Fabricante de fundición inyectada de zinc en China
OEM Contrato zinc fundición a presión servicio de fabricación con zamak 3, zamak 5...
Fundición inyectada de zinc, su proceso, aplicaciones y consejos de diseño
Cuando se trata de fabricar piezas metálicas, fundición inyectada de zinc es una opción muy demandada. Utiliza diferentes aleaciones para fabricar piezas complejas de zinc metal. Estas piezas tienen fuertes propiedades mecánicas. Además de su resistencia, estas piezas poseen unas propiedades mecánicas excepcionales. Por eso se utilizan mucho en diferentes aplicaciones. Aquí hablaremos de estas aplicaciones en detalle. Además, trataremos en detalle todo su proceso, consejos de diseño, ventajas, desventajas y alternativas.
¿Cómo definiría la fundición a presión de zinc?
Se trata de un proceso de fundición de aleaciones metálicas. En primer lugar, la aleación de zinc se funde. A continuación, una alta presión introduce el zinc fundido en una cavidad (molde de fundición a presión de metal). A continuación, el zinc adquiere la forma de una matriz. A continuación, el zinc se enfría y se expulsa de la matriz. Por lo tanto, esta técnica es la más adecuada para fabricar grandes volúmenes de piezas de aleaciones medias de zinc. A menudo se utiliza este proceso para producir piezas de gran precisión. Además, puede tratar diferentes aleaciones de zinc, como Zamak (zamak 3, zamak 5) y la serie ZA.
¿Cuáles son los procesos que intervienen en el troquelado del zinc?
A continuación se describen detalladamente las etapas de la fundición a presión de componentes de zinc.
1. Diseño y utillaje
La fundición a presión de zinc comienza con la fase de diseño. Esta fase puede incluir el diseño de la pieza de aleación de zinc y el diseño de las herramientas. Los ingenieros utilizan software inteligente, es decir, CAD o CAM, para diseñar las piezas y las herramientas. Añaden todos los pequeños detalles a los diseños para garantizar la precisión de la pieza de aleación de zinc. Consideran cuidadosamente los siguientes aspectos del diseño de piezas:
- Ángulo de tiro: Los ingenieros fijan los ángulos de desmoldeo entre 1 y 3 grados. Ayuda a retirar la pieza de aleación de zinc de la matriz.
- Espesor de pared: Mantienen un espesor de pared uniforme. Así, pueden evitar defectos y permitir un llenado adecuado.
- Costillas y filetes: Los ingenieros incorporan nervios y filetes a sus diseños. Las nervaduras contribuyen a reforzar el componente de aleación metálica. Los filetes ayudan a evitar esquinas afiladas para prevenir tensiones.
Además, en el diseño de utillaje, los ingenieros fabrican primero una matriz o molde. Los ingenieros suelen construirlo con aceros de alta calidad como H13, 8407 y 1.2344. Así pues, este troquel consta de dos mitades, a saber, el troquel de la tapa (mitad de fijación) y el troquel del expulsor (mitad móvil). Por lo tanto, hemos diseñado correctamente el troquel para alinearlo con los diseños CAD. Esto garantiza que la pieza final será exactamente igual que un troquel.
2. Fusión e inyección
Este paso incluye la fusión del material de zinc. Esto suele hacerse en un horno. Aquí, nos aseguramos de ajustar la temperatura entre 370°C y 430°C (700°F y 800°F). Este rango ayuda a mantener el zinc metálico en estado fundido. A continuación, el zinc fundido se inyecta en la máquina de fundición a presión. Esta máquina consta de un punzón, una cavidad para la matriz y una cámara de refrigeración. Tras inyectar la aleación fundida en la máquina, el punzón aplica una alta presión, forzándola a entrar en la cavidad de la matriz. Entonces, el zinc fundido adopta la forma de la matriz y alcanza todas sus dimensiones.
