Çin'de Çinko Basınçlı Döküm Üreticisi
Zamak 3, zamak 5 ile OEM Sözleşmeli çinko döküm imalat hizmeti ...
Çinko Basınçlı Döküm, Süreci, Uygulamaları ve Tasarım İpuçları
Metal parçaların üretimi söz konusu olduğunda, çi̇nko döküm parçası yüksek talep gören bir seçenektir. Karmaşık çinko metal parçalar yapmak için farklı alaşımlar kullanır. Bu parçalar güçlü mekanik özelliklere sahiptir. Güçlerine ek olarak, bu parçalar olağanüstü mekanik özelliklere sahiptir. Bu nedenle farklı uygulamalarda yaygın olarak kullanılırlar. Burada, bu uygulamaları ayrıntılı olarak tartışacağız. Ayrıca, tüm süreci, tasarım ipuçlarını, avantajlarını, dezavantajlarını ve alternatiflerini ayrıntılı olarak tartışacağız.
Çinko basınçlı dökümü nasıl tanımlarsınız?
Bir metal alaşım döküm işlemidir. İlk olarak, çinko alaşımı eriyerek erimiş hale gelir. Daha sonra, yüksek basınç erimiş çinkoyu bir kalıp boşluğuna (metal döküm kalıbı) zorlar. Daha sonra çinko bir kalıp şeklini alır. Çinko daha sonra soğur ve kalıptan dışarı atılır. Bu nedenle, bu teknik büyük hacimli orta çinko alaşımlı parçalar yapmak için en uygun yöntemdir. İnsanlar bu işlemi genellikle son derece hassas parçalar üretmek için kullanır. Ayrıca, Zamak (zamak 3, zamak 5) ve ZA serisi gibi farklı çinko alaşımlarıyla da başa çıkabilir.
Çinko kalıp kaplamada yer alan süreçler nelerdir?
İşte çinko döküm bileşenlerinde yer alan adımların ayrıntılı bir açıklaması.
1. Tasarım ve kalıplama
Çinko basınçlı döküm tasarım aşaması ile başlar. Bu aşama çinko alaşımlı parça tasarımı ve takım tasarımını içerebilir. Mühendisler parçaları ve takımları tasarlamak için CAD veya CAM gibi akıllı yazılımlar kullanır. Çinko alaşımlı parçanın hassasiyetini sağlamak için tasarımlara tüm küçük ayrıntıları eklerler. Parça tasarımında aşağıdaki hususları dikkatle göz önünde bulundururlar:
- Taslak Açısı: Mühendisler çekim açılarını 1-3 derece arasında ayarlar. Çinko alaşımlı parçanın kalıptan çıkarılmasına yardımcı olur.
- Duvar Kalınlığı: Düzgün bir duvar kalınlığı sağlarlar. Böylece kusurları önleyebilir ve düzgün doluma izin verebilirler.
- Pirzola ve Fileto: Mühendisler tasarımlarına nervür ve filetoları dahil ederler. Kaburgalar metal alaşımlı bileşenin güçlenmesine katkıda bulunur. Dolgular, gerilimi önlemek için keskin köşelerden kaçınmaya yardımcı olur.
Ayrıca, takım tasarımında, mühendisler önce bir kalıp veya kalıp yaparlar. Mühendisler bunu genellikle H13, 8407 ve 1.2344 gibi yüksek kaliteli çeliklerden yaparlar. Dolayısıyla, bu kalıp iki yarıdan oluşur, yani kapak kalıbı (sabitleme yarısı) ve ejektör kalıbı (hareketli yarı). Bu nedenle, kalıbı CAD tasarımlarıyla uyumlu olacak şekilde uygun şekilde tasarladık. Bu, nihai parçanın tam olarak bir kalıp gibi olacağını garanti eder.
