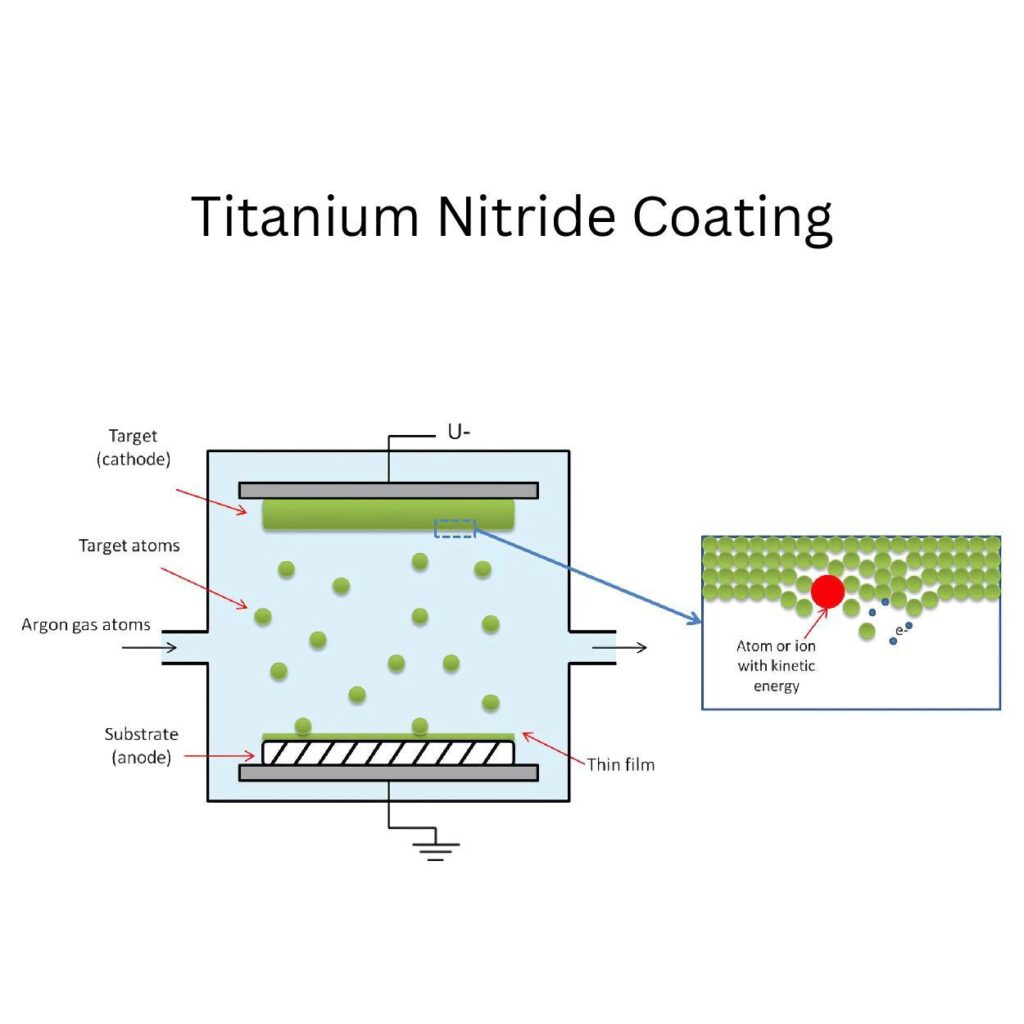
Titanium nitride coating is made with two elements; Titanium and Nitrogen. It is applied on metal surfaces. TiN coating hardness is around 2000-3000 HV. Tin coating has gold like color. Its thermal stability is 550°C (1022°F). However, its thickness is limited to limited to 5 μm (0.0002 in).
Key Takeaways of the article:
1: Basic Concept of Titanium Nitrite Coating
2: Tin Coating Techniques
3: Tin Coating Proess
4: Benefits of Titanium Coating
5: Applications of Nitride Coating
What is Titanium Nitride Coating?
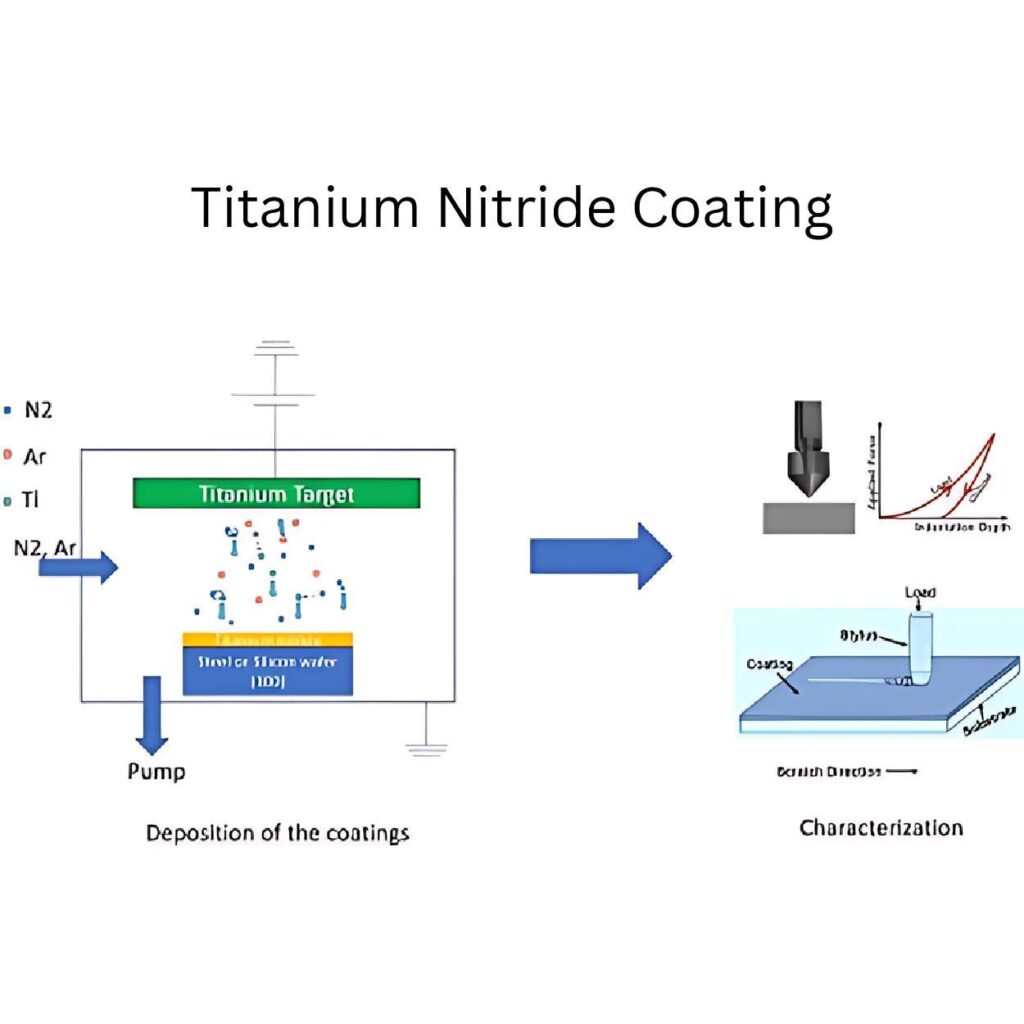
Titanium nitride is a durable ceramic compound. It is applied to the surfaces of metals. This coating is celebrated for its highly valued properties. For instance, hardness, stability, and resilience. The combinations of titanium and nitride elements create a recognized golden hue. This attractive shade provides an aesthetic values, whether it is a functional or decorative item. Such as cutting tools, medical devices, and consumer goods.