3. Enfriamiento y solidificación
Tras el proceso de inyección, el sistema de refrigeración enfría el zinc fundido. El molde de acero empieza a enfriar rápidamente el zinc fundido. Pero este enfriamiento tiene ciertos límites. Por eso, se suele sujetar mediante los canales de refrigeración. El refrigerante, o agua, se deja pasar a través de este canal. Ayudan a enfriar el zinc. Tras el enfriamiento, el zinc empieza a solidificarse. En esta fase, adquiere las dimensiones del molde. Además, el enfriamiento rápido ayuda a obtener estructuras de grano fino y gran resistencia. Además, este tiempo de enfriamiento depende del tamaño de la pieza y de su complejidad. Los diseños más sencillos se enfrían antes.
4. Expulsión y recorte
El último paso del proceso de fundición a presión de zinc es la expulsión y el recorte de la pieza de zinc. Tras la solidificación, la matriz se abre. A continuación, los pasadores expulsores empiezan a empujar la pieza fuera del molde. Este molde está diseñado de forma inteligente. Puede salir fácilmente de la cavidad de la matriz sin causar ningún daño. Además, si hay un exceso de material, es decir, flash, se adhiere alrededor de los bordes de la pieza de zinc. Es importante eliminarlo. Esto se consigue mediante el proceso de recorte. Este proceso puede utilizar diferentes operaciones mecánicas, como cortar, esmerilar o limar. Todos estos procesos tienen como resultado la producción de piezas finas.
5. Procesos secundarios
Algunas piezas se finalizan tras el recorte. Pero algunas necesitan procesos adicionales. Pueden conseguir un mejor aspecto y dimensiones específicas. Por ejemplo, taladrar agujeros, roscar o refinar superficies. Mientras que algunas piezas pueden necesitar un mejor aspecto y propiedades adicionales como resistencia a la corrosión y funcionamiento, pueden someterse al proceso de pintura. Además, algunas piezas de zinc pueden necesitar un acabado duradero. Pueden tolerar condiciones ambientales duras; pueden someterse a un proceso de recubrimiento en polvo.
Aleaciones de zinc más utilizadas en la fundición a presión
He aquí las diferentes aleaciones de zinc. Tienen diversas aplicaciones en distintos campos. Analicemos en detalle sus propiedades, composición y aplicaciones.
Aleación de Zn |
Composición |
Propiedades |
Aplicaciones típicas |
Zamak 3 |
Zn 96%, Al 4%, Mg 0,03% |
Buen equilibrio entre resistencia, ductilidad y moldeabilidad |
Piezas de automóvil, ferretería, carcasas eléctricas |
Zamak 5 |
Zn 95%, Al 4%, Cu 1% |
Mayor resistencia y dureza, buena resistencia a la fluencia |
Engranajes, palancas, pequeños componentes mecánicos |
Zamak 7 |
Zn 99,99%, Al 0,05%, Mg 0,01% |
Ductilidad y fluidez superiores, gran pureza |
Conectores electrónicos, componentes de precisión |
Zamak 2 |
Zn 94%, Al 4%, Cu 3% |
La mayor resistencia y dureza entre las aleaciones de Zamak |
Piezas mecánicas pesadas, herramientas |
ZA-8 |
Zn 92%, Al 8%, Cu 1% |
Alta resistencia y dureza, buenas propiedades portantes |
Rodamientos, bujes, piezas de maquinaria pequeña |
ZA-12 |
Zn 88%, Al 12%, Cu 1% |
Alta resistencia, dureza, buena colabilidad |
Piezas estructurales, componentes de alta carga |
ZA-27 |
Zn 73%, Al 27%, Cu 2% |
Mayor resistencia y dureza, menor densidad |
Aplicaciones pesadas, grandes piezas de maquinaria |
Consejos fundamentales de diseño para la fundición a presión de zinc
Estos son algunos consejos importantes que puede utilizar para que la fundición a presión de zinc sea más eficaz y eficiente.
Aspecto del diseño |
Consejos fundamentales |
Dibujos simplificados |
Ángulos de calado |
Incorpore ángulos de inclinación (normalmente de 1 a 3 grados). |
|
Espesor de pared |
Mantener un espesor de pared uniforme (0,040-0,120 pulgadas para el zinc). |
|
Costillas |
Añada nervaduras para reforzar zonas sin aumentar el grosor total. |
|
Filetes |
Utilice filetes en lugar de esquinas afiladas (radio de 0,020 pulgadas o más). |
|
Socava |
Reduzca al mínimo los destalonamientos o utilice núcleos deslizantes si es necesario. |
|
Jefes |
Diseñar los resaltes con la altura y el diámetro adecuados (relación 1:1 a 3:1). |
|
Agujeros y ranuras |
Diseño con tamaño y espaciado coherentes (diámetro mínimo de 0,040 pulgadas). |
|
Texturización |
Añada texturas a superficies planas para mejorar la estética. |
|
Tolerancias |
Utilice tolerancias realistas (de ±0,002 a ±0,005 pulgadas). |
|
Línea de separación |
Coloque la línea de separación estratégicamente. |
Aplicaciones de la fundición a presión de zinc
Al igual que otros procesos, la fundición a presión de zinc también se utiliza ampliamente en diferentes industrias. Analicemos sus aplicaciones en detalle.
1. Industria del automóvil
La fundición a presión de zinc tiene muchas aplicaciones en el sector de la automoción. Se utiliza para fabricar piezas precisas y duraderas. Entre ellas se encuentran los carburadores. Estos carburadores necesitan una gran precisión dimensional y acabado superficial. La fundición a presión de zinc es la mejor opción. Además, algunas piezas de freno necesitan una gran resistencia y fiabilidad. En este caso, la fundición a presión de zinc es una buena opción. Además, la fundición a presión de zinc tiene muchas aplicaciones para fabricar piezas que puedan soportar la tensión y el desgaste.
2. Industria electrónica
La fundición a presión de zinc ha encontrado aplicaciones en la industria electrónica. Ayuda a fabricar piezas complejas y detalladas. Estas piezas presentan una excelente conductividad eléctrica y propiedades de apantallamiento. Además, las piezas de fundición a presión de zinc son más ligeras. Por lo tanto, proporcionan resistencia y durabilidad. Por otra parte, los conectores eléctricos exigen precisión y formas consistentes. En este caso, las piezas de fundición a presión de zinc encajan muy bien. También ayudan a disipar el calor de los componentes electrónicos. En general, aumenta el rendimiento y la longevidad del componente.
3. Bienes de consumo
En este sector, la fundición a presión de zinc es una solución relativamente rentable. Puede añadir estética a las piezas funcionales. Además, es bastante duradera y fácil de manejar. Por eso se utiliza mucho para fabricar grandes cantidades con formas y dimensiones personalizadas. Se utiliza para fabricar distintos productos. Suelen ser maletas, puertas y electrodomésticos. Se debe a su resistencia y acabado estético.
4. Equipamiento industrial
Además de otros sectores, la fundición a presión de zinc tiene muchas aplicaciones en sectores industriales. Se utiliza para fabricar diferentes componentes. Éstos suelen necesitar gran precisión y resistencia. Además, tienen una gran resistencia a las duras condiciones ambientales. El mejor ejemplo son los componentes de bombas. Las fundiciones a presión de zinc ayudan a fabricar estas piezas. Suelen ser carcasas e impulsores. Además, este proceso también se utiliza mucho para fabricar válvulas, maquinaria y equipos.
¿Cuáles son las ventajas de la fundición a presión de zinc?
Al igual que otros métodos, la fundición a presión de zinc también ofrece distintas ventajas. Analicémoslas en detalle.
1. Precisión
Esta técnica ofrece una gran precisión dimensional. Es capaz de producir detalles complejos. Además, la fundición a presión de zinc es ideal para fabricar piezas que requieren tolerancias estrechas. Su propia precisión demuestra que el producto final cumplirá sin duda las especificaciones del diseño. Ayudará a reducir los extensos procesos posteriores a la fundición y el mecanizado. Además, minimiza la necesidad de acabado.