2. Eritme ve Enjeksiyon
Bu adım çinko malzemenin eritilmesini içerir. Bu işlem genellikle bir fırında yapılır. Burada, sıcaklığı 700°F ile 800°F (370°C ile 430°C) arasında ayarladığımızdan emin oluruz. Bu aralık çinko metalini erimiş halde tutmaya yardımcı olur. Bundan sonra, erimiş çinkonun kalıp döküm makinesine enjekte edilmesine izin verilir. Bu makine bir zımba, bir kalıp boşluğu ve bir soğutma odasından oluşur. Erimiş alaşım makineye enjekte edildikten sonra, zımba yüksek basınç uygulayarak onu kalıp boşluğuna zorlar. Ardından erimiş çinko bir kalıp şeklini alır ve tüm boyutlarına ulaşır.
3. Soğutma ve katılaştırma
Enjeksiyon işleminden sonra, erimiş çinko soğutma sistemi tarafından soğutulur. Çelik kalıp erimiş çinkoyu hızla soğutmaya başlar. Ancak bu soğutmanın belirli sınırları vardır. Bu yüzden genellikle soğutma kanalları kullanılarak sabitlenir. Soğutma sıvısının veya suyun bu kanaldan geçmesine izin verilir. Çinkonun soğumasına yardımcı olurlar. Soğuduktan sonra çinko katılaşmaya başlar. Bu aşamada kalıp ölçülerini alır. Bunun yanı sıra hızlı soğutma, yüksek mukavemete sahip ince taneli yapılar elde edilmesine yardımcı olur. Ek olarak, bu soğutma süresi parça boyutuna ve karmaşıklığına bağlıdır. Daha basit tasarımlar daha erken soğur.
4. Fırlatma ve Düzeltme
Çinko basınçlı döküm işleminin son adımı çinko parçanın çıkarılması ve kırpılmasıdır. Katılaşmadan sonra kalıp açılır. Ardından itici pimler parçayı kalıptan dışarı itmeye başlar. Bu kalıp akıllıca tasarlanmıştır. Herhangi bir hasara yol açmadan kalıp boşluğundan kolayca çıkabilir. Ek olarak, aşırı malzeme, yani flaş varsa, çinko parçanın kenarlarına yapışır. Bunu çıkarmak önemlidir. Kırpma işlemi bunu gerçekleştirir. Bu işlem kesme, taşlama veya eğeleme gibi farklı mekanik işlemler kullanabilir. Tüm bu işlemler ince parçaların üretimiyle sonuçlanır.
5. İkincil Süreçler
Bazı parçalar kırpıldıktan sonra son halini alır. Ancak birkaçının ek işlemlere ihtiyacı vardır. Daha iyi bir görünüm ve belirli boyutlar elde edebilirler. Örneğin, delik delme, diş açma veya yüzeyleri düzeltme. Bazı parçalar daha iyi bir görünüme ve korozyon direnci ve işlevsellik gibi ek özelliklere ihtiyaç duyabilirken, boyama işleminden geçebilirler. Ayrıca, bazı çinko parçaların dayanıklı finisaja ihtiyacı olabilir. Zorlu çevre koşullarını tolere edebilirler; toz kaplama işleminden geçebilirler.
Basınçlı Döküm için Yaygın Olarak Kullanılan Çinko Alaşımları
İşte farklı çinko alaşımları. Farklı alanlarda çeşitli uygulamaları vardır. Özelliklerini, bileşimlerini ve uygulamalarını ayrıntılı olarak tartışalım.