Chemically, TiN is a biological element that reduces temperature and degradation over time. It maintains stability at room temperature and protects the goods from extreme heat and corrosion, enabling long-lasting wearability. Tin coating surface treatments are generally used for metals like steel, carbide, and titanium to provide hardness and low friction.
Techniques of TiN Coating
Traditional methods of Titanium nitride coating are unsuitable for TiN. Manufacturers can apply the tin coating via advanced methods like physical vapour deposition (PVD) and chemical vapor deposition (CVD). Selecting the right technique from both methods depends on your item criteria. So that you can properly stick the coating layers on parts.
- Physical Vapor Deposition (PVD)
- Chemical Vapor Deposition (CVD)
Physical Vapor Deposition (PVD)
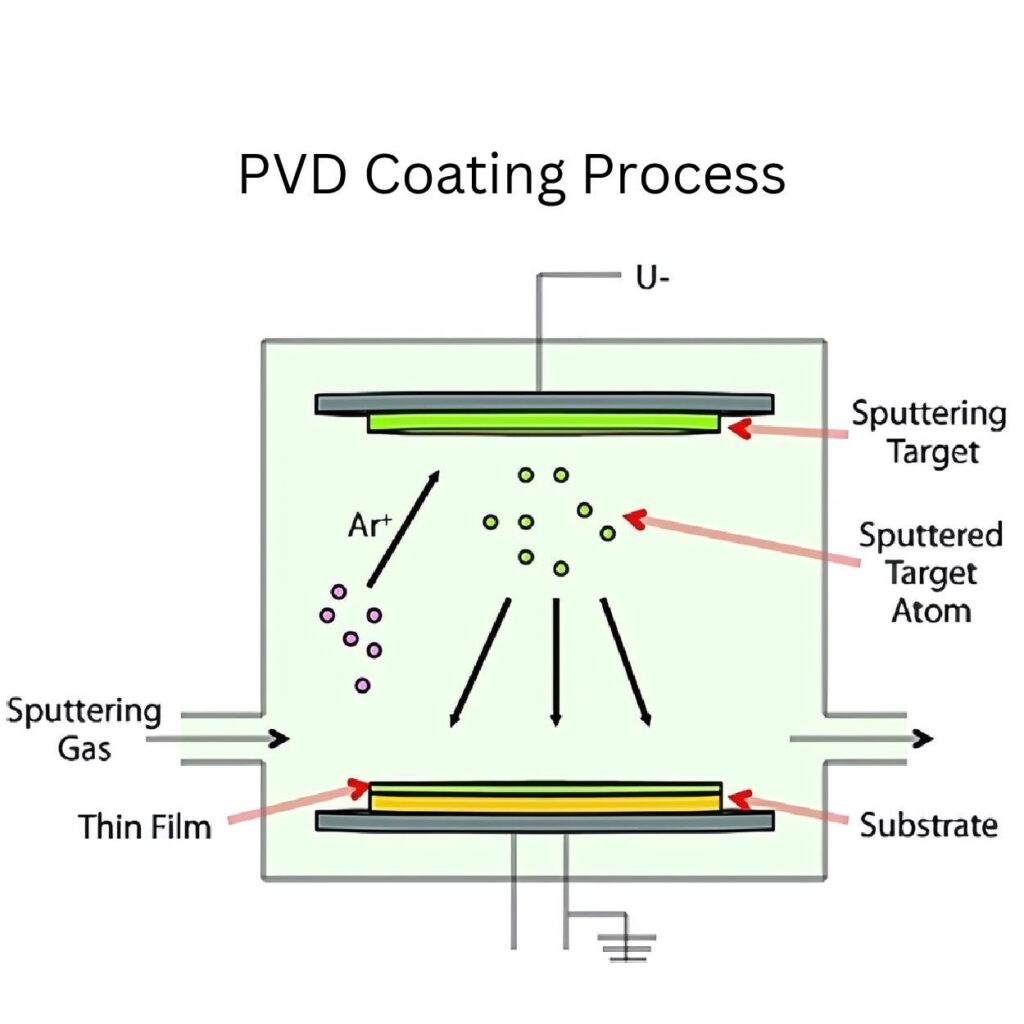
The operators vaporized the titanium component via a high-temperature vacuum, interacting with nitrogen elements. This vaporization forms the TiN coating on the metal surfaces. PVD coating is well known for its thin and adhesive coating layers. It has been widely used in the past with special needs of thin and hard coating at a time.
