravitáció hatására alumíniumban és cinkben gazdag rétegekké válnak. A függőleges keverés elkeveri az olvadékot; az erős keverést kerülni kell, mivel az elősegíti az oxidációt. Ha az olvadék egyszer már elkeveredett, akkor az olvadéknak egyenletesnek kell maradnia. Kritikus, hogy a keletkezett salakréteg ne feltételezhetően leváljon és ne keverjük be. A ZA-27-et nem szabad 540 °C alatt tárolni, mert az oldatban lévő vas masszív intermetallikus részecskék formájában kicsapódik.
A specifikációnak megfelelő ingotok olvasztása és tárolása problémamentes lehet mindaddig, amíg megfelelő hőmérséklet-szabályozást tartanak fenn, és nem történik véletlen szennyeződés. A futók és a törmelék újraolvasztásakor különböző szempontokat kell figyelembe venni.
A visszajuttatásokat szigorúan el kell különíteni, különösen azokban az üzletekben, amelyek alumíniumötvözeteket is olvasztanak. Egyes alumínium kifutók keveredése a 4% cinkötvözetekkel magas alumíniumtartalmú öntvényeket eredményez, amelyek így törékennyé válnak. Ugyanez a probléma lép fel, ha a ZA ötvözetet normál ötvözettel kombinálják.
A forgács, a pernye és más könnyű, a felülettel szennyezett anyag közvetlen újraolvasztása túlzott salakanyagot termel, és szennyeződéseket vehet fel. Az ilyen anyagokat célszerű külön kezelni, hogy az újraolvasztott ingot összetételét meg lehessen határozni. A salakot azonos okokból külön kell kezelni. A fluxus hajlamos magnéziumot kivonni, különösen a fém felmelegítésekor. A galvanizált öntvények különleges figyelmet igényelnek. Az olvasztás során a galvanizáló bőr a felszínen marad, és le lehet hámozni. A lemezt nem szabad széttörni és az olvadékba keverni, mert különösen a nikkel kemény foltokat hozhat létre.
Az olvasztás és az öntés során az ötvözet kis mennyiségű magnéziumot (elpárolgás útján) és alumíniumot (a vassal való kölcsönhatáson keresztül, majd salak formájában történő eltávolítással) veszít. Ugyanannak a fémnek a folyamatos újraolvasztása végül a specifikációtól eltérő öntvényeket eredményezne. A No3 ötvözeten végzett vizsgálatok azt mutatták, hogy hét ciklusra van szükség ahhoz, hogy a magnézium a megadott szint alá csökkenjen. Ennek az esetleges romlásnak az elkerülése érdekében a folyamatba folyamatosan új öntvényt kell juttatni.
Hibák a cink öntésnél
Az alábbiakban felsorolt gyakori hibák cink öntvény, az alumínium öntvények, magnézium öntvények esetében nagyjából ugyanazok a problémák merülnek fel, mint a cinköntésnél,
Belső Hibák a cink öntvényben
Zsugorodás Porozitás
Ahogy az ötvözet folyékonyból szilárddá válik, az öntvény térfogatának több százalékával zsugorodik. Üreg képződik, ha nem áll rendelkezésre további folyékony fém a zsugorodáshoz. Ez a zsugorodó porozitás. Gyakran elszigetelt nehéz részekben, hatalmas szabálytalan lyukak formájában jelentkezik (S ábra), de előfordulhat interdendritikus, repedésszerű formában is, különösen a hosszú fagyasztási tartományú ötvözetekben, mint például a ZA-27 és az Acuzinc.
A belső porozitás felfedhető, ha az olyan felületeket, mint a peremek vagy furatok, meg kell munkálni, ami selejtet eredményezhet. A porozitás a megmunkálási folyamatok során szerszámkopáshoz és fúró elsodródásához is vezethet. A szilárdságra gyakorolt hatást a porozitás eloszlása és mennyisége egyaránt meghatározza. Fontos emlékeztetni arra, hogy az ötvözetekre megadott "könyv szerinti" szilárdsági értékeket tipikus porozitású mintákon érték el.
A zsugorodási porozitás korlátozásához növelje a fémnyomást, és győződjön meg arról, hogy a kapu elég vastag ahhoz, hogy a megszilárdulás során aktív legyen. A dugattyú nem kúszhat olyan messzire, hogy elérje a lúdnyak alját, ami a fémre gyakorolt nyomás hiányát eredményezheti. A tömítési időnek elegendőnek kell lennie a teljes megszilárduláshoz; ellenkező esetben a fém a dugattyú visszatérésekor kihúzódik az üregből. A helyi hűtés minimalizálhatja a forró pontokat, és így megakadályozhatja a folyékony fém elszigetelt foltjainak kialakulását, amelyek fagyasztáskor pórusokat hoznak létre.
