Pressofusione ad alta pressione è simile al volo dei calabroni: entrambi sono teoricamente impossibili. Tuttavia, oltre 150 anni di funzionamento effettivo, con produttività e qualità dei componenti in costante aumento, hanno dimostrato che la pressofusione è intrinsecamente robusta e in grado di raggiungere elevati livelli di capacità di processo. Anche nelle officine meglio gestite si verificano degli scarti e di seguito vengono illustrati la diagnosi, le cause e il trattamento dei difetti che possono verificarsi nelle pressofusioni di zinco; tutti questi problemi sono uguali a quelli delle pressofusioni di alluminio e di magnesio.
Esistono diversi modi per organizzare i difetti in modo da fornire una trattazione coerente dell'argomento. In questo articolo viene adottato un approccio graduale, dalla ricezione del lingotto di lega alla spedizione del prodotto finito, e vengono presentate informazioni su ogni tipo di difetto nel momento in cui si verifica. Altri metodi di identificazione dei difetti e vari sistemi di individuazione dei difetti saranno discussi in seguito. Le fasi del processo sono elencate di seguito:
Inoltre, i canali di colata e gli scarti saranno riciclati in varie fasi e si dovrà tenere conto dello stoccaggio e della movimentazione tra i processi. Non tutti i getti saranno sottoposti a tutte le procedure.
Lingotto di lega di zinco Specifiche:
Le composizioni delle leghe di zinco da colata sono state sviluppate metodicamente nell'arco di 75 anni. Le gamme di elementi di lega sono state messe a punto e i massimi di contaminanti pericolosi sono stati attentamente determinati. Per produrre getti affidabili, è necessario utilizzare lingotti che soddisfino i requisiti accettati a livello internazionale. Inoltre, la qualità della lega deve essere mantenuta durante le operazioni di fusione e colata, per garantire che i componenti fusi soddisfino i criteri di composizione della colata.
Le piccole discrepanze tra gli standard di lingotto (tabella 1) e di colata (tabella 2) per ciascun tipo di lega sono intese a tenere adeguatamente conto delle variazioni causate dai normali processi di lavorazione e riciclaggio. L'uso di lingotti fuori specifica, in particolare quelli carichi di impurità altamente tossiche come piombo, stagno o cadmio, non è mai giustificabile.
Le leghe sono suddivise in tre famiglie: leghe di alluminio 4% (Zamak 3 e 5, oltre ai nn. 2 e 7), leghe di alluminio superiore ZA (nn. 8, 12 e 27) e leghe di rame (A cu zinc 5 e 10).
Inoltre, alcune altre leghe non sono state accettate commercialmente. Quasi tutti i getti in lega di zinco sono prodotti in Zama No3 o No5, mentre altre leghe sono specificate solo quando sono richieste qualità specifiche.
Effetto della contaminazione
Gli effetti degli elementi contaminanti, come il piombo sui getti, sono comparabili per tutte le leghe. I massimi di impurità specifici indicati riflettono la gravità variabile dell'effetto e la facilità con cui è possibile produrre lingotti con bassi livelli di elementi in traccia.
Piombo, stagno e cadmio
Questi elementi, insieme agli analoghi ma meno comuni indio e tallio, possono causare cedimenti catastrofici per corrosione intergranulare. "Le impurità si segregano ai confini dei grani, facilitando la corrosione intergranulare, soprattutto in ambienti caldi e umidi. I getti si gonfiano e si rompono, formando cumuli di polvere grigia (figura 1).
Se i livelli di magnesio sono mantenuti al di sopra dei minimi, l'effetto è insignificante nei getti che contengono fino ai massimi prescritti di questi inquinanti. I metodi di prevenzione includono l'acquisto corretto dei lingotti e una buona gestione della casa per evitare la contaminazione dalla rifusione o dall'ambiente dell'officina, come ad esempio la saldatura.
Ferro
Il ferro è solo leggermente solubile nello zinco e l'eccesso di ferro si combina con l'alluminio della lega per generare il complesso intermetallico alluminuro di ferro (FeAl3). Questo composto è estremamente duro e, se entra nella colata, può creare problemi di lavorazione, usura eccessiva degli utensili e problemi di lucidatura, poiché le particelle si staccano o si staccano. Quantità eccessive possono limitare la fluidità della lega e quindi la sua capacità di riempire gli stampi. Infine, se si concentrano in punti sollecitati, la resistenza e la duttilità possono diminuire. È dimostrato che la dimensione delle particelle, piuttosto che la quantità totale presente, determina la lavorabilità del ferro perché il ferro proviene dal crogiolo. La protezione chiave consiste nel tenere sotto controllo le temperature del metallo.
Nichel, cromo, manganese e silicio
Livelli eccessivi di questi componenti hanno lo stesso effetto sul getto del ferro extra. Va notato che il nichel non è un contaminante nella lega n. 7; piuttosto, la piccola quantità indicata (inferiore al limite di solubilità) è un'aggiunta intenzionale per ridurre la corrosione intergranulare in questa lega priva di magnesio e ad alta fluidità.
Effetto degli elementi di lega
Alluminio
Ad eccezione delle leghe di acuzinc, l'alluminio è l'elemento di lega più comune. Sia la resistenza che la colabilità delle leghe dipendono dal loro livello all'interno delle specifiche. Le proprietà possono cambiare rapidamente al di fuori degli intervalli molto limitati indicati, in particolare per le leghe di zinco 2, 3, 5 e 7.
L'eccesso di alluminio in queste leghe 4%Al riduce significativamente la resistenza all'urto (Figura 2), pertanto l'alluminio non deve essere raccolto durante la lavorazione. Se il livello di alluminio scende al di sotto del minimo prescritto, gli effetti sono meno evidenti. Le possibili implicazioni includono una tendenza alla lacerazione a caldo, che riduce la resistenza, una minore fluidità e una maggiore tendenza della lega ad aderire alla matrice (saldatura).
