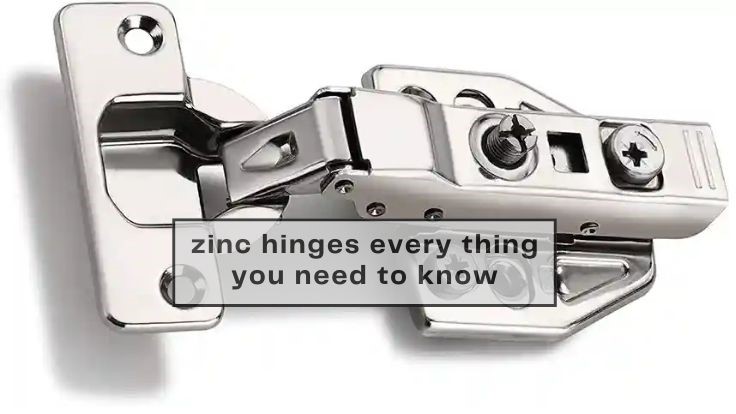
Zinc Hinges Everything You Need To Know
Zinc plated hinges have established a dominant position in providing smooth mechanical motion and secure fastening in doors, cabinets, gates and industrial enclosures in both commercial and residential domains. In particular, if those items are to be used outdoors,...
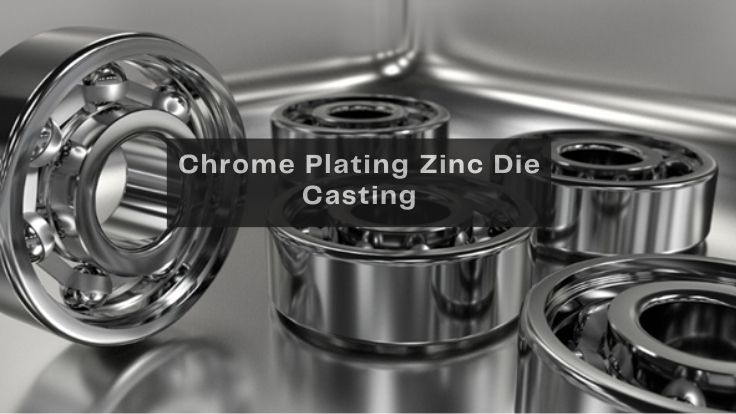
Chrome Plating Zinc Die Casting
Chrome plating zinc die casting parts is one of the most effective ways to attain both durability and aesthetic value. In the light of the modern manufacturing world, it (function combined with the look) is a necessity, even in industries like automotive, electronics,...
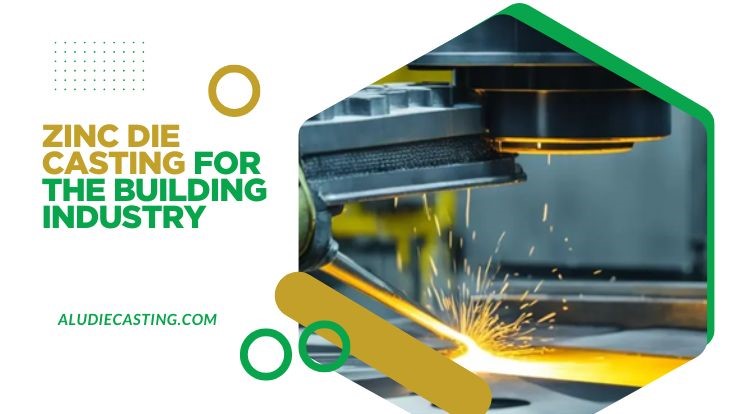
Цинковое литье под давлением для строительной промышленности
Emerging technologies and materials are constantly built into the building industry to help the constantly evolving fields with sustainability, precision, durability and cost efficiency needs. Zinc die casting is one of the less commonly highlighted, yet critically...

Литье под давлением цинка для автомобильной промышленности
Zinc is a multipurpose and important metal with important roles in a wide industrial, commercial, and biological applications. Zinc is used industrially, in construction, and for protective coatings because of its high corrosion resistance and bluish-silver...
