What is die casting mold/tooling?
Die casting mold, also known as die casting tooling, fills a sealed cavity with molten metal at high pressure and temperature. The metal is quickly cooled until the hardened portion becomes sufficiently rigid to be removed from the mold.
You must use high-quality tool steel, such as H13, DIN 1.2343, or 8407, to make the die casting mold. The cavity, core, and sliders must be heat-treated to the correct hardness, typically HRC 48-52. To ensure its longevity, it is also necessary to machine the mold base to precise standards.
In order to produce a high-quality casting part that meets customers’ required shape and design, the two die halves are placed in a die casting machine that is operated at the necessary temperatures and pressures. The customer’s requirements for part size and geometry features will directly affect the die casting tooling cost.
Choosing the right die casting tooling depends on various factors, such as the number of cavities, the quantity of cores or slides required, the weight of the die casting mold, the machining process, the surface finish requirements, and polishing and plating, among others. Creating a custom die-casting mold is a complex task.
When selecting die casting tooling, consider factors such as the number of cavities, cores, or slides required. Also, think about the mold weight, machining process, surface finish requirements, polishing, and plating. Each of these factors plays a role in the decision-making process. Creating a custom die-casting mould is a complex task.
Today most of die casting manufacturers are buying die casting molds from China die casting mold companies, becaues Chinese die casting mold factory can make high quality die casting tooling with fast lead time and high precision dies. if you are looking for aluminum die casting mold for your project, China die casting mold company will be one of your best place to go.
In this article, we will discuss die casting tooling and how the die casting mold manufacturer produces high-quality die casting components using the most economical production methods.
Die casting uses a variety of metals, such as zinc, magnesium, lead, copper, and aluminum (or aluminum). Each metal necessitates specific die requirements for the casting process. For instance, the Zamak 3, 5, and ZA series can utilize zinc. The A356, A380, ADC 12, AL6061, AL6063, and other series can also utilize aluminum.
The descriptions and settings provided in this article are generic due to these variations. Options are provided where feasible, but they should only be used as a basic reference. The customer and the die casting mold manufacturer should confer before making any final decisions.
A-PARTING LINE |
B-LEADER/GUIDE |
C- Casting part |
D- Mold CAVITY & CORE |
E-RUNNER & GATES |
F-COLD CHAMBER |
F1-SPRUE HOLE |
Surface where two die casting tooling halves |
Align the two die halds in the correct position when die cating mold closing |
Casting part customer required |
Casting medium/ Forming medium |
Feeding metal from |
Channel which metal |
Spure runners & gates |
G-CORE INSERTS |
H-Fixing/A Plate |
I-RETURN PIN |
J-EJECTOR PIN |
K-MOVING/B PLATE |
L-SUPPORT PLATE |
M- EJECTOR PLATES |
Small round pin or sqaure insert used to cast hole or deep ribs features |
Fixing/A plate that |
Ejector pin that push the ejector plate back |
Pin which release the cating from die |
B plate that contains and supports the core inserts. |
Supporting B plate and ejetor plate and clamping slots |
Fastens and pushes the |
N-SUPPORT PILLAR |
O-EJECTION GUIDING SYSTME |
P-CLAMPING SLOT |
||||
Features to keep the B plate stable during injection |
Guide system to lead the ejector pins |
Lots to fasten the die halves to machine |
Types of Die Casting Molds
There are several varieties of die-casting molds, each serving a specific requirement for the consumer. Typically, the type of die casting mold depends on the customer’s requirements. Below is a list of some common types of die-casting molds.
1. Prototyping die casting mold
Customers typically request prototypes to produce a small quantity of castings under production conditions. Before going into full production, they allow for extensive product testing and market exposure. Typically, new projects in the development stage utilize this method. This prototype die casting allows you to get high-quality parts without the need to pay for tooling costs.
A variety of prototype techniques can be utilized to simulate a die-cast component for subsequent die-cast manufacturing. These include CNC machining prototypes and sand casting, which includes the plaster mold process.
2. Rapid die casting tooling
Rapid die cast tooling involves creating dies and inserts more quickly than the traditional method. This process skips steps like rough machining, heat treatment, and finish machining. It allows for faster production of the necessary tools for die casting.
Quick die casting tools usually use pre-hardened steel for small amounts, from a few hundred to a thousand. For these small quantity requirements, we sometimes use investment casting or gravity casting.
3. Production Die casting mold
These are the most commonly used types of die-casting molds. Molds can vary from simple to complex, with different numbers of cavities and slides. High-grade tool steel (DIN 1.2343, DIN 1.2344, H13, 8407) forms the cavities, cores, insert, sliders, and a solid holder block, known as A plate and B plate, holds them in place. We have listed the types of die-casting molds below.
- Single-cavity die casting tooling: this tool produces one casting part at a time.
- Multiple-cavity die-casting mold: this mold produce more than one die casting part at a time.
- Family die casting tooling: this tool produces a number of different family die casting alloy parts in one cycle.
4. Trim Die casting tooling
Trim die casting tooling is a tool that removes runners, overflows, and flashes from casting components. Trim tooling refers to single- or multiple-cavity tools that have the same configuration as die casting tooling.
For alloy casting parts, the trim die can be simple or complex. Some have a basic open-and-close design, while others have multiple slides for the die casting process. Certain situations involve the use of multiple station trim die casting tools for subsequent trimming operations.
Trim die casting tooling needs careful design and high-quality materials to last. It’s just as important as die casting tools to ensure productivity and longevity. Conventional casting dies come in a variety of shapes.
Die-Casting Mold Structure and Consideration
The geometry and design of the die casting alloy part determine the complexity of die casting tooling. The small size and simple design of the casting part result in low costs for both the die casting tooling and production.
When you start a die casting project, you should consider the casting in terms of overall manufacturing costs. The die casting mold manufacturer will aid the customer in ascertaining the casting component’s design feasibility. They will also help with any additional steps that may be required, such as machining, finishing, or meeting specific tolerances.
The following factors determine castability and die casting tooling costs:
Do the ribs and walls have consistent thicknesses, or do they differ significantly? Will the design’s thin channels produce a tiny, standing steel insert in the die cavity? Are there any designs that necessitate extremely small inserts, which could be challenging to cast? Does the design have any sharp corners that encourage stress cracks?
Specifications for surface finish, secondary machining, and pressure tightness must be thoroughly considered in order to build high-quality production die casting tools correctly. In order to design the die-cast mould to minimize porosity in the areas of the casting that will be machined, it is necessary to thoroughly address these areas of the casting at the beginning.
There will be particular stages involved in completing the die’s cavities in order to meet the casting’s surface finish requirements. The customer should explain the final requirements of the die casting components in advance to the die casting manufacturer.
Die casting molds typically consist of four parts: the mold base, the forming cavity and core, the ejection systems, the cooling system, and the feeding system. Below are guides that explain the most common components found in a die casting mold.
Die casting Mold base
Die Casting Molds are made from many components. The mold base serves as a structural support that is used to hold all the other mold components together. We divide the mold base into two halves: the “moving half” and the “fixing half.” We refer to the splitting line as the tooling parting line.
The die-casting mold’s opening and closing during regular operation creates pinch hazards near the mold parting line. Given its danger, every worker must be aware of this pinch hazard.
Melt alloy may also spurt out through the die parting line if the die casting tooling does not completely close during injection. This could put anyone near the die-casting mold at risk of burns. Safety doors and shields typically guard this region.
Mold bases are typically made from S50C; sometimes the 1.2311 or P-20 will be used on A/B plates and ejector plates. in our China die casting mold company, we mostly use 1.2311 for A/B plate and the H13 or 8407 steel for the cavity and core, of course if you want other specially steel for your die casting mold, most of chinese die casting mold manufacturers can meet your requirement.
Die Casting Mold Slider
In order to cast undercut features in the cast part, fixed cores and core sliders are designed in the die casting mold. This will eliminate the necessity for some secondary machining of the cast part. Core sliders can be moved by different types of motion, like collet or cam motions. Most of the time, angle pins and hydraulic cylinders are used.
The angle pin is drived by the die casting mold opening and closing. Some of its benefits include the absence of hydraulics and limit valves, as well as its generally more cost-effective manufacturing process. It is restricted to brief slide travel and lacks control over the slide pull cycle. It is not advised for use on the upper slides.
Its limitations are that it can only be used for short-side action movements and that you can’t change how often the slide pulls. When designing the die casting mold, it is not recommended to design this type of slider on the top of the mold (a slider with a hydraulic cylinder is recommended in that case).
The hydraulic way of moving sliders lets you choose from different cycles, put slides on top of the die casting mold, and take the casting out of the die without any problems (like with the angle pin).
Rack and pinion, ejector lifter, and cam bars are some of the other ways to move things. Which motion to use varies depending on things like the number of parts being made, the size of the die, the length of the slide’s traveling distance, the size of the area being cored out, and the shape of the cast part.
When you have a project that needs a China die casting mold facotry. You can trust the die casting mold manufacturer to give you the best advice on core sliders. If you are not sure which design is best for your die casting project, feel free to contact us, as one of the top China die casting mold companies, we will offer you the best options according to your part design.
Die Casting Tooling Parting Line
The parting line is the border of the cavity and core on the casting that marks the separation area between the two halves (the fixing half and the moving half) of the die casting mold. This line determines which half is the fixing half and which is the ejection half of the die.
This line also affects any tolerances that must be maintained in this part of the casting. Below are examples of two types of parting line, Engineering and Design presents tolerancing criteria tailored to part properties at the die parting line.
On a casting drawing, it is not always clear where the parting line should be designed. In cases when the part designer indicates an unreasonