Les rivets sont des attaches mécaniques permanentes. Ils sont utilisés pour assembler deux ou plusieurs matériaux. Il existe trois types de rivets les plus courants : les rivets pleins, les rivets aveugles (comme les rivets pop) et les rivets semi-tubulaires.
Principaux enseignements de l'article :
- Définition du rivet
- Types de rivets
- Applications des rivets
- Techniques de pose des rivets
- Comparaison entre le rivetage et les autres méthodes de fixation
Qu'est-ce qu'un rivet ?
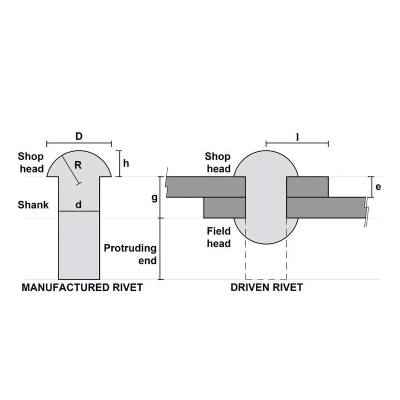
Rivets sont des attaches semi-permanentes. Elles sont utilisées pour assembler les différentes parties des applications. Il s'agit d'une forme cylindrique avec une tête d'un côté et une queue de l'autre.
Avant d'être installée, la partie arrière des rivets est insérée dans l'outil. Elle subit ensuite le processus d'application d'une force de compression. Cette force déforme les rivets en une forme plate, reliant une pièce à l'autre.
Ces attaches mécaniques sont généralement fabriquées en acier doux, en laiton, en cuivre et en acier inoxydable. aluminium. Les fabricants utilisent les rivets pour plusieurs projets et la fabrication de pièces industrielles. Par exemple, les ponts, les opérations de tôlerie, les charpentes, les navires et les secteurs aérospatiaux.
Types de rivets
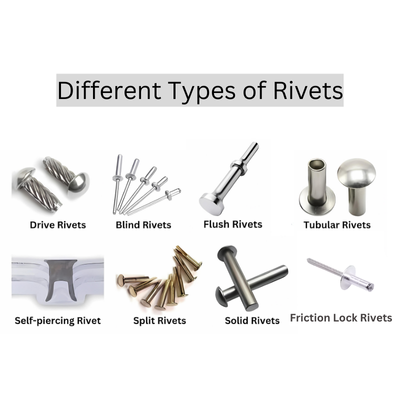
Les rivets sont disponibles sous différentes formes et types, avec différentes utilisations. Mais nous allons essayer de parler des types spécifiques qui sont typiquement utilisés dans toutes sortes de travaux, des pièces légères aux pièces lourdes et performantes. Découvrons-les :
- Rivets pleins
- Rivets aveugles
- Rivets d'entraînement
- Rivets affleurants
- Rivets autoperceurs
- Rivets fendus
- Rivets tubulaires
- Rivets à friction
Rivets pleins
Les rivets pleins sont les méthodes classiques pour relier les matériaux. Ces attaches contiennent des formes rondes, également connues sous le nom de rivets ronds. La déformation de la queue peut être réalisée à l'aide d'outils de martelage ou de sertissage. Ces rivets assemblent les pièces tout en les rendant inviolables et résistantes aux vibrations.
L'acier, l'aluminium et le cuivre sont des matériaux qui conviennent à la fabrication de rivets pleins. Ces types d'attaches sont utilisés dans des applications aéronautiques, aérospatiales, de construction, de produits ménagers, d'électronique, etc.
Rivets aveugles
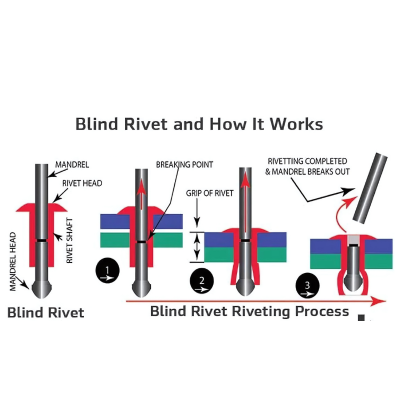
Les rivets aveugles sont connus pour être des rivets pop, construits avec des formes cylindriques avec une tête et un mandrin au centre. Il s'agit de rivets tubulaires qui peuvent être installés dans des pièces percées.