Le variazioni del contenuto di alluminio hanno un effetto meno evidente sulle caratteristiche delle leghe ZA a più alto contenuto di alluminio, con conseguenti intervalli più ampi consentiti. Tuttavia, come per le leghe 4%, le composizioni sono state ottimizzate per fornire la combinazione ottimale di caratteristiche e il superamento dei limiti comporterà modifiche che potrebbero essere deleterie.
Magnesio
Sebbene l'aggiunta di magnesio abbia un effetto rinforzante, il suo scopo principale è quello di prevenire la corrosione intergranulare nelle leghe contenenti piombo, stagno e altri metalli a livelli fino al massimo consentito. I getti contenenti meno magnesio del minimo consentito possono corrodersi in servizio. Un livello di magnesio superiore all'intervallo consentito può causare strappi a caldo, con conseguente perdita di resistenza o difficoltà di rivestimento. Un elevato contenuto di magnesio riduce la fluidità della lega, con conseguenti problemi di riempimento.
Rame
L'aggiunta di rame alla lega base 4%Al aumenta la resistenza e la durezza a scapito della duttilità e fa sì che le leghe cambino maggiormente dimensione durante l'invecchiamento. Anche la resistenza all'urto nelle leghe ad alto contenuto di rame diminuisce con l'invecchiamento. Di conseguenza, le leghe che non rientrano nei limiti di rame applicabili avranno qualità intermedie a quelle delle leghe specificate.
La componente di rame delle leghe ZA ha un impatto significativo sulle loro proprietà meccaniche. In generale, un alto contenuto di rame riduce la duttilità, mentre un basso contenuto di rame riduce la resistenza alla trazione.
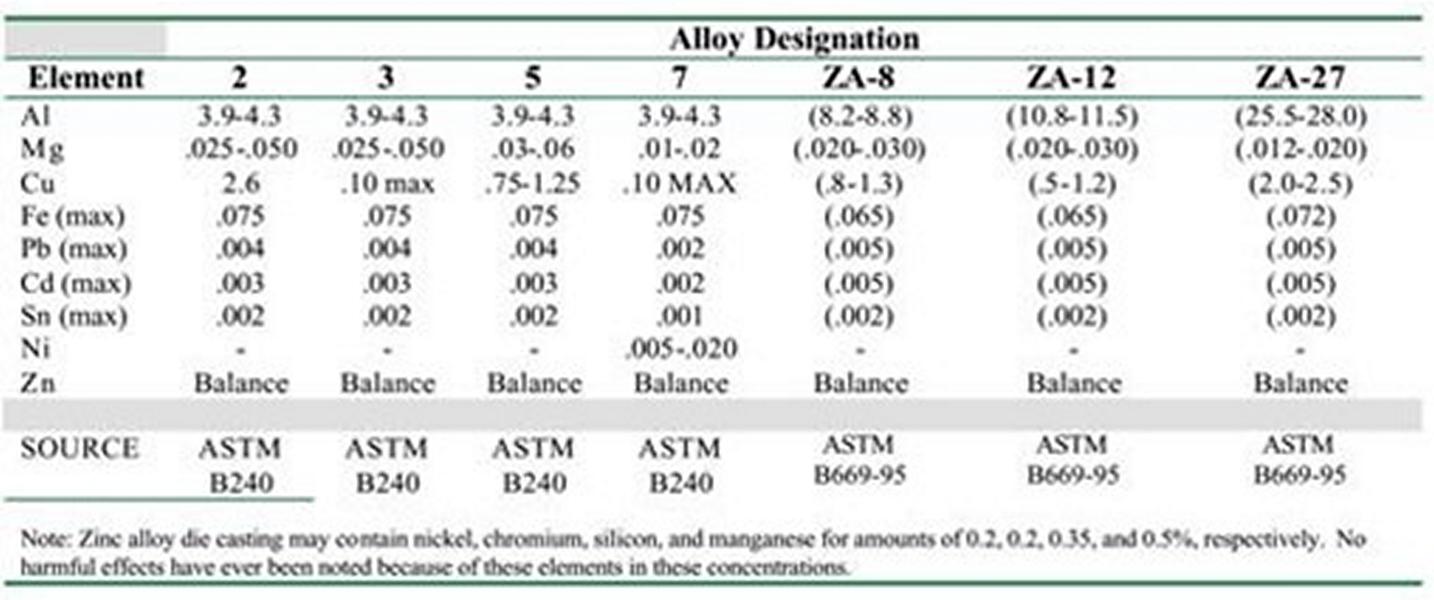
Tabella 1. GOMPOSIZIONE DELLE LEGHE DI ZINCO PER LA CASTRAZIONE A PRESSIONE LIMITI DI INGRANAGGIO, IN PESO.
La principale aggiunta di lega nelle leghe di Acuzinc è il rame, che conferisce maggiore durezza e resistenza alle alte temperature rispetto alle altre leghe a base di zinco. I livelli relativi di rame e alluminio delle leghe di Acuzinc sono stati ottimizzati per bilanciare le caratteristiche e la colabilità. Poiché l'elevato livello di rame si verifica in un sistema di fase distinto, il suo effetto sulla variazione dimensionale dell'invecchiamento può essere diverso da quello riportato nelle leghe 4%Al.
Fusione, trasferimento e mantenimento dei metalli
Ad eccezione delle leghe ZA-12, ZA-27 e Acuzinc10, che attaccano il ferro e l'acciaio a una velocità inaccettabile, le leghe di zinco possono essere fuse e conservate in contenitori metallici. Questa caratteristica ne consente la fusione con il processo a camera calda, che impiega un sistema di iniezione a immersione.