Zn alaşımı |
Kompozisyon |
Özellikler |
Tipik Uygulamalar |
Zamak 3 |
Zn 96%, Al 4%, Mg 0,03% |
İyi mukavemet, süneklik ve dökülebilirlik dengesi |
Otomotiv parçaları, donanım, elektrik muhafazaları |
Zamak 5 |
Zn 95%, Al 4%, Cu 1% |
Daha yüksek mukavemet ve sertlik, iyi sürünme direnci |
Dişliler, kollar, küçük mekanik bileşenler |
Zamak 7 |
Zn 99,99%, Al 0,05%, Mg 0,01% |
Üstün süneklik ve akışkanlık, yüksek saflık |
Elektronik konektörler, hassas bileşenler |
Zamak 2 |
Zn 94%, Al 4%, Cu 3% |
Zamak alaşımları arasında en yüksek mukavemet ve sertlik |
Ağır hizmet tipi mekanik parçalar, aletler |
ZA-8 |
Zn 92%, Al 8%, Cu 1% |
Yüksek mukavemet ve sertlik, iyi taşıma özellikleri |
Rulmanlar, burçlar, küçük makine parçaları |
ZA-12 |
Zn 88%, Al 12%, Cu 1% |
Yüksek mukavemet, sertlik, iyi dökülebilirlik |
Yapısal parçalar, yüksek yük bileşenleri |
ZA-27 |
Zn 73%, Al 27%, Cu 2% |
En yüksek mukavemet ve sertlik, daha düşük yoğunluk |
Ağır hizmet uygulamaları, büyük makine parçaları |
Çinko Basınçlı Döküm için Temel Tasarım İpuçları
İşte çinko dökümünü daha etkili ve verimli hale getirmek için kullanabileceğiniz bazı önemli ipuçları.
Tasarım Yönü |
Temel İpuçları |
Basitleştirilmiş Çizimler |
Taslak Açıları |
Çekim açılarını dahil edin (tipik olarak 1-3 derece). |
|
Duvar Kalınlığı |
Tek tip duvar kalınlığını koruyun (çinko için 0,040-0,120 inç). |
|
Kaburga |
Toplam kalınlığı artırmadan alanları güçlendirmek için nervür ekleyin. |
|
Fileto |
Keskin köşeler yerine filetolar kullanın (0,020 inç veya daha fazla yarıçap). |
|
Alt Kesimler |
Alt kesimleri en aza indirin veya gerekirse kayar karot kullanın. |
|
Patronlar |
Uygun yükseklik ve çapta (1:1 ila 3:1 oranında) başlıklar tasarlayın. |
|
Delikler ve Yuvalar |
Tutarlı boyut ve aralıklarla tasarlayın (minimum 0,040 inç çap). |
|
Dokulandırma |
Estetiği iyileştirmek için düz yüzeylere doku ekleyin. |
|
Toleranslar |
Gerçekçi toleranslar kullanın (±0,002 ila ±0,005 inç). |
|
Ayrılık Hattı |
Ayırma çizgisini stratejik olarak konumlandırın. |
Çinko kalıp döküm uygulamaları
Diğer prosesler gibi, çinko döküm de farklı endüstrilerde yaygın olarak kullanılmaktadır. Uygulamalarını ayrıntılı olarak tartışalım.
1. Otomotiv Endüstrisi
Çinko dökümün otomotiv sektöründe birçok uygulaması vardır. Hassas ve dayanıklı parçalar yapmak için kullanılır. Bunlar karbüratörleri içerebilir. Bu karbüratörlerin yüksek boyutlu hassasiyete ve yüzey işlemeye ihtiyacı vardır. Çinko basınçlı döküm, kullanılabilecek en iyi seçenektir. Bunun yanı sıra, bazı fren parçaları yüksek mukavemet ve güvenilirliğe ihtiyaç duyar. Bu durumda, çinko basınçlı dökümler iyi seçeneklerdir. Ayrıca, çinko basınçlı dökümün stres ve aşınmayı yönetebilen parçalar yapmak için birçok uygulaması vardır.
2. Elektronik Endüstrisi
Çinko basınçlı döküm, elektronik endüstrisinde uygulama alanı bulmuştur. Karmaşık ve ayrıntılı parçaların yapılmasına yardımcı olur. Bu parçalar mükemmel elektrik iletkenliği ve ekranlama özellikleri gösterir. Bunun yanı sıra, çinko basınçlı dökümler ağırlık olarak daha hafiftir. Bu nedenle güç ve dayanıklılık sağlarlar. Ayrıca, elektrik konektörleri hassas ve tutarlı şekiller gerektirir. Burada, çinko dökümler çok iyi uyum sağlar. Ayrıca elektronik bileşenlerden gelen ısının dağıtılmasına da yardımcı olur. Genel olarak, bileşenin performansını ve uzun ömürlülüğünü artırır.