Az interdendritikus porozitás szivárgáshoz vezethet a nyomásálló alkatrészeknél. Minél hosszabb az ötvözet fagyási tartománya, annál nagyobb a szivárgás valószínűsége. Az alacsony szerszámhőmérsékleten történő öntés megvastagítja az öntőbőrt, és csökkenti a szivárgás lehetőségét. Ezt a folyamatot azonban akadályozhatja, hogy a kívánt felületi megjelenés eléréséhez elég magas szerszámhőmérsékletre van szükség. A szerszámfelület hőmérséklete általában 170 °C és 240 °C között mozog.
Gáz porozitás
Mivel a szerszám gyorsan megtelik, hatalmas mennyiségű gáz szorulhat be. A nagynyomású megszilárdulást követően a gáz kvázigömb alakú buborékokat képez, általában a középvonal körül (4. ábra). A gáz és a zsugorodási porozitás együtt létezhet; ebben az esetben a gáz hajlamos a zsugorodási porozitást lekerekíteni.
A gázporozitás ugyanazokat a hibákat okozza, mint a zsugorodási porozitás, azonban a szivárgás kevésbé valószínű, mivel a gázlyukak ritkán kapcsolódnak egymáshoz. Továbbá a gázporozitás az öntvények hólyagosodásának elsődleges oka. Ha az ötvözet gyenge, a magas hőmérsékletre való hevítés következtében a pórusban lévő óriási gáznyomás elfújhatja a környező fémbőrt. A hűtési idő növelésével és/vagy a szerszám hőmérsékletének csökkentésével csökkenthető a hólyagosodás előfordulása röviddel a kilökés után.
Ideális esetben az üregben rekedt gáz mennyiségét a lehető legkisebbre kell csökkenteni. Ez a lehető legnagyobb első lépcsős löket és a lehető leghosszabb töltési idő alkalmazásával érhető el (miközben szem előtt tartjuk a rövid töltési idők ellentmondásos szükségességét az elfogadható felületi megjelenés elérése érdekében). A szellőzőnyílásokat maximalizálni kell, és megfelelően kell elhelyezni. Előnyös, ha a fröccsenést minimálisra csökkentjük. A porozitás gyakran kisebb problémát jelent, és minden bizonnyal kevesebb hólyagosodást okoz, ha az nem néhány nagy, hanem sok mikroszkopikus pórus formájában van jelen. A kis pórusok kialakulását nagy fémsebességgel lehet elősegíteni; a cél a 40 m/s-os kapuzási sebesség kell, hogy legyen. A vákuumos öntés kiküszöböli ezt a fajta pórusosságot.
Mikroporozitás Hibák az öntvényben
A látható porozitás mellett olyan méretű porozitás is lesz, amely csak mikroszkóppal figyelhető meg. Ez a mikropórusosság, ha hiányzik az öntőbőrből (mint ahogy gyakran előfordul), nincs negatív hatással, kivéve, ha később, a felület bevonása előtti polírozási folyamatok során feltárul.
Könnyek and Repedések
A forró szakadások, mint a neve is mutatja, a megszilárdulási tartományhoz közeli hőmérsékleten keletkeznek. A repedést a nagy igénybevételű, kis feszültségű deformáció alatti öntvénytörés okozza, és gyakran egyenetlen mintázatot követ (5. ábra). Ez ellentétben áll a lényegesen egyenesebb repedésekkel, amelyek alacsonyabb hőmérsékleten, nagy feszültség és kis alakváltozás mellett keletkezhetnek. Ezenkívül a törésfelületek megjelenése is változik e kétféle hibatípus között.
Az alkatrész formája jelentősen hozzájárul a forró szakadáshoz. Ez akkor következik be, ha a megszilárdulási zsugorodás egy kis területre korlátozódik, különösen, ha ez a terület egyben forró zóna is. A ZA-27 és az Acuzinc hajlamosabb erre a hibára, mint a többi ötvözet, kivéve, ha alumíniumtartalmuk az előírás alatt van, vagy ha magnéziumtöbbletet tartalmaznak. A szerszámhőmérséklet eloszlásán kívül az öntési paraméterek nincsenek hatással a forró szakadásra. A szerszám forró területeinek hűtése segíthet a probléma megoldásában.