Tuttavia, questa preziosa caratteristica è ottenibile solo attraverso un rigoroso controllo della temperatura. Al di sotto dei 450°C circa, la lega di zinco scioglie il ferro a un ritmo sufficientemente lento da consentire l'utilizzo di parti metalliche a contatto con la lega. Poiché il tasso di reazione cresce esponenzialmente con la temperatura, è suscettibile a modeste fluttuazioni di temperatura.
La reazione avviene tra l'alluminio della lega e il ferro del crogiolo e delle parti della macchina.
Alluminio + ferro > Particella intermetallica
3Al + Fe > FeAl3
L'intermetallico ferro-alluminato galleggia in superficie e reagisce con lo strato di ossido generando scorie. Se la scoria viene mescolata al metallo o se il livello del vaso si abbassa a tal punto da risucchiare il metallo sotto la superficie nel collo d'oca, la colata conterrà particelle dure che daranno origine ai difetti indicati alla voce ferro nella sezione contaminazione.
Una temperatura eccessiva causa anche la perdita di magnesio, elemento volatile che viene consumato. Un basso livello di magnesio espone la colata a notevoli difficoltà di corrosione durante il servizio.
Vale la pena notare che la temperatura complessiva della fusione non è l'unico fattore da considerare. Se c'è un punto caldo nel forno, come ad esempio un bruciatore mal calibrato, l'alta temperatura causerà il ritiro del ferro. In circostanze gravi, il crogiolo può essere consumato, provocando un run-out.
Consigliato metallo getto temperature sono:
Zama n. 2,3,5,7 |
415-4S0°C |
ZA8 |
420-445°C |
ZA12 |
465-495°C |
ZA27 |
550-580°C |
Acuzinc 5 |
~ 480°C |
Acuzinc 10 |
~ 5S0°C |
Quando le leghe ZA, in particolare la ZA-27, vengono fuse, tendono a separarsi per gravità in strati ricchi di alluminio e zinco. L'agitazione verticale mescolerà la fusione; si deve evitare un'agitazione forte, poiché favorisce l'ossidazione. Una volta miscelata, la fusione deve rimanere stabile. È fondamentale che l'eventuale strato di scorie creato non venga separato e mescolato. Lo ZA-27 non deve essere conservato a temperature inferiori a 540°C perché il ferro in soluzione precipita sotto forma di particelle intermetalliche massicce.
La fusione e il mantenimento di lingotti conformi alle specifiche dovrebbero essere privi di problemi, purché si mantenga un adeguato controllo della temperatura e non si verifichino contaminazioni involontarie. Quando si rifondono i canali di colata e gli scarti, si devono considerare diversi aspetti.
I resi devono essere rigorosamente segregati, soprattutto nelle officine che fondono anche leghe di alluminio. Mescolando alcuni canali di alluminio con le leghe di zinco 4% si ottengono getti con un elevato contenuto di alluminio, che li rende fragili. Lo stesso problema si verifica se la lega ZA viene combinata con una lega normale.
La rifusione diretta di trucioli, bave e altro materiale contaminato dalla superficie a basso spessore produce scorie eccessive e può potenzialmente raccogliere impurità. È meglio trattare questo materiale separatamente, in modo da poter determinare la composizione del lingotto rifuso. Le scorie devono essere trattate singolarmente per motivi identici. Il fondente tende a estrarre il magnesio, soprattutto quando il metallo viene riscaldato. Le fusioni galvaniche richiedono un'attenzione particolare. Durante la fusione, la pelle dell'elettroplacca rimane in superficie e può essere sfiorata. La piastra non deve essere spezzettata e mescolata alla fusione perché il nichel, in particolare, può creare punti duri.
Durante la fusione e la colata, la lega perde una piccola quantità di magnesio (per volatilizzazione) e di alluminio (per interazione con il ferro e successiva rimozione come scoria). La rifusione continua dello stesso metallo finirebbe per produrre getti fuori specifica. I test sulla lega No3 hanno indicato che sono necessari sette cicli per ridurre il magnesio a un livello inferiore a quello specificato. Per evitare questa degradazione finale, è necessario fornire continuamente lingotti vergini al processo.
Difetti della pressofusione di zinco
Di seguito sono elencati i difetti più comuni in pressofusione di zincoPer quanto riguarda la pressofusione di alluminio, la pressofusione di magnesio, ci saranno più o meno gli stessi problemi della pressofusione di zinco,
Interno Difetti nella pressofusione di zinco
Restringimento Porosità
Quando la lega passa da liquida a solida, si restringe di qualche punto percentuale del suo volume di fusione. Se non è disponibile metallo liquido aggiuntivo per alimentare il ritiro, si forma un vuoto. Si tratta della porosità da ritiro. Spesso si presenta in porzioni isolate e pesanti come enormi buchi irregolari (figura S), ma può anche avere una forma interdendritica, simile a una crepa, in particolare nelle leghe a lungo intervallo di congelamento come ZA-27 e Acuzinc.
La porosità interna può essere rivelata se si devono lavorare superfici come flange o fori, con conseguente scarto. La porosità può anche portare all'usura degli utensili e alla deriva delle punte durante i processi di lavorazione. L'influenza sulla resistenza sarà determinata sia dalla distribuzione che dalla quantità della porosità. È importante ricordare che i valori di resistenza "a libro" indicati per le leghe sono stati ottenuti su campioni con livelli di porosità tipici.
Per limitare la porosità da ritiro, aumentare la pressione del metallo e assicurarsi che il gate sia abbastanza spesso da essere attivo durante la solidificazione. Lo stantuffo non deve spostarsi così tanto da toccare il fondo del collo d'oca, il che potrebbe causare una mancanza di pressione sul metallo. Il tempo di impaccamento deve essere sufficiente a consentire la completa solidificazione; in caso contrario, il metallo verrà estratto dalla cavità al ritorno dello stantuffo. Il raffreddamento locale può ridurre al minimo i punti caldi e quindi evitare la produzione di chiazze isolate di metallo liquido che, una volta congelate, producono pori.
La porosità interdendritica può causare perdite nei componenti a tenuta di pressione. Più lungo è l'intervallo di congelamento della lega, maggiore è la probabilità di perdite. La colata a bassa temperatura dello stampo ispessisce la pelle della colata e riduce la possibilità di perdite. Tuttavia, questo processo può essere ostacolato dalla necessità di una temperatura dello stampo sufficientemente elevata per ottenere un aspetto superficiale desiderabile. Le temperature della superficie dello stampo variano in genere da 170°C a 240°C.
Porosità del gas
Quando lo stampo si riempie rapidamente, enormi volumi di gas possono rimanere intrappolati. Dopo la solidificazione ad alta pressione, il gas forma bolle quasi sferiche, di solito intorno alla linea centrale (figura 4). Possono coesistere gas e porosità da ritiro; in questo caso, il gas tende ad arrotondare la porosità da ritiro.
La porosità gassosa provoca gli stessi difetti della porosità da ritiro, ma è meno probabile che si verifichino perdite, poiché i fori gassosi sono raramente interconnessi. Inoltre, la porosità gassosa è la causa principale della formazione di bolle nei getti. Se la lega è debole, a causa del riscaldamento ad alte temperature, l'enorme pressione del gas nel poro può spazzare via il rivestimento metallico circostante. Aumentando il tempo di raffreddamento e/o diminuendo la temperatura dello stampo si può ridurre la formazione di bolle subito dopo l'espulsione.
Idealmente, la quantità di gas intrappolata nella cavità dovrebbe essere ridotta al minimo. Ciò si ottiene impiegando la corsa più grande possibile per il primo stadio e il tempo di riempimento più lungo possibile (tenendo presente la necessità di periodi di riempimento brevi per ottenere un aspetto superficiale accettabile). Gli sfiati devono essere massimizzati e posizionati correttamente. È vantaggioso ridurre al minimo gli spruzzi della matrice. La porosità è spesso meno problematica, e certamente produce meno bolle, quando si presenta sotto forma di molti pori microscopici piuttosto che di pochi pori grandi. I pori piccoli sono incoraggiati dall'uso di velocità elevate del metallo; l'obiettivo dovrebbe essere quello di raggiungere una velocità di 40 m/s. La pressofusione sotto vuoto elimina questo tipo di porosità.
Difetti di microporosità nella pressofusione
Oltre alla porosità visibile, ci sarà una porosità di dimensioni tali da poter essere osservata solo al microscopio. Questa microporosità, se assente dalla pelle della colata (come spesso accade), non ha alcun impatto negativo, a meno che non venga esposta in seguito da processi di lucidatura prima del rivestimento superficiale.
Lacrime and Crepe
Le cricche a caldo, come dice il nome, si verificano a temperature prossime all'intervallo di solidificazione. La cricca è causata dal cedimento della colata in condizioni di elevata deformazione e bassa tensione e spesso segue un andamento irregolare (Figura 5). Ciò contrasta con le cricche notevolmente più diritte che possono verificarsi a temperature più basse in condizioni di elevata sollecitazione e bassa deformazione. Inoltre, l'aspetto delle facce di frattura varia tra questi due tipi di faglie.
La forma del componente contribuisce in modo significativo alla lacerazione a caldo. Si verifica quando il ritiro di solidificazione è limitato a una piccola area, in particolare se tale area è anche una zona calda. Lo ZA-27 e l'Acuzinc sono più inclini a questo difetto rispetto alle altre leghe, a meno che il loro contenuto di alluminio sia inferiore alle specifiche o includano un eccesso di magnesio. Ad eccezione della distribuzione della temperatura dello stampo, i parametri di colata non hanno alcun effetto sulla lacerazione a caldo. Il raffreddamento delle zone calde dello stampo può contribuire a risolvere il problema.
La cricca si verifica durante l'espulsione quando si generano forze eccessive a causa dell'intasamento della colata nello stampo. Questo è spesso il risultato di errori di costruzione degli utensili che hanno causato sottosquadri, tiraggio inadeguato o fiammate. Il prolungamento del periodo di raffreddamento per rendere il getto più duro e in grado di assorbire meglio le sollecitazioni di espulsione può aiutare a prevenire le cricche. Tuttavia, quando la forza è causata dal ritiro del getto sulla matrice, i tempi di raffreddamento prolungati sono inefficaci e l'espulsione anticipata può essere vantaggiosa.
Problemi di inclusione
Questo problema è molto meno sentito nelle leghe di zinco che in quelle con formatori di film di ossido più forti. In effetti, le intermetalliche di ferro create da una gestione inadeguata della fusione sono spesso le uniche a creare problemi nella pratica. Il livello del metallo nella pentola non deve scendere fino al punto in cui il metallo sotto la superficie entra nel collo d'oca.
Difetti di superficie nella pressofusione
Giri d'oro.
Questo difetto (noto anche come "flowmarks" o "cold flow") si sviluppa quando i flussi di metallo che si sono pre-solidificati a contatto con la matrice non vengono rifusi nella massa del getto quando arriva altro metallo. La superficie appare come un solco irregolare con un effetto a squama di pesce che varia in profondità a seconda della gravità del giro (figura 6). La sezione trasversale mostra la caratteristica distintiva di un cold lap, ovvero la misura in cui la frattura superficiale continua orizzontalmente e genera una discontinuità sottosuperficiale (figura 7).
