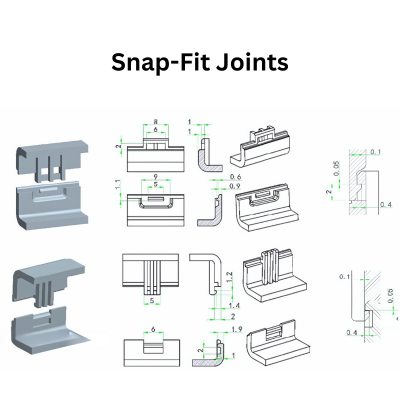
Snap-fit joints have gained popularity in manufacturing as cheap and fastest connectors. These joints are common mechanical systems that join two or more products’s parts without requiring any tools or techniques. For instance, the back cover of the TV remote can be snapped into place and removed to change the battery.
Keep reading more interesting facts about snap-fit joints with details on their designs, uses, and insights.
What are snap-fit joints?
Have you ever wondered how the cap of a bottle perfectly fits on it every time? There is a proper technique behind it that is developed to create easy-to-use and cost-effective joints for products. Snap-fit joints are a type of fastening that enables a repeatable assembly process. These parts are designed with interlocking connections and can be joined with other parts without using any tool. For example, ball and socket joints. Bottle caps, remote frames, battery covers, etc.
Common Types of Snap-Fit Joints
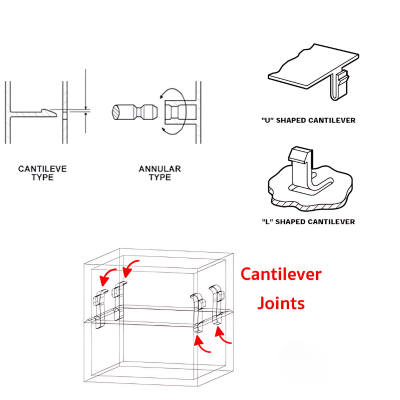
- Cantilever Snap-Fit
- Annular Snap-Fit
- U-Shaped Snap-Fit
Cantilever Snap-Fit
Cantilever snap-fit parts are constructed with thermoplastic materials. These are the easiest fasteners, containing the cantilever beam with a hook on the end. That allows for easy insertion and flexibility while snapping into place.
Applications | Cantilever Snap-Fit Parts |
Consumer Electronics | Smartphones, laptops, tablets |
Toys and games | Molds, building blocks, Puzzles |
Packaging | Item enclosures and container lids |
Home appliances | Power tools, vacuum cleaner |
Strap buckle | Buckles, tie-down straps |
Automotive | Trim panels, headlights |
Annular Snap-Fit
Annular snap-fit parts are built by adding a ring or circular snap mechanism. It contains the ridge around the circumstances of one part. This ridge is locked into a groove in the relevant part. It can be used to join cylindrical-shaped parts.
Applications | Annular Snap-Fit Parts |
Sealing | Cosmetic containers, jars, and bottle lids |
Assembling Caps | Pens and bottles with snap-on caps |
Household Items | Lamp housings |
Automotive | Ball-and-socket |
U-Shaped Snap-Fit
U-shaped snap-fit designs can provide a firm attachment whose one arm is half folded onto itself. These types of fasteners can be used to secure larger or heavier assemblies.
Applications | U-Shaped Snap-Fit Parts |
Tool Cases | Lid closures in power tool cases, tackle boxes, and first-aid kits |
Electronic housing | Plastic housings in laptops, printers, and mobile phones |
Automotive | Door trim panels, dashboard covers, and center console components |
Design Considerations for Snap-Fit Joints
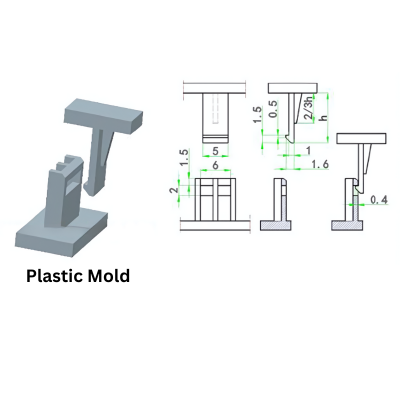
- Design Flexibility
- Material Selection
- Tolerance Analysis
Design flexibility
Flexibility is an important element that must be weighed during the design process of snap-fit joints. This factor enables the engineers to produce parts with modular features. Because products with modular elements allow for interchangeable parts, easy assembly and disassembling of products, personalization, and quality standards.
