Zinkdruckguss Hersteller in China
OEM-Auftragsfertigung von Zinkdruckguss mit Zamak 3, Zamak 5...
Zinkdruckguss, sein Verfahren, seine Anwendungen und Design-Tipps
Wenn es um die Herstellung von Metallteilen geht, Zinkdruckguss Teil ist eine sehr gefragte Option. Es werden verschiedene Legierungen verwendet, um komplexe Zinkmetallteile herzustellen. Diese Teile haben starke mechanische Eigenschaften. Neben ihrer Festigkeit besitzen diese Teile auch außergewöhnliche mechanische Eigenschaften. Aus diesem Grund werden sie in verschiedenen Anwendungen eingesetzt. Hier werden wir diese Anwendungen im Detail besprechen. Außerdem werden wir den gesamten Prozess, Designtipps, Vorteile, Nachteile und Alternativen im Detail besprechen.
Wie würden Sie Zinkdruckguss definieren?
Es handelt sich um ein Verfahren zum Gießen von Metalllegierungen. Zunächst schmilzt die Zinklegierung in einen geschmolzenen Zustand ein. Anschließend wird das geschmolzene Zink mit hohem Druck in einen Formhohlraum (Metalldruckgussform) gepresst. Dann nimmt das Zink die Form einer Matrize an. Anschließend kühlt das Zink ab und wird aus der Form ausgestoßen. Daher eignet sich diese Technik am besten für die Herstellung großer Mengen von Teilen aus einer mittleren Zinklegierung. Dieses Verfahren wird häufig zur Herstellung hochpräziser Teile verwendet. Außerdem können verschiedene Zinklegierungen verarbeitet werden, z. B. Zamak (Zamak 3, Zamak 5) und die ZA-Serie.
Welche Verfahren werden bei der Herstellung von Zinkdruckguss eingesetzt?
Hier finden Sie eine ausführliche Beschreibung der Schritte, die bei der Herstellung von Zinkdruckgussbauteilen erforderlich sind.
1. Konstruktion und Werkzeugbau
Der Zinkdruckguss beginnt mit der Konstruktionsphase. Diese Phase kann die Konstruktion von Teilen aus Zinklegierung und die Konstruktion von Werkzeugen umfassen. Die Ingenieure verwenden intelligente Software, d.h. CAD oder CAM, um die Teile und Werkzeuge zu entwerfen. Sie fügen alle kleinen Details zu den Entwürfen hinzu, um die Präzision des Zinklegierungsteils zu gewährleisten. Sie berücksichtigen sorgfältig die folgenden Aspekte des Teiledesigns:
- Entwurfswinkel: Die Ingenieure stellen die Entformungswinkel zwischen 1 und 3 Grad ein. Das hilft, das Teil aus der Zinklegierung aus der Form zu entfernen.
- Wanddicke: Sie erhalten eine gleichmäßige Wandstärke. So können sie Defekte verhindern und eine ordnungsgemäße Füllung ermöglichen.
- Rippchen und Filets: Die Ingenieure bauen Rippen und Verrundungen in ihre Entwürfe ein. Die Rippen tragen zur Verstärkung des Bauteils aus einer Metalllegierung bei. Die Verrundungen helfen dabei, scharfe Ecken zu vermeiden, um Spannungen zu verhindern.
Außerdem stellen die Ingenieure bei der Konstruktion von Werkzeugen zunächst eine Matrize oder Form her. Diese wird in der Regel aus hochwertigen Stählen wie H13, 8407 und 1.2344 hergestellt. Diese Matrize besteht also aus zwei Hälften, nämlich der Deckelmatrize (feststehende Hälfte) und der Auswerfermatrize (bewegliche Hälfte). Daher haben wir die Matrize so entworfen, dass sie mit den CAD-Entwürfen übereinstimmt. Das garantiert, dass das endgültige Teil genau wie eine Matrize aussehen wird.