I giri a freddo degradano l'aspetto dei getti e causano problemi con le future procedure di finitura, in particolare con la galvanica, con conseguente rottura del rivestimento. Se gravi, i giri possono compromettere la duttilità della colata. Il tempo di riempimento della cavità e la temperatura dello stampo sono i parametri chiave della colata che influenzano la produzione di colate a freddo. Caratteristiche meno importanti sono il modello di flusso, la distanza di flusso, la velocità del metallo, la superficie della matrice e la temperatura del metallo. Lo spessore della colata è fondamentale. I laps sono più comuni nei getti a sezione sottile.
È stato determinato il legame tra aspetto della superficie, spessore della parete, temperatura dello stampo e tempo di riempimento. Il Predittore di superficie (figura 8) può essere utilizzato per determinare il tempo massimo di riempimento della cavità e la temperatura minima dello stampo per ottenere una superficie galvanica. Se il pezzo deve essere verniciato, sono accettabili tempi di riempimento più lunghi e temperature dello stampo più basse. Una superficie strutturata sullo stampo può aumentare il tempo di riempimento massimo di 50%.
A volte compaiono dei giri anche se la matrice è calda e il tempo di riempimento della cavità è breve. quando questo accade sono di solito associati a un modello di flusso vorticoso che ha intrappolato il gas. La contropressione esercitata dal gas a il fine di cavità riempire rallenta il circondare metallo vapori e quindi produce il condizioni necessario per locale giro formazione. In questo caso, esso volontà essere necessario a ridurre il aria intrappolato in il dado (vedi sezione sulla porosità) o modificare lo schema di riempimento per evitare la formazione di tali lapsus.
Laminazione
Le laminazioni sono fogli di metallo sovrapposti che si estendono su un'area più ampia e in modo più uniforme rispetto ai cold laps. Possono verificarsi quando si verificano problemi con il sistema di iniezione della macchina e lo stampo si riempie in una serie di impulsi. Una laminazione si forma anche se la corsa del primo stadio è troppo lunga, con il risultato che il primo metallo che entra nella cavità si muove lentamente e si congela.
Misrun
Se la matrice è troppo fredda e il tempo di riempimento è troppo lungo, non si otterrà una colata completa. Il metallo si solidificherà completamente prima che la cavità sia riempita e si otterrà un errore di colata (figura 9). Piccole aree di composizione incompleta, ad esempio alle estremità delle alette o al centro dei vortici, possono essere causate da gas intrappolati che impediscono al metallo di riempire completamente la cavità. Se si supera la capacità di iniezione della macchina, il "colpo corto" causerà un errore di produzione.
Colpo o schizzo
Come i labbri, sono il risultato di una pre-solidificazione, ma l'aspetto e la causa sono diversi. Il difetto può essere puramente superficiale, dove produce una consistenza ruvida, o può essere incorporato come un "inclusione di lega" (figura 10). Il "scatti" sono globuli di lega che sono stati spruzzati fuori dal flusso principale di metallo e non sono stati successivamente adsorbiti.
Gli spruzzi possono derivare dall'impulso quando il primo metallo passa attraverso il gate o possono essere vortici che si arricciano sul bordo del flusso di metallo. Questo è il motivo per cui gli spruzzi si verificano di solito vicino alla porta. A volte gli spruzzi sono così poco legati alla colata che una parte di essi viene lasciata indietro al momento dell'espulsione. Questo materiale formerà delle "inclusioni" nella colata successiva.
L'aumento della temperatura dello stampo dovrebbe migliorare la situazione, ma il rimedio principale sarà quello di modificare il gate in modo da ottenere un riempimento anteriore più solido.
Questi depressioni in il getto superficie sono meno comune in zinco lega di alcuni altro metalli e molto meno di un problema rispetto agli stampi in plastica. La causa è lo stesso ritiro di solidificazione che è il motore della formazione della porosità. Una sezione pesante locale mostra un avvallamento superficiale piuttosto che un poro interno quando la distribuzione della temperatura è tale che il centro di calore è vicino a una superficie. Il ritiro finale attira quindi verso il basso la debole pelle della colata solida, formando una depressione (figura 11).
In leghe come la ZA-27 l'aspetto può essere diverso. In questo caso, il difetto è presente su un'area più ampia e appare ghiacciato. Il lungo intervallo di congelamento ha modificato il comportamento in modo tale che, invece di un affondamento definito, il ritiro ha prosciugato la superficie del liquido eutettico, lasciandola ruvida e semi-porosa.
I rimedi al processo sono gli stessi indicati nella sezione Porosità da ritiro. Se possibile, è necessario riprogettare il getto per ridurre il punto caldo.
Laghi
Un lago è un ampio gradino nella superficie di fusione con un'altezza di soli 5 - S0 micrometri. Diventa molto evidente sui componenti che vengono successivamente lucidati e placcati, dove produce un effetto increspatura insoddisfacente (figura 12).
Nonostante intensivo indagine, il causa, e quindi il rimedio resti sfuggente. Lì è prove che il termine "lago" può essere attribuito a due difetti dello stesso aspetto, Quando vengono sezionati, alcuni laghi mostrano una microstruttura diversa sotto il lago rispetto alla massa della colata o alla superficie circostante. Laghi di questo tipo sembrano essere associati a una precoce solidificazione locale e i rimedi adottati per i giri freddi possono essere utili.
Altri laghi, invece, non mostrano alcun cambiamento microstrutturale. Inoltre, sui getti sottili, non è raro che il difetto sia trasversale allo spessore, con una depressione su un lato e un'area rialzata sull'altro. In effetti, la colata si è piegata di qualche decina di micron. Ciò indica che il lago si è formato quando la colata era solida e si è tentati di ipotizzare un restringimento limitato che ha prodotto un'anomalia. "barattolo di olio" distorsione.
È abbastanza chiaro che il difetto è legato al calore e probabilmente riflette i gradienti di temperatura all'interno dell'utensile.
Vesciche
L'apertura di queste protuberanze dalla superficie liscia rivela il loro centro cavo. Le vesciche sono causate dall'espandel gas ad alta pressione intrappolato nei pori di gas che gonfiano la pelle superficiale del getto (figura 1).3). Le bolle si formano quando la lega è troppo debole per contenere le forze generate dal gas interno, quando il getto è troppo caldo. La formazione di bolle si previene riducendo la temperatura del getto al momento dell'espulsione.
Ciò si ottiene aumentando il raffreddamento dello stampo e/o aumentando il tempo di raffreddamento dello stampo. La formazione di bolle può essere attenuata riducendo la quantità di aria intrappolata (si veda la sezione sulla porosità del gas) e utilizzando un'elevata velocità del gate per affinare le dimensioni dei pori del gas.
Crepe
Le cricche superficiali possono avere due cause principali. La prima forma, che si riscontra comunemente in corrispondenza dei cambi di sezione, è quella delle lacerazioni a caldo, in cui l'elevata deformazione locale indotta dal ritiro limitato in prossimità del punto di fusione ha portato a una frattura intergranulare. Il secondo tipo si verifica quando la colata si blocca nello stampo, provocando pressioni significative al momento dell'espulsione. Queste fratture sono tipicamente meno intergranulari e più rettilinee di quelle causate dalle lacerazioni a caldo.
La lacerazione a caldo è più evidente nelle leghe a lungo intervallo di congelamento, come la ZA-27, ed è dovuta principalmente alla forma del componente. Il raffreddamento locale della regione interessata può essere utile. (Per ulteriori informazioni, consultare la sezione dedicata ai lingotti).
La cricca da espulsione deve essere affrontata inizialmente eliminando eventuali problemi dello stampo, come sottosquadri, conicità inadeguata e superfici ruvide. Se si riduce la temperatura dello stampo e si aumenta il periodo di raffreddamento, il getto sarà più forte e quindi in grado di resistere meglio alle forze di espulsione. Tuttavia, se l'incollamento è causato dal ritiro del getto sullo stampo, come ad esempio un foro nel perno d'anima, può essere utile un'espulsione precoce per ridurre il ritiro. Per essere efficace come agente separatore, lo spray per stampi deve coprire adeguatamente la superficie dello stampo.
Trascinamento Marchi
Lo sfregamento tra la colata e lo stampo durante l'espulsione del componente causa segni lungo la linea di trazione (vedi figura 14). I segni di trascinamento sono causati da un tiraggio insufficiente, da sottosquadri e rugosità della superficie, nonché da un'inadeguata spruzzatura dello stampo. È impossibile evitare le rigature quando il getto si restringe strettamente contro il componente. In questi casi, è necessaria la massima conicità possibile e l'ottimizzazione del tempo (temperatura) di espulsione del getto.
Distorsione
Le fusioni piegate, le rientranze o le perforazioni dei perni di espulsione si verificano quando la fusione è troppo debole per resistere alle forze di espulsione (figura 15). Lo stampo deve essere innanzitutto controllato per verificare la presenza di sottosquadri, tiraggio insufficiente e superficie ruvida. Il problema può essere controllato abbassando la temperatura di espulsione del getto. Ciò si ottiene abbassando la temperatura dello stampo e/o aumentando il tempo di raffreddamento dello stesso.
Erosione
L'erosione produce usura e cavità nella superficie dello stampo che possono causare segni sulla colata e problemi di espulsione. Inoltre, riduce la durata dello stampo. La lega fusa consuma fisicamente lo stampo nei punti in cui il flusso di metallo colpisce lo stampo ad alta velocità. L'usura può verificarsi anche nei punti in cui il metallo ad alta velocità produce gorghi e cavitazione idraulica. In entrambi i casi, la riduzione della velocità del metallo riduce la quantità di erosione. L'erosione si riduce anche abbassando la temperatura dello stampo. È più probabile che si verifichi negli stampi che sono temperati sul lato morbido della gamma di durezza.
Il calore Controllo
Un motivo di alette impazzite sulla superficie della colata è dovuto alla rottura della superficie dello stampo (heat checking). La causa è lo stress superficiale indotto dal ciclo di temperatura che si verifica ad ogni colata. La gravità delle sollecitazioni dipende dalla temperatura di fusione della lega. Poiché le leghe di zinco hanno bassi intervalli di fusione, questo difetto è raro e si riscontra solo in stampi che hanno prodotto milioni di getti.
Saldatura
Si tratta dell'accumulo sulla superficie dello stampo di uno strato di lega che aderisce sia fisicamente che chimicamente. La colata è segnata quando la pelle incollata viene strappata via durante l'espulsione e il sottosquadro prodotto dall'accumulo porta anche alla rigatura della colata. La saldatura è più probabile quando le velocità del gate sono elevate e la matrice temperatura è alto. Morire spruzzo mosto essere adeguato in ordine a produrre a protettivo strato su il acciaio superficie.
L'accumulo dovuto alla saldatura è difficile da rimuovere dalla matrice. Questo lo distingue dall'accumulo dovuto all'eccesso di spray della matrice, che di solito può essere eliminato.
Flash
Quando il metallo penetra tra le facce di accoppiamento delle parti dello stampo e le metà dello stampo, si formano strati sottili di materiale estraneo. ous materiale sono sinistra su il getto (figura 16). A prevenire questo il matrici mosto essere fortemente costruito e perfettamente chiuso.
Anche in questo caso, le deviazioni termiche possono portare all'apertura di fessure alla temperatura di esercizio. Se la forza di bloccaggio della macchina è inadeguata alle dimensioni del getto che si sta realizzando, le matrici si separeranno e si formeranno aree estese di bava. Riducendo la pressione del metallo si riduce la probabilità che le matrici si sfaldino. Anche l'aumento del tempo di riempimento, e quindi la riduzione della temperatura del metallo quando raggiunge la linea di divisione, ridurrà la penetrazione tra le facce di accoppiamento.
Dimensionale Coerenza
L'intera questione delle tolleranze dimensionali è trattata a lungo in un altro capitolo di questo manuale. Viene qui menzionato perché la non conformità può essere considerata un difetto di fusione.
La riproducibilità di una dimensione as-cast, colpo dopo colpo, è quasi esclusivamente funzione della costanza della temperatura. Il fattore che influisce maggiormente è la temperatura del getto nel momento in cui viene espulso dalla matrice. StabilisQuesta temperatura migliora la riproducibilità dimensionale e favorisce il mantenimento di tolleranze strette.
A causa degli effetti dell'invecchiamento metallurgico, dopo la colata si verifica un leggero ritiro. La quantità è piccola e riproducibile e rappresenta un problema solo per i componenti specificati con tolleranze molto strette. Se necessario, si può ricorrere a un trattamento termico a bassa temperatura, in genere qualche ora a 95°C, per stabilizzare la colata.
Trimming e Abitoing
Generale problemi in questo area di il produzione operazione sono inaccettabile cambiamento di contorno dovuto a oltre... asportazione di metallo e distorsione dovuta a manipolazione approssimativa o a problemi di allineamento.
Interruzione Difetti
Le porte sottili possibili nella fusione di leghe di zinco fanno sì che in molti casi si possa optare per la troncatura piuttosto che per la rifilatura alla pressa. La troncatura può essere manuale o meccanica con macchine a coclea o a buratto. Un taglio netto dipende dalla forma e dallo spessore della porta.
Earring
I cancelli leggermente curvi possono essere rotti ma tendono a lasciare "orecchie" sul getto quando si utilizzano cancelli conici. A seconda del progetto e della direzione di curvatura, anche su un cancello dritto la terra può essere lasciata in fieri rispetto al getto..
Break in
In questo caso, la forma del cancello e la direzione di piegatura hanno fatto sì che la frattura entrasse nel getto, lasciando così un sottosquadro nel getto.
Linea del cancello Porosità
Anche quando il cancello si rompe in modo netto, sul getto rimane un testimone. Il metallo esposto è diverso dalla pelle circostante del getto; è tipico dell'interno del getto e può quindi contenere porosità (figura 17). Quanto più spesso è il cancello, tanto più è probabile che questa porosità sia visibile. La quantità di linea del cancello porosLa microporosità sarà influenzata dai fattori trattati nella sezione Porosità di questo capitolo. Anche se non visibile, la microporosità esposta può causare problemi dopo il rivestimento.
Stampa Trim Difetti nella pressofusione di zinco
Punteggio
L'errato posizionamento del componente e/o l'errato allineamento e gioco dello stampo possono portare lo stampo di rifilatura a rasare il lato della colata.
Pieghevole
Quando la scoria è sottile e si estende solo per una breve distanza, la duttilità della lega è tale che la scoria può piegarsi piuttosto che essere tagliata. Il risultato è una sottile piega di metallo sulla superficie del componente. Se questo è un problema, può essere preferibile eseguire deliberatamente una scottatura trasversale, piuttosto che una chiusura infruttuosa, in modo da avere uno spessore definito da tagliare con l'utensile di rifilatura.
Finiturag Difetti nella pressofusione di zinco
Un'asportazione eccessiva della superficie espone la microporosità. Questa può non essere visibile, ma può causare problemi se il getto viene successivamente rivestito.
Barrellinog/Vibropolihing Difetti
Scala
Eccessivo trattamento di pesantemente doppiato fusioni può piombo a il giri sollevamento o diventando completamente staccato (figura 18).
Lucidatura Difetti
Un'eccessiva asportazione di metallo espone la microporosità. La comparsa di piccole protuberanze e di code di cometa è dovuta a a particelle dure nella colata dovute a contaminazione metallica. Come nel caso della barilatura e della vibrolucidatura, tL'azione di brunitura nasconde solo i difetti superficiali, come ad esempio i lapsus. La discontinuità sottostante è ancora presente e può causare problemi in seguito.
Lavorazione meccanica e assemblaggio Difetti nella pressofusione di zinco
Strumento Indossare
L'usura rapida degli utensili da taglio può essere dovuta a particelle dure nella lega derivanti dalla contaminazione della fusione. Le cause e le misure di controllo per evitarlo sono trattate nella sezione Lingotto. L'usura e la rottura possono anche essere causate dalla penetrazione degli utensili in grandi pori di gas o di ritiro. La prevenzione delle porosità è trattata nella sezione Colata.
Esposto Porosità
La rimozione del rivestimento superficiale sano può esporre porosità sulle facce lavorate, ad esempio sulle flange o sui fori. Il controllo della porosità è trattato nella sezione Colata.
Fracture
Le operazioni di rivettatura e piegatura sono frequentemente utilizzate per assemblare colata in lega di zincos. Se i rivetti e le alette non sono ben fatti, si può verificare la frattura di questi elementi. Le superfici devono essere prive di eccessivi risvolti e cricche (vedere la sezione Colata). Il processo di invecchiamento che avviene dopo la colata influisce sulla duttilità. Il processo di invecchiamento è minimo, circa tre settimane dopo la colata. La duttilità della lega aumenta notevolmente con la deformazione a temperature moderatamente elevate.
