Our most important asset is our people – people in our Die Casting Manufacturer who are well trained, highly motivated and know how to put our state-of-the-art equipment to its very best use, to the ultimate benefit of our customers in terms of cost savings and speed to market. We have created an environment in which the manufacturing process has been streamlined for maximum efficiency, and our people are well schooled in the principles of lean manufacturing.
Value add CNC machining is linked to our die casting operations, using cellular technology and demand-pull triggering of requirements. We use single-piece flow where applicable, and we modify the manufacturing process, to the extent possible to meet any customer’s individual requirements.
We have developed strategic relationships with global tool manufacturers who can take our customer’s final model and convert it quickly and efficiently into a tool to produce parts.
We use rapid prototyping tools to obtain dies in less than half the lead time it takes to deliver the same die from other manufacturers. Program managers monitor the progress and critical path to ensure timely delivery of the tooling.
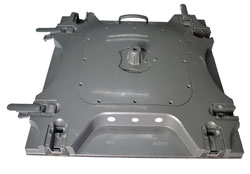
Our equipment and manufacturing processes include:
- CAD and Solid Modeling Capabilities
- Rapid tooling and prototyping for fast implementation of ideas into products using the latest technology and analytical tools.
- Surface treatment methods and technologies for reduced soldering and die maintenance
- Parts and process approval using PPAP procedures
- Six Sigma problem solving techniques
- Value added machining and finishing department with advanced machining capabilities to produce parts ready for the customer’s application
- Single Minute Exchange of Dies program
- State-of-the-art process and shot monitoring equipment form continuous process control
- Automated processes ensuring consistent high quality
Each customer is assigned a Product Engineer from our Technical Staff. Our Engineer will assist you in all phases of a project and will be your single source at CNM TECH for all design and tooling related needs.
Each project is overseen by your Engineer. This personal attention begins with order placement through scrutiny by our Advance Quality Planning (AQP) team, which is comprised of a cross section of associates from Quality, Engineering and Manufacturing.
Our Engineer then oversees the tool design, tool build, sampling and dimensional verification.
Die casting mold and gating is designed using UG software. Starting with placement of a purchase order, you will receive project status updates every week until the project is approved for production.
Die casting Parts in zinc and aluminium alloys (to a casting weight of 12 Kg.)
Die die casting parts design and manufacture.
Volume component production.
Vibratory finishing
0 Comments