Chemical Vapor Deposition (CVD)
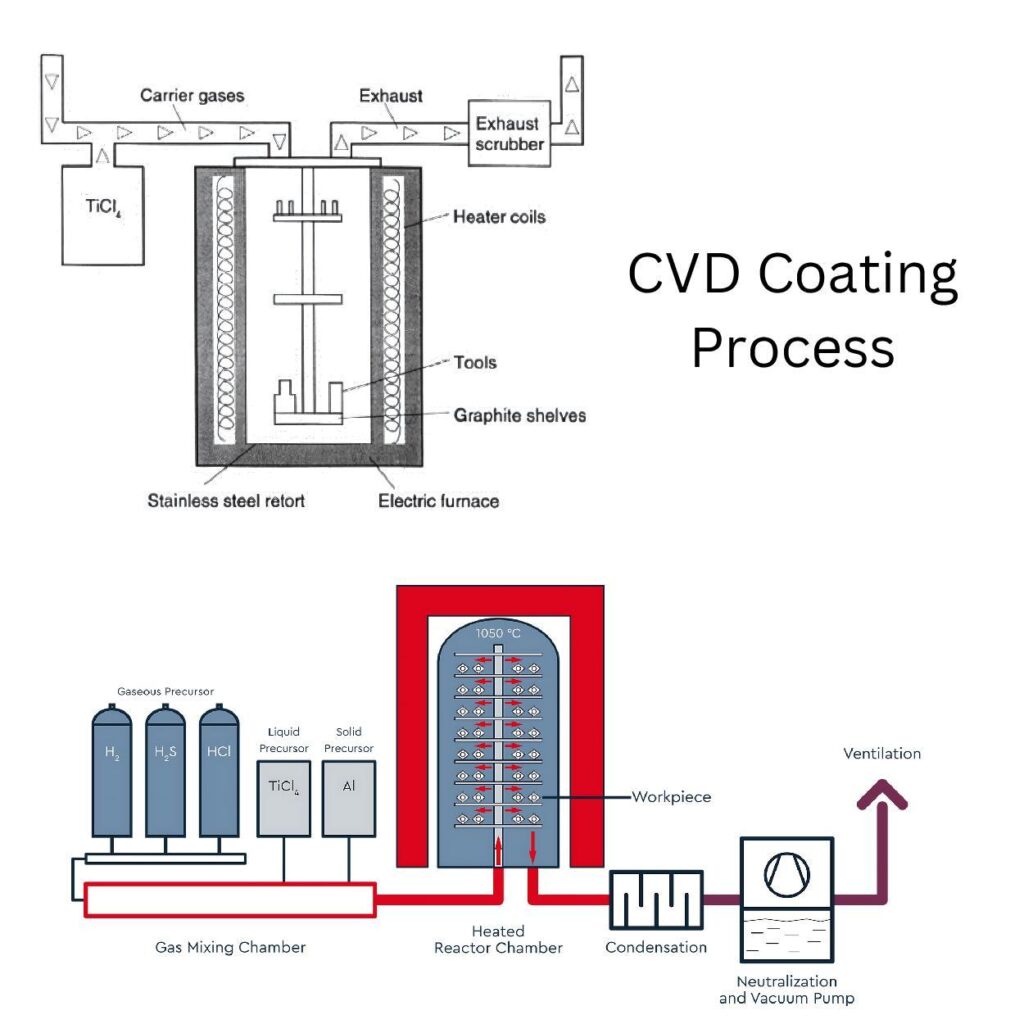
Tin coating via CVD is done by creating a chemical reaction to produce the layer over the metals. The manufacturers employ high temperatures to apply caoting through CVD compared to PVD. Thicker layers of coating for additional durability and protection under extreme stress are crucial. Therefore, CVD techniques are suitable for heavy-duty products.
TiN Coating Process
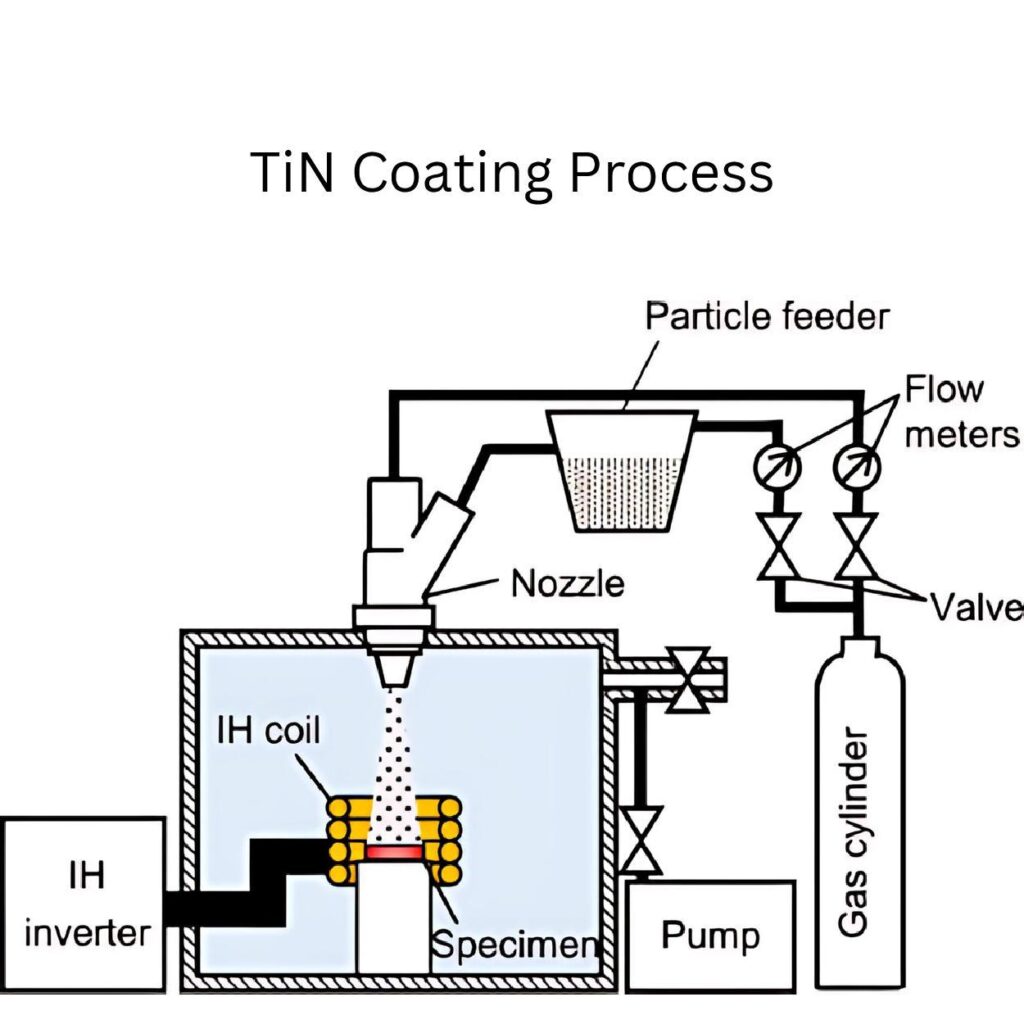
Manufacturing industries utilize PVD or CVD techniques to form the TiN coating on metal parts. They ensure the method meets the component’s unique demands, from surface finish to durability. These are the following steps to be focused on while proceeding with the coating:
- Surface Preparation
- Titanium Application
- Thermal Treatment
- Quality Control
Surface Preparation
The initial step of coating is to prepare the surface of metal. Use a detergent mixture to clean surfaces. Remove all dirt, debris, and oil thoroughly. Then dry the surfaces using soft cotton fabric.