3. Tüketim Malları
Bu sektörde çinko basınçlı döküm nispeten uygun maliyetli bir çözümdür. İşlevsel parçalara estetik katabilir. Üstelik oldukça dayanıklıdır ve kullanımı kolaydır. Bu nedenle, özelleştirilmiş şekil ve boyutlara sahip toplu miktarların yapımında yaygın olarak kullanılır. Farklı ürünler yapmak için kullanılır. Genellikle bagajlar, kapılar ve aletleri içerirler. Bunun nedeni güçleri ve estetik kaplamalarıdır.
4. Endüstriyel Ekipmanlar
Diğer sektörlerin yanı sıra, çinko dökümün endüstriyel sektörlerde de birçok uygulaması vardır. Farklı bileşenler yapmak için kullanılır. Bunlar genellikle yüksek hassasiyet ve mukavemete ihtiyaç duyar. Ayrıca, zorlu çevre koşullarına karşı yüksek dirence sahiptirler. Buna en iyi örnek pompa bileşenleridir. Çinko kalıp dökümler bu parçaların yapılmasına yardımcı olur. Bunlar genellikle gövdeler ve pervanelerdir. Ayrıca, bu işlem valf, makine ve ekipman yapımında da yaygın olarak kullanılmaktadır.
Çinko dökümün artıları nelerdir?
Tıpkı diğer yöntemler gibi çinko basınçlı döküm de farklı avantajlar sunar. Bunları ayrıntılı olarak tartışalım.
1. Hassasiyet
Bu teknik yüksek boyutlu doğruluk sağlar. Karmaşık detaylar üretme kapasitesine sahiptir. Bunun yanı sıra, çinko döküm sıkı tolerans gerektiren parçaların yapımı için idealdir. Hassasiyeti, nihai ürünün tasarım özelliklerini kesinlikle karşılayacağını kanıtlar. Kapsamlı döküm sonrası işlemlerin ve talaşlı imalatın azaltılmasına yardımcı olacaktır. Bunun yanı sıra, finisaj ihtiyacını da en aza indirir.
2. Güç ve Dayanıklılık
Çinko basınçlı döküm çeşitli alaşım kullanımlarına izin verir. Bu alaşımlar mükemmel mekanik özelliklere ihtiyaç duyar. İyi darbe direnci ve gerilme mukavemeti içerebilirler. Bunun yanı sıra, çinko basınçlı döküm parçaları güçlü ve dayanıklı hale getirir. Böylece, parça önemli mekanik stres ve aşınmayı daha iyi taşıyabilir hale gelir. Bu nedenle çinko döküm, otomotiv ve endüstriyel ekipman gibi uygulamalarda yaygın olarak kullanılmaktadır.
3. Yüzey İşlemi
Çinko basınçlı döküm, pürüzsüz yüzeylere sahip parçaların üretilmesine yardımcı olur. Bu nedenle, kaplama ve son işlem uygulamak gerçekten kolaydır. Bununla birlikte, doğal bir yüzey kalitesine sahiptir. Bu nedenle, farklı döküm sonrası işlemlere izin verir. Bunlar boyama, toz kaplama ve elektro kaplamayı içerebilir. Böylece çinko kalıp dökümler estetik çekiciliği ve korozyon direncini garanti eder. Bunun yanı sıra, son derece hassas nihai ürünler de üretir.
4. Verimlilik
Çinko basınçlı döküm, metal parçalar üretmenin etkili ve güvenilir bir yoludur. Minimum işleme gerektiren yüksek üretim oranlarına sahiptir. Dahası, büyük miktarlarda üretim yapabilir. Bu nedenle, yüksek hacimli üretim çalışmaları yapmak için uygundurlar. Böylece üretim süresini ve maliyetini azaltırlar.