2. Schmelzen und Einspritzen
Dieser Schritt umfasst das Schmelzen des Zinkmaterials. Dies geschieht in der Regel in einem Schmelzofen. Dabei achten wir darauf, dass die Temperatur zwischen 370°C und 430°C (700°F und 800°F) liegt. Dieser Bereich trägt dazu bei, dass das Zinkmetall in einem geschmolzenen Zustand bleibt. Danach kann das geschmolzene Zink in die Druckgussmaschine eingespritzt werden. Diese Maschine besteht aus einem Stempel, einem Formhohlraum und einer Kühlkammer. Nach dem Einspritzen der geschmolzenen Legierung in die Maschine übt der Stempel einen hohen Druck aus, der die Legierung in den Formhohlraum drückt. Dann nimmt das geschmolzene Zink die Form einer Matrize an und erreicht alle ihre Abmessungen.
3. Abkühlung und Erstarrung
Nach dem Einspritzvorgang wird das geschmolzene Zink durch das Kühlsystem abgekühlt. Die Stahlform beginnt, das geschmolzene Zink schnell abzukühlen. Diese Abkühlung hat jedoch gewisse Grenzen. Daher wird sie in der Regel mit Hilfe von Kühlkanälen fixiert. Durch diese Kanäle wird das Kühlmittel, also Wasser, geleitet. Sie tragen zur Abkühlung des Zinks bei. Nach der Abkühlung beginnt das Zink zu erstarren. In diesem Stadium nimmt es die Abmessungen der Form an. Außerdem trägt die schnelle Abkühlung dazu bei, feinkörnige Strukturen mit hoher Festigkeit zu erhalten. Außerdem hängt die Abkühlzeit von der Größe und Komplexität des Teils ab. Einfachere Konstruktionen kühlen früher ab.
4. Auswerfen und Beschneiden
Der letzte Schritt des Zinkdruckgussverfahrens ist das Ausstoßen und Beschneiden des Zinkteils. Nach der Erstarrung öffnet sich die Form. Dann beginnen die Auswerferstifte, das Teil aus der Form zu drücken. Diese Form ist intelligent konstruiert. Es kann sich leicht aus dem Formhohlraum lösen, ohne Schaden anzurichten. Außerdem setzt sich überschüssiges Material, d. h. Grat, an den Kanten des Zinkteils fest. Es ist wichtig, diesen zu entfernen. Dies wird durch den Entgratungsprozess erreicht. Bei diesem Prozess können verschiedene mechanische Verfahren wie Schneiden, Schleifen oder Feilen zum Einsatz kommen. Alle diese Verfahren führen zur Herstellung von Feinteilen.
5. Sekundäre Prozesse
Einige Teile sind nach dem Beschnitt fertiggestellt. Aber einige von ihnen müssen zusätzlich bearbeitet werden. Sie können ein besseres Aussehen und bestimmte Abmessungen erhalten. Zum Beispiel das Bohren von Löchern, Gewinden oder das Veredeln von Oberflächen. Einige Teile benötigen ein besseres Aussehen und zusätzliche Eigenschaften wie Korrosionsbeständigkeit und Funktionstüchtigkeit, weshalb sie lackiert werden können. Außerdem benötigen einige Zinkteile eine dauerhafte Oberflächenbehandlung. Sie können rauen Umgebungsbedingungen standhalten; sie können einem Pulverbeschichtungsverfahren unterzogen werden.
Häufig verwendete Zinklegierungen für den Druckguss
Hier sind die verschiedenen Legierungen von Zink. Sie haben verschiedene Anwendungen in unterschiedlichen Bereichen. Lassen Sie uns ihre Eigenschaften, Zusammensetzung und Anwendungen im Detail besprechen.
