Magnesium Die Casting Manufacturer in China
OEM Contract magnesium die casting manufacturing service, fast lead time.
High Quality Magnesium Alloy Die Casting Parts from AZ91, AM60, AM50, AZ31, AE44…
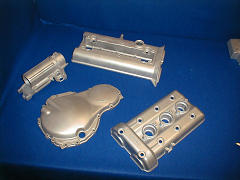
What is Magnesium die casting
The process of magnesium die casting utilizes a liquid metal that is forced into a mold to create complex geometries. It is applicable in industries that demand high-precision parts, like the automotive and aerospace sectors.
The products produced take advantage of magnesium’s light weight, which contributes to improved fuel efficiency where weight reduction is crucial. Mechanical properties such as strength and stiffness are also increased during the die casting process.
While dimensional accuracy remains excellent at all times, thus enabling them to fit perfectly within intricate assemblies without any post-treatment, this method is suitable for manufacturers who want to enhance their production efficiency as well as product performance.
The Process of Magnesium Die Casting
To finish a product in magnesium die casting, it is important that the raw materials are liquefied by heating. After this point, liquid metal is forced into a strong steel mold called a ‘die’ under high pressure.
The reason why the high-pressure injection method is used is because it ensures each part of the die is filled with magnesium, thereby trapping intricate details and complex geometries that may not be achieved through other forms of metalworking.
When the metal cools down and hardens into a solid state, the die can be opened up to reveal a replica that closely mimics most of its features in terms of accuracy.
With this technique, mass production can be done within short durations because they have fast cycle times, thus making them appropriate for applications where there are high volume production requirements coupled with speediness and precision.
Materials and Alloys Used in Magnesium Die Casting
In die casting, the choice of material is crucial in determining the suitability and performance of a product for any given application. Most commonly used magnesium alloys like magnesium die casting alloy AZ91D, AM60B, and AZ31 because they have good properties such as high strength, corrosion resistance, thermal conductivity, etc.
Each brings different features to the table, with some examples being that AZ91D balances strength against corrosiveness, thus finding wide use in various fields including automobiles or consumer electronics; this therefore shows how critical it is to select an appropriate one since its behavior in real-world situations affects everything from durability to heat transfer through a cast item.
Design Considerations in Magnesium Die Casting
When designing for magnesium die casting, one needs to be strategic so that what comes out at last can not only meet functional requirements but also remain within the bounds of manufacturing possibilities.
Some key areas of concern include: wall thickness, which determines strength as well as material usage efficiency; draft angles that allow easy removal of parts from molds without causing damage or sticking due to friction between them during the ejection process.
Fillets should be designed where sharp corners exist so as to avoid having stress-raisers there, which might lead to cracking later on after cooling down rapidly following the solidification step.
Failure to take these things into account may result in defects like warping or cracking during the pouring operation itself. Proper design enhances manufacturability while greatly affecting production efficiency and overall life expectancy, coupled with the performance capabilities exhibited by products cast using such methods.
Advantages of Magnesium Die Casting vs. other die castings
There are many benefits associated with magnesium die casting compared to copper, zinc, and aluminum die casting. Among the biggest advantages are as follows:
One observes an excellent strength-to-weight ratio. Magnesium alloys have an outstanding strength-to-weight ratio, which provides the best combination of considerable strength with little weight. This holds true even if magnesium alloys are comparatively light. The production procedure is justified by the fact that it works well for high-performance parts that need to be durable without gaining weight.
Because magnesium is the lightest metal compared to related alloy materials, magnesium die-cast components are ideal for uses where weight is an important factor. This is one of the best options for the automobile and aerospace industries. Among all the structural metals, magnesium is the lightest. Lightweighting has the ability to greatly increase fuel economy and lower emissions.
Excellent Ratio of Strength to Weight Magnesium alloys offer the perfect mix between high strength and low weight because of their high strength-to-weight ratio, despite their low weight. Production of it is justified since it is perfect for high-performance components that need durability without adding weight.
large capacity for damping Great dampening qualities allow magnesium alloys to more successfully absorb shocks and vibrations than do alloys made of zinc or aluminum. This functionality may be useful for consumer and automotive electronics, which need endurance and noise reduction.
Magnesium alloys are less dense and harder than many other metal alloys, which makes their production easier. This is because the machinability of magnesium alloys is quite good. This facilitates easier modification of die-cast parts after casting, which may lead to lower production times and manufacturing costs.
Good corrosion resistance If magnesium alloys have the proper surface treatments and protective coatings, they can show good corrosion resistance. Nevertheless, it is important to remember that magnesium is, by nature, more reactive chemically. This reactivity could make magnesium more susceptible to corrosion if improperly protected.
Higher than that of plastics, magnesium alloys have a heat conductivity that is on par with other commonly used die casting metals. Moreover, magnesium alloys are in every way better than plastics. They are thus beneficial for uses like heat sinks and other components where heat dissipation is crucial.
Using recycled magnesium can greatly lower the amount of energy used and the environmental effect compared to producing primary magnesium because it is so easily recyclable. This aspect is becoming more and more important to take into account as companies shift to less environmentally damaging production techniques.
But there are some considerations to make and challenges associated with magnesium die casting as well. These consist of the higher costs of raw materials and the need for specialized handling and processing methods when magnesium melts since it melts with a high degree of reactivity and flammability. Apart from the previously mentioned factors, the advantages must be considered while choosing the metal that is best suited for a certain application.
Surface Finishing Techniques
Surface finishing during the die casting of magnesium is an important stage because it enhances the appearance and performance of the parts. Painting, among other methods, provides a wide range of colors and increases resistance to weathering.
Plating entails coating components with metals such as nickel or chromium, which not only improves aesthetics but also greatly increases the wear and corrosion resistance required for severe service conditions. Another common method is anodizing, in which the surface hardness of magnesium parts is increased through an electrochemical process, resulting in a long-lasting corrosion-resistant coat.
This kind of finish is particularly beneficial in automotive applications where sustained durability and protection against harsh environmental conditions are needed.
Therefore, these finishes serve to extend both the life span and range of application for magnesium die castings.
Quality Control in Magnesium Die Casting
It is essential to work with materials like magnesium die casting to high standards, especially when various industries heavily rely on them, such as the aerospace or automotive sectors; otherwise, they might fail at critical points, leading to disastrous consequences.
X-ray inspection is used as one of the quality control measures that detects internal faults within castings, hence ensuring their soundness. On the other hand, dye penetrant testing provides a good way through which superficial cracks can be detected.
Even if invisible to the naked eye, dimensional analysis should always be done so that each part meets the required tolerances necessary for complex assemblies.
These stringent checks are aimed at ensuring every component performs reliably within its intended environment, thus keeping satisfied customers and safe businesses running.
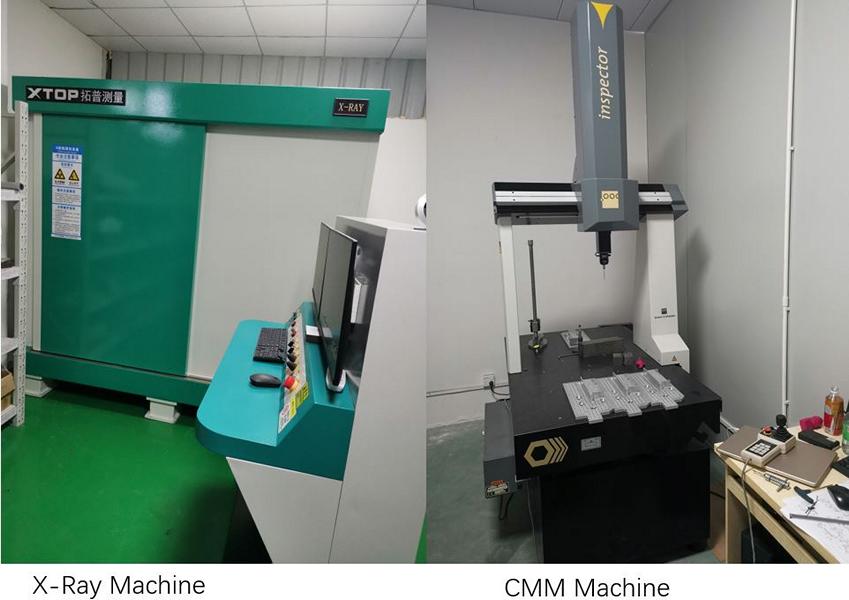
Applications of Magnesium Die Casting
There are numerous areas where magnesium die casting finds application across various industries due to its exceptional strength-to-weight ratio coupled with ease in forming intricate shapes during production processes.
The automotive industry benefits from this technology by utilizing gearbox cases made out of magnesium alloy, which helps in weight reduction, thus enhancing fuel efficiency and performance levels.
Consumer electronics also employ these castings; for instance, thin but strong laptop frames can be produced through such means, as can compact camera housings.
Additionally, lightweight surgical instruments require manufacturing within the medical sector using die casting methods so as to achieve the desired features for accurate operations in high-risk environments. This versatility and efficiency displayed by magnesium die casting in meeting different manufacturing needs is evident from the wide range of applications.
Innovations in Magnesium Die Casting Technology
The world of magnesium die casting keeps changing every day. This is because recent developments have broadened its application areas and made it more efficient. The introduction of new magnesium alloys is a great leap forward since they have better properties, including high strength and improved resistance to corrosion in aggressive environments.
In addition, the current enhanced methods of casting can help reduce porosity, which was one major challenge with previous techniques, thereby improving mechanical characteristics and prolonging component life.
These advancements not only raise quality requirements for castings but also lower them cost-wise, making them greener through waste reduction during production and energy savings, among other benefits.
The Future of Magnesium Die Casting
The future magnesium die casting industry looks promising considering that lightweight materials are becoming more in demand across various sectors.
Still looking into ways of improving efficiency in their products through fuel consumption reduction and emissions mitigation, automotive aerospace, among others, needs to adopt technologies like magnesium die casting too.
Hence, recycling method advancement coupled with sustainable manufacturing practices will also go a long way in enhancing the environmental friendliness associated with magnesium die-casting processes over time, so a wider application should be expected alongside this creative use so as to foster efficient, affordable, yet sustainable manufacturing solutions.
Related Die Casting Parts Services
Aluminum Die Casting
Customized Aluminum die casting parts from different metals, special aluminum alloys are available.
Zinc die casting parts
Zinc die casting parts from zamak 3, Zamak 5, surface finish all in one stop services
Precision CNC Machining
Prototype CNC Machining, aluminum casting machining, plastic CNC machining services…
Contact Us
GC Precision Mould Co., Ltd
Office Address:401 Room, 10 Building,HuYing DoshiHuaHu, ChangPing Town,GongGuan City,GuangDong Province,China. 523000
Factory Address: Room 101, No.40, Donghu road, Jinglian, Qiaotou zhen, Dongguan city, Guangdong Province, China. 523520.