We use aluminum every day. It is used in cars, homes, factories, and other places. There are many reasons behind aluminum’s popularity. One of the most crucial reasons is the aluminum’s strength against weight ratio. Another critical factor here is the “Melting Point of Aluminum.”
Aluminum typically has a low melting point compared to SS or CS. Because of this, it is easy to process and handle and is widely used in many industries. Houses, cars, aircraft, computers, and many others are typical examples.
Aluminum is also very resistant to corrosion. But if you’re working with aluminum, there’s a critical point to consider: The Melt Point of Aluminum. Why is this so important?
In general, aluminum’s melting point is 660.32 degrees Celsius. Most processing and handling jobs are conducted based on this value. Some conventional processes include welding, casting, extrusion, and heat treatment. This information is essential to engineers and manufacturers to set the correct temperatures. Here, the melting point of aluminum can be used as a threshold.
The melting point is involved in all stages of aluminum processing, from heating to other activities. It impacts issues with storage, transport, and even the material to be used. With aluminum alloys, this threshold varies slightly. Therefore, when looking for aluminum as a material to use for a particular job, you ought to know these melting points.
This article is about “What’s the Melting Point of Aluminum.” It will mainly discuss a wide range of melting points of aluminum. Also, you will know what factors affect this value. We believe this article can help you get more information about various types of aluminum and their melting points.
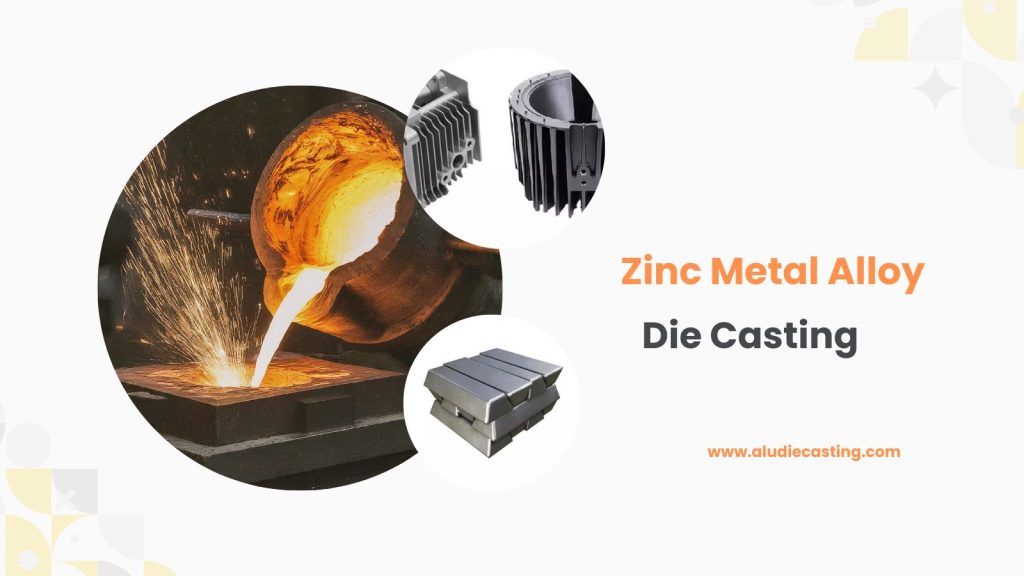
What is the Melting Point of Aluminum?
The melting point of aluminum is where it begins to liquefy. At this point, the material undergoes a significant transformation. You can see the transformation if you observe the process in a container. At the melting point, aluminum starts to move into a liquid state from a solid or rigid form.
For aluminum, this change occurs at exactly 660.3°C or 1220.54 degrees Fahrenheit. The melting process usually has three main phases. First, the aluminum remains solid, which remains below 660.32 degrees Celsius. Second, the aluminum goes into the transition point, which is at 660.32 degrees Celsius. Finally, the aluminum turns into liquid when the temperature is above 660.32 degrees Celsius.
This might be just a number, but it is crucial in many applications. It gives engineers a dependable guide for handling, processing, and using aluminum. However, this melting point may vary depending on the type of aluminum.
Generally, we can classify aluminum into three primary categories: commercial, binary, and casting alloys.