Legierung aus Zn |
Zusammensetzung |
Eigenschaften |
Typische Anwendungen |
Zamak 3 |
Zn 96%, Al 4%, Mg 0,03% |
Gute Ausgewogenheit von Festigkeit, Duktilität und Gießbarkeit |
Autoteile, Hardware, elektrische Gehäuse |
Zamak 5 |
Zn 95%, Al 4%, Cu 1% |
Höhere Festigkeit und Härte, gute Kriechstromfestigkeit |
Zahnräder, Hebel, kleine mechanische Komponenten |
Zamak 7 |
Zn 99,99%, Al 0,05%, Mg 0,01% |
Hervorragende Duktilität und Fließfähigkeit, hohe Reinheit |
Elektronische Steckverbinder, Präzisionskomponenten |
Zamak 2 |
Zn 94%, Al 4%, Cu 3% |
Höchste Festigkeit und Härte unter den Zamak-Legierungen |
Mechanische Hochleistungsteile, Werkzeuge |
ZA-8 |
Zn 92%, Al 8%, Cu 1% |
Hohe Festigkeit und Härte, gute Lagereigenschaften |
Lager, Buchsen, kleine Maschinenteile |
ZA-12 |
Zn 88%, Al 12%, Cu 1% |
Hohe Festigkeit, Härte, gute Gießbarkeit |
Strukturelle Teile, hochbelastete Komponenten |
ZA-27 |
Zn 73%, Al 27%, Cu 2% |
Höchste Festigkeit und Härte, geringere Dichte |
Heavy-Duty-Anwendungen, große Maschinenteile |
Grundlegende Konstruktionshinweise für Zinkdruckguss
Hier finden Sie einige wichtige Tipps, die Sie nutzen können, um den Zinkdruckguss effektiver und effizienter zu gestalten.
Design-Aspekt |
Grundlegende Tipps |
Vereinfachte Zeichnungen |
Entwurfswinkel |
Berücksichtigen Sie Schräglagen (normalerweise 1-3 Grad). |
|
Wanddicke |
Behalten Sie eine einheitliche Wandstärke bei (0,040-0,120 Zoll für Zink). |
|
Rippen |
Fügen Sie Rippen hinzu, um Bereiche zu verstärken, ohne die Gesamtdicke zu erhöhen. |
|
Filets |
Verwenden Sie Hohlkehlen anstelle von scharfen Ecken (Radius von 0,020 Zoll oder mehr). |
|
Unterschneidet |
Minimieren Sie Hinterschneidungen oder verwenden Sie, falls erforderlich, Gleitkerne. |
|
Chefs |
Entwerfen Sie Vorsprünge mit angemessener Höhe und Durchmesser (Verhältnis 1:1 bis 3:1). |
|
Löcher und Schlitze |
Design mit einheitlicher Größe und Abstand (Mindestdurchmesser von 0,040 Zoll). |
|
Texturierung |
Fügen Sie Texturen zu flachen Oberflächen hinzu, um die Ästhetik zu verbessern. |
|
Toleranzen |
Verwenden Sie realistische Toleranzen (±0,002 bis ±0,005 Zoll). |
|
Trennungslinie |
Positionieren Sie die Trennungslinie strategisch günstig. |
Anwendungen des Zinkdruckgießens
Wie andere Verfahren ist auch der Zinkdruckguss in verschiedenen Branchen weit verbreitet. Lassen Sie uns seine Anwendungen im Detail besprechen.
1. Autoindustrie
Der Zinkdruckguss findet in der Automobilbranche zahlreiche Anwendungen. Er wird für die Herstellung präziser und haltbarer Teile verwendet. Dazu können Vergaser gehören. Diese Vergaser erfordern eine hohe Maßgenauigkeit und Oberflächenbearbeitung. Zinkdruckguss ist hier die beste Wahl. Außerdem benötigen einige Bremsteile eine hohe Festigkeit und Zuverlässigkeit. In diesem Fall sind Zinkdruckgussteile eine gute Wahl. Darüber hinaus gibt es viele Anwendungen für Zinkdruckguss zur Herstellung von Teilen, die Belastungen und Verschleiß standhalten können.