Des riveteuses et des outils uniques sont choisis pour placer les rivets sur les pièces à usiner. La force est appliquée pour pousser le mandrin à travers le rivet. De cette façon, la force dilate le tube entre l'outil et le mandrin pour bloquer la tôle.
Les rivets aveugles sont inaccessibles et utilisés pour assembler un côté des pièces. Ils présentent une grande résistance au cisaillement et à la traction. Les applications courantes de ces rivets sont la construction navale, l'électronique, l'armée, l'aérospatiale et les applications domestiques.
Rivets d'entraînement
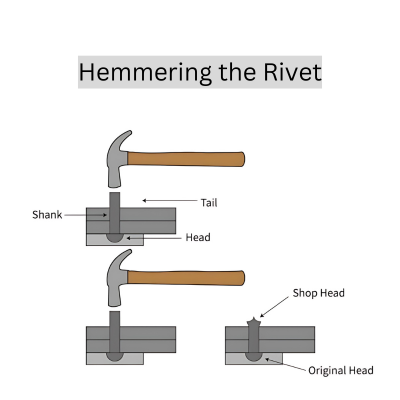
Les rivets d'entraînement sont similaires aux fixations aveugles. Ils sont fabriqués à l'aide d'un mandrin court qui traverse le centre des rivets. Les fabricants peuvent fixer les rivets d'entraînement à l'aide d'un marteau ou d'un outil de blocage.
Ces rivets peuvent être utilisés pour fixer des composants automobiles, des panneaux architecturaux et des travaux de maçonnerie. Ils ne percent pas les trous des blocs, des panneaux ou des feuilles pendant le processus de fixation.
Rivets affleurants
Les rivets à fleur sont conçus avec des têtes qui affleurent les surfaces métalliques à fixer. Ils sont également connus sous le nom de rivets à tête fraisée. Cela minimise les traînées aérodynamiques et maintient les surfaces lisses.
Les fabricants utilisent des rivets affleurants pour les applications où l'apparence est importante. Ces arbres sont couramment utilisés pour fabriquer des pièces externes d'avions et d'autres applications industrielles, comme l'automobile et la marine.
Rivets autoperceurs
Les rivets autoperceurs sont construits avec des extrémités en biseau ou des pointes chanfreinées. Ces catégories de rivets peuvent être assemblées sur des pièces sans percer de trous ni perforer la surface.
Les fabricants placent les deux composants sur la presse. Ils insèrent des rivets auto-perçants dans le support de l'ébauche. Ce dernier exerce alors une force en pressant les rivets sur la face supérieure de la pièce.
Les opérateurs cessent de percer le rivet jusqu'à ce que sa moitié soit encastrée dans la seconde partie. C'est la procédure la plus rapide pour réaliser des connexions étanches ou des joints de gaz utilisés dans les secteurs de l'aérospatiale.
Rivets fendus
Les rivets fendus ou rivets bifurqués sont fabriqués en divisant l'arbre ou ses extrémités opposées en deux jambes distinctes. Les pièces comportant des trous pré-percés sont assemblées à l'aide de rivets fendus. Un marteau est utilisé pour aplatir les pattes fendues des rivets.
Les matériaux souples et légers peuvent être assemblés à l'aide de ces rivets, comme le plastique, le textile et les feuilles de métal fines. Cependant, ils ne constituent pas un bon choix pour fixer des articles à haute performance.
Rivets tubulaires
Les rivets tubulaires sont des attaches en forme de tube. Ces arbres sont constitués d'une tête à une extrémité, d'une tige et d'un tube partiellement creux de l'autre côté.
Les rivets tubulaires n'ont pas besoin d'une force de compression élevée pour se déformer, contrairement aux rivets pleins. Vous pouvez assembler n'importe quelle pièce en utilisant la technologie du formage à froid, où les parois du trou s'aplatissent vers l'extérieur pour assembler les pièces.
Ce rivet est l'option préférée pour les applications commerciales d'appareils électriques, de conduits de chauffage, de ventilation et de climatisation, et d'autres pièces à faible risque.
Rivets à friction
Les rivets à friction sont les types de rivets aveugles qui sont fabriqués sous forme de coupole ou d'enfoncement. Ces rivets sont également appelés rivets autogrippants. Ils ressemblent à des boulons qui utilisent la pression interne de la tige pour dilater l'arbre. Les tiges de ces rivets s'enclenchent sur la surface inférieure des pièces en raison de la présence de tensions élevées. Les fabricants utilisent les rivets à friction pour réparer les applications aéronautiques telles que les feux.