Titanium Application
Select the appropriate technique to apply the TiN coating as the protective layer on the metals.
Thermal Treatment
The coating needs to be treated under high-heat segments so that it becomes adhesive and hardens, increasing its durability.
Quality Control
Inspect coated pieces to check the stickiness and solidification of layers. Make sure the parts meet the required quality standards. They perform well under high stress with stability.
Benefits of Titanium Nitride Coating
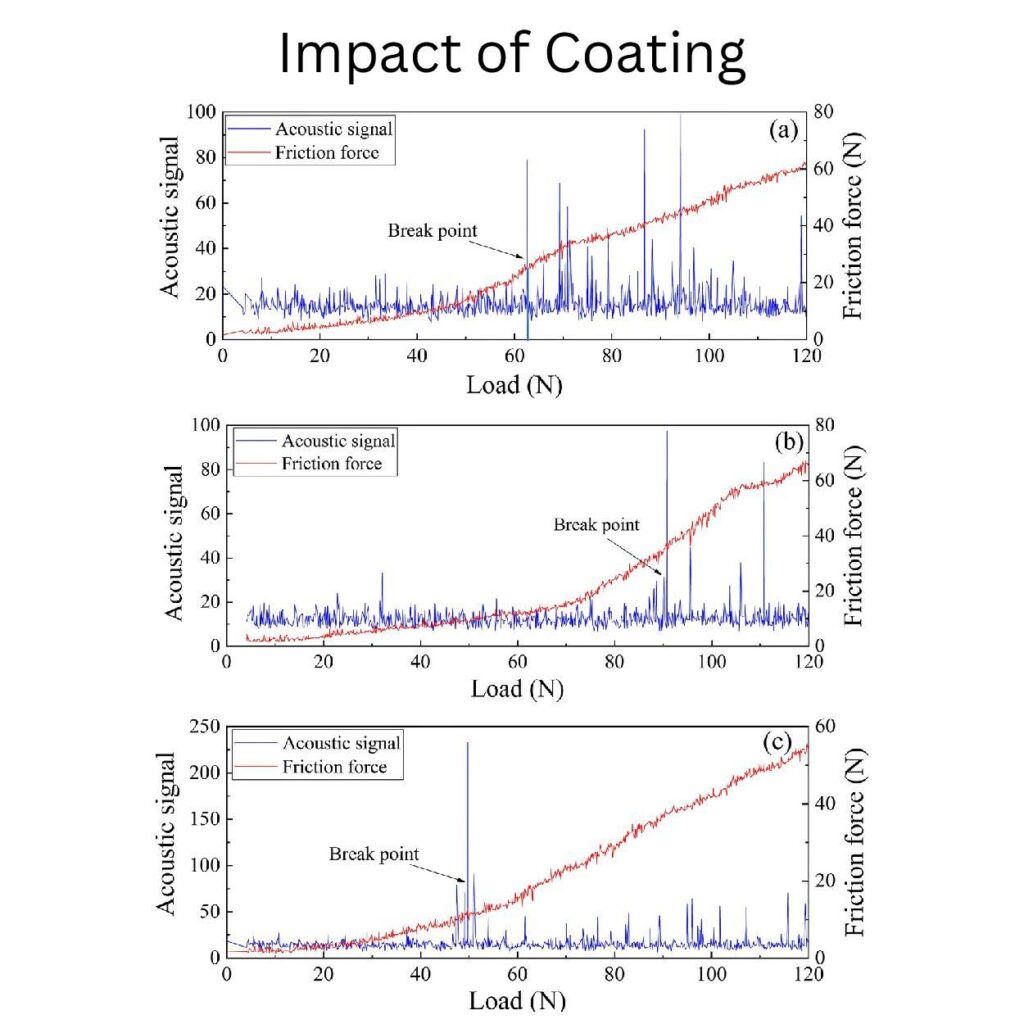
Titanium nitride protective layers significantly improved the performance of metal machinery and parts. These are the advantageous techniques to provide the component with strong, reliable resistance to oxidation and longevity. The major benefits of titanium coating include:
- Enhanced Durability
- Hardness
- Wear Resistance
- Surface Treatment
Enhanced Durability
Increasing the durability of metals like steel or carbide, TiN coating extends their service life. It also caters to reducing maintenance needs and replacement costs in the long run.
Hardness
TiN coatings reign supreme in hardness for coated surfaces. These protective layers make the parts harder, making them ideal for tools and machinery. The hardness capabilities of materials also perform well under extremely critical temperatures. This strength resists damage from impact, abrasions, and friction.
Wear Resistance
Titanina nitride boasts impressive wear resistance. It enables surfaces of metal to function effectively under high friction or for repeated use. It reduces the wear and tear of coated parts, maintaining their integrity and smoothness.
Surface Treatment
Metal parts that are made to perform under extreme conditions require effective surface treatments. Particularly, TiN coating is the process that prevents the surface from degrading over time. This layer is particularly needed for applications where repeated motions and high-speed operations are subject.