2. Resistencia y durabilidad
La fundición a presión de zinc permite utilizar diversas aleaciones. Estas aleaciones necesitan excelentes propiedades mecánicas. Pueden incluir una buena resistencia al impacto y a la tracción. Además, esto hace que las piezas de fundición a presión de zinc sean fuertes y duraderas. Así, la pieza es más capaz de soportar tensiones mecánicas y desgastes importantes. Por eso, la fundición a presión de zinc se utiliza mucho en aplicaciones de automoción y equipos industriales.
3. Acabado superficial
La fundición a presión de zinc ayuda a fabricar piezas con superficies lisas. Por tanto, es muy fácil aplicar el chapado y el acabado. Además, tiene una calidad de superficie inherente. Por tanto, permite diferentes procesos posteriores a la fundición. Pueden incluir pintura, recubrimiento en polvo y galvanoplastia. Así, las piezas de fundición a presión de zinc garantizan el atractivo estético y la resistencia a la corrosión. Además, también produce productos finales de gran precisión.
4. Eficacia
La fundición a presión de zinc es un método eficaz y fiable de fabricar piezas metálicas. Ofrece altos índices de producción con un mecanizado mínimo. Además, puede fabricar grandes cantidades. Por tanto, son adecuadas para hacer series de producción de gran volumen. Así, disminuyen el tiempo y el coste de fabricación.
5. Rentable
Esta técnica es muy económica en comparación con otros métodos de fundición a presión. Proporciona un acabado liso. Por tanto, no hay necesidad de operaciones secundarias. Pero sí, el coste inicial de la fundición a presión de zinc es bastante elevado, es decir, el coste de diseño de las herramientas. Pero cuando se trata de producción en serie, el coste disminuye y da resultados consistentes.
¿Cuáles son los contras de la fundición a presión de zinc?
Al igual que las ventajas, la fundición a presión de zinc también tiene algunos inconvenientes. Así que vamos a discutirlos aquí.
1. Restricciones de tamaño
La fundición inyectada de zinc es adecuada para producciones pequeñas o medianas. Si se trata de fabricar piezas de gran tamaño, entonces este proceso ofrece limitaciones. Suele ocurrir debido a las máquinas de fundición a presión y al tamaño de los moldes. Por lo tanto, puede encontrar otras alternativas para fabricar piezas grandes.
2. Coste inicial elevado
Como hemos comentado antes, el método de fundición a presión de zinc necesita diseños y utillajes específicos. Por tanto, es obvio que tiene un coste más elevado que otras técnicas. Esto lo hace menos útil para pequeñas producciones. Sin embargo, puede utilizarse para fabricar grandes volúmenes de producción con diseños consistentes.
3. 3. Conductividad térmica
Las aleaciones de zinc son mejores conductores térmicos que otros metales. Por tanto, resulta difícil manejar el calor durante el proceso. Por tanto, hay que diseñar cuidadosamente el molde. Además, hay que añadir estrategias de refrigeración adecuadas para evitar cualquier defecto.
¿Cuáles son las alternativas disponibles para la fundición a presión de zinc?
Comparando las ventajas y los inconvenientes de la fundición inyectada de cinc, podemos probar a utilizar diferentes alternativas para obtener las piezas deseadas. Así, su explicación se encuentra en la siguiente tabla.