5. Uygun Maliyetli
Bu teknik diğer kalıp döküm yöntemlerine kıyasla çok ekonomiktir. Kendine pürüzsüz bir yüzey verir. Dolayısıyla, ikincil işlemlere gerek yoktur. Ancak evet, çinko basınçlı dökümün başlangıç maliyeti, yani kalıp tasarım maliyeti oldukça yüksektir. Ancak toplu üretim söz konusu olduğunda, maliyet düşer ve tutarlı sonuçlar verir.
Çinko dökümün dezavantajları nelerdir?
Avantajları olduğu gibi, çinko dökümün bazı dezavantajları da vardır. Şimdi bunları burada tartışalım.
1. Boyut Kısıtlamaları
Çinko döküm küçük veya orta ölçekli üretimler için uygundur. Büyük boyutlu parçalar yapmaya çalışırsanız, bu işlem sınırlamalar sunar. Bunun nedeni genellikle basınçlı döküm makineleri ve kalıp boyutlarıdır. Dolayısıyla, büyük parçaları yapmak için başka alternatifler bulabilirsiniz.
2. Yüksek Başlangıç Maliyeti
Daha önce de bahsettiğimiz gibi, çinko döküm yöntemi özel tasarımlara ve takımlara ihtiyaç duyar. Dolayısıyla, diğer tekniklerden daha yüksek bir maliyete sahip olduğu açıktır. Bu da onu küçük üretimler için daha az kullanışlı hale getirmektedir. Bununla birlikte, bu yöntem tutarlı tasarımlarla büyük üretim hacimleri üretmek için kullanılabilir.
3. Termal iletkenlik
Çinko alaşımları diğer metallere göre daha iyi ısı iletkenleridir. Bu nedenle, işlem sırasında ısıyla başa çıkmak zorlaşır. Bu yüzden kalıbı dikkatlice tasarlamanız gerekir. Bunun yanı sıra, herhangi bir kusurdan kaçınmak için uygun soğutma stratejileri de eklemeniz gerekir.
Çinko basınçlı döküm için mevcut alternatifler nelerdir?
Çinko dökümün hem faydalarını hem de dezavantajlarını karşılaştırarak, istenen parçaları elde etmek için farklı alternatifler kullanmayı deneyebiliriz. Bunların açıklamaları aşağıdaki tabloda yer almaktadır.
Alternatif |
Malzeme |
Avantajlar |
Dezavantajlar |
Uygulamalar |
Alüminyum alaşımlar |
Hafif, korozyona dayanıklı |
Daha yüksek erime noktası |
Otomotiv parçaları, havacılık ve uzay bileşenleri |
|
Magnezyum alaşımları |
Çok hafif, iyi güç/ağırlık oranı |
Daha pahalı malzeme |
Tüketici elektroniği, otomotiv bileşenleri |
|
Plastik Enjeksiyon Kalıplama |
Termoplastikler |
Hafif, çok yönlü |
Daha düşük güç ve dayanıklılık |
Tüketim malları, tıbbi cihazlar |
Kum Döküm |
Çeşitli metaller |
Büyük parçalar için iyi, daha düşük takım maliyeti |
Pürüzlü yüzey kalitesi, daha düşük hassasiyet |
Motor blokları, büyük makine parçaları |
Yatırım Döküm |
Çeşitli metaller |
Yüksek hassasiyet, mükemmel yüzey kalitesi |
Yüksek maliyet, daha uzun üretim süresi |
Türbin kanatları, tıbbi implantlar |
Toz Metalurjisi |
Metaller ve alaşımlar |
Yüksek hassasiyet, minimum atık |
Daha küçük parçalar, yüksek takım maliyetleri |
Dişliler, rulmanlar, yapısal parçalar |
Damgalama |
Metaller |
Yüksek hızlı üretim, düşük maliyet |