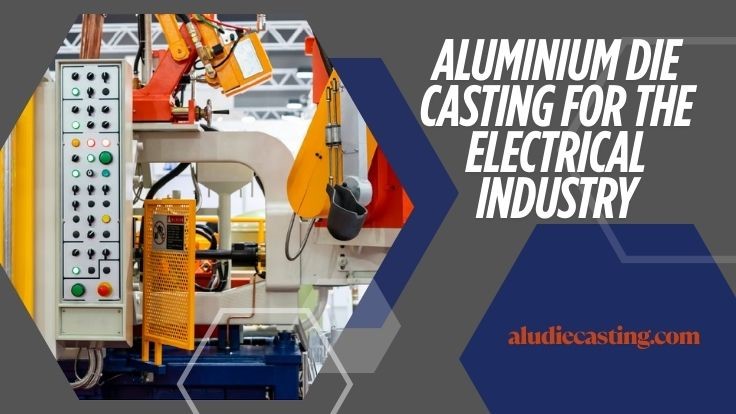
Литье алюминия под давлением для электротехнической промышленности
Современное общество в значительной степени зависит от электротехнической промышленности, которая является одним из его важнейших элементов. Рост отрасли как в промышленных энергосистемах, так и в бытовой электронике зависит от производительности, точности и инноваций. В...
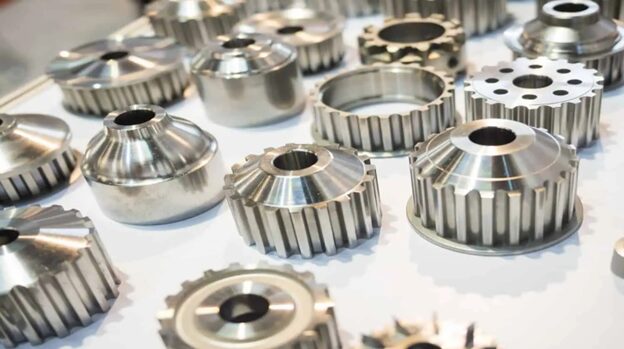
Алюминиевое литье под давлением для строительства
Одна из таких технологий производства, литье алюминия под давлением, стала популярной, поскольку обеспечивает экономичность и эффективность массового производства сложных, легких и прочных компонентов. Процесс впрыска расплавленного алюминия в точно спроектированную форму под...
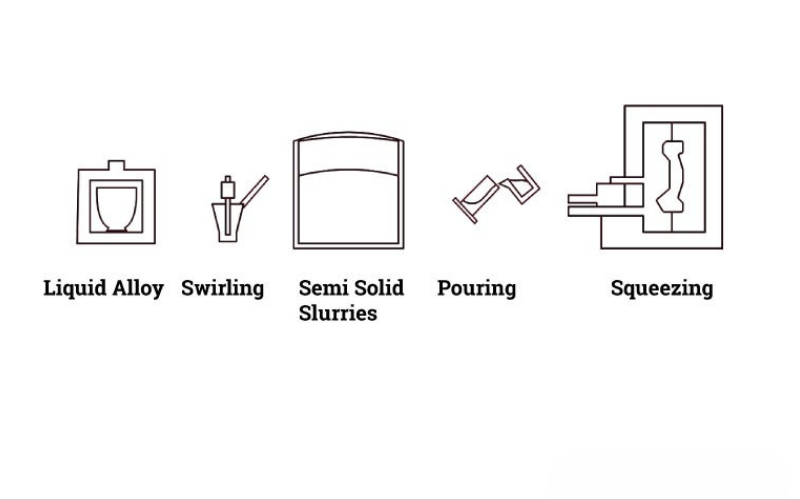
Полутвердое литье под давлением (SSDC): Преимущества и области применения
Откройте для себя возможности полутвердого литья под давлением (SSDC) для создания сложных, прочных металлических деталей с минимальным количеством дефектов и экономией энергии. Узнайте о реокастинге, тиксокастинге и их применении.
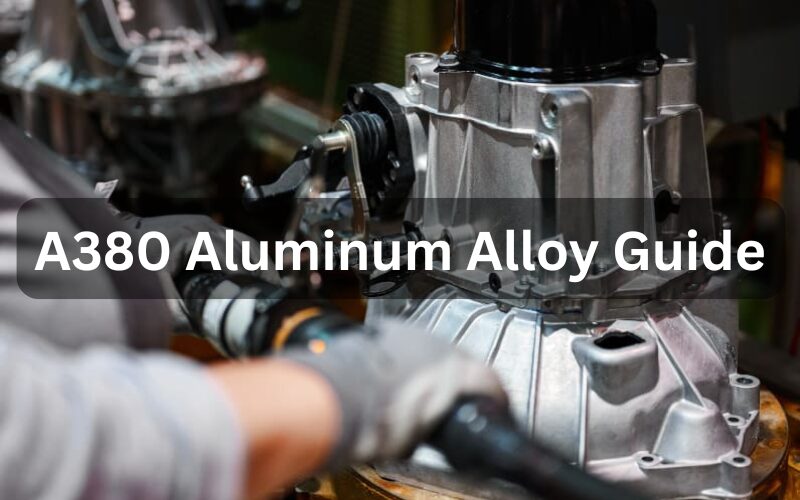
Алюминиевый сплав A380: Свойства, состав и применение
Откройте для себя алюминий A380: Универсальный сплав, известный своей превосходной литейной способностью и теплопроводностью. Ознакомьтесь с его свойствами, составом, применением и термообработкой.
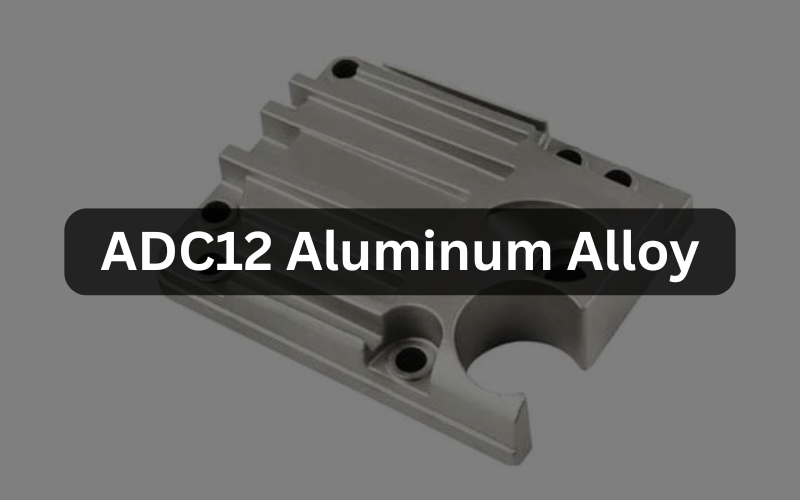
Что такое алюминиевый сплав ADC12? Руководство по свойствам и литью под давлением
Алюминиевый сплав ADC12 - это экономически эффективный алюминиевый сплав, идеально подходящий для литья под давлением. Узнайте о его свойствах, применении, преимуществах и сравнении с ADC10 и ADC14.
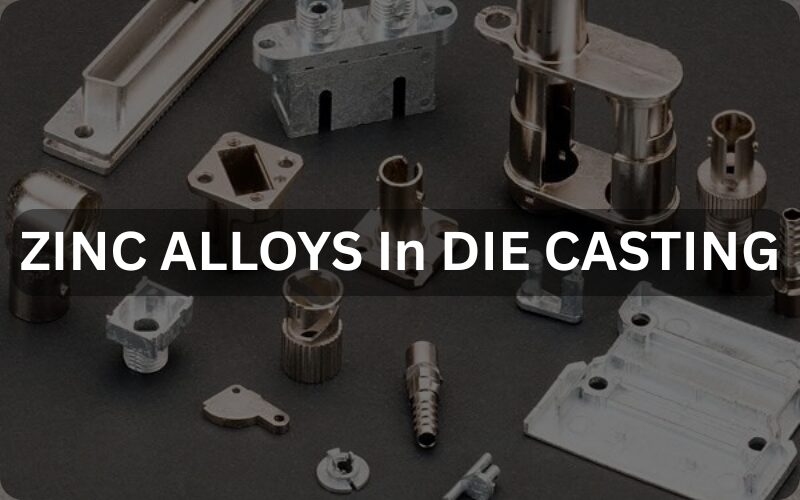
Литые цинковые сплавы: Руководство по типам, свойствам и применению
Изучите литые цинковые сплавы: Zamak, ZA, AcuZinc и другие. Поймите их уникальные свойства, преимущества, ограничения и технологии производства, такие как литье под давлением.