2. Elektronikindustrie
Der Zinkdruckguss findet in der Elektronikindustrie Anwendung. Es hilft bei der Herstellung komplexer und detaillierter Teile. Diese Teile weisen eine ausgezeichnete elektrische Leitfähigkeit und Abschirmungseigenschaften auf. Außerdem haben Zinkdruckgussteile ein geringeres Gewicht. Daher bieten sie Festigkeit und Haltbarkeit. Außerdem erfordern elektrische Steckverbinder Präzision und gleichmäßige Formen. Hier passen Zinkdruckgussteile sehr gut. Er hilft auch bei der Wärmeableitung von elektronischen Bauteilen. Insgesamt erhöht es die Leistung und Langlebigkeit des Bauteils.
3. Konsumgüter
In diesem Bereich ist der Zinkdruckguss eine relativ kostengünstige Lösung. Er kann funktionalen Teilen ein ästhetisches Aussehen verleihen. Außerdem ist es sehr haltbar und leicht zu bedienen. Daher wird es häufig für die Herstellung großer Mengen mit individuellen Formen und Abmessungen verwendet. Sie wird für die Herstellung verschiedener Produkte verwendet. Dazu gehören in der Regel Gepäckstücke, Türen und Geräte. Der Grund dafür ist ihre Stärke und ästhetische Verarbeitung.
4. Industrielle Ausrüstung
Neben anderen Sektoren findet der Zinkdruckguss auch in der Industrie zahlreiche Anwendungen. Er wird zur Herstellung verschiedener Komponenten verwendet. Diese erfordern im Allgemeinen eine hohe Präzision und Festigkeit. Außerdem sind sie sehr widerstandsfähig gegen harte Umweltbedingungen. Das beste Beispiel sind Pumpenteile. Zinkdruckguss hilft bei der Herstellung dieser Teile. Dabei handelt es sich in der Regel um Gehäuse und Laufräder. Darüber hinaus wird dieses Verfahren auch häufig für die Herstellung von Ventilen, Maschinen und Geräten verwendet.
Was sind die Vorteile des Zinkdruckgießens?
Genau wie andere Verfahren bietet auch der Zinkdruckguss verschiedene Vorteile. Lassen Sie uns diese im Detail besprechen.
1. Präzision
Diese Technik bietet eine hochdimensionale Genauigkeit. Es ist in der Lage, komplexe Details herzustellen. Außerdem ist der Zinkdruckguss ideal für die Herstellung von Teilen, die enge Toleranzen erfordern. Seine Präzision beweist, dass das Endprodukt mit Sicherheit den Konstruktionsspezifikationen entsprechen wird. Der Zinkdruckguss trägt dazu bei, die umfangreichen Nachbearbeitungsprozesse nach dem Gießen und die maschinelle Bearbeitung zu reduzieren. Außerdem wird der Bedarf an Nachbearbeitung minimiert.
2. Stärke und Langlebigkeit
Beim Zinkdruckguss können verschiedene Legierungen verwendet werden. Diese Legierungen müssen ausgezeichnete mechanische Eigenschaften aufweisen. Dazu gehören eine gute Schlagzähigkeit und Zugfestigkeit. Außerdem machen sie Zinkdruckgussteile stark und haltbar. So kann das Teil erheblichen mechanischen Belastungen und Verschleiß besser standhalten. Aus diesem Grund wird Zinkdruckguss in vielen Bereichen eingesetzt, z. B. in der Automobilindustrie und in der Industrieausrüstung.
3. Oberflächengüte
Mit Zinkdruckguss lassen sich Teile mit glatten Oberflächen herstellen. Daher lassen sich Beschichtungen und Veredelungen sehr leicht durchführen. Darüber hinaus hat es eine inhärente Oberflächenqualität. Daher sind verschiedene Nachbearbeitungen nach dem Gießen möglich. Dazu gehören Lackieren, Pulverbeschichten und Galvanisieren. Der Zinkdruckguss garantiert also Ästhetik und Korrosionsbeständigkeit. Außerdem lassen sich damit hochpräzise Endprodukte herstellen.