Material Selection
Material selection plays a vital role in manufacturing long-lasting and durable snap-fit joints. Check out the comparison of common materials.
Material | Durability | Flexibility | Environmental Resistance | Typical Applications |
ABS (Acrylonitrile Butadiene Styrene) | Moderate: resistant to impact but prone to UV degradation | High – easy to design complex snap-fits | Moderate – limited outdoor use due to UV sensitivity | Electronic housings, appliance parts |
Polycarbonate (PC) | High – excellent impact resistance | Moderate: more rigid, best for precise fits | High – resists UV, temperature, and chemical exposure | Automotive parts, high-end electronics |
Nylon (Polyamide) | Very high—strong and tough under stress | Moderate: flexible yet durable | High – excellent chemical and wear resistance | Automotive clips, industrial equipment components |
Polypropylene (PP) | Good—impact-resistant, especially in low-stress applications | High, very flexible, ideal for living hinges | Moderate: resists moisture but is less UV-resistant | Food containers, medical device casings |
POM (Polyoxymethylene or Acetal) | High-durable and wear-resistant | Moderate – high stiffness, good snap action | High – strong resistance to moisture and chemicals | Gear housings, automotive fasteners |
Tolerance Analysis
The tolerance analysis indicates the predetermined steps. That facilitates the production of high-performance products with reliability. Proper tolerance analysis demonstrates the product’s ability to withstand critical situations in the future.
Tolerance Analysis Workflow
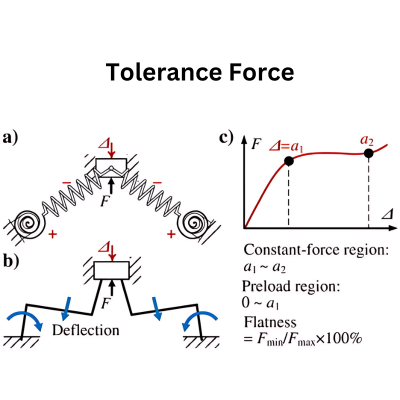
Tips for Calculating Tolerances
- Material-Specific Deformation: Always check the wearability and strength of materials like polypropylene before choosing them for snap-fit joint production. Ensure the part can bear the heavy loads while stretched or compressed.
- Environmental Considerations: Consider the changing effect of whether on materials like nylon to reduce its humidity.
- Allowable Stress: Determined the stress limitations of the material to avoid the risk of metal fatigue over time.
Common Tolerance Issues and Solutions
Issues | Solutions |
Over-tight tolerance may trouble the snapping and separation of parts. | Create the parts by allowing small degrees of lateral or rotational flexibility. This will accommodate the assembly and misalignment issues. |
It may enhance wear and deformation. | Select a material that provides good strength and fatigue resistance components. You can also add reinforcing ribs to the design. |
The Role of Snap-Fit Joints in DIY Projects
Snap Fit joints are largely leveraged in the DIY task. They enable the construction of products with modular, repeatable, and customizable designs. In addition, it makes prototyping operations easy and quick to design the specific parts.
Snap Fit joints offer tool-free assembly. You can further access 3D printing to test and refine the joints for your DIY projects.
Tips for DIY Enthusiasts
- Use 3D printing for Prototyping
- Consider scaling and tolerances
Use 3D printing for Prototyping
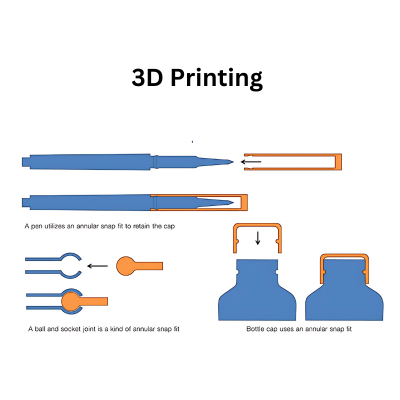
- Material selection
- Test Fit and Functions
- Iterate with adjustments
Material selection
Gather the 3D printing materials to initiate the prototyping process of snap-fit joints. You can choose from PLA and PETG; both are suitable. In particular, PLA can be used to make low-stress items, while PETG is good for slightly more stressed parts with flexibility and durability.
Test Fit and Functions
It is an advisable option to print the small sections of designs as testing products. Check the necessary functions of parts to see if they work accordingly or not. Like ease of assembly, flexiblity and durability.
Iterate with Adjustments
Customize the tolerance, thickness, and angles of your project using 3D modeling. It will increase the functionality of your parts and allow reliable snap-fit designs.
Consider scaling and tolerances.
- Adjust for Printer Accuracy
- Use Layer Orientation Wisely
Adjust for Printer Accuracy
Utilize the inherent dimensional properties of 3D printing. Adjust the tolerances of your design while gauging the specific measurements. This step will cater your parts to be a better fit.
Use Layer Orientation Wisely
Use the right axis to make sure your snap-fit components are capable of repeated procedures. Optimized layer bonding can increase the durability of parts. That can be achieved through printing in direction.
Global Perspectives on Snap-Fit Design
Snap-fit joints are increasingly popular in various fields worldwide. Every industry tries its best to produce its parts, incorporating optimized features, durability, and modularity.
Moreover, the engineering team and manufacturers are reining in the techniques for best outputs. These snap-fit joints are used in automobiles, electronics, households, and medical equipment.
Cultural Approaches to Snap-Fit Design
The majority of countries across the globe are leveraging the snap-fit joints for their products, creating novel inventions in designs. Automotive and electronic are the example fields that are looking for high-precision joints.
Japan
Japan is achieving its ambitious goal of precise automotive parts with snap-fit joints. They emphasize their miniaturization. The polpular companies of Japan, like Toyota and Honda, use snap fits to streamline the assembly of dashboards and internal frames.
Germany
German automotive companies like BMW and Volkswagen secure their components of engine bays and air filters with snap-fit joints. They focus on creating parts with strong and relaiable features. Their efforts make the part high stress responsive and eliminate the vibration issues.
Engineering Design and Prototype Testing
Adopting computer-aided design (CAD) software and conducting prototype testing operations are beneficial for engineering reliable snap-fit joints. Proper planning, modeling, and testing steps can ensure the best input results.
The role of CAD molding
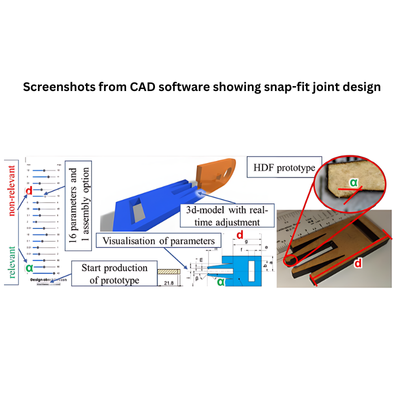
CAD modeling helps the manufacturers modify the size, tolernace and geometric measurements of parts before the prototyping stage. The popular choice of CAD software creates the complex parts with appropriate tolerance and simlating stress. For instance, SolidWorks, Fusion 360, and CATIA.
Key CAD Modeling Techniques for Snap-Fit Joints
- Parametric Modeling
- Filleting and Rounding
- Draft Angle and Clearance
Parametric Modeling
Parametric modeling allows the manufacturer to customize the measurement, balancing the thickness and weight of metal.
Filleting and Rounding
The sharp edges of components cause the fracture faults. To avoid this, filleting and rounding processes must be adapted.
Draft Angle and Clearance
Modify the part by adding draft angles of 1 to 2 degrees. It will help ensure the proper clarity and prevent overtight and loose changes.
Prototype Testing and Validation
Prototype testing and validation considerations aid the snap-fit joint in performing an expected task under different stress. These tests can be done by:
- Simulation-Based Testing
- Physical Prototype Testing
Simulation-Based Testing
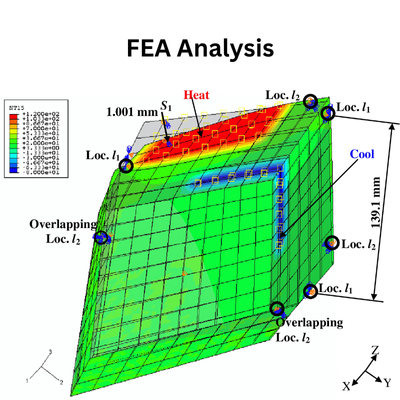
When modeling stress, strain, and deformation on snap-fit joints, manufacturers can implement finite element analysis (FEA). These are the effective technologies present in CAD software. For instance, Solidworks and Fusion 360. The software helps you predict failure points. You get innovative insights.
Additionally, dynamic load testing tools simulate the joints to tackle the different forces. Such as bending and torsional pressures. You can determine the product ability by visualizing the joint reaction of forces and heavy loads.
Physical Prototype Testing
Create the testing pieces of the snap-fit joint through the protopye. Check their fitting points, diemsnions and performance.
The operator can also minimize the stress and fatigue of parts by repeatedly performing assmbling and desmlbing processes. These tests will demonstrate the weaknesses and unexpected stress points.