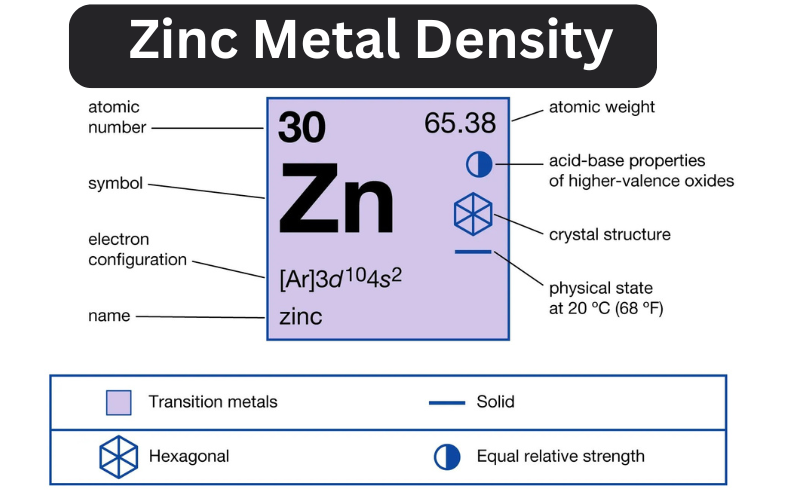
Плотность металла цинка: Свойства, применение и принцип работы
Узнайте о свойствах плотности металлического цинка, включая его плотность (7140 кг/м³), электронную конфигурацию и кристаллическую структуру. Ознакомьтесь с областями применения цинка в производстве, от строительства до электроники, и узнайте, как плотность влияет на его использование в литье под давлением и балласте.
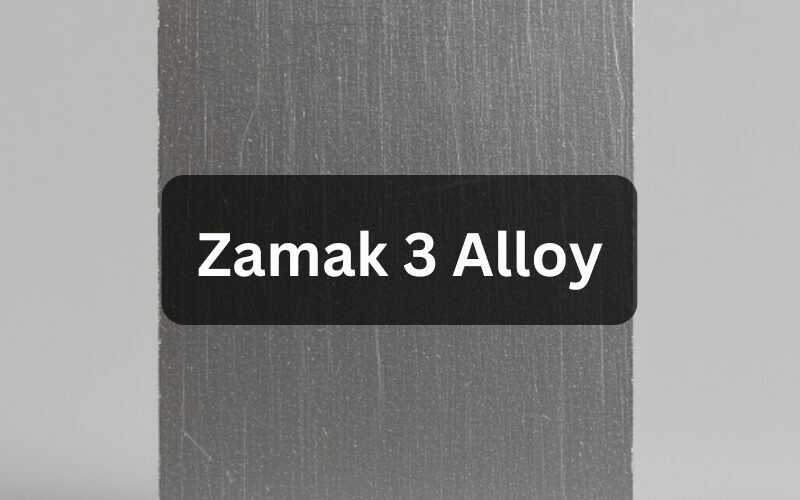
Сплав Zamak 3: Состав, свойства и руководство по обработке
Zamak 3: полное руководство по его составу, свойствам (механическим и физическим), применению (автомобильная промышленность, электротехника и т.д.), особенностям обработки и коррозионной стойкости.