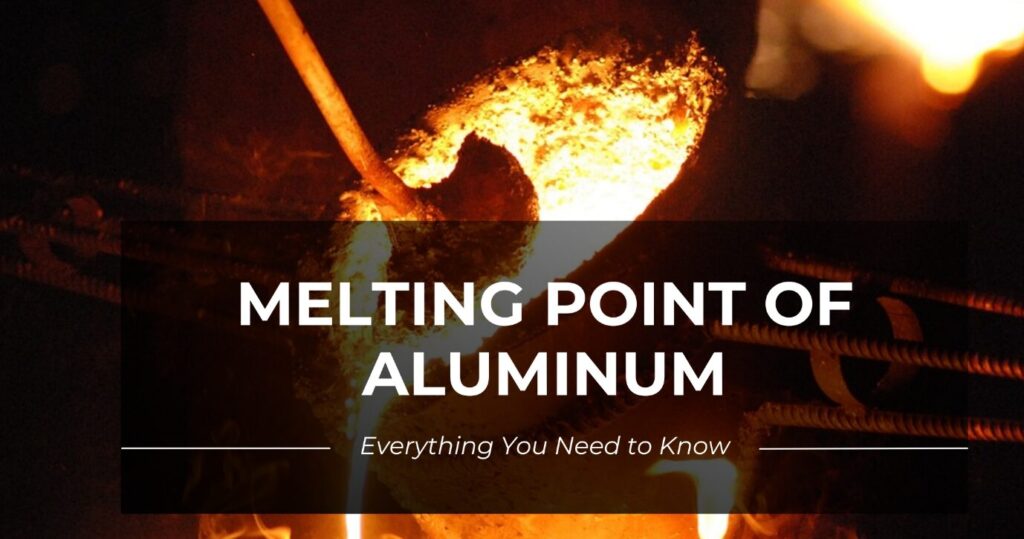
Commercial Alloy Series
Commercial alloys are the primary aluminum grades in the family. They are the “go-to” options for everyday applications. People widely use them in construction, transportation, or packaging. These alloys combine aluminum with various elements, like magnesium or silicon. The primary reason behind this mixing is to ensure strength and corrosion resistance. They’re reliable, versatile, and used everywhere.
Alloy Name | Melt Point of Aluminum |
Alloy 2024 | 500 to 635°C |
3003 Al alloy | 643 to 654°C |
Aluminum Alloy 6061 | 582 to 652°C |
7075 Al alloy | 477 to 635°C |
A356 Aluminum Alloy | 667 to 796°C |
Binary Alloy Systems
Binary alloy systems are simple yet effective. They combine aluminum with just one element, hence the name “binary.” These alloys focus on strengthening specific properties by keeping the mix simple. If you need something lightweight but very robust, such as binary alloys, do the best job here. These aluminum alloys are widely used in special machinery and electronics.
Alloy Name | Melt Point of Aluminum |
Al-Cu | 548°C |
Al-Si | 577°C |
Al-Mg | 600°C |
Al-Zn | 382°C |
Casting Alloys
Casting alloys are used to shape molten aluminum into molds. They have a very high melting range. These alloys are typically easy to shape and work well under high temperatures. People use them for intricate designs or precision parts. These alloys are built to withstand heat and pressure. People widely use them in high-stress environments.
Alloy Name | Melt Point of Aluminum |
A360 Aluminum Alloy | 1030 to 1100°C |
A380 Aluminum Alloy | 1000 to 1100°C |
A413 Aluminum Alloy | 1070 to 1080°C |
Why is Melting Point Important?
The melting point of aluminum affects almost every aspect of its use in manufacturing. It tells you exactly when the aluminum alloy will soften and mold. Understanding the melting point keeps your process efficient and safe when handling aluminum. You must understand the melting point of aluminum for three main reasons.
Material Handling
In material handling, knowing the melting point of aluminum can prevent costly errors. When aluminum is near its melting temperature, it needs extra care. Overheating is a common problem when handling aluminum. Sometimes, you might find defects like warping or degradation, which are common symptoms of overheating. In this case, if you are aware of the melting point of aluminum, you can reduce this at the highest level.
Surface Protection
Surface protection also hinges on temperature awareness. When aluminum nears its melting point, it becomes more vulnerable to surface damage. Coatings and anodized layers protect aluminum’s surface but can deteriorate if they exceed specific temperatures. So, you must know aluminum’s specific melting point.
Equipment and Tools
Every tool used on aluminum is affected by its melting point. High temperatures typically require special tools that don’t degrade while working close to aluminum’s melting threshold. Using the right equipment for hot aluminum makes for a safer workspace and minimizes tool wear and tear.