Applications des rivets
Au fil du temps, les industries ont eu recours aux fixations par rivets pour fabriquer leurs multiples composants avec des joints solides. En fixant les pièces multiples, les rivets éliminent les mouvements internes et les vibrations.
Applications spécifiques à l'industrie
- Applications dans l'aérospatiale
- Automobile
- Secteurs de la construction.
Applications dans l'aérospatiale
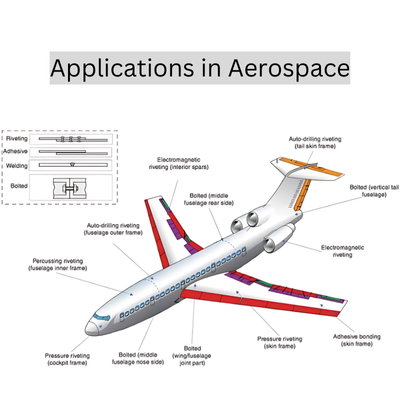
En général, des matériaux solides et résistants à la corrosion, comme l'aluminium, le cuivre et l'acier, sont utilisés dans les applications aérospatiales. Les ingénieurs assemblent les pièces de l'avion en appliquant des fixations par rivets. Ces rivets sont généralement fabriqués à partir de composites d'aluminium, ce qui permet d'alléger les pièces non structurelles. Ils alignent et forment de multiples pièces, notamment
- Cadres de fuselage
- cadre de la peau de la queue
- Portes et trappes
- Les longerons intérieurs
- cadre du cockpit
- Fixations du train d'atterrissage
- Nacelles et supports de moteur
- Structures des ailes
Automobile
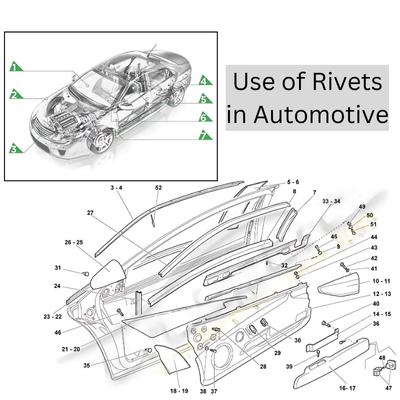
Les rivets à faible poids fabriqués en alliage d'aluminium sont le choix préféré des ingénieurs pour alléger le poids des pièces automobiles. La diversité des utilisations des rivets comprend la déformation pour assembler des pièces en aluminium, en acier et en cuivre. Ce sont les pièces des véhicules sur lesquelles les rivets sont appliqués :
- Panneaux de carrosserie
- Châssis et cadre
- Boîtiers de batterie
- Pièces de suspension
- Structure de collision, zones de déformation
- Portes et fenêtres
- Systèmes d'échappement
Secteur de la construction
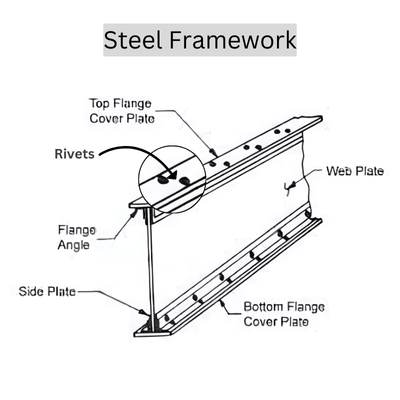
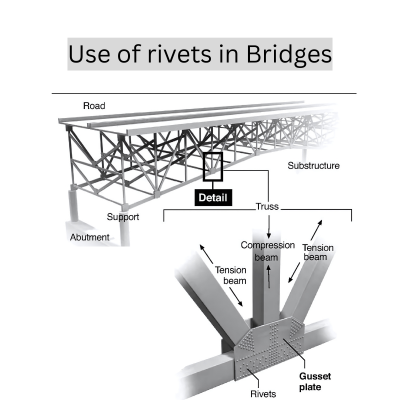
L'assemblage de pièces structurelles et non structurelles peut se faire à l'aide de rivets. Ils sont très efficaces dans les applications de construction. La fixation par rivets est l'étape la plus facile à mettre en œuvre pour assembler plusieurs composants. Vous pouvez en tirer parti pour fabriquer les pièces suivantes :
- Charpente et poutre en acier
- Ponts
- Toiture métallique
- Systèmes de façade et de bardage
- fenêtres et murs-rideaux
- Mains courantes et garde-corps
- Escaliers et sorties de secours
Le processus de rivetage
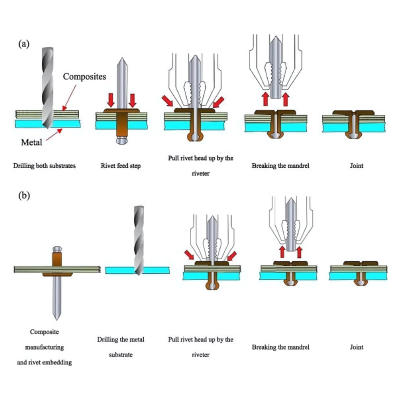
Techniques de pose des rivets