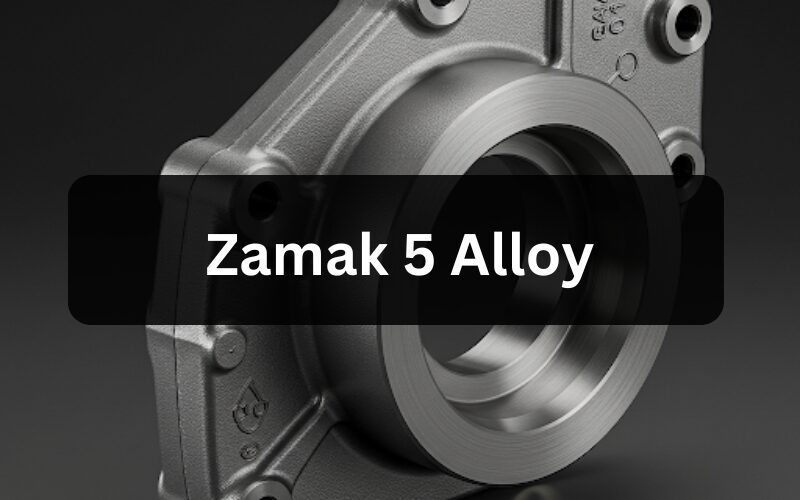
Сплав Zamak 5: Состав, свойства, применение и преимущества
Узнайте все о сплаве Zamak 5 - его химический состав, физико-механические свойства, процесс литья и основные преимущества. Сравните Zamak 5 и Zamak 3 для ваших производственных нужд.
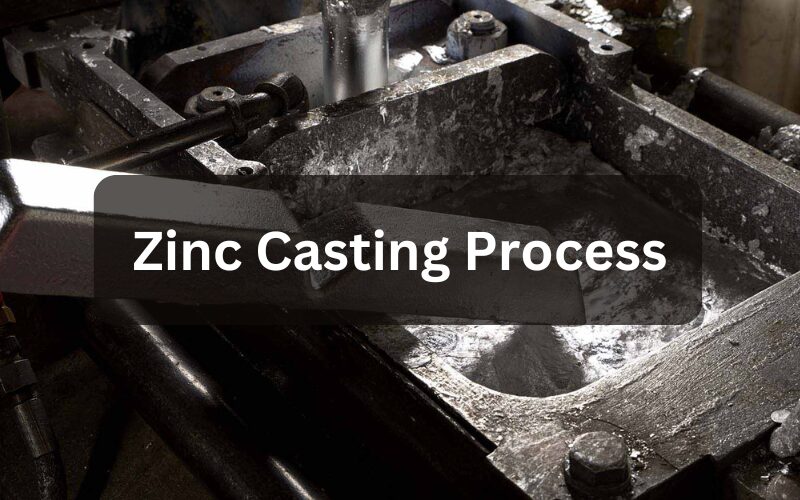
Литье цинка: Процесс, применение и преимущества
При литье цинка используется расплавленный цинк. Расплавленный цинк поступает в форму. Форма придает цинку форму по мере его остывания. Таким образом, получаются прочные детали. Литье цинка подходит для быстрого изготовления большого количества деталей. Процесс литья цинка используется для производства прочных деталей с точной точностью.....
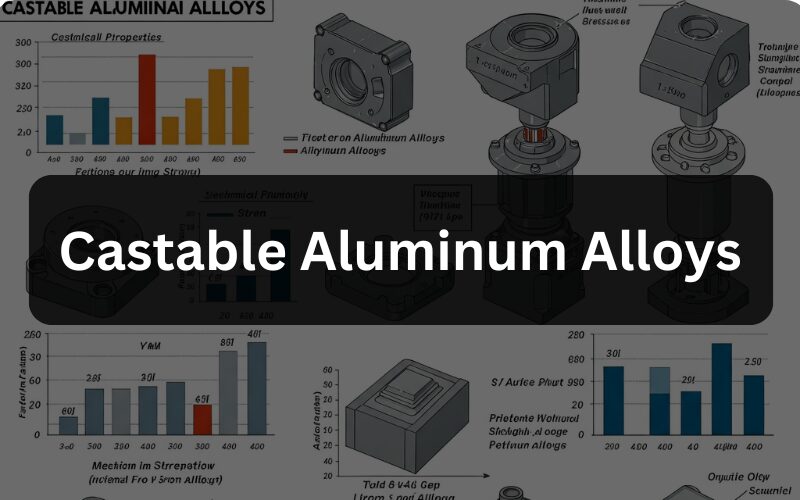
Литейные алюминиевые сплавы: Состав, свойства и области применения
Ознакомьтесь со свойствами литейных алюминиевых сплавов, таких как A380, A356 и 6061. Узнайте об их прочности на разрыв, коррозионной стойкости и влиянии на такие отрасли промышленности, как автомобильная, аэрокосмическая и электронная.