Melting Points of Common Aluminum Alloys
Aluminum alloys are the most widely used aluminum in today’s world. From lightweight strength to corrosion resistance, they’ve got it all. However, one key factor that stands out here is the melting point. You have already known why knowing the melting point of aluminum is crucial. Note that each alloy has its unique melting range.
Alloy | 2024 | 3003 | 5052 | 6061 | 7075 |
Density | 2.78 g/cc | 2.73 g/cc | 2.68 g/cc | 2.7 g/cc | 2.81 g/cc |
Melting Point | 502 – 638°C | 643 – 654°C | 607 – 649°C | 582 – 652°C | 477 – 635°C |
Melting Point of Aluminum 2024
Aluminum 2024 is known for its unique strength and fatigue resistance. Due to its strength-to-weight ratio, this alloy is frequently used in aerospace applications. The melting range for aluminum 2024 is between 500 degrees and 638 degrees Celsius.
Aluminum 2024 isn’t the best for corrosion resistance, so it’s often paired with a protective layer or treated with anodizing. If you’re considering heat-treating this alloy, note that its melting range needs precision. A slight misstep might compromise its structural integrity.
Component | Weight % |
Al (Aluminum) | 90.7 – 94.7 |
Cr (Chromium) | 0.1 |
Cu (Copper) | 4.9 |
Fe (Iron) | 0.5 |
Mg (Magnesium) | 1.2 – 1.8 |
Mn (Manganese) | 0.3 – 0.9 |
Other (each) | 0.05 |
Other (total) | 0.15 |
Si (Silicon) | 0.5 |
Ti (Titanium) | 0.15 |
Zn (Zinc) | 0.25 |
Melting Point of Aluminum 3003
Consider this aluminum alloy if you need more corrosion resistance and decent strength. Its melting point lies between 643 and 654 degrees Celsius, making it a prevalent choice for relatively high-temperature applications.
Unlike 2024, aluminum 3003 is not very strong. However, it is malleable and easy to work with. Its higher melting point makes it ideal for handling welding and bending work.
Component | Weight % |
Mn (Manganese) | 1.1 – 1.5 |
Fe (Iron) | 0.7 |
Cu (Copper) | 0.2 |
Mg (Magnesium) | 0.05 |
Si (Silicon) | 0.6 |
Zn (Zinc) | 0.1 |
Al (Aluminum) | Balance |
Other (each) | 0.15 |
Melting Point of Aluminum 5052
If you are looking for an aluminum alloy with both strength and flexibility, Al 5052 is the best choice. This material is prevalent for superior corrosion resistance. People mostly prefer this aluminum alloy for marine environments and fuel tanks. Aluminum’s melting point generally ranges from 607 to 649 degrees Celsius.
Aluminum 5052 doesn’t respond well to heat treatment to increase strength. However, it is highly workable. You can easily shape, bend, or weld it, making it highly versatile for various applications.
Component | Weight % |
Al (Aluminum) | 95.7 – 97.7 |
Cr (Chromium) | 0.15 – 0.35 |
Cu (Copper) | 0.1 |
Fe (Iron) | 0.4 |
Mg (Magnesium) | 2.2 – 2.8 |
Mn (Manganese) | 0.1 |
Other (each) | 0.05 |
Other (total) | 0.15 |
Si (Silicon) | 0.25 |
Zn (Zinc) | 0.1 |
Melting Point of Aluminum 6061
Aluminum 6061 is ideal for structural applications. It is strong and corrosion-resistant, and you can weld it. The melting point of aluminum alloy 6061 typically lies between 582 and 652 degrees Celsius. This material also offers some flexibility. It is not only durable but also a very lightweight aluminum alloy.
Aluminum 6061 is widely used for bike frames, bridges, and machinery parts. It can balance strength, formability, and weldability.
Al (Aluminum) | 95.8 – 98.6 |
Cr (Chromium) | 0.04 – 0.35 |
Cu (Copper) | 0.15 – 0.4 |
Fe (Iron) | 0.7 |
Mg (Magnesium) | 0.8 – 1.2 |
Mn (Manganese) | 0.15 |
Other (each) | 0.05 |
Other (total) | 0.15 |
Si (Silicon) | 0.4 – 0.8 |
Ti (Titanium) | 0.15 |
Zn (Zinc) | 0.25 |
Melting Point of Aluminum 7075
If you are looking for more strength, aluminum 7075 is an option you can consider. This aluminum alloy is famous for its high strength-to-weight ratio. It is often used in aircraft and automotive applications. Its melting point lies between 477 and 635 degrees Celsius.