4. Wirkungsgrad
Zinkdruckguss ist eine effiziente und zuverlässige Methode zur Herstellung von Metallteilen. Es hat hohe Produktionsraten bei minimaler Bearbeitung. Außerdem können große Mengen hergestellt werden. Sie eignen sich daher für die Herstellung von Großserien. Auf diese Weise lassen sich die Herstellungszeit und die Kosten senken.
5. Kostengünstig
Diese Technik ist im Vergleich zu anderen Druckgießverfahren sehr wirtschaftlich. Es ergibt sich eine glatte Oberfläche. Es sind also keine Nachbearbeitungen erforderlich. Allerdings sind die anfänglichen Kosten für den Zinkdruckguss recht hoch, d. h. die Kosten für die Werkzeugkonstruktion. Aber wenn es um die Massenproduktion geht, sinken die Kosten und es werden gleichmäßige Ergebnisse erzielt.
Was sind die Nachteile des Zinkdruckgießens?
Neben den Vorteilen hat der Zinkdruckguss auch einige Nachteile. Lassen Sie uns diese also hier besprechen.
1. Größenbeschränkungen
Der Zinkdruckguss eignet sich für kleine oder mittelgroße Produktionen. Wenn Sie versuchen, großformatige Teile herzustellen, dann bietet dieses Verfahren Einschränkungen. Das liegt in der Regel an den Druckgießmaschinen und den Formgrößen. Sie können also andere Alternativen finden, um die großen Teile herzustellen.
2. Hohe Anfangskosten
Wie wir bereits erwähnt haben, erfordert das Zinkdruckgussverfahren spezielle Konstruktionen und Werkzeuge. Es liegt also auf der Hand, dass dieses Verfahren teurer ist als andere Techniken. Das macht es für kleine Produktionen weniger nützlich. Es kann jedoch für die Herstellung großer Produktionsmengen mit gleichbleibenden Designs verwendet werden.
3. Wärmeleitfähigkeit
Zinklegierungen sind bessere Wärmeleiter als andere Metalle. Daher wird es schwierig, mit der Hitze während des Prozesses umzugehen. Daher muss die Form sorgfältig entworfen werden. Außerdem müssen Sie geeignete Kühlstrategien einbauen, um Defekte zu vermeiden.
Welche Alternativen gibt es für den Zinkdruckguss?
Wenn wir die Vor- und Nachteile des Zinkdruckgusses vergleichen, können wir verschiedene Alternativen ausprobieren, um die gewünschten Teile zu erhalten. Diese werden in der folgenden Tabelle erläutert.
Alternative |
Material |
Vorteile |
Benachteiligungen |
Anwendungen |
Aluminium-Legierungen |
Leichtes Gewicht, korrosionsbeständig |
Höherer Schmelzpunkt |
Automobilteile, Komponenten für die Luft- und Raumfahrt |
|
Magnesium-Legierungen |
Sehr leicht, gutes Verhältnis von Festigkeit zu Gewicht |
Teureres Material |
Unterhaltungselektronik, Automobilkomponenten |
|
Kunststoff-Spritzgießen |
Thermoplastische Kunststoffe |
Leicht, vielseitig |
Geringere Festigkeit und Haltbarkeit |
Konsumgüter, medizinische Geräte |
Sandgießen |
Verschiedene Metalle |
Gut für große Teile, geringere Werkzeugkosten |
Grobe Oberflächengüte, geringere Genauigkeit |
Motorblöcke, große Maschinenteile |
Feinguss |
Verschiedene Metalle |
Hohe Präzision, hervorragende Oberflächengüte |
Hohe Kosten, längere Produktionszeit |
Turbinenschaufeln, medizinische Implantate |
Pulvermetallurgie |
Metalle und Legierungen |
Hohe Präzision, minimaler Abfall |