Essayez toujours de suivre chaque étape sans sauter pour obtenir des assemblages durables et sûrs des pièces à l'aide de rivets. Ces étapes peuvent comprendre
- Outils
- Processus d'installation étape par étape
Outils
- Pistolets à rivets
- Barres de renfort
- Perceuses et pinces
Processus d'installation étape par étape
- Préparation
- Placement des rivets
- Rivetage
- Inspection de la qualité
Préparation
Nettoyer la surface des pièces destinées à être assemblées par rivetage. Utilisez un mélange d'eau et de détergent pour éliminer les traces collantes et les taches sur le métal.
En avançant, marquez le métal avec les points corrects et une dimension légèrement supérieure à celle des rivets. Vous pourrez ainsi réaliser les trous par perçage.
Placement des rivets
Façonnez les têtes de rivets à l'aide de barres de flambage. Prenez ensuite le pistolet à rivets pour commencer le processus de rivetage. Placez l'extrémité opposée du rivet dans les fentes du pistolet. Vous pouvez ajuster la taille des boulons du pistolet en fonction de la taille des rivets.
Rivetage
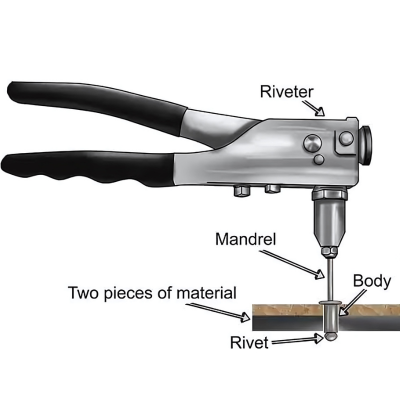
Placez les deux pièces de fixation ensemble, de manière équivalente aux trous percés. Saisissez ensuite la pince à rivets avec les rivets insérés pour les placer sur la surface du trou. Appuyer manuellement sur le pistolet pour tirer la queue contre la tête du rivet jusqu'à ce qu'elle s'aplatisse et que la queue se brise.
Inspection de la qualité
Inspecter minutieusement les pièces afin d'identifier toute fissure ou cassure, en veillant à ce que la finition soit affleurante. Ces étapes supplémentaires permettent d'assurer la garantie de qualité contre les défaillances structurelles. Cela est nécessaire pour des raisons de sécurité.
Méthodes d'inspection
- Inspections visuelles
- Contrôle par ultrasons
- Essai de cisaillement
Inspections visuelles
L'équipe chargée de la gestion de la qualité doit examiner minutieusement chaque pièce. Elle peut vérifier les défauts des têtes de rivets fissurées, un mauvais alignement ou des dommages de surface sans utiliser d'outil spécifique.
Contrôle par ultrasons
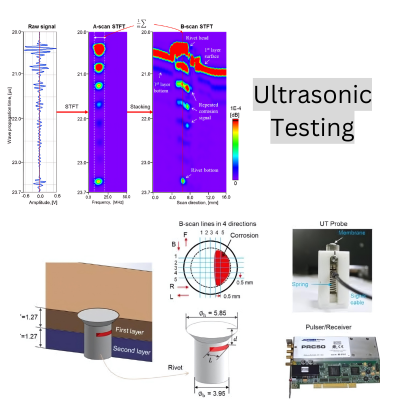
Utilisez des outils à ultrasons pour inspecter des pièces complexes et détaillées. Cette technique d'essai non destructive permet d'identifier les faux rivets, en montrant les rayons qui traversent les métaux assemblés.