The lower melting range does come with some cons, though. While aluminum 7075 is highly strong, it’s not as corrosion-resistant as other alloys, like 5052. To maximize its performance, you can coat or anodize it to protect the surface from oxidation. Its lower melting point also means it needs careful handling during heat treatment.
Component | Weight % |
Al (Aluminum) | 87.1 – 91.4 |
Cr (Chromium) | 0.18 – 0.28 |
Cu (Copper) | 1.2 – 2 |
Fe (Iron) | 0.5 |
Mg (Magnesium) | 2.1 – 2.9 |
Mn (Manganese) | 0.3 |
Other (each) | 0.05 |
Other (total) | 0.15 |
Si (Silicon) | 0.4 |
Ti (Titanium) | 0.2 |
Zn (Zinc) | 5.1 |
Factors Affecting The Melt Point of Aluminum
The melting point of aluminum is not fixed. Several factors influence it, including its composition, physical properties, and manufacturing processes. These factors heavily determine when aluminum will transition from solid to liquid.
Alloy Composition or Purity Levels
Pure aluminum’s melting point is typically around 660.32 degrees Celsius. However, in industry, pure aluminum isn’t always practical. It’s often alloyed with other elements to improve strength, flexibility, and durability.
Elements like copper, magnesium, silicon, and zinc are often added to aluminum. These elements help aluminum to withstand different applications but change its melting behavior. For instance, the melting point of aluminum alloy 6061 is 582 to 652 degrees, which is lower than that of pure aluminum. In 6061 aluminum alloy, you will find chromium, copper, iron, magnesium, and more.
Unlike pure metals, alloys usually don’t have a single, sharp melting point. Instead, they have a melting range. The material melts at a lower temperature and enters the mushy phase before fully liquefying. This range varies by composition and can affect the process in which the alloy is used.
Heat Treatment Methods
Heat treatment can reshape aluminum at a molecular level. Sometimes, after casting or extrusion, your product may not behave the way it did before. In this case, heat treatment acts like a reset button on aluminum’s properties. Several types of heat treatment methods affect aluminum’s melting point.
Quenching
Quenching involves heating aluminum to a certain temperature and then cooling it. Although quenching doesn’t necessarily lower aluminum’s melting point, it does change its microstructure. In some cases, quenched aluminum may melt less uniformly.
Annealing
Annealing is the opposite of quenching. It heats the aluminum and then cools it slowly. As a result, the aluminum parts become softer and more ductile. Annealing reduces internal stress. It can create more consistent melting behavior. Since annealed aluminum offers high precision, it is often used in metal casting.
Precipitation Hardening
This process improves the strength of aluminum alloys by heating and cooling them. This heat treatment method is done in a very controlled environment.
Precipitation hardening generally doesn’t lower the melting point. However, it does increase the temperature stability.
Physical Characteristics
Physical properties also heavily affect aluminum’s melting point. Grain size, stress levels, and sample size are some of the critical factors.
Size of the Grain
Grain size in metals refers to the size of individual crystals that form in the metal. Fine grains and large grains have different melting behaviors.
Smaller can raise the melting point slightly, as they add strength. Larger grains, however, may lower the melting point. Note that larger-grain aluminum is easy to work with in lower-temperature applications.
Stress and Strain
You can stress aluminum, bend, stretch, or compress it based on your needs. When you do these, the aluminum part experiences a change in its internal structure.
The internal energy from strain in stressed aluminum can reduce the energy needed to initiate melting so that it may melt at lower temperatures.
Sampling Size
Sample size also matters, especially in lab testing melting points. Large samples tend to have more consistent melting behavior. On the other hand, smaller samples can exhibit variable melting ranges due to surface-area effects.
Chemical Properties
As you know, the difference between pure aluminum and its alloys. Each of these aluminum can provide unique chemical properties. As a result, you can get different melting of each aluminum.
However, oxidation also affects aluminum’s melting temperature. Although aluminum is naturally corrosion-resistant, it may still corrode under harsh conditions. The corrosion layer can influence aluminum’s melting behavior.