Stress Analysis and Mechanical Interlocking
- Analyzing Stress in Snap-Fit Joint Design
- Mechanical Interlocking Techniques
- Hybrid Snap-Fit Designs
Analyzing Stress in Snap-Fit Joint Design
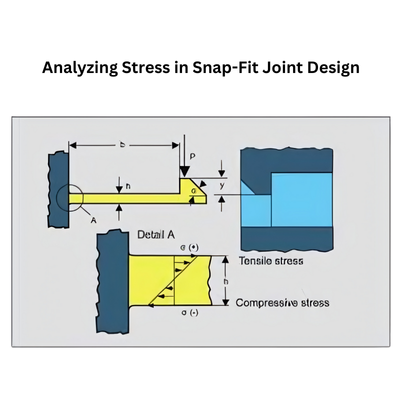
Identifying Stress Concentrations: Being a powerful tool, finite element (FEA) spots the sharp and thinner areas of stress accumulations to prevent failure.
- Optimizing Material Usage: the metalworkers can change the dimensions, material, thickness, and weight according to FEA predictions. It will reduce the stress and increase the longevity of the item.
- Predicting Deformation: The FEA tool will guide how your part will react under load. They will highlight the elements that can cause breakage and warping.
Mechanical Interlocking Techniques for Strength and Stability
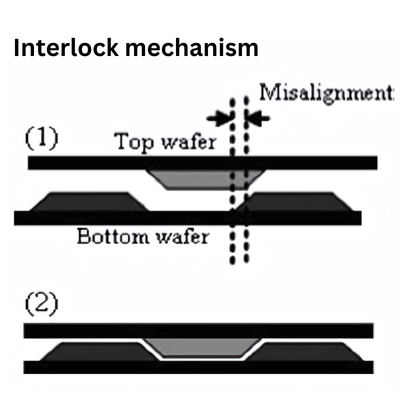
Mechanical interlocking techniques provide resistance against separation and improve the stability of snap joints.
Types of Interlocking Variations
- Undercuts and Hooks
- Tapered and Serrated Tabs
- Latching Mechanisms
Undercuts and Hooks
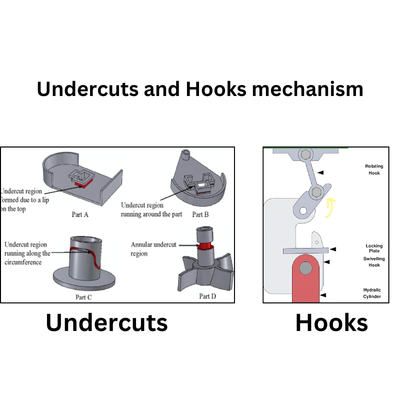
These types of interlocing are used for products requiring a strong hold. They prevent the high stress, providing resistance separation.
Tapered and Serrated Tabs
Tapered and serrated tabs create a strong grip on the joints to securely protect them from vibrations and force impacts.
Latching Mechanisms
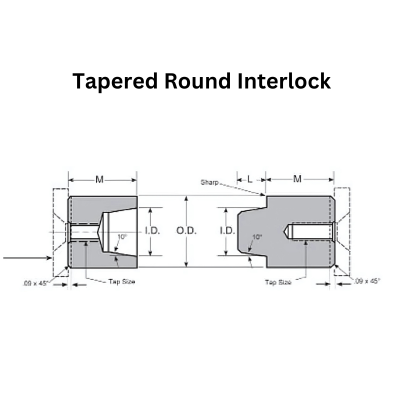
Latching mechanisms incorporate clips or buttons. These techniques are good for controlling the assembly and disabling of products.
Hybrid Snap-Fit Designs for Enhanced Stability
Hybrid Snapfit designs increase the strength and stability of parts, making them a versatile option. These additional phases include:
- Snap-Fit with Screw Fasteners
- Multi-Directional Interlocking
Snap-Fit with Screw Fasteners
Automotive and industrial parts required jointing with additional fasteners. Therefore, adding screws and other tools improves their stability in applications.
Multi-Directional Interlocking
Adding multiple directions to the joint to accommodate the parts, fighting against forces from differing angles.
Conclusion:
Snap-fit joints are functional components across diverse industries, whether it is the packaging industry or top-rated automotive companies like Toyota. It is a cost-effective and efficient choice to fasten the different parts of the product, enabling tool-free assembly. For example, mobile stands, pen and bottle caps, etc. Understanding the fundamental aspect of its intricate design material and interlocking technology will cater to producing well-performing snap-fit joints.
0 Comments