Applications of Titanium Nitride Coating
Tool Coatings in Manufacturing
Tool/Component | Description | Benefits of TiN Coating |
Drill Bits | Used in drilling operations across various materials, including metal, wood, and plastic. | Increases hardness and wear resistance.Reduces friction for smoother cuts.Extends tool life in high-speed applications. |
Cutting Tools (end mills, reamers, lathe tools) | Used for shaping and cutting metals. | Enhances edge retention.Prevents wear.Allows tools to maintain sharpness longer.Even under high-temperature conditions. |
Milling Cutters | Used in milling machines for removing material from a workpiece’s surface. | Provides greater durability.Reduces friction.Improves cutting efficiency.Making it suitable for heavy-duty machining tasks. |
Taps and Dies | Tools used to create and shape threads in holes (taps) and on rods (dies) in metals and other materials. | Reduces wear on the threading edges.Increases precision in thread cutting.Prolong tool life in industrial settings. |
Saw Blades | Used in metal and wood cutting, including circular and band saws. | Improves cutting performance.Reduces wear from friction.Provides smoother, cleaner cuts. |
Punches and Dies | Components used in stamping and forming operations to shape and cut materials. | Increases resistance to impact and wear.Extends component lifespan.Maintains sharp edges for high-quality stamping output. |
Injection Molding Tools | Molds are used in the plastic injection molding process to shape plastic parts. | Protects against wear from repeated mold cycles.Reduces maintenance needs.Improves release properties for molded parts. |
Broaches | Used to remove material in a single pass, creating complex shapes with high precision. | Enhances tool longevity.Reduces friction during material removal.Maintains cutting accuracy. |
Color Options and Aesthetic Benefits
Besides possessing impressive properties, TiN coatings also provide attractive appearances to the metals. It increases the aesthetic appeal and offers versatile color options. Discover the following benefits of tin coating color properties:
- Gloss and Matte Finishes
- Gold-Like Color Appeal
- Enhanced Product Value
- Applications in Decorative and Functional Items
Gloss and Matte Finishes
The availability of TiN coatings in silky, glossy, and matte finishes offers a reflective premium gold look. It creates a luxurious feel for items with good looks. Jewelry, watches, and other wearable accessories are examples. Moreover, companies benefit from the matte finishing of coating to make their parts sleek enough to use them for professional terms.
Gold-like Color Appeal:
The gold-like color appeal of the TiN coating provides visual appeal and durability to the parts. It resists color fading and maintains luster. These layers also protect the parts from hazardous elements. Gold tone is a decent look, not only for consumer goods but also for medical equipment and decorative parts.
Enhanced Product Value
Coating layers increased the visual impact of the product, adding a premium touch. Surgical parts, luxury products and hardware tool benefits form the beauty of coating without compromising their functionality.
Applications in Decorative and Functional Items
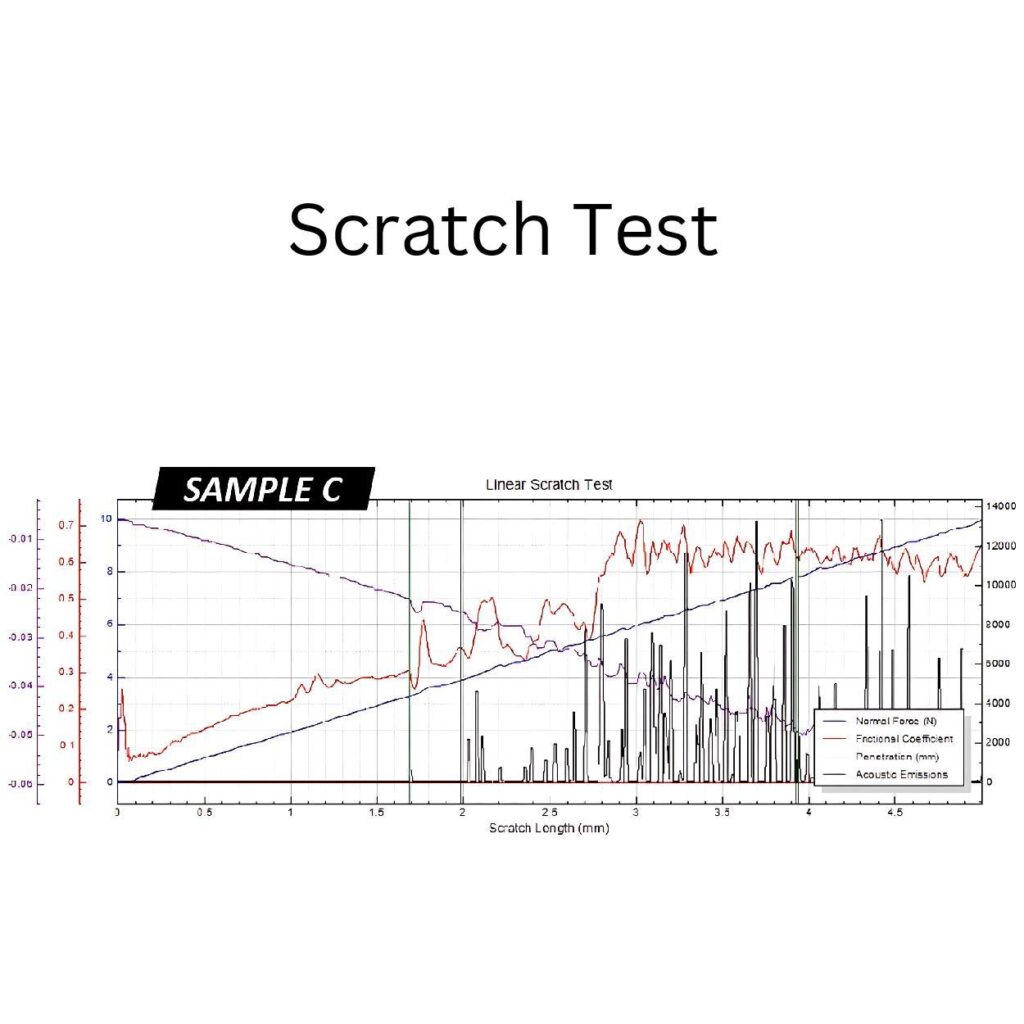
TiN coating is the most commonly used in decorative and functional items. They need to resist scratches, tarnishing, and corrosion. For instance, kitchen fixtures, eyewear and electronics.
Titanium Nitride Coating Challenges and Solutions
Titanium nitride coating notably addresses the various challenges of the industry. The susceptible parts of applications are improved with coating layers. These coatings drastically increase durability, reliability, and performance across diverse sectors.