Düz veya basit şekiller, yüksek ilk takımlama maliyeti |
Otomotiv panelleri, elektronik bileşenler |
Dövme |
Metaller |
Yüksek mukavemet, mükemmel dayanıklılık |
Daha basit şekiller, daha yüksek malzeme israfı |
Otomotiv, havacılık ve uzay bileşenleri |
Sonuç
Sonuç olarak, çinko basınçlı döküm metal parçalar yapmak için akıllı bir tekniktir. Birçok sektörde birçok uygulaması vardır. Burada çinko metali erimiş bir hale dönüşür ve bir fırına enjekte edilir. Bundan sonra yüksek basınca maruz kalır ve kalıp boşluğuna yerleştirilir. Daha sonra kalıp şeklini almaya başlar ve soğumaya bırakılır. Katılaşmadan sonra, çinko parça kalıp boşluğundan dışarı çıkar ve düzeltme veya yüzey bitirme gerektirip gerektirmediğini kontrol eder. Yani, bu oldukça basit bir adımdır. Bu, küçük parçalar yapmak ve büyük üretimlere hitap etmek için önemli ölçüde kullanılır. Bu nedenle, birçok endüstride yaygın olarak kullanılmaktadır.
Sıkça Sorulan Sorular
Q1. Çinko basınçlı döküm ile alüminyum basınçlı dökümü nasıl karşılaştırabilirsiniz?
İkisi de çi̇nko döküm ve alüminyum basınçlı döküm bileşenleri metalin eritilmesiyle başlar ve ardından kalıbın şeklini alır. Ancak çinko basınçlı dökümler hassasiyete ve yüzey kaplamasına sahiptir. Öte yandan, alüminyum basınçlı dökümler iyi korozyon direncine sahip daha hafif parçalar için kullanışlıdır.
Q2. Çinko döküm parçaları geri dönüştürebilir misiniz?
Kesinlikle evet, çinko döküm parçalar termal iletkendir. Dolayısıyla, belirli sıcaklıklarda kolayca eriyebilirler. Bu nedenle tamamen geri dönüştürülebilirler ve çevre için son derece faydalıdırlar.
Q3. Çinko döküm parçalar yapmak için genellikle hangi işlem sonrası teknikler kullanılır?
Birden fazla var. Dolayısıyla, en yaygın son işlem teknikleri talaşlı imalat, kaplama, boyama ve toz kaplamadır.
Ürünler Galerisi
LED Lamba Isı Emici Bileşenleri, Denizcilik Bileşenleri, Mimari Donanım Bileşenleri, otomobil bileşenleri, Makine Mühendisliği Bileşenleri, Otomobil Parçaları, LED aydınlatma muhafazası ve parçaları, pencere ve kapı Donanımı, Spor Ekipmanları Bileşenleri, Otomotiv Bileşenleri, Elektrikli Alet Parçaları.
Hakkımızda
1999 yılında kurulan GC Precision Mold Co. ltd (Was Alüminyum döküm üreticisi (Çin) Limited), şu anda yüksek kaliteli ürünlerin önde gelen küresel tedarikçilerinden biri haline gelmektedir. döküm parçalari ave demir dışı metal ürünlerin işlenmesi.
Üretim hattımız, bunlarla sınırlı olmamak üzere alüminyum döküm, çinko döküm içerir, bronz kum döküm, alüminyum yerçekimi dökümÜrünlerimiz ISO 9001 tarafından tanındı ve sertifikalandırıldı, Çin'deki güvenilir ortağınız ve tedarikçiniz olmaya her zaman hazırız.
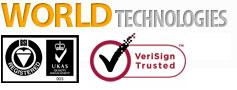
Ev Çözüm Destek Bağlantılar Kariyer Blog Site Haritası
Telif Hakkı © 2011-2014 GC Hassas Kalıp tüm hakları saklıdır