Essai de cisaillement
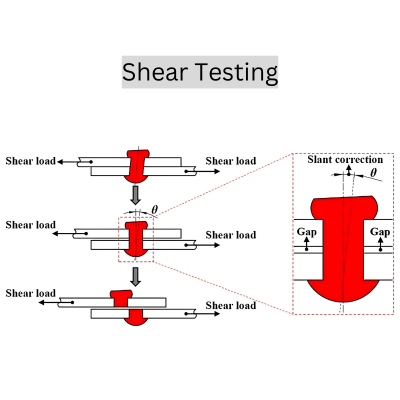
Vérifiez la résistance des pièces fixées en appliquant la force de cisaillement. Vous saurez ainsi si les pièces fixées résistent ou non aux pressions opérationnelles.
Analyse comparative entre le rivetage et les autres méthodes de fixation
Aspect | Rivetage | Soudage | Collage d'adhésifs | Boulons |
Méthode | Fixation mécanique par rivets | Processus de fusion des métaux | Liaison chimique avec des adhésifs | Inséré et serré avec des outils |
Utilisation principale | Permanent, pour les structures métalliques, les avions, les ponts | Permanent, pour les joints structurels et les joints à usage intensif | Semi-permanent, utilisé pour les matériaux mixtes | Joints métalliques structurels et amovibles |
Matériaux joints | Métaux, matériaux composites | Métaux (par exemple, acier, aluminium) | Métaux, plastiques, composites | Métaux ou matériaux similaires |
Caractéristiques de résistance | Bonne résistance au cisaillement, résistance modérée à la traction | Résistance élevée à la traction et au cisaillement | Résistance modérée ; convient bien pour les matériaux non porteurs. | Résistance élevée à la traction et au cisaillement |
Implication de la chaleur | Pas de chaleur nécessaire | Nécessite une chaleur élevée pour fondre | Pas de chaleur, durcissement par le temps, la pression ou les UV | Pas de chaleur nécessaire |
Processus d'installation | Insérer le rivet, utiliser le pistolet à rivets/la barre de serrage pour former la tête. | Aligner les matériaux, souder les bords à haute température | Appliquer l'adhésif, presser les surfaces l'une contre l'autre et durcir | Insérer le boulon, le serrer à l'aide d'une clé ou d'autres outils |
Processus d'éloignement | Percer ou couper le rivet pour l'enlever | Nécessite un découpage ou un meulage | Solvant ou chaleur pour affaiblir l'adhérence, décoller | Dévissé à l'aide d'outils (clé, cliquet, etc.) |
Exigences en matière d'inspection | Essais visuels, ultrasoniques ou de cisaillement | Visuel et CND (ultrasons, radiographie) | Essai visuel, parfois essai de traction | Inspection visuelle, test de couple |
Avantages | Grande durabilité, pas de déformation due à la chaleur | Joint continu très solide | Convient à une variété de matériaux, liaison souple | Facile à installer et à retirer, permet le démontage |
Inconvénients | Prend du temps, nécessite un alignement précis | Risque de distorsion thermique, irréversible | Sensible à l'environnement (par exemple, à l'humidité) | Susceptible de se desserrer sous l'effet des vibrations, nécessite un resserrage |