1. Aerospace Industry Challenges
Aerospace parts are prone to critical issues like extreme heat, intense pressure changes, and high mechanical stress. These challenges cause damage to wear, corrosion, and oxidation.
TiN Coating as a Solution
Tin coating overcomes the challenges of aerospace parts. These layers enhance the wear resistance and thermal stability of components. It increases the lifespan of moving parts, recovering the energy losses. Moreover, additional coating layers improve the fuel efficiency without deteriorating.
2. Automotive sector solutions
Automotive industries demand parts that can endure continuous friction, intense speed, and overheating electronics parts. The parts of automotive vehicles, like pistons and transmissions, are liable to suffer wear.
TiN Coating as a Solution
TiN coating overcomes the challenges of high friction, corrosion, and wear and tear in automotive parts. It enhances the longevity of parts by providing low-friction surfaces for smooth operations. The other factors, like fuel efficiency, chemical oils, and automotive fluids, are also treated through TiN coatings.
3. Medical Applications
The medical equipment must be built to maintain strict performance and safety standards. Many surgical tools, orthopedic implants, and dental equipment are used continuously and need to be biocompatible and corrosion-resistant. These parts should be strong enough to pass the frequent sterilization process without losing integrity.
TiN Coating as a Solution
TiN coating repairs the surface of medical instruments. It makes the parts non-toxic and biocompatible for safer use. These coatings allow repeated sterilization processes under intense chemicals. Several infection risks and bacterial adhesions can also be reduced through the TiN coating process.
Comparative Analysis of Titanium Nitride Coating Techniques
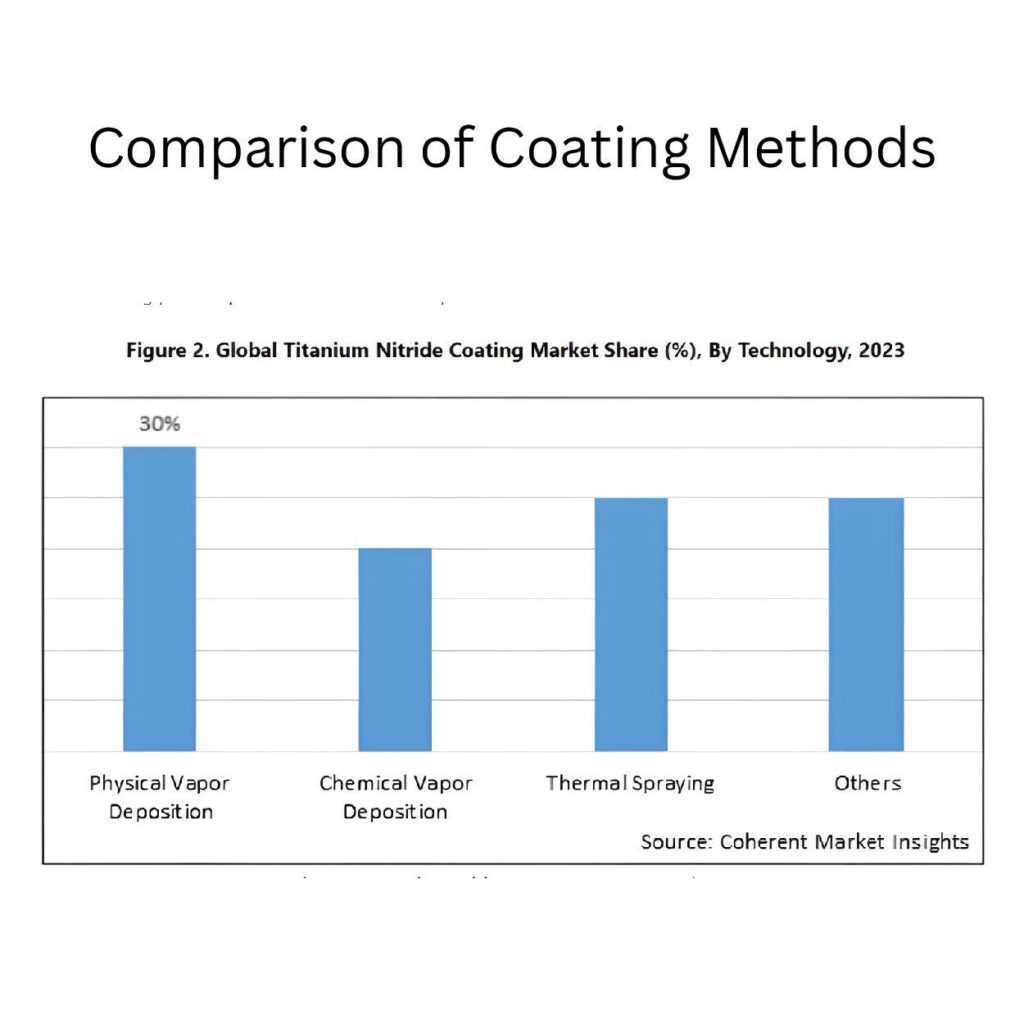
Coating Type | Titanium Nitride (TiN) | Carbide Coating | Chromium Plating |
Appearance | Golden, metallic appearance; available in gloss and matte finishes | Gray to metallic; typically matte | Shiny, reflective silver finish |
Hardness | High hardness; excellent wear resistance | Very high hardness; often harder than TiN | Moderate hardness, lower than TiN and carbide coatings |