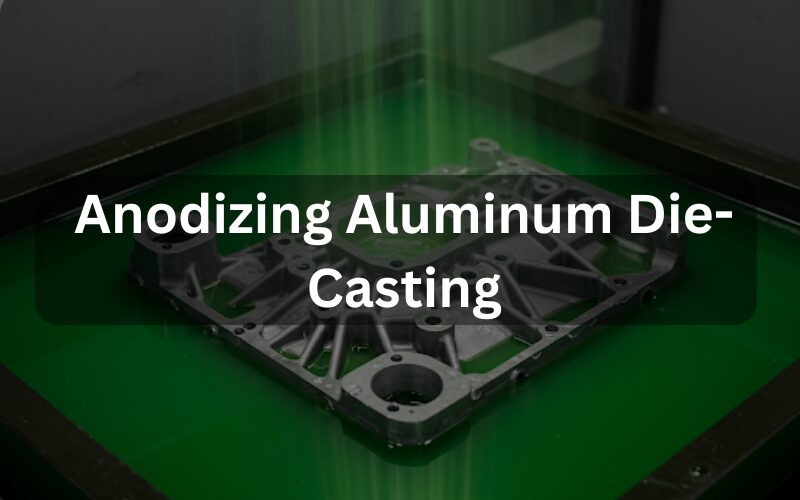
Анодирование алюминиевого литья под давлением | Полное руководство
Анодирование литого под давлением алюминия создает защитную поверхность. Сначала деталь для литья алюминия очищается. Затем под действием электрического тока в кислотной ванне образуется оксидный слой. Этот слой укрепляет алюминий, повышая его износостойкость. Наконец, анодированная деталь...
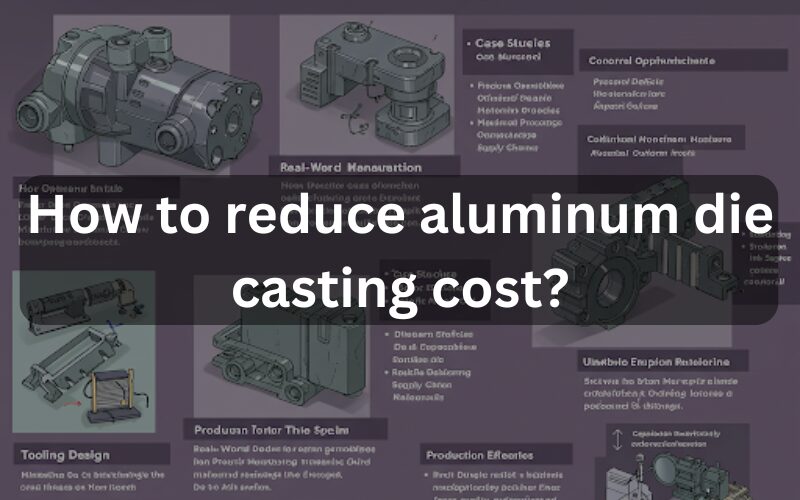
Как снизить стоимость литья алюминия под давлением?
Стоимость литья алюминия под давлением в расчете на 1 кг составляет примерно от 4$ до 6$ USD. Аналогично, стоимость оснастки может составлять от 8,000$ до 15,000$ USD. Если у вас простой дизайн, вы можете сэкономить $5,000-$10,000 на стоимости оснастки. Более того, правильный алюминиевый сплав, как у A380, может сократить до 10%...
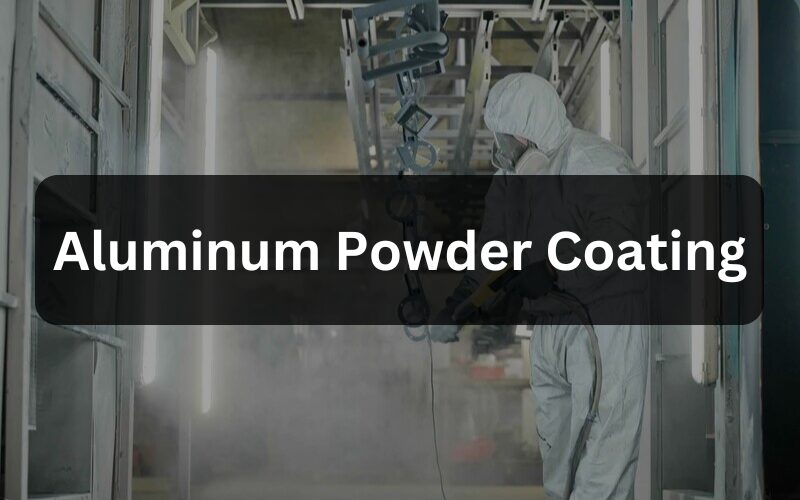
Что такое порошковая окраска алюминия? Полное руководство
При порошковом покрытии алюминия сначала очистите алюминий. Затем распылите на него сухой порошок. Затем запеките его в духовке, чтобы расплавить порошок. И наконец, дайте ему остыть. Получается прочное, защитное покрытие. Можно использовать порошок разных цветов. Покрытие получается прочным и долговечным.
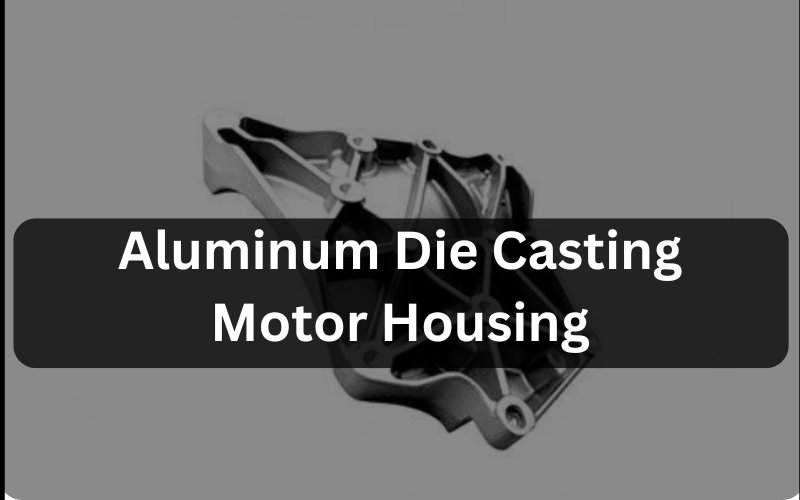
Алюминиевый литой корпус двигателя | Полное руководство
Литье алюминия под давлением - распространенная технология изготовления корпусов двигателей. Она достаточно эффективна, чтобы справиться с любым уровнем сложности конструкции. Процесс начинается с нагрева алюминия до температуры плавления и установки его в форму. Корпуса двигателей, изготовленные из алюминия, содержат меньше...
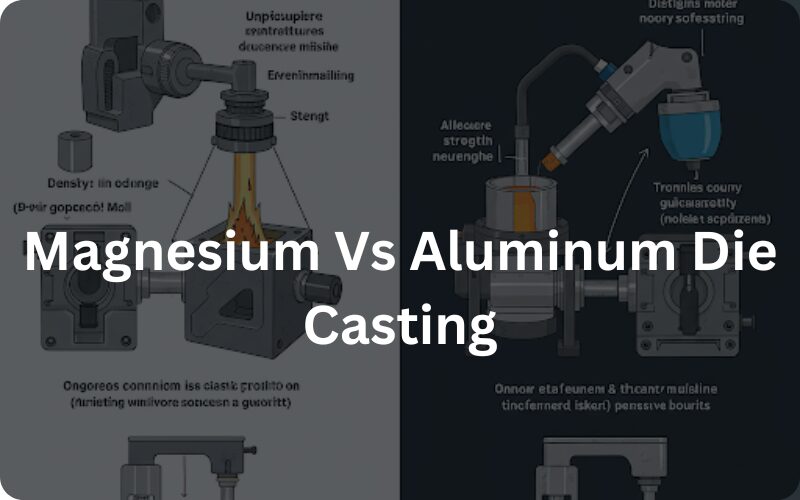
Разница между литьем магния под давлением и литьем алюминия под давлением
Литье магния под давлением и литье алюминия под давлением - это способы изготовления металлических деталей. Горячий расплавленный металл заливается в формы для создания фигур. Из магния получаются очень легкие, но прочные для своего веса детали.