Comparaison des coûts du rivetage, du soudage, du collage et du boulonnage
Méthode d'assemblage | Coût approximatif par joint |
Rivetage | $0.10 – $1.00 |
Soudage | $0.50 – $5.00 |
Collage d'adhésifs | $0.25 – $2.00 |
Boulonnage | $0.20 – $1.50 |
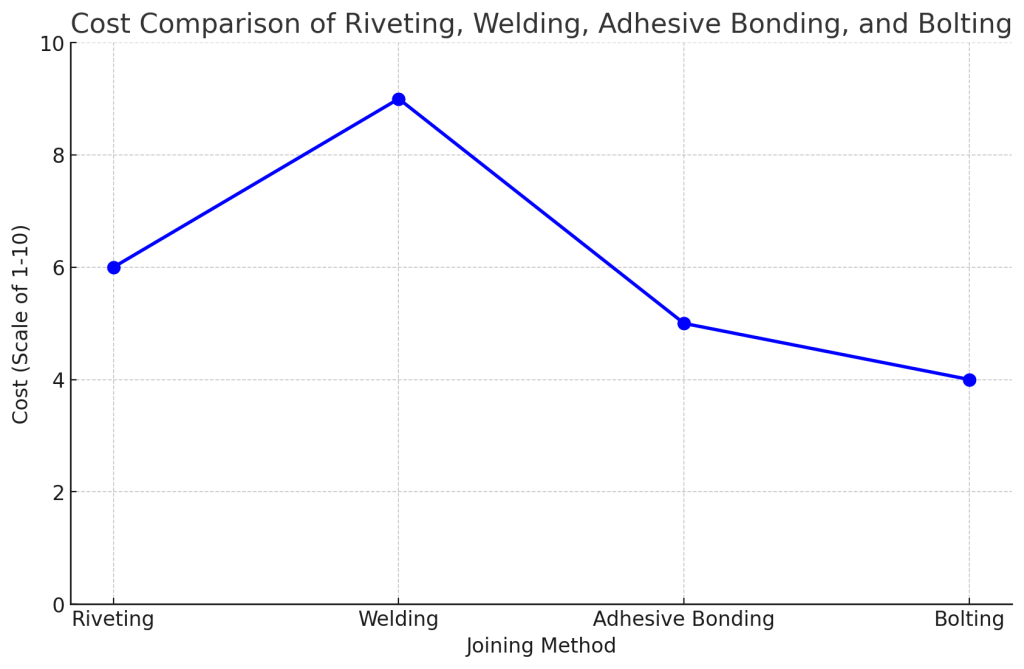
Ce graphique linéaire montre la fluctuation des prix des méthodes de rivetage, de soudage, de collage et de boulonnage sur une échelle de 1 à 10. La fixation par soudage est la méthode la plus coûteuse. Elle implique une installation spécifique, des dépenses d'outillage et des coûts de main-d'œuvre. En revanche, le boulonnage est un choix économique pour tous les types de secteurs. Les prix du rivetage et du collage indiquent des coûts modérés se situant entre les deux.
Technologies innovantes de rivetage
Progrès dans les technologies de rivetage
Systèmes de rivetage robotisés et automatisés
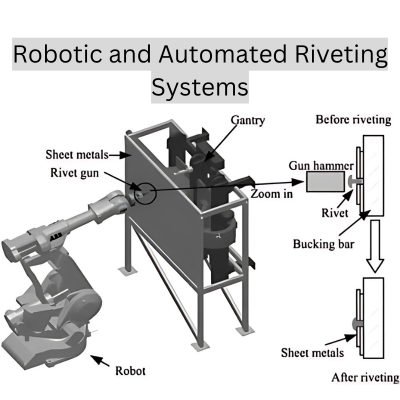
Les techniques de rivetage ont été améliorées par l'introduction de bras robotisés et de machines à commande numérique. Ces outils permettent une pose précise et exacte avec une pression constante sur chaque rivet déformé.
Calculateurs de rivets
Les calculateurs de rivets facilitent la fixation des différentes pièces. Ces outils de mesure tiennent compte de la taille exacte, du matériau de construction ou des valeurs d'espace. En outre, ils rationalisent les pressions de charge précises, les épaisseurs et la résistance des rivets. Le calculateur de rivets permet d'optimiser les options en matière de durabilité et de sécurité.
Impact sur l'efficacité et la qualité :
Les progrès réalisés dans les processus de fabrication et de rivetage apportent des facteurs d'assurance qualité. Ils réduisent la durée des opérations et produisent des pièces de grande qualité. L'utilisation d'un bras robotisé et de calculateurs permet d'éviter les problèmes de fatigue du métal et de produire rapidement avec précision.
Conclusion :
Les rivets sont les meilleures attaches qui ne sont pas plus chères que le soudage. Ils permettent d'obtenir des joints durables avec des finitions suffisantes. Ces rivets peuvent être fabriqués à partir de différents matériaux tels que l'acier, l'aluminium ou le cuivre. En outre, les rivets sont de plusieurs types, avec leur utilisation spécifique pour les applications. Le respect des étapes essentielles de la technique du rivetage et l'adaptation des systèmes modernes permettent d'obtenir le résultat souhaité.
0 commentaires