Melting Point in Industrial Application and Processing
Aluminum melting point is necessary in almost every aluminum factory. Where there are processing or aluminum parts, the melting point of aluminum is a crucial factor. In this section, you will be familiar with some industrial applications.
Heat Treatment
Heat treatment is one of the most common applications where the melting point is critical. This method typically changes aluminum strength, flexibility, or durability. You can’t use a higher temperature above the melting point or do it at very low temperatures when heat-treating aluminum. You must maintain an optimal temperature for heat treatment.
Knowing aluminum’s melting point typically allows for setting precise parameters. This is especially necessary for annealing and precipitation hardening.
Metal Casting
Metal casting also heavily depends on aluminum’s melting point. Die-casting, permanent mold casting, and sand casting are common casting methods.
Aluminum casting involves heating the metal to a molten state and pouring it into molds to create the exact shape of the final part. If too much heat is applied, mold integrity will suffer. On the other hand, being too cool might result in incomplete fills or visible defects.
Whatever the method is, the goal is to ensure a smooth pour.
Die Casting
Die casting is one of the most popular methods for shaping aluminum. This process forces molten aluminum into a mold cavity at high pressure.
Temperature control is vital in die casting. Parts might weaken if the temperature drifts too close to aluminum’s melting point. In contrast, you risk damaging the die if the temperature is too high. You want uniformity in every casting. In this case, temperature stability can help you get there.
Permanent Mold Casting
Permanent mold casting is different from die casting. As the name suggests, this method uses a permanent mold that can be used multiple times. The melting point of aluminum plays a significant role in selecting the mold material. Because the mold comes into contact with molten aluminum, it must withstand the heat.
To handle aluminum, you don’t need high heat resistance mold material. You can carefully choose cheaper mold material that can withstand heat with your working material. On the other hand, if the material is low-quality, it will wear out faster. Either way, you might count higher costs and experience more downtime.
Sand Casting
Sand casting is the most straightforward and most conventional method. When aluminum is poured into a sand mold, its melting point determines how fast or slow it cools. If aluminum cools too quickly, it may not fill the mold. Cooling too slowly can impact the part’s structural integrity and lead to many problems.
Extrusion Process
Extrusion forces a hot aluminum billet through a die to create specific shapes. The machine continuously heats the aluminum. In this case, it is essential to note that the extrusion process can not cross the melting point of aluminum. This is necessary because aluminum’s behavior becomes unpredictable when it reaches the melting point. Because of this, your aluminum parts may get inconsistent shapes or even fail.
Aluminum Welding
Welding aluminum is tricky without worrying about melting points. Aluminum has a high thermal conductivity, which means it heats up fast and cools down just as quickly. For welding to work, aluminum must reach the right temperature to fuse without melting completely.
Frequently Asked Questions
Which Metal Melts Fast?
The speed of melting typically depends on its thermal conductivity. Copper and aluminum have very high thermal conductivity in general. While aluminum has a melting point of 660.32 degrees, copper has a value of 1085 degrees Celsius.
What Is the Melting Point of Pure Aluminum?
The melting point of pure aluminum is 660.32 degrees Celsius, a critical number for anyone working with aluminum manufacturing. However, pure aluminum is less popular than aluminum alloys.
Is It Possible to Determine the Identity of The Impurities Based on Melting Point?
Yes, you can often get clues about impurities by observing melting behavior. Indeed, it’s the quickest and easiest solution to find the impurities. Pure metal, like aluminum, has a sharp melting point. However, if there are impurities, the melting point can drop, or the metal may not reach a border temperature range.
Which Aluminum Alloy Has the Lowest Melting Point?
The aluminum alloy 7075 has the lowest melting point, between 477 and 635 degrees Celsius. This lower melting range makes this alloy highly suitable for brazing and bonding applications.
What Lowers the Melting Point of Aluminum?
One crucial factor that lowers aluminum’s melting point is adding certain elements. As you know, aluminum 7075 offers the lowest melting point among the family. If you observe its chemical structure, you will find that it has other elements.
How Does the Temperature Affect Aluminum?
Temperature has a significant impact on aluminum. At higher temperatures, aluminum becomes softer. Becoming softer has both benefits and limitations. It mainly depends on specific applications.
Get in Touch with Us!
If you have any questions, contact our customer support team. GC Mold is specializes in various aluminum parts and equipment. The company has the latest machinery for aluminum casting and extrusion. So, you are always welcome to our customer support for any aluminum service.
0 Comments