Polvere di Coating difetti di pressofusione di zinco
In questa sezione vengono esaminati i difetti che si verificano durante il rivestimento e quelli che si verificano durante il servizio. Solo quelli difetti causato da difetti in il getto sono coperto. A di più completo copertura, che comprende difetti in il cappotto stesso, è riportato negli opuscoli "Placcatura di zinco fusioni" e "Rivestimento in polvere di stampi in zinco fusioni" pubblicati dalla Zinc Development Association, Londra, Regno Unito.
Distorsione
La resistenza della lega di zinco diminuisce con la temperatura, quindi alle temperature del forno di verniciatura è piuttosto debole e anche la temperatura del bagno di placcatura ha un certo effetto. Pertanto, se i getti sono mal supportati o le maschere esercitano una forza elastica troppo elevata, i getti si deformano. La deformazione può verificarsi anche a causa dell'alleggerimento delle tensioni della colata. Il rapido raffreddamento durante la colata può bloccare le tensioni causate dal ritiro differenziale. Il livello di stress dipende in larga misura dalla forma del componente.
Irregular Surface
L'aspetto a squame di pesce dei giri freddi si manifesta attraverso lo strato di placcatura e, se grave, anche attraverso lo strato di vernice più spesso. I confini dei laghi si presentano come un segno di increspatura sulla superficie placcata o verniciata. Le cause e i rimedi di questi difetti sono descritti nella sezione Colata.
Plating Difetti nella pressofusione di zinco
Vesciche
Le bolle nella placca sono un difetto di fusione (le bolle e altri difetti possono essere causati anche da problemi di processo di placcatura) e sono causate dall'intrappolamento di terra, gas e soluzioni di placcatura nelle imperfezioni della superficie. La formazione di gas dietro il rivestimento impermeabile ne provoca la formazione di bolle e persino la frantumazione. L'espansione causata dai prodotti di corrosione prodotti dalla reazione della colata e delle soluzioni corrosive intrappolate avrà un effetto simile.
Se l'intrappolamento è causato da giri a freddo, sia la superficie di colata che la piastra possono sollevarsi. Si noti che le pieghe causate dalla piegatura del flash sulla superficie producono problemi identici a quelli dei laps. In caso di messa in servizio, il danneggiamento dello strato placcato provoca la corrosione. (Figure 7 e 19).
I getti che presentano una superficie con lamine fredde o una superficie in cui sono state esposte porosità o microporosità, possono produrre bolle nello strato placcato. Per maggiori informazioni su questi difetti, consultare le sezioni Colata e Ravvivatura.
Pain.t. Difetti nella pressofusione di zinco
Vesciche
Le bolle sulla superficie verniciata di un getto possono essere di due tipi. È fondamentale distinguerle, poiché le azioni correttive necessarie sono diverse.
Le bolle di dimensioni moderate che possono emergere sui lati opposti della colata sono generate dalla porosità del gas all'interno della colata (figura 13). Questo può essere verificato raschiando lo strato di vernice o tagliando la bolla. Si tratta di un blister di gas se il difetto è nella fusione e non nella vernice. Il problema si verifica perché la lega di zinco è debole alle temperature di cottura della vernice, causando il rigonfiamento della colata a causa dell'alta pressione del gas all'interno dei pori.
La temperatura di cottura è fondamentale e, se la procedura prevede diverse circostanze, si dovrebbe scegliere l'opzione di una cottura più lunga ma a una temperatura più bassa. I getti che verranno cotti ad alte temperature (200°C) devono contenere una quantità minima di gas intrappolati e finemente dispersi.
Le bolle più piccole sono causate dalla risalita di gas dalla superficie di colata e dall'incastro nella pellicola di vernice. A volte il gas fuoriesce, ma la vernice che si solidifica è troppo dura per ricostituire una superficie liscia, dando origine a una bolla simile a un vulcano in miniatura (figura 20). Per evitare questi problemi, la colata deve essere priva di discontinuità superficiali che potrebbero intrappolare gas e terra, come giri freddi, pieghe e porosità visibili. La cottura prima dell'aggiunta dello strato organico consentirà alla colata di espellere i gas e di risolvere il problema.
Scheggiato Vernice
Il distacco della vernice può talvolta essere causato da un difetto di fusione o da una manipolazione impropria dopo la verniciatura. Se una piega (ad esempio, un'intermittenza piegata) viene verniciata e poi sottoposta a urti, può staccarsi, rivelando la superficie sottostante non rivestita.
Manipolazione, stoccaggio e imballaggio
Una manipolazione inadeguata potrebbe causare danni alla superficie o distorsioni della pressofusione. Negli utensili a più cavità, i collegamenti di fusione tra componenti fragili possono essere efficaci per fornire un supporto. La quantità di danni superficiali accettabili dipende dai requisiti di qualità e dal rivestimento utilizzato.
Quando i getti nudi devono essere conservati per un qualsiasi periodo di tempo, devono essere asciutti. L'umidità favorisce la formazione di ruggine bianca e la corrosione superficiale. Se l'acqua di spruzzatura o di tempra si è degradata, con conseguente sviluppo di composti acidi, la corrosione può essere più grave. I getti devono essere rivestiti o verniciati non appena possibile dopo la colata e la lucidatura per ridurre il rischio di contaminazione superficiale.
Le fusioni devono essere imballate in materiali asciutti, poiché il cartone umido crea acidi che danneggiano e anneriscono le fusioni di zinco.
0 commenti