Alüminyum Alaşımlı Döküm Özellikleri
Çünkü her ikisi de alümi̇nyum döküm alaşimlari ve dövme eşdeğerleri istenen niteliklerini alaşım elementlerinden ve ısıl işlemden alırlar, kimyasal olarak oldukça benzerdirler. İkisi arasındaki ayırt edici bir özellik, döküm özelliği geliştirme süreci sırasında iş sertleşmesinin olmamasıdır. Bu farklılık nedeniyle, döküm alaşımlarında ve dövme alaşımlarında kullanılan belirli alaşım elementleri farklı rollere hizmet eder.
Bir ürünün dökülebilirliği alümi̇nyum döküm alaşimi dövme bir alaşımdan ayırt etmek için ana kriterdir. Döküm alaşımları, tipik olarak temel yuvarlak veya dikdörtgen kesitlere öncelik veren döküm teknikleri kullanılarak yapılan dövme ürünlere kıyasla farklı zorluklar sunar. Karmaşık geometrilere ve değişen katılaşma hızlarına sahip mühendislik dökümleri için alaşımların katılaşma sırasındaki davranışlarına ilişkin özel hususlar gereklidir. Bu eğilimleri sınırlamak için, katılaşma sırasında ve sonrasında çatlamayı önleyecek ve iç büzülmeyi azaltacak şekilde form dökümü için alaşımların seçilmesi gerekli hale gelir.
"Dökülebilirlik" kelimesi, bir bileşimin belirli bir döküm işleminde katılaştırılıp katılaştırılamayacağını anlamada önemli bir faktördür ve mükemmel dökümlerin yapıldığından emin olmak için gereklidir. Kokil dökümde bir şeyin dökülebilmesini etkileyen çeşitli faktörler vardır. Bunlar arasında kalıbın ne kadar iyi doldurulabileceğini ölçen akışkanlık, katılaşma sırasında ve sonrasında sıcak çatlamaya karşı direnç ve katılaşma sırasında metalin akmasını kolaylaştırarak büzülme boşlukları riskini azaltan besleme özellikleri yer alır.
Çok yönlü bir faktör olduğu için kokil dökümde akışkanlığı doğru bir şekilde ölçmek ve tanımlamak mümkündür. Likidüsün üzerindeki sıcaklıklar veya aşırı ısınma derecesi bu özellik üzerinde en fazla etkiye sahiptir. Ötektik veya neredeyse ötektik bileşimlerin normal dolum sıcaklıklarında daha fazla akışkanlığa sahip olması yaygındır.
Basınçlı döküm için, bir şeyi artık dökülebilir yapan şeyler arasında sıcak çatlamaya, akışa, kalıp lehimlemeye ve yüzey kaplamasına direnme yeteneği bulunmaktadır. Bu parçaların her biri döküm işleminin çalışması için çok önemlidir. Bu faktörler arasında doğru dengeyi bulmak, dökümlerin hatasız olmasını, farklı döküm yöntemlerinin ihtiyaçlarını karşılamasını ve son ürünün sağlam kalmasını sağlamak için önemlidir.
Dar solidus-likidus bantları, özellikle ötektik sıcaklıkta daha yüksek bir sıvı yüzdesi olduğunda, genellikle daha iyi besleme özellikleriyle bağlantılıdır. Elementlerin yüksek sıcaklık mukavemeti ve katılaşma hızı üzerindeki etkileri, bir şeyin katılaşma ve katılaştıktan sonra çatlama olasılığını belirleyen ana unsurlardır.
Metal kimyasının, dökümün önemli bir parçası olan kalıp lehimleme ile çok ilgisi vardır. Ancak kalıp durumu ve diğer proses faktörleri de çok önemlidir. A'dan F'ye veya 1'den 10'a ya da "mükemmel döküm özellikleri" ile "zayıf döküm özellikleri" arasında değişen dökülebilirlik dereceleri çok sayıda uygulama ile oluşturulmuştur.