Thermal Stability | High thermal resistance; suitable for high-temperature applications | Exceptional heat resistance; suitable for extreme temperatures | Good thermal resistance but lower than TiN and carbide |
Corrosion Resistance | Excellent corrosion resistance, particularly in harsh environments | Moderate corrosion resistance may vary by specific carbide type | Good corrosion resistance, though prone to cracking over time |
Coefficient of Friction | Low friction reduces wear and improves smoothness in moving parts | Low friction, but may vary; commonly used to reduce tool wear | Higher friction than TiN and carbide; not ideal for low-friction needs |
Biocompatibility | Biocompatible; suitable for medical applications | Generally not biocompatible for medical applications | It can be biocompatible if specific standards are met |
Durability | Long-lasting; ideal for high-wear applications | Very durable; especially suited for cutting tools | Good durability but may crack or chip with prolonged use |
Application Suitability | Ideal for tools, aerospace parts, automotive components, and medical devices | Commonly used in machining tools, industrial cutting applications | Decorative and protective on industrial parts, hardware, and consumer goods |
Cost | Moderate to high, depending on thickness and application method | High, especially for tools with specialized carbide coating | Moderate; typically lower than TiN and carbide |
Typical Application Techniques | PVD and CVD deposition methods | Thermal spray and sintering processes | Electroplating or hard chrome plating |
Titanium Nitride vs. Other Coatings
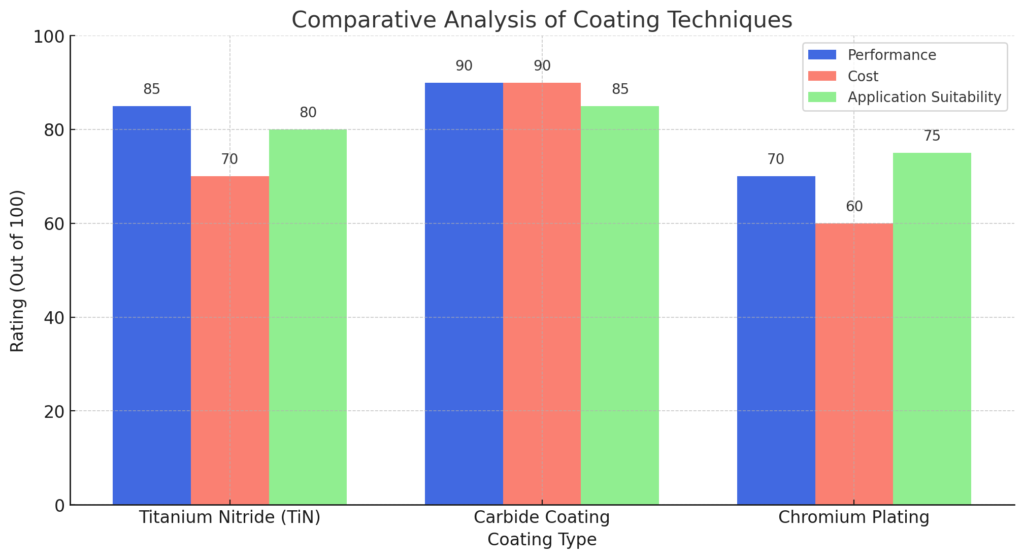
The comparative represents the hypothetic ratings for TiN carbide coating and chromium plating. Incorporating their performance, cost and application suitability.
Future Innovation in TiN Coating
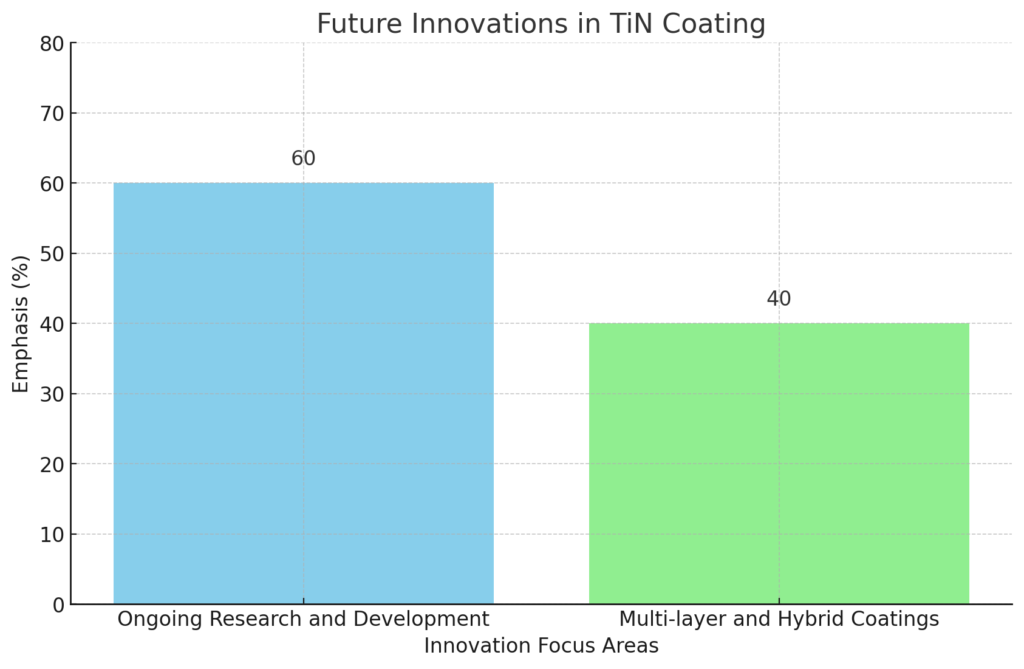
Ongoing Research and Development
Manufacturing processes and developments of TiN coating are concentrated on refining the deposition processes, like PVD and CVD. So that they can achieve the thinner and more uniform coating layers with improved adhesion attributes. The nanostructure TiN coating is also under improvement section to coat the nanosized particles at molecular state.