Alternativa |
Material |
Ventajas |
Desventajas |
Aplicaciones |
Aleaciones de aluminio |
Ligero, resistente a la corrosión |
Punto de fusión más alto |
Piezas de automóviles, componentes aeroespaciales |
|
Aleaciones de magnesio |
Muy ligero, buena relación resistencia-peso |
Material más caro |
Electrónica de consumo, componentes de automoción |
|
Moldeo por inyección de plásticos |
Termoplásticos |
Ligero y versátil |
Menor resistencia y durabilidad |
Bienes de consumo, productos sanitarios |
Fundición en arena |
Metales diversos |
Bueno para piezas grandes, menor coste de utillaje |
Acabado superficial rugoso, menor precisión |
Bloques de motor, piezas de grandes máquinas |
Fundición a la cera perdida |
Metales diversos |
Alta precisión, excelente acabado superficial |
Coste elevado, mayor tiempo de producción |
Álabes de turbina, implantes médicos |
Pulvimetalurgia |
Metales y aleaciones |
Alta precisión, mínimo desperdicio |
Piezas más pequeñas, costes de utillaje elevados |
Engranajes, rodamientos, piezas estructurales |
Estampación |
Metales |
Alta velocidad de producción, bajo coste |
Formas planas o simples, coste inicial de utillaje elevado |
Paneles de automoción, componentes electrónicos |
Forja |
Metales |
Alta resistencia, excelente durabilidad |
Formas más sencillas, mayor desperdicio de material |
Componentes aeroespaciales y de automoción |
Conclusión
En conclusión, la fundición a presión de zinc es una técnica inteligente para fabricar piezas metálicas. Tiene muchas aplicaciones en muchos sectores. En ella, el metal de zinc pasa a estado fundido y se inyecta en un horno. Después, se somete a alta presión y se introduce en la cavidad de la matriz. Entonces empieza a adquirir la forma del molde y se deja enfriar. Tras la solidificación, la pieza de zinc sale de la cavidad de la matriz y se comprueba si necesita recorte o acabado superficial. Se trata, pues, de un paso bastante sencillo. Se utiliza mucho para fabricar piezas pequeñas y para grandes producciones. Por lo tanto, se utiliza ampliamente en muchas industrias.
Preguntas frecuentes
Q1. ¿Cómo se puede comparar la fundición a presión de zinc con la de aluminio?
Bueno, ambos fundición inyectada de zinc Los componentes de fundición a presión de zinc y aluminio comienzan con la fundición del metal, que luego adquiere la forma del molde. Pero las piezas fundidas a presión de zinc tienen precisión y un acabado superficial. Por otro lado, las piezas fundidas a presión de aluminio son útiles para piezas más ligeras con buena resistencia a la corrosión.
Q2. ¿Se pueden reciclar las piezas de fundición inyectada de zinc?
Absolutamente Sí, las piezas de fundición inyectada de zinc son conductores térmicos. Por tanto, pueden fundirse fácilmente a determinadas temperaturas. Por lo tanto, son totalmente reciclables y muy buenas para el medio ambiente.
Q3. ¿Qué técnicas de postprocesado se utilizan generalmente para fabricar piezas de fundición inyectada de cinc?
Existen múltiples. Así, las técnicas de postprocesado más comunes son el mecanizado, el chapado, la pintura y el recubrimiento en polvo.
Galería de productos
Componentes de disipadores de calor de lámparas LED, componentes marinos, componentes de hardware arquitectónico, componentes de automóviles, componentes de ingeniería mecánica, piezas de automóviles, caja y piezas de iluminación LED, hardware de puertas y ventanas, componentes de equipos deportivos, componentes de automoción, piezas de herramientas eléctricas.
Quiénes somos
Fundada en 1999, GC Precision Mold Co. ltd (Was Fabricante de fundición a presión de aluminio (China) Limited ), se está convirtiendo en uno de los principales proveedores mundiales de piezas de fundición a presión ay mecanizado de productos metálicos no férreos.
Nuestra línea de producción incluye, entre otras, la fundición a presión de aluminio, la fundición a presión de cinc, fundición de bronce en arena, fundición de aluminio por gravedadmecanizado de precisión CNC. nuestros productos fueron reconocidos y certificados por la norma ISO 9001, siempre estamos dispuestos a ser su socio de confianza y proveedor en China.
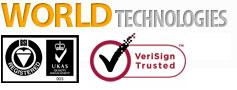
Inicio Solución Ayuda Enlaces Carreras profesionales Blog Mapa del sitio
Copyright © 2011-2014 Molde de precisión GC todos los derechos reservados