Çoğu dövme alaşımdan daha fazla silisyum içeren döküm alaşımlarının, özellikle yüksek hacimli kullanımlar için çok fazla kullanımı vardır. Şekillendirilmiş kalıplara silikon eklemek onları daha akışkan, yüksek sıcaklıklarda çatlama olasılığı daha düşük ve beslenmesi daha kolay hale getirir. Farklı döküm yöntemleri en iyi sonuçları almak için farklı miktarlarda silikona ihtiyaç duyar. Çok fazla ısı kullanan prosesler daha fazla silikon içeren metalleri tercih eder, bu da onları daha akışkan hale getirir. Döküm prosesi, besleme mekanizmasını etkileyen katılaşma bölgesindeki gradyanları kontrol eder. Bu mekanizma iç büzülmeyi dengelemek için çok önemlidir. Genel olarak, daha küçük katılaşma aralıklarına sahip metallerin dökümü daha kolaydır.
Döküm için iyi çalışsalar da, birçok popüler döküm alüminyum alaşımı sadece silikona bağlı değildir. Alüminyumla ilgili en iyi şeylerden biri geri dönüştürülebilmesidir. Bu, özellikle yeniden eritilmiş hurdadan bir şeyler yapmak için üretilen döküm alaşımlarının yaratılmasına yol açmıştır. Bu "ikincil" formüller daha geniş safsızlık aralıklarına sahiptir çünkü hammaddelerdeki farklılıkları hesaba katmak için safsızlık olarak daha fazla element içerirler. Birincil alaşımlar ise eritilmiş alüminyum, endüstriyel metaller ve ana alaşımlardan yapılır. Elementlerle ilgili safsızlıklar konusunda daha katı sınırlara sahiptirler.
Alüminyum Alaşımlı Dökümlerin Avantajları ve Sınırlamaları
Alüminyum alaşımlı dökümlerin üretimi, elde edilebilir özelliklerde kapsamlı çok yönlülüğü vurgulayan geniş bir alaşım yelpazesi sergiler. Alüminyum Birliği 100'den fazla bileşimi kayıt altına alırken, küresel olarak 300'den fazla alaşım uygulama alanı bulmaktadır. Metal-matris ve diğer kompozit yapıların sunduğu çok yönlülüğün ötesinde, bu alaşımlar aşağıdakileri içeren çok çeşitli özellikler sergiler:
Çekme mukavemeti, ksi (MPa) 10-72 (70-505)
Akma dayanımı, ksi (MPa) 3-65 (20-455)
Uzama, % <1-30
Sertlik, HB 30-150
Elektriksel iletkenlik, %IACS 18-60
Isı iletkenliği, 77 °F'de Btu - in./h - ft2 - °F
(25 °C'de W/m - K)
660-1155 (85-175)
Yorulma limiti, ksi (MPa) 8-21 (55-145)
Doğrusal termal genleşme katsayısı
68-212 °F'de (20-100 °C)
9.8-13.7 [1] 10-6/°F
(17.6-24.7) [1] 10-6/°C)
Kesme mukavemeti, ksi (MPa) 6-46 (42-325)
Elastisite modülü, 106 psi (GPa) 9,5-11,2 (65-80)
Özgül ağırlık 2.57-2.95
Doğru boyutlara, düzenlenmiş yüzey kalitesine, iç geçişler de dahil olmak üzere karmaşık geometrilere ve belirtilen mühendislik standartlarına uygun özelliklere sahip neredeyse hassas parçalar üretme kabiliyeti, aşağıdaki gibi önemli üretim avantajları oluşturmaktadır.
- Birçok durumda, çok bileşenli kaynaklı veya birleştirilmiş montajlar tek bir döküm parça ile değiştirilebilir.
- Azaltılmış işleme gereksinimleri maliyet ve zaman tasarrufuna katkıda bulunur.
- Alüminyum alaşımlı dökümler, döküm yüzeyinde kontrollü varyasyonlar gösterir.
- Hoş kozmetik etkiler yaratmak için döküm ve işlenmiş yüzeyler arasındaki kontrastlar vurgulanabilir.
- Sermaye gereksinimleri genellikle dövme ürünlere kıyasla daha düşüktür.
- Kalıp seçenekleri, basit kalıplardan karmaşık takım çeliği kalıplarına kadar uzanır ve çeşitli ürün gereksinimlerini ve üretim hacimlerini karşılar.
- Rutin döküm, metalürjik veya mekanik olarak bağlanmış bimetal parçaları içerir.
- Alüminyum parçalar, hacim, üretkenlik, kalite, mekanizasyon ve özel yetenekler açısından çok yönlülük sunan çeşitli süreçlerle dökülür.
- Çoğu alüminyum döküm alaşımı, dökümhane gereksinimleriyle uyumludur ve yüksek kaliteli parçaların üretilmesini sağlar.
- Çeşitli alüminyum döküm alaşımları, ince kesitlerin ve karmaşık detayların dökümünü kolaylaştıran mükemmel akışkanlık gösterir.
- Alüminyum döküm alaşımları için daha düşük ergitme sıcaklıkları enerji verimliliğine katkıda bulunur.
- Alüminyum döküm prosesleri yüksek otomasyon seviyelerine uygundur, ancak dökülemeyebilecek çok ince kesitlerle ilgili zorluklar gibi bazı sınırlamalar geçerlidir.
Alüminyum alaşımlı dökümler, karmaşık mühendislik konfigürasyonlarında veya özel döküm yöntemlerinde dökümü engelleyebilecek belirli alaşımların katılaşma davranışından etkilenen belirli döküm işlemlerinde pratik boyut sınırlamalarıyla karşılaşır. Dövme, ekstrüzyon ve haddelenmiş ürünlerin üretimine kıyasla döküm işleminin basitliğine ve daha düşük sermaye yoğunluğuna rağmen, diğer imalat seçeneklerine benzer şekilde karmaşık geometrik şekillerde katılaşma, yüzey süreksizliklerine ve değişen derecelerde kaliteye sahip iç mikroyapı özelliklerine yol açabilir ve ardından özellikleri ve performansı etkileyebilir.
Özellikle, alüminyum alaşımlı dökümler, çoğu dövme, ekstrüzyon ve haddelenmiş plakalarla karşılaştırılabilir gerilme özellikleri sergileme potansiyeline sahiptir. Belirli anizotropi ve yüksek dokulu mikroyapısal özelliklere sahip ince rekristalize tane yapıları gibi dövme ürünlerin ayırt edici özellikleri, genellikle daha kaba tane yapılarına sahip dökümlere kıyasla uzunlamasına yönlerde daha fazla süneklikle sonuçlanır. Buna karşılık, döküm yapılarda tipik olarak tek eksenli tane yapısı ve anizotropinin olmaması, tasarım mühendislerinin işini kolaylaştırarak enine özellik sınırlamalarıyla ilgili zorlukları ortadan kaldırır.
Ne tür alüminyum basınçlı döküm malzemeleri kullanılır?
Alüminyum döküm söz konusu olduğunda, malzeme seçimi nihai bileşenlerin özelliklerini ve işlevselliğini önemli ölçüde etkiler. Birçok alüminyum alaşımı belirli ihtiyaçlara hizmet eder. Mukavemet, korozyon direnci, termal iletkenlik ve döküm karakterizasyonu gibi bir dizi kriter bu alaşımların seçimini belirler. Bunlar, alüminyum basınçlı dökümde kullanılan en yaygın malzeme türlerinden bazılarıdır:
Alüminyum Alaşım | Özellikler | Uygulamalar |
A380 | İyi akışkanlık, yüksek mukavemet ve mükemmel korozyon direnci | Özellikle ABD'de kullanılan otomotiv bileşenleri, ev aletleri ve endüstriyel uygulamalar. |
ADC12 | Mükemmel dökülebilirlik yüksek mukavemet, iyi korozyon direnci | Otomotiv parçaları, elektronik bileşenler, ağırlığa duyarlı uygulamalar ve ADC12 dünya çapında kullanılmaktadır. |
A383 | Sıcak çatlamaya karşı geliştirilmiş direnç; iyi akışkanlık; ve iyi korozyon direnci | Otomotiv, elektronik ve tüketim malları için karmaşık dökümler |
A360 | Yüksek mukavemet, basınç sızdırmazlığı ve mükemmel korozyon direnci | Otomotiv parçaları Telekomünikasyon ekipmanları Özel olarak kum döküm veya kokil dökümde kullanılan yapısal bileşenler |
6061 | ısıl işlem uygulanabilir, yüksek mukavemetli, iyi korozyon direnci | Havacılık ve uzay bileşenleri, yapısal parçalar ve döküm sonrası ısıl işlem içeren uygulamalar ekstrüzyon alanında kullanılmaktadır, ancak yüksek basınçlı döküm hala işe yaramaktadır. |
7075 | Isıl işlem uygulanabilir: çok yüksek mukavemet ve tokluk | Havacılık ve uzay bileşenleri; askeri uygulamalar yüksek gerilimli yapısal parçalar, özellikle parçaların işlenmesi için. |
AlZn10Si8Mg | İyi dökülebilirlik yüksek mukavemet ve mükemmel korozyon direnci | Otomotiv bileşenleri ve endüstriyel uygulamalar Özellikle Avrupa'da kullanılan yapısal parçalar |
Al-Si7Mg | İyi ısı direnci yüksek mukavemet, iyi korozyon direnci | Özellikle Avrupa'da kullanılan otomotiv bileşenleri, motor bileşenleri ve endüstriyel uygulamalar |
6063 | İyi ekstrüde edilebilirlik orta mukavemet; mükemmel korozyon direnci | mimari uygulamalar Elektrikli bileşenler Otomotiv trimi ekstrüzyon profilinde özel olarak kullanılır, ancak 6063 yüksek basınçlı döküm hala çalışır. |
LM25 | İyi dökülebilirlik orta mukavemet; iyi korozyon direnci | Otomotiv bileşenleri; denizcilik uygulamaları genel mühendislik, özellikle kum döküm veya gravite dökümde kullanılır, ancak yüksek basınçlı döküm hala |
Alüminyum Alaşımlı döküm Özellikleri
Alüminyum döküm alaşımları için farklı kurallar ve spesifikasyonlar geçerlidir. Bu durum özellikle Alüminyum Birliği'nin alaşım kimyası ve sıcaklık uygulamalarını takip ettiği ABD'de geçerlidir. Tedarik için standartlar ve gereklilikler ASTM, ordu ve federal kurumlar gibi gruplar tarafından belirlenir ve uygulanır. Bu standartların kapsadığı prosedürler arasında radyografik ve penetrant muayene, kimyasal, mekanik ve fiziksel özellikleri bulmak için test teknikleri ve diğer önemli adımlar yer alır. Alıcı genellikle belirli parçalara veya parça gruplarına uyması için özellikleri değiştirir. Satın alma yapılmadan önce hem döküm üreticisinin hem de müşterinin spesifikasyonlar ve istisnalar üzerinde anlaşması çok önemlidir.
Alüminyum alaşım formülleri için spesifikasyonlar, her biri farklı bir işleve sahip olan majör, minör ve safsızlık elementlerini içerir:
Başlıca alaşım elementleri: Bunlar, metalin ne kadar iyi yapılabileceğini ve özelliklerinin zaman içinde nasıl değişeceğini kontrol eden aralıkları belirler.
Alüminyum döküm alaşımlarındaki minör elementler: alaşımın katılaşma şeklini, ötektik yapısını, ana fazları, tane boyutunu ve oluşumunu ve fazların gelişimini değiştirirler. Bunun yanı sıra, kirliliğin azaltılmasına yardımcı olurlar.
Safsızlık unsurları: Bunlar malzemenin ne kadar kolay dökülebileceğini ve fazların ne kadar çözünmez hale geleceğini etkiler, bu da bazen istenen niteliklere yardımcı olabilir veya zarar verebilir.
Alüminyum döküm alaşımları için spesifikasyonlar majör, minör ve safsızlık elementleri için en iyi konsantrasyonların ve ilişkilerin ne olduğunu tam olarak söylemese de, nominal kimyalar otomatik olarak en iyi sonuçları vaat etmez. Belirli kimyasal sınırlar dahilinde, yapıyı kontrol eden elementler tek başlarına veya gruplar halinde eklenebilir. Bu durum özellikle "Diğer Elementler" altında özellikle belirtilmedikleri zaman geçerlidir.
Tercih edilen faz oluşumu için stokiyometrik oranlar verebilirsiniz, ancak bunlar her zaman net veya kontrollü olmayabilir. Konsantrasyon limitleri size dökülebilirliği ve özellik gelişimini iyileştirmek için bileşimi değiştirme özgürlüğü verir. En güçlü malzemeleri elde etmek için sertleştirme fazları oluşturan elementlerin en yüksek miktarlarını elde etmek mümkündür. Öte yandan, daha iyi süneklik için, daha ince yapılar, daha düşük miktarlarda çözünmeyen elementler ve en az zararlı metaller arası bileşenlerin oluşumunu teşvik etmek için safsızlık seviyelerinin dikkatli bir şekilde kontrol edilmesi gerekir. Bileşim önyargısı külçe satın alındığında ayarlanabilir veya alaşımlama dövme sırasında değiştirildiğinde gerçekleşebilir.
GC Precision Mould'a hoşgeldiniz, üstün ürünler için ilk adresiniz alümi̇nyum döküm alaşimlari Çin'de çözümler. Lider bir şirket olarak basınçlı döküm Çin üretici ve KALIP YAPIMCISIyüksek kaliteli plastik kalıplar, basınçlı döküm kalıpları ve alüminyum, çinko ve magnezyum gibi birinci sınıf malzemelerden hazırlanmış çok çeşitli basınçlı döküm parçalar sunma konusunda uzmanız.
GC Precision Mould'daki değişmeyen hedefimiz, müşterilerimize mümkün olan en iyi alüminyum döküm ve diğer döküm ürün ve hizmetlerini sunmaktır. Ürettiğimiz her bir parçanın doğruluk ve kalite için en katı gereksinimleri karşıladığından emin olmak için profesyonel deneyimli mühendislerimiz ve teknisyenlerimiz var. hakkında bilgi alüminyum döküm gövde Eğer sana yardım edebilirse.
Otomotiv, tüketici elektroniği, medikal ve endüstriyel ekipman dahil olmak üzere çok sayıda sektör geniş ürün yelpazemizi kullanmaktadır. Müşterilerimizle güçlü ilişkiler geliştirmekten, onların özel ihtiyaçlarını öğrenmekten ve taleplerini tam olarak karşılayan özel çözümler üretmekten büyük memnuniyet duyuyoruz.
Alüminyum Alaşımlı Döküm gereksiniminiz için Neden GC Precision Mould'u Seçmelisiniz?
Üst Düzey Uzmanlık: Her alüminyum alaşımlı döküm projesi, deneyimli profesyonellerden oluşan ekibimiz tarafından kalite ile ele alınır.
En İleri Teknoloji: Döküm süreçlerimizde en yüksek kalite standartlarını garanti etmek için en son teknolojik gelişmelerden ve yaratıcı metodolojilerden yararlanıyoruz.
Çok Sayıda Endüstri Uygulaması: Ürünlerimiz, alüminyum alaşımlı döküm hizmetlerimizin uyarlanabilirliğini ve çeşitliliğini gösteren geniş bir sektör yelpazesine hizmet etmektedir.
Kişiye Özel Çözümler: Müşterilerimizin benzersiz ihtiyaçlarını tam olarak kavramak ve üretim hedeflerini tam olarak yerine getiren özel çözümler sunmak için onlarla yakın işbirliği içinde çalışıyoruz.
Her Şey Dahil Hizmetler: Tek bir plastik kalıptan tüm bir basınçlı döküm üretim hattına kadar projenin boyutundan bağımsız olarak olağanüstü sonuçlar sağlayacak bilgi birikimine ve araçlara sahibiz.
Alüminyum alaşımları için en üst düzey döküm mükemmelliğini keşfetmek için GC Precision Mould ile çalışın. Tekliflerimiz hakkında daha fazla bilgi edinmek ve üretim faaliyetlerinizi yeni zirvelere taşımak için deneyimlerimizden nasıl kolayca yararlanabileceğinizi öğrenmek için hemen şimdi bizimle iletişime geçin. En iyi fırsatlar ve eşsiz kalite için, yaklaşan bir kalıp döküm projeniz varsa veya alüminyum alaşımlı döküm için güvenilir kalıp tedarikçileri arıyorsanız bizimle iletişime geçin. Mükemmellik ve hassasiyetin çarpıştığı GC Hassas Kalıp ile başarınız burada başlar.
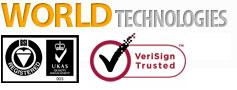
Ev Çözüm Destek Bağlantılar Kariyer Blog Site Haritası
Telif Hakkı © 2011-2014 GC Hassas Kalıp tüm hakları saklıdır