Fabricant de pièces moulées sous pression en zinc en Chine
OEM Service de fabrication de pièces moulées sous pression en zinc avec zamak 3, zamak 5...
Le moulage sous pression du zinc, son processus, ses applications et ses conseils de conception
Lorsqu'il s'agit de fabriquer des pièces métalliques, moulage sous pression du zinc est une option très demandée. Elle utilise différents alliages pour fabriquer des pièces complexes en zinc métal. Ces pièces ont de fortes propriétés mécaniques. Outre leur résistance, ces pièces possèdent des propriétés mécaniques exceptionnelles. C'est pourquoi elles sont largement utilisées dans différentes applications. Nous examinerons ici ces applications en détail. En outre, nous examinerons en détail l'ensemble du processus, les conseils de conception, les avantages, les inconvénients et les alternatives.
Comment définiriez-vous le moulage sous pression du zinc ?
Il s'agit d'un procédé de coulée d'alliage métallique. Tout d'abord, l'alliage de zinc fond jusqu'à l'état fondu. Ensuite, une pression élevée force le zinc fondu à pénétrer dans une cavité de la matrice (moule de coulée sous pression). Le zinc prend alors la forme d'une matrice. Le zinc se refroidit ensuite et est éjecté de la matrice. Cette technique est donc mieux adaptée à la fabrication de grands volumes de pièces en alliage de zinc moyen. Ce procédé est souvent utilisé pour produire des pièces très précises. En outre, il permet de traiter différents alliages de zinc, tels que le zamak (zamak 3, zamak 5) et la série ZA.
Quels sont les procédés utilisés pour le matriçage du zinc ?
Voici une description détaillée des étapes du moulage de composants en zinc sous pression.
1. Conception et outillage
Le moulage sous pression du zinc commence par la phase de conception. Cette phase peut inclure la conception de la pièce en alliage de zinc et la conception de l'outillage. Les ingénieurs utilisent des logiciels intelligents (CAO ou FAO) pour concevoir les pièces et les outils. Ils ajoutent tous les petits détails aux conceptions pour garantir la précision de la pièce en alliage de zinc. Ils prennent soigneusement en compte les aspects suivants de la conception des pièces :
- Angle de tirant d'eau : Les ingénieurs règlent les angles de dépouille entre 1 et 3 degrés. Cela permet de retirer la pièce en alliage de zinc de la matrice.
- Épaisseur de la paroi : Ils maintiennent une épaisseur de paroi uniforme. Ils peuvent donc prévenir les défauts et permettre un remplissage correct.
- Côtes et filets : Les ingénieurs intègrent des nervures et des filets dans leurs conceptions. Les nervures contribuent à renforcer le composant en alliage métallique. Les filets permettent d'éviter les angles vifs afin de prévenir les tensions.
En outre, lors de la conception de l'outillage, les ingénieurs commencent par fabriquer une matrice ou un moule. Les ingénieurs le construisent généralement à partir d'aciers de haute qualité comme le H13, le 8407 et le 1.2344. Cette matrice comprend donc deux moitiés, à savoir la matrice du couvercle (moitié fixe) et la matrice de l'éjecteur (moitié mobile). Par conséquent, nous avons correctement conçu la matrice pour l'aligner sur les conceptions de la CAO. Cela garantit que la pièce finale sera exactement comme une matrice.
2. Fusion et injection
Cette étape comprend la fusion du zinc. Cette opération s'effectue généralement dans un four. Ici, nous veillons à ajuster la température entre 700°F et 800°F (370°C et 430°C). Cette fourchette permet de maintenir le zinc à l'état fondu. Ensuite, le zinc en fusion peut être injecté dans la machine de coulée sous pression. Cette machine se compose d'un poinçon, d'une cavité de coulée et d'une chambre de refroidissement. Après avoir injecté l'alliage en fusion dans la machine, le poinçon applique une pression élevée qui le force à pénétrer dans la cavité de la filière. Le zinc en fusion prend alors la forme d'une matrice et en atteint toutes les dimensions.
3. Refroidissement et solidification
Après le processus d'injection, le zinc fondu est refroidi par le système de refroidissement. Le moule en acier commence à refroidir rapidement le zinc en fusion. Mais ce refroidissement a certaines limites. C'est pourquoi il est généralement fixé à l'aide de canaux de refroidissement. Le liquide de refroidissement, ou l'eau, est autorisé à passer à travers ce canal. Ils aident à refroidir le zinc. Après refroidissement, le zinc commence à se solidifier. À ce stade, il prend les dimensions du moule. En outre, un refroidissement rapide permet d'obtenir des structures à grains fins très résistantes. En outre, le temps de refroidissement dépend de la taille et de la complexité de la pièce. Les conceptions plus simples se refroidissent plus tôt.
4. Ejection et parage
L'étape finale du processus de moulage sous pression du zinc est l'éjection et l'ébarbage de la pièce en zinc. Après la solidification, le moule s'ouvre. Les broches d'éjection commencent alors à pousser la pièce hors du moule. Ce moule est conçu de manière intelligente. Il peut facilement sortir de la cavité du moule sans causer de dommages. En outre, s'il y a un excès de matière, c'est-à-dire une bavure, celle-ci se fixe sur les bords de la pièce en zinc. Il est important de l'enlever. Le processus d'ébarbage permet d'y parvenir. Ce processus peut faire appel à différentes opérations mécaniques, telles que le découpage, le meulage ou le limage. Tous ces procédés permettent de produire des pièces fines.
5. Processus secondaires
Certaines pièces sont finalisées après l'ébarbage. Mais certaines d'entre elles nécessitent des traitements supplémentaires. Elles peuvent obtenir un meilleur aspect et des dimensions spécifiques. Par exemple, le perçage de trous, le filetage ou l'affinage des surfaces. Si certaines pièces ont besoin d'un meilleur aspect et de propriétés supplémentaires telles que la résistance à la corrosion et le fonctionnement, elles peuvent être soumises au processus de peinture. En outre, certaines pièces en zinc peuvent nécessiter une finition durable. Elles peuvent tolérer des conditions environnementales difficiles ; elles peuvent être soumises à un processus de revêtement par poudre.
Alliages de zinc couramment utilisés pour le moulage sous pression
Voici les différents alliages de zinc. Ils ont des applications variées dans différents domaines. Examinons en détail leurs propriétés, leur composition et leurs applications.
Alliage de Zn |
Composition |
Propriétés |
Applications typiques |
Zamak 3 |
Zn 96%, Al 4%, Mg 0,03% |
Bon équilibre entre résistance, ductilité et coulabilité |
Pièces automobiles, quincaillerie, boîtiers électriques |
Zamak 5 |
Zn 95%, Al 4%, Cu 1% |
Résistance et dureté plus élevées, bonne résistance au fluage |
Engrenages, leviers, petits composants mécaniques |
Zamak 7 |
Zn 99,99%, Al 0,05%, Mg 0,01% |
ductilité et fluidité supérieures, grande pureté |
Connecteurs électroniques, composants de précision |
Zamak 2 |
Zn 94%, Al 4%, Cu 3% |
Résistance et dureté les plus élevées parmi les alliages de Zamak |
Pièces mécaniques lourdes, outils |
ZA-8 |
Zn 92%, Al 8%, Cu 1% |
Résistance et dureté élevées, bonnes propriétés de portance |
Roulements, coussinets, petites pièces de machines |
ZA-12 |
Zn 88%, Al 12%, Cu 1% |
Haute résistance, dureté, bonne coulabilité |
Pièces structurelles, composants à forte charge |
ZA-27 |
Zn 73%, Al 27%, Cu 2% |
Résistance et dureté supérieures, densité inférieure |
Applications lourdes, pièces de machines de grande taille |
Conseils fondamentaux de conception pour la coulée sous pression du zinc
Voici quelques conseils importants que vous pouvez utiliser pour rendre le moulage sous pression du zinc plus efficace.
Aspect de la conception |
Conseils fondamentaux |
Dessins simplifiés |
Angles d'ébauche |
Incorporer des angles de dépouille (généralement de 1 à 3 degrés). |
|
Épaisseur de la paroi |
Maintenir une épaisseur de paroi uniforme (0,040-0,120 pouces pour le zinc). |
|
Côtes |
Ajouter des nervures pour renforcer les zones sans augmenter l'épaisseur totale. |
|
Filets |
Utilisez des filets plutôt que des angles vifs (rayon de 0,020 pouce ou plus). |
|
Sous-coupes |
Minimiser les contre-dépouilles ou utiliser des carottes de glissement si nécessaire. |
|
Patrons |
Concevoir des bossages d'une hauteur et d'un diamètre appropriés (rapport de 1:1 à 3:1). |
|
Trous et fentes |
Conception avec une taille et un espacement cohérents (diamètre minimum de 0,040 pouce). |
|
Texture |
Ajouter des textures aux surfaces planes pour améliorer l'esthétique. |
|
Tolérances |
Utilisez des tolérances réalistes (±0,002 à ±0,005 pouces). |
|
Ligne de séparation |
Placez la ligne de démarcation de manière stratégique. |
Applications du moulage sous pression du zinc
Comme d'autres procédés, le moulage sous pression du zinc est également largement utilisé dans différentes industries. Examinons ses applications en détail.
1. L'industrie automobile
Le moulage sous pression du zinc a de nombreuses applications dans le secteur automobile. Elle permet de fabriquer des pièces précises et durables. Il peut s'agir de carburateurs. Ces carburateurs ont besoin d'une grande précision dimensionnelle et d'une finition de surface. Le moulage sous pression du zinc est la meilleure option. Par ailleurs, certaines pièces de frein nécessitent une résistance et une fiabilité élevées. Dans ce cas, le zinc moulé sous pression est une bonne option. En outre, le moulage sous pression du zinc a de nombreuses applications pour la fabrication de pièces capables de résister au stress et à l'usure.
2. Industrie électronique
Le moulage sous pression du zinc a trouvé des applications dans l'industrie électronique. Il permet de fabriquer des pièces complexes et détaillées. Ces pièces présentent d'excellentes propriétés de conductivité électrique et de blindage. En outre, les pièces en zinc moulées sous pression sont plus légères. Ils sont donc plus résistants et plus durables. En outre, les connecteurs électriques exigent une précision et des formes constantes. Dans ce cas, les pièces en zinc moulé sous pression conviennent parfaitement. Elles contribuent également à dissiper la chaleur des composants électroniques. Dans l'ensemble, elles augmentent les performances et la longévité du composant.
3. Biens de consommation
Dans ce secteur, le moulage sous pression du zinc est une solution relativement rentable. Elle permet d'ajouter de l'esthétique à des pièces fonctionnelles. En outre, il est assez durable et facile à utiliser. Elle est donc largement utilisée pour produire des quantités importantes avec des formes et des dimensions personnalisées. Il est utilisé pour fabriquer différents produits. Il s'agit généralement de bagages, de portes et d'appareils électroménagers. Cela s'explique par leur solidité et leur finition esthétique.
4. Équipement industriel
Outre d'autres secteurs, le moulage sous pression du zinc a de nombreuses applications dans les secteurs industriels. Elle est utilisée pour fabriquer différents composants. Ceux-ci nécessitent généralement une grande précision et une grande solidité. En outre, ils présentent une grande résistance aux conditions environnementales difficiles. Le meilleur exemple est celui des composants de pompes. Les pièces moulées sous pression en zinc permettent de fabriquer ces pièces. Il s'agit généralement de boîtiers et de roues. En outre, ce procédé est largement utilisé pour fabriquer des vannes, des machines et des équipements.
Quels sont les avantages du moulage sous pression du zinc ?
Tout comme les autres méthodes, le moulage sous pression du zinc offre également différents avantages. Examinons-les en détail.
1. Précision
Cette technique offre une grande précision dimensionnelle. Elle permet de produire des détails complexes. En outre, le moulage sous pression du zinc est idéal pour la fabrication de pièces nécessitant des tolérances serrées. Sa précision prouve que le produit final répondra certainement aux spécifications de la conception. Elle permet de réduire les nombreux processus de post-coulée et d'usinage. En outre, elle minimise également le besoin de finition.
2. Solidité et durabilité
Le moulage sous pression du zinc permet d'utiliser différents alliages. Ces alliages doivent avoir d'excellentes propriétés mécaniques. Elles peuvent inclure une bonne résistance aux chocs et à la traction. En outre, les pièces en zinc moulé sous pression sont solides et durables. Ainsi, la pièce devient plus apte à supporter des contraintes mécaniques et une usure importantes. C'est pourquoi le zinc moulé sous pression est largement utilisé dans des applications telles que l'automobile et l'équipement industriel.
3. Finition de la surface
Le moulage sous pression du zinc permet de réaliser des pièces aux surfaces lisses. Il est donc très facile d'appliquer le placage et la finition. En outre, il présente une qualité de surface inhérente. Il permet donc différents processus de post-coulée. Il peut s'agir de peinture, de revêtement en poudre et de galvanoplastie. Ainsi, les pièces moulées en zinc sous pression garantissent un aspect esthétique et une résistance à la corrosion. En outre, il permet de fabriquer des produits finis d'une grande précision.
4. L'efficacité
Le moulage sous pression du zinc est un moyen efficace et fiable de fabriquer des pièces métalliques. Elle offre des taux de production élevés et ne nécessite qu'un minimum d'usinage. En outre, elle permet de produire de grandes quantités. Elle est donc adaptée à la production de grandes séries. Elle permet donc de réduire le temps et le coût de fabrication.
5. Rentabilité
Cette technique est très économique par rapport aux autres méthodes de moulage sous pression. Elle permet d'obtenir une finition lisse. Il n'est donc pas nécessaire de procéder à des opérations secondaires. Mais il est vrai que le coût initial du moulage sous pression du zinc est assez élevé, c'est-à-dire le coût de conception de l'outillage. Mais lorsqu'il s'agit d'une production en série, le coût diminue et donne des résultats constants.
Quels sont les inconvénients du moulage sous pression du zinc ?
Tout comme les avantages, le moulage sous pression du zinc présente également certains inconvénients. Nous allons donc les examiner ici.
1. Contraintes de taille
Le moulage sous pression du zinc convient aux petites et moyennes productions. Si vous essayez de fabriquer des pièces de grande taille, ce procédé présente alors des limites. Cela est généralement dû à la taille des machines de coulée sous pression et des moules. Vous pouvez donc trouver d'autres solutions pour fabriquer des pièces de grande taille.
2. Coût initial élevé
Comme nous l'avons vu précédemment, la méthode de coulée sous pression du zinc nécessite des conceptions et un outillage spécifiques. Il est donc évident que son coût est plus élevé que celui des autres techniques. Elle est donc moins utile pour les petites productions. Toutefois, elle peut être utilisée pour produire des volumes de production importants avec des conceptions cohérentes.
3. Conductivité thermique
Les alliages de zinc sont de meilleurs conducteurs thermiques que les autres métaux. Il devient donc difficile de gérer la chaleur au cours du processus. Il faut donc concevoir le moule avec soin. En outre, vous devez également ajouter des stratégies de refroidissement appropriées afin d'éviter tout défaut.
Quelles sont les alternatives disponibles pour le moulage sous pression du zinc ?
En comparant les avantages et les inconvénients du moulage sous pression du zinc, nous pouvons essayer d'utiliser différentes alternatives pour obtenir les pièces souhaitées. Leur explication figure dans le tableau ci-dessous.
Alternative |
Matériau |
Avantages |
Inconvénients |
Applications |
Alliages d'aluminium |
Léger, résistant à la corrosion |
Point de fusion plus élevé |
Pièces automobiles, composants aérospatiaux |
|
Alliages de magnésium |
Très léger, bon rapport résistance/poids |
Matériau plus cher |
Électronique grand public, composants automobiles |
|
Moulage par injection de plastique |
Thermoplastiques |
Léger, polyvalent |
Résistance et durabilité moindres |
Biens de consommation, dispositifs médicaux |
Moulage au sable |
Métaux divers |
Bon pour les grandes pièces, coût d'outillage réduit |
Finition de surface grossière, précision moindre |
Blocs moteurs, pièces de grandes machines |
Moulage à la cire perdue |
Métaux divers |
Haute précision, excellente finition de surface |
Coût élevé, temps de production plus long |
Aubes de turbines, implants médicaux |
Métallurgie des poudres |
Métaux et alliages |
Haute précision, déchets minimes |
Pièces plus petites, coûts d'outillage élevés |
Engrenages, roulements, pièces structurelles |
Estampillage |
Métaux |
Production à grande vitesse, faible coût |
Formes plates ou simples, coût initial d'outillage élevé |
Panneaux automobiles, composants électroniques |
Forgeage |
Métaux |
Haute résistance, excellente durabilité |
Formes plus simples, déchets de matériaux plus importants |
Composants automobiles et aérospatiaux |
Conclusion
En conclusion, le moulage sous pression du zinc est une technique intelligente de fabrication de pièces métalliques. Elle a de nombreuses applications dans de nombreuses industries. Ici, le zinc devient un métal en fusion et est injecté dans un four. Il subit ensuite une forte pression et est inséré dans la cavité de la matrice. Il commence alors à prendre la forme du moule et on le laisse refroidir. Après solidification, la pièce en zinc est éjectée de la cavité du moule et l'on vérifie si elle a besoin d'être ébarbée ou de subir une finition de surface. Il s'agit donc d'une étape assez simple. Elle est utilisée de manière significative pour fabriquer de petites pièces et répondre à de grandes productions. Elle est donc largement utilisée dans de nombreuses industries.
Questions fréquemment posées
Q1. Comment pouvez-vous comparer le moulage sous pression du zinc avec le moulage sous pression de l'aluminium ?
Eh bien, les deux moulage sous pression du zinc et les pièces moulées sous pression en aluminium commencent par la fusion du métal, qui prend ensuite la forme du moule. Les pièces moulées sous pression en zinc sont toutefois précises et présentent une finition de surface. En revanche, les pièces moulées sous pression en aluminium sont utiles pour les pièces plus légères présentant une bonne résistance à la corrosion.
Q2. Pouvez-vous recycler les pièces en zinc moulé sous pression ?
Oui, les pièces en zinc moulé sous pression sont des conducteurs thermiques. Elles peuvent donc facilement fondre à certaines températures. Elles sont donc entièrement recyclables et très bonnes pour l'environnement.
Q3. Quelles sont les techniques de post-traitement généralement utilisées pour fabriquer des pièces en zinc moulé sous pression ?
Il en existe plusieurs. Ainsi, les techniques de post-traitement les plus courantes sont l'usinage, le placage, la peinture et le revêtement par poudre.
Galerie des produits
Composants de dissipateur thermique de lampe à LED, composants marins, composants de quincaillerie architecturale, composants automobiles, composants de génie mécanique, pièces automobiles, boîtiers et pièces d'éclairage à LED, quincaillerie pour portes et fenêtres, composants d'équipement sportif, composants automobiles, pièces d'outils électriques.
À propos de nous
Fondée en 1999, GC Precision Mold Co. ltd (Was Fabricant de pièces moulées sous pression en aluminium (Chine) Limited ), est en train de devenir l'un des principaux fournisseurs mondiaux de produits de haute qualité. pièces moulées sous pression aet l'usinage de produits en métaux non ferreux.
Notre ligne de production comprend, entre autres, le moulage sous pression de l'aluminium, le moulage sous pression du zinc, coulée de bronze au sable, moulage par gravité de l'aluminiumNos produits ont été reconnus et certifiés par la norme ISO 9001. Nous sommes toujours prêts à être votre partenaire et fournisseur de confiance en Chine.
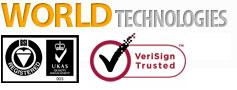
Accueil Solution Soutien Liens Carrières Blog Plan du site
Copyright © 2011-2014 GC Precision Mold tous droits réservés