Multi-layer Coating
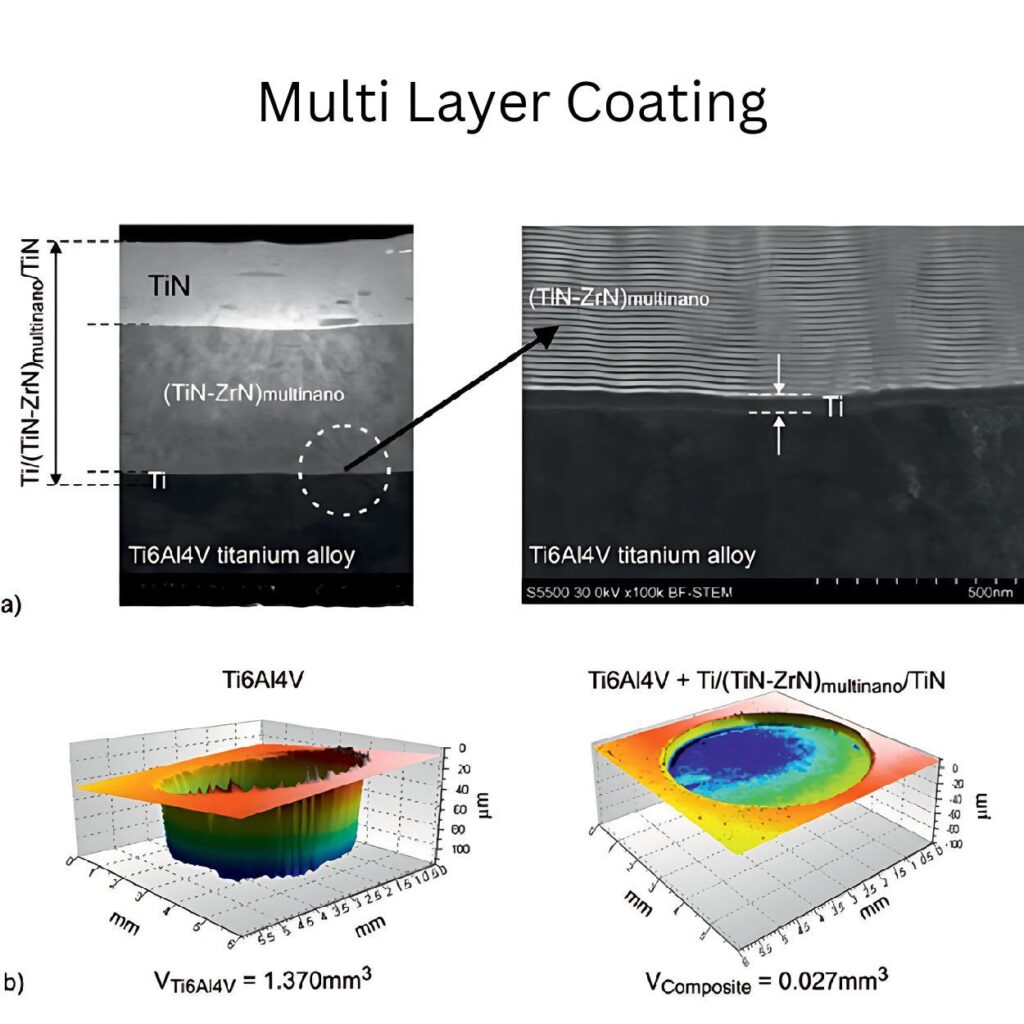
Multi-layer Titanium nitride coating is an exciting technology that enables the coating of multi-layer materials. These layers can incorporate aluminum or diamond-like carbon. This layer increases the functionality of parts beyond traditional ones.
Hybrid Coating
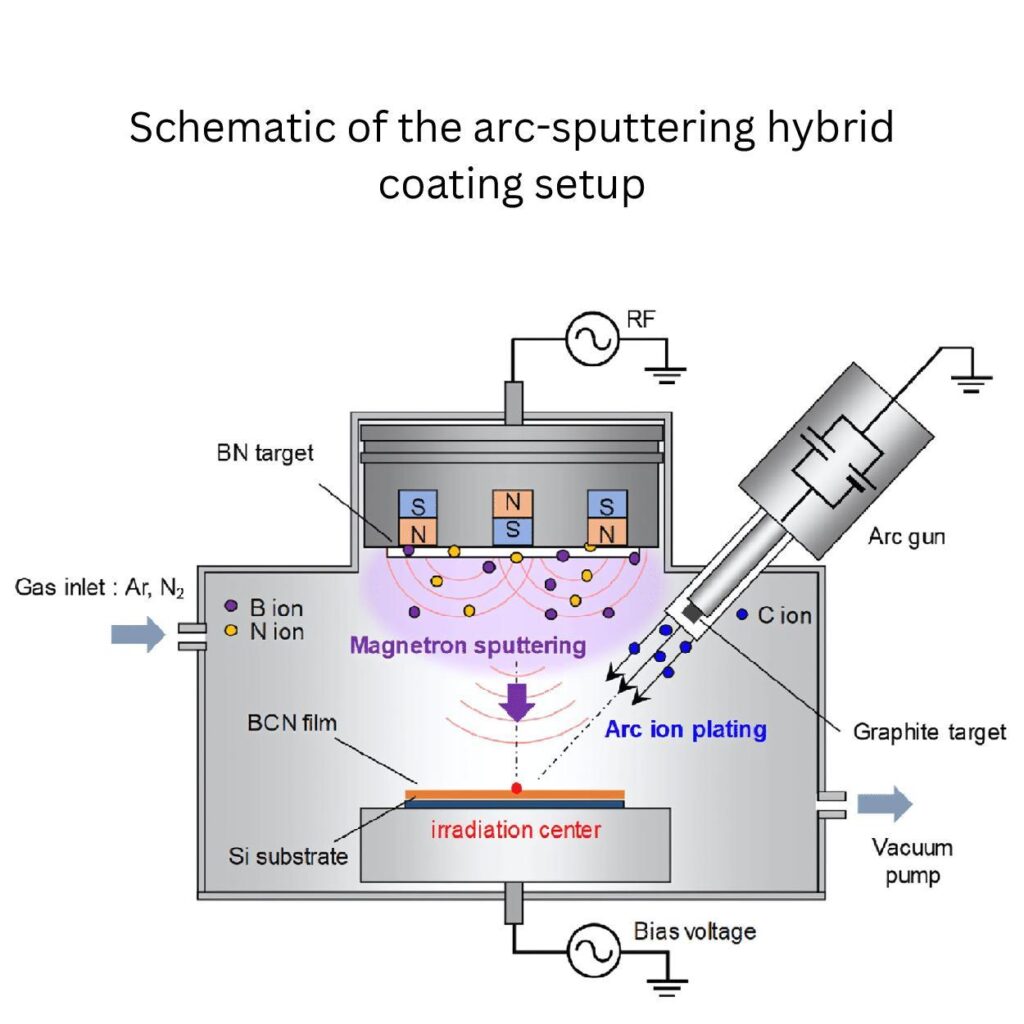
The hybrid coating is the combination of other ceramic or carbide layers tailored to solve unique part requirements. For instance, this coating can provide ultra-hard surfaces across high-pressure parts and machining tools.
Conclusion:
Every metal needs a special layer of protection to fight against several challenges, such as corrosion, oxidation, harsh chemicals, durability, and strength. Therefore, the metal die casters incorporate titanium nitride coating. This protective layer increases the performance of parts, providing exceptional solutions for different thermal and physical challenges.
0 Comments