A repedés a kidobás során következik be, amikor az öntvénynek a szerszámban való eltömődése miatt túlzott erő keletkezik. Ez gyakran a szerszámkészítés hibáinak eredménye, amelyek alulvágást, nem megfelelő huzatot vagy villámlást okoztak. A hűtési idő meghosszabbítása, hogy az öntvény keményebbé váljon, és jobban el tudja fogadni a kidobási feszültségeket, segíthet a repedés megelőzésében. Ha azonban az erőt az öntvénynek a szerszámra való kemény zsugorodása okozza, a hosszabb hűtési idő hatástalan, és a hamarabb történő kidobás előnyös lehet.
Befogadási kérdések
Ez a cinkötvözeteknél sokkal kevésbé jelent problémát, mint az erősebb oxidfilmképzőket tartalmazó ötvözeteknél. Valójában gyakran csak a nem megfelelő olvadékkezelés miatt keletkező vas-intermetallikumok okoznak problémát a gyakorlatban. A fém szintje az edényben nem csökkenhet olyan szintre, hogy a felszín alatti fém a lengőnyakba kerüljön.
Die Casting felületi hibák
Arany körök.
Ez a hiba (más néven folyásnyomok vagy hideg folyás) akkor alakul ki, amikor a szerszámmal érintkezve előszilárdult fémáramokat nem olvasztják vissza az öntvény nagy részébe, amikor további fém érkezik. A felület egyenetlen, halpikkely hatású barázdaként jelenik meg, amelynek mélysége a hurok súlyosságától függően változik (6. ábra). A keresztmetszet mutatja a hideg ív meghatározó jellemzőjét, amely az, hogy a felületi törés milyen mértékben folytatódik vízszintesen, és a felszín alatti folytonosságot hoz létre (7. ábra).
A hideg ívek rontják az öntvények megjelenését, és problémákat okoznak a későbbi befejező eljárásokkal, különösen a galvanizálással, ami a bevonat meghibásodásához vezet. Súlyos esetben a hézagok ronthatják az öntvény alakíthatóságát. Az üreg kitöltési ideje és a szerszám hőmérséklete a legfontosabb öntési paraméterek, amelyek befolyásolják a hideg ívek kialakulását. Kevésbé fontos jellemzők az áramlási mintázat, az áramlási távolság, a fém sebessége, a szerszámfelület és a fém hőmérséklete. Az öntvény vastagsága döntő fontosságú. A vékony szelvényű öntvényeknél gyakrabban fordulnak elő ívek.
Meghatározták a felület megjelenése, a falvastagság, a szerszám hőmérséklete és a töltési idő közötti kapcsolatot. A Surface Predictor (8. ábra) segítségével meghatározható a maximális üregkitöltési idő és a minimális szerszámhőmérséklet, amely galvanizálható felületet eredményez. Ha az alkatrészt festeni fogják, hosszabb töltési idő és alacsonyabb szerszámhőmérséklet is elfogadható. A szerszámon lévő texturált felület 50%-vel növelheti a maximális töltési időt.
Néha előfordul, hogy a körök akkor is megjelennek, ha a szerszám forró, és az üreg töltési ideje rövid. általában olyan örvényes áramlási mintázathoz kapcsolódnak, amelyben gáz van csapdába esve. Az ellennyomás, amelyet a gáz a címen. a vége a üreg töltse ki lassítja a a körbeveszi a fém gőzök és ezért a honlapon található. a feltételek szükséges a helyi öles formáció. A oldalon. ez eset, it will legyen szükséges a címre. csökkentse a air csapdába esett a oldalon. a die (lásd porozitásról szóló szakasz), vagy módosítsa a töltésmintát az ilyen körök kialakulásának megakadályozása érdekében.
Laminálás
A laminálás olyan átfedő fémlemezek, amelyek szélesebb területen és egyenletesebb módon terjednek el, mint a cold laps. Ezek akkor keletkezhetnek, ha a gépi befecskendező rendszerrel olyan problémák merülnek fel, amelyek következtében a szerszám impulzusok sorozatában töltődik fel. Lamináció akkor is kialakul, ha az első szakasz lökése túl hosszú, aminek következtében az üregbe belépő első fém lassan mozog és lefagy.
Misrun
Ha a szerszám túl hideg, és a töltési idő túl hosszú, nem lesz teljes öntvény. A fém teljesen megszilárdul, mielőtt az üreg kitöltődne, és ez hibás öntést eredményez (9. ábra). A hiányos öntés kis területeit, pl. a bordák végén vagy az örvények középpontjában, a megrekedt gáz okozhatja, amely megakadályozza, hogy a fém teljesen kitöltse az üreget. Ha a gép lövedékkapacitását túllépjük, akkor a "rövid lövés" hibás befutást okoz.
Lövés vagy fröccsenés
A körökhöz hasonlóan ezek is az előszilárdulás eredményei, de megjelenésük és okuk eltérő. A hiba lehet tisztán felületi, ahol durva textúrát eredményez, vagy lehet beágyazott, mint egy "ötvözet bevonása" (10. ábra). A "lövések" olyan ötvözetgömbök, amelyek a fő fémáramból kiszóródtak, és később nem adszorbeálódtak.
A permet keletkezhet az impulzusból, amikor az első fém átfolyik a kapun, vagy lehetnek a fémáram széléről lepergő örvények. Ezért fordul elő a fröccsenés általában a kapu közelében. Néha a fröccsenés olyan lazán kötődik az öntvényhez, hogy a kilövéskor némi része visszamarad. Ez az anyag azután "zárványokat" képez a következő öntvényben.
A szerszám hőmérsékletének emelése javíthat a helyzeten, de a fő megoldás a kapu módosítása lesz, hogy szilárdabb elülső kitöltést érjünk el.
Ezek a depressziók a oldalon. a casting felület a kevesebb közös a oldalon. cink ötvözet mint a néhány egyéb fémek és sok kevésbé jelent problémát, mint a műanyag idomoknál. Az ok ugyanaz a megszilárdulási zsugorodás, amely a porozitás kialakulásának mozgatórugója. Egy helyi nehéz szakasz inkább felületi süllyedést mutat, mint belső pórust, ha a hőmérséklet-eloszlás olyan, hogy a hőközpont közel van az egyik felülethez. A végső zsugorodás ekkor lehúzza a gyenge szilárd öntőbőrt, hogy mélyedést képezzen (11. ábra).
Az olyan ötvözeteknél, mint a ZA-27, a megjelenés eltérő lehet. Itt a hiba szélesebb területen jelentkezik, és fagyosnak tűnik. A hosszú fagyasztási tartomány megváltoztatta a viselkedést, így a határozott süllyedés helyett a zsugorodás az eutektikus folyadékot lecsapolta a felületről, és az érdes és félig pórusos maradt.
A folyamat orvoslása megegyezik a zsugorodási porozitásnál megadottakkal. Ha lehetséges, az öntvényt át kell tervezni a forró pont csökkentése érdekében.
Tavak
A tó széles lépcső az öntési felületen, amelynek lépcsőmagassága mindössze 5 és S0 mikrométer között van. Nagyon feltűnő a később polírozott és galvanizált alkatrészeken, ahol nem kielégítő hullámosságot eredményez (12. ábra).
A ellenére intenzív vizsgálat, a ok, és ezért a orvosság marad megfoghatatlan. Ott a bizonyíték hogy a kifejezés "tó" két azonos megjelenésű hiba is megadható, de más okból. szelvényezéskor egyes tavak a tó alatt más mikroszerkezetet mutatnak, mint az öntés nagy részében vagy a környező felszínen. Úgy tűnik, hogy az ilyen típusú tavak korai helyi megszilárdulással járnak, és a hideg ívekre alkalmazott gyógymódok jótékony hatásúak lehetnek.
Más tavak azonban nem mutatnak mikroszerkezeti változást. Ráadásul a vékony öntvényeken nem ritka, hogy a hiba vastagságon átívelő, az egyik oldalon mélyedés, a másikon pedig kiemelkedő terület van. Valójában az öntvény néhány tíz mikrométerrel meghajlott. Ez azt jelzi, hogy a tó akkor keletkezett, amikor az öntvény szilárd volt, és csábító a feltételezés, hogy a visszafogott zsugorodás egy ilyen tó kialakulását eredményezi. "olajkanna" torzítás.
Elég egyértelmű, hogy a hiba hővel kapcsolatos, és valószínűleg a szerszámon belüli hőmérsékleti gradienseket tükrözi.
Hólyagok
Ha ezeket a sima felületű kiemelkedéseket felvágjuk, feltárul üreges középpontjuk. A hólyagokat az expanzió okozzaa nagynyomású gáznak az öntvény felszíni bőrét duzzasztó gázpórusokban való csapdázása (1. ábra).3). A hólyagok akkor alakulnak ki, amikor az ötvözet túl gyenge ahhoz, hogy a belső gáz által keltett erőket megfékezze, amikor a az öntés túl forró. A hólyagosodás megelőzhető az öntvény hőmérsékletének csökkentésével a kidobáskor.
Ez a szerszámhűtés növelésével és/vagy a szerszámhűtési idő növelésével érhető el. A hólyagosodás enyhíthető a csapdába esett levegő mennyiségének csökkentésével (lásd a gázporozitásról szóló részt) és a gázpórusok méretének finomítása érdekében nagy kapufordulatszám alkalmazásával.
Repedések
A felületi repedéseknek két fő oka lehet. Az első, a szelvényváltásoknál gyakran előforduló forma a forró szakadás, amelyben az olvadáspont közelében a korlátozó zsugorodás által kiváltott nagy helyi alakváltozás szemcsék közötti töréshez vezetett. A második típus akkor fordul elő, amikor az öntvény megtapad a szerszámban, ami a kidobáskor jelentős nyomást eredményez. Ezek a repedések jellemzően kevésbé intergranulárisak és egyenesebbek, mint a forró szakadások által okozott repedések.
A forró szakadás a hosszú fagyasztási tartományú ötvözeteknél, mint például a ZA-27, jobban megfigyelhető, és elsősorban az alkatrészformának köszönhető. A problémás terület helyi hűtése előnyös lehet. (További információért lásd az ingot fejezetet).
A kilökődési repedéseket kezdetben a szerszámmal kapcsolatos problémák, például az alulmetszések, a nem megfelelő kúposság és a durva felületek eltávolításával kell kezelni. Ha a szerszám hőmérsékletét csökkentjük és a hűtési időt növeljük, az öntvény erősebb lesz, és így jobban ellenáll a kilökődő erőknek. Ha azonban a tapadást az öntvénynek a szerszámra való zsugorodása okozza, például a magcsapba fúródott lyuk, akkor a zsugorodás csökkentése érdekében a korai kidobás előnyös lehet. Ahhoz, hogy elválasztószerként hatékony legyen, a süllyesztékpermetnek megfelelően le kell fednie a süllyeszték felületét.
Drag Márkok
Az öntvény és a szerszám közötti súrlódás az alkatrész kilökésekor a húzási vonal mentén karcolásokat okoz (lásd a 14. ábrát). A húzási nyomokat a nem megfelelő huzat, az alulvágások és a felületi érdesség, valamint a nem megfelelő szerszámpermetezés okozza. Lehetetlen elkerülni a karcolásokat, amikor az öntvény szorosan az alkatrészhez zsugorodik. Ezekben az esetekben a lehető legnagyobb kúposságra van szükség, valamint az öntvény kilövési idejének (hőmérsékletének) optimalizálására.
Torzítás
A hajlított öntvények, a kidobószegek által okozott bemélyedések vagy átütések akkor keletkeznek, ha az öntvény túl gyenge ahhoz, hogy ellenálljon a kidobóerőknek (15. ábra). A szerszámot először is ellenőrizni kell, hogy nincs-e benne alulmetszés, elégtelen huzat és érdes felület. A probléma ezután az öntvény kilökési hőmérsékletének csökkentésével kezelhető. Ez a szerszám hőmérsékletének csökkentésével és/vagy a szerszám hűtési idejének növelésével érhető el.
Erózió
Az erózió kopást és üregeket eredményez a szerszám felületén, ami nyomokat okozhat az öntvényen és kilökődési problémákat. Emellett csökkenti a szerszám élettartamát. Az olvadt ötvözet fizikailag elkoptatja a szerszámot azokon a helyeken, ahol a fémáram nagy sebességgel a szerszámhoz ér. kopás jelentkezhet azokon a pontokon is, ahol a nagy sebességű fém örvénylik és hidraulikus kavitációt hoz létre. Mindkét esetben a fém sebességének csökkentése csökkenti az erózió mértékét. Az erózió a szerszám hőmérsékletének csökkentésével is csökken. Nagyobb valószínűséggel fordul elő olyan szerszámokban, amelyeket a keménységi tartomány lágyabb oldalára edzettek.
Hő Ellenőrzés
Az öntőfelületen megjelenő őrült bordamintázat az öntőforma felületének felszakadásából (hőellenőrzés) adódik. Az ok a felületi feszültség, amelyet az egyes öntvények készítésekor fellépő hőmérsékleti ciklus okoz. A feszültség súlyossága az ötvözet olvadási hőmérsékletétől függ. Mivel a cinkötvözetek olvadási tartománya alacsony, ez a hiba ritka, és csak olyan szerszámoknál fordul elő, amelyek több millió öntvényt gyártottak.
Forrasztás
Ez egy fizikailag és kémiailag is tapadó ötvözetréteg felhalmozódása a szerszám felületén. Az öntvényt ott jelölik meg, ahol a megtapadt bőr a kidobáskor leszakad, és a felhalmozódás által létrehozott alulvágás az öntvényen is pontozáshoz vezet. A forrasztás nagyobb valószínűséggel fordul elő, ha a kapu sebessége nagy és a szerszám hőmérséklet a magas. Die spray kell legyen megfelelő a oldalon. megrendelés a címre. a honlapon található. a védő réteg a oldalon. a acél felszínre.
A forraszanyagból származó felhalmozódást nehéz eltávolítani a süllyesztékről. Ez különbözteti meg a felesleges fröccsenés miatti felhalmozódástól, amely általában letörölhető.
Flash
Amikor a fém behatol a szerszámrészek és a szerszám felének illeszkedő felületei közé, vékony külső fémrétegek keletkeznek a szerszámban. ous anyag a balra a oldalon. a casting (ábra 16). A címre. megakadályozza a ez a meghal kell legyen erősen épített és tökéletesen kizárva.
Még ekkor is előfordulhat, hogy a termikus eltérések miatt üzemi hőmérsékleten megnyílnak a rések. Ha a gép záróereje nem megfelelő a készülő öntvény méretéhez képest, a szerszámok szétválnak, és nagy kiterjedésű villanófelületek keletkeznek. A fémnyomás csökkentése csökkenti a szerszámok kivillanásának valószínűségét. A töltési idő növelése, és ezáltal a fém hőmérsékletének csökkentése, mire az eléri a hasadási vonalat, szintén csökkenti az illeszkedő felületek közötti behatolást.
Méretarányos Következetesség
A mérettűrések kérdésével e kézikönyv egy másik fejezetében hosszasan foglalkozunk. Itt azért említjük meg, mert a nem megfelelőség öntési hibának tekinthető.
Az öntött méret reprodukálhatósága lövésről lövésre szinte kizárólag a hőmérséklet állandóságának függvénye. A legnagyobb hatást az öntvény hőmérséklete gyakorolja, amikor az öntőformából kilökik. StabilisEz a hőmérséklet javítja a méretek reprodukálhatóságát és segíti a szoros tűrések betartását.
A kohászati öregedési hatások miatt az öntés után idővel enyhe zsugorodás következik be. Ennek mértéke kicsi és reprodukálható, és csak a legszűkebb tűréshatárok között meghatározott alkatrészeknél jelent problémát. Szükség esetén az öntvény stabilizálására alacsony hőmérsékletű hőkezeléssel, jellemzően néhány órás, 95 °C-on végzett hőkezeléssel lehet stabilizálni az öntvényt.
Trimming és Ruhaa oldalon.g
Általános problémák a oldalon. ez terület a a termelés művelet a elfogadhatatlan megváltoztatni a kontúr due a címre. over- a fém eltávolítása és a durva kezelés vagy az igazítási problémák miatti torzulás.
Letörés Hibák
A cinkötvözet-öntvényben lehetséges vékony kapuk miatt sok esetben a sajtolás helyett inkább a letörés a megoldás. A letörés történhet kézzel vagy mechanikusan, tekercs- vagy billenőgépeken. A tiszta törés a kapu alakjától és vastagságától függ.
Earring
Az enyhén ívelt kapukat el lehet törni, de általában hagynak "fülek" az öntvényen, ha kúpos kapukat használnak. A kialakítástól és a hajlítás irányától függően még az egyenes kapuknál is előfordulhat, hogy az öntvényből kiemelkedik a sík..
Break a oldalon.
Itt a kapu alakja és a hajlítás iránya vezetett ahhoz, hogy a törés az öntvénybe hatolt, így az öntvényen alulvágás keletkezett.
Kapuvezeték Porozitás
Még akkor is, ha a kapu tisztán törik, egy tanú marad az öntvényen. A feltárt fém eltér a környező öntvénybőrtől; ez az öntvény belsejére jellemző, és így porozitást tartalmazhat (17. ábra). Minél vastagabb a kapu, annál valószínűbb, hogy ez a porozitás láthatóvá válik. A kapuszín mennyisége porosA porozitás mértékét az e fejezet Porozitás című fejezetében tárgyalt tényezők befolyásolják. Még ha nem is látható, a feltárt mikroporozitás problémát okozhat a bevonat után.
Nyomja Trim Hibák a cink öntvényben
Pontozás
Az alkatrész helytelen illesztése és/vagy a szerszám helytelen igazítása és a hézagok helytelen beállítása ahhoz vezethet, hogy a vágószerszám leborotválja az öntvény oldalát.
Összecsukható
ha a villanás vékony és csak rövid távolságra terjed ki, az ötvözet képlékenysége olyan, hogy a villanás inkább meghajlik, mint hogy elvágódjon. Az eredmény egy vékony fémredő lesz az alkatrész felületén. ahol ez problémát jelent, ott jobb lehet szándékosan átvillantani, mint sikertelenül elzárni, hogy a vágószerszámnak legyen egy határozott vastagsága a vágáshoz.
Finishing Hibák a cink öntvényben
A felület túlzott eltávolítása mikroporozitást tár fel. Ez lehet, hogy nem látható, de problémákat okoz, ha az öntvényt később bevonják.
Barrelling/Vibropolisha oldalon.g Hibák
Méretezés
Túlzott kezelés a erősen lappangó öntvények lehet ólom a címre. a körök emelés vagy a címen. teljesen különálló (18. ábra).
Polírozás Hibák
A túlzott fémeltávolítás feltárja a mikroporozitást. Az apró dudorok és üstökösfarkak megjelenése a következőknek köszönhető a fémszennyezésből származó kemény részecskék az öntvényben. Mint a hordózás és a vibrációs polírozás, tA polírozás csak a felületi hibákat, például a köröket fedi el. A mögöttes folytonossági hiba továbbra is jelen van, és később problémákat okozhat.
Megmunkálás és összeszerelés Hibák a cink öntvényben
Szerszám Viseljen
A forgácsolószerszámok gyors kopása az olvadék szennyeződéséből származó, az ötvözetben lévő kemény részecskék miatt következhet be. Az okokat és az ennek elkerülésére irányuló ellenőrző intézkedéseket a Rögök fejezetben tárgyaljuk. kopást és törést okozhat az is, hogy a szerszámok nagy gáz- vagy zsugorodási pórusokba hatolnak. A pórusképződés elkerülése az öntés szakaszban kerül tárgyalásra.
Kitett Porozitás
Az egészséges felületi bőr eltávolítása porozitást tárhat fel a megmunkált felületeken, például a karimákon vagy a furatokon. A porozitás ellenőrzésével az öntés fejezetben foglalkozunk.
Fracture
A szegecselési és hajlítási műveleteket gyakran használják a következők összeszereléséhez cinkötvözet öntvénys. Ha az öntött szegecsek és a fülek nem jól vannak elkészítve, akkor ezek a részek törése előfordulhat. A felületeknek mentesnek kell lenniük a túlságosan nagy hézagoktól és repedésektől (lásd az öntésről szóló szakaszt). Az öntés után bekövetkező öregedési folyamat befolyásolja a képlékenységet. Ez az öntés után legalább három hétig tart. Az ötvözet alakíthatóságát jelentősen növeli a mérsékelten magas hőmérsékleten történő deformálás.
Púder coating cink öntési hibák
Ebben a szakaszban a bevonatolás során és a bevonat üzem közbeni hibáit vizsgáljuk. Csak azokat hibák okozta a hibák a oldalon. a casting a lefedve. A további teljes lefedettség, amely tartalmazza a címet. hibák a oldalon. maga a kabát a füzetekben található. "A cink szerszám bevonása öntvények" és "A cink szerszám porbevonata öntvények" amelyeket a Cinkfejlesztési Egyesület (London, Egyesült Királyság) adott ki.
Torzítás
A cinkötvözet szilárdsága csökken a hőmérséklettel, így a festékkályha hőmérsékletén meglehetősen gyenge, és még a galvanizálófürdő hőmérséklete is hatással van rá. Így ha az öntvények rosszul vannak alátámasztva, vagy a jigek túl nagy rugóerőt fejtenek ki, az öntvények deformálódni fognak. az öntvény feszültségmentesítése miatt vetemedés is előfordulhat. Az öntés során bekövetkező gyors lehűlés rögzítheti a differenciális zsugorodás okozta feszültségeket. A feszültség mértéke nagymértékben függ az alkatrész alakjától.
Irregular Surface
A hideg körök halpikkelyes megjelenése át fog látszani a galvanizáló rétegen, és ha súlyos, akkor a vastagabb festékrétegen is át lehet látni. A tavak határai hullámos jelként jelennek meg a bevonatolt vagy festett felületen. E hibák okait és orvoslását az öntés fejezetben ismertetjük.
Plata oldalon.g Hibák a cink öntvényben
Hólyagok
A galvanizálólemezen lévő hólyagok öntési hibák (a hólyagokat és más hibákat a galvanizálási folyamat problémái is okozhatják), és a talaj, a gáz és a galvanizálási oldatok felületi hibákba való beszorulása okozza őket. A gázképződés az áthatolhatatlan bevonat mögött hólyagosodást, sőt, akár szilánkosodást is okozhat. Az öntvény és a csapdába esett korróziós oldatok reakciója során keletkező korróziós termékek okozta tágulás hasonló hatást fejt ki.
Ha a beszorulást hideg ívek okozzák, mind az öntőfelület, mind a lemez megemelkedhet. Vegye figyelembe, hogy a felületre hajlított villanófény okozta ráncok ugyanolyan problémákat okoznak, mint az ívek. Üzembe helyezés esetén a lemezelt rétegben okozott kár korróziót eredményez. (7., 19. ábra).
Az olyan öntvények, amelyek felülete hideg íveket tartalmaz, vagy amelyek felületén durva porozitás vagy mikroporozitás van, valószínűleg hólyagokat képeznek a bevonaton. Az ilyen hibákról az öntés és a kikészítés szakaszok tartalmaznak részleteket.
Paint Hibák a cink öntvényben
Hólyagok
Az öntvény festett felületén lévő hólyagok kétfélék lehetnek. Fontos különbséget tenni közöttük, mivel a szükséges korrekciós intézkedések eltérőek.
A közepes méretű hólyagok, amelyek az öntvény ellentétes oldalain keletkezhetnek, az öntvényen belüli gázporozitás miatt keletkeznek (13. ábra). Ez a festékréteg lekaparásával vagy a hólyag szétvágásával ellenőrizhető. Gázhólyagról akkor van szó, ha a hiba nem a festékben, hanem az öntvényben van. A probléma azért jelentkezik, mert a cinkötvözet gyenge a festékkályha hőmérsékletén, ami a pórusokban lévő nagynyomású gáz miatt az öntvény felfúvódását okozza.
A tűzhely hőmérséklete döntő fontosságú, és ha az eljárás különböző körülményeket tesz lehetővé, akkor a hosszabb ideig tartó, de alacsonyabb hőmérsékleten történő pörkölés lehetőségét kell választani. A magas hőmérsékleten (200°C) sütésre kerülő öntvényeknek minimális mennyiségű, finoman eloszló, csapdába esett gázt kell tartalmazniuk.
A kisebb hólyagokat az öntőfelületről felszálló és a festékrétegben megrekedt gáz okozza. Néha a gáz kiszabadul, de a megszilárduló festék túl kemény ahhoz, hogy újra sima felületet képezzen, ami egy miniatűr vulkánhoz hasonló hólyagot eredményez (20. ábra). E problémák elkerülése érdekében az öntvénynek mentesnek kell lennie a felület olyan megszakításaitól, amelyek a gázt és a szennyeződést csapdába ejthetik, mint például a hideg ívek, a ráncok és a látható porozitás. A szerves réteg hozzáadása előtti sütés lehetővé teszi, hogy az öntvény kiürítse a gázt, és megoldja a problémát.
Chipped Festék
A festék leválását néha öntési hiba vagy a bevonat utáni nem megfelelő kezelés okozhatja. Ha egy hajtást (pl. egy meghajlított villanófényt) lefestenek, majd ütésnek teszik ki, az letörhet, felfedve az alatta lévő bevonat nélküli felületet.
Kezelés, tárolás és csomagolás
A nem megfelelő kezelés a felület sérülését vagy torzulását eredményezheti. öntvényöntés. A több üregű szerszámoknál a gyenge alkatrészek közötti öntvénykapcsolatok hatékonyak lehetnek a megtámasztás biztosítására. Az elfogadható felületi sérülések mértékét a minőségi követelmény és az alkalmazott bevonat határozza meg.
Ha a csupasz öntvényeket bármilyen hosszú ideig tárolják, száraznak kell lenniük. A nedves körülmények elősegítik a fehér rozsda és a felületi korrózió kialakulását. Ha a fröccsöntő- vagy oltóvíz megromlott, ami savas vegyületek kialakulásához vezet, a korrózió súlyosabb lehet. Az öntvényeket az öntés és a polírozás után a lehető leghamarabb be kell vonni vagy le kell festeni, hogy csökkentsék a felületi szennyeződés kockázatát.
Az öntvényeket száraz anyagba kell csomagolni, mivel a nedves karton savakat képez, amelyek károsítják és megfeketítik a cinköntvényeket.
0 hozzászólás