Kleinere Teile, hohe Werkzeugkosten |
Zahnräder, Lager, Konstruktionsteile |
Stanzen |
Metalle |
Hohe Produktionsgeschwindigkeit, niedrige Kosten |
Flache oder einfache Formen, hohe Anschaffungskosten für Werkzeuge |
Automobilverkleidungen, elektronische Komponenten |
Schmieden |
Metalle |
Hohe Festigkeit, ausgezeichnete Haltbarkeit |
Einfachere Formen, höherer Materialabfall |
Automobil-, Luft- und Raumfahrtkomponenten |
Schlussfolgerung
Zusammenfassend lässt sich sagen, dass der Zinkdruckguss eine intelligente Technik zur Herstellung von Metallteilen ist. Es hat viele Anwendungen in vielen Branchen. Dabei wird das Zinkmetall geschmolzen und in einen Ofen eingespritzt. Danach wird es unter hohem Druck in den Formhohlraum eingeführt. Dann beginnt es, die Form der Gussform anzunehmen, und wird abgekühlt. Nach der Erstarrung wird das Zinkteil aus dem Formhohlraum ausgeworfen und geprüft, ob es beschnitten oder oberflächenbehandelt werden muss. Dies ist also ein recht einfacher Schritt. Dieses Verfahren wird in erster Linie zur Herstellung kleiner Teile und für große Produktionen verwendet. Daher ist es in vielen Branchen weit verbreitet.
Häufig gestellte Fragen
Q1. Wie können Sie Zinkdruckguss mit Aluminiumdruckguss vergleichen?
Nun, beide Zinkdruckguss und Aluminiumdruckgussteile beginnen mit dem Schmelzen des Metalls, das dann die Form der Gussform annimmt. Zinkdruckguss hat jedoch eine hohe Präzision und Oberflächengüte. Aluminiumdruckguss hingegen ist für leichtere Teile mit guter Korrosionsbeständigkeit geeignet.
Q2. Können Sie die Zinkdruckgussteile recyceln?
Absolut ja, Zinkdruckgussteile sind Wärmeleiter. Sie können also bei bestimmten Temperaturen leicht schmelzen. Sie sind also vollständig recycelbar und sehr gut für die Umwelt.
Q3. Welche Nachbearbeitungstechniken werden im Allgemeinen bei der Herstellung von Zinkdruckgussteilen eingesetzt?
Es gibt mehrere. Die gebräuchlichsten Nachbearbeitungstechniken sind maschinelle Bearbeitung, Beschichtung, Lackierung und Pulverbeschichtung.
Produkte Galerie
LED-Lampen-Kühlkörper-Komponenten, Schiffskomponenten, architektonische Hardware-Komponenten, Autokomponenten, Maschinenbau-Komponenten, Automobilteile, LED-Beleuchtungsgehäuse und -teile, Fenster- und Tür-Hardware, Sportgeräte-Komponenten, Automobil-Komponenten, Elektrowerkzeug-Teile.
Über uns
Das 1999 gegründete Unternehmen GC Precision Mold Co. ltd (Was Hersteller von Aluminium-Druckguss (China) Limited ), ist heute einer der weltweit führenden Anbieter von qualitativ hochwertigen Druckgussteile aund Bearbeitung von Nichteisen-Metallerzeugnissen.
Unsere Produktionslinie umfasst unter anderem Aluminiumdruckguss und Zinkdruckguss, Bronze-Sandguss, Aluminium-KokillengussCNC-Präzisionsbearbeitung. Unsere Produkte wurden nach ISO 9001 anerkannt und zertifiziert, wir sind immer bereit, Ihr zuverlässiger Partner und Lieferant in China zu sein.
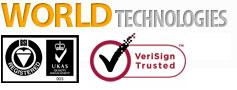
Startseite Lösung Unterstützung Links Karriere Blog Inhaltsverzeichnis
Urheberrecht © 2011-2014 GC Präzisionsform alle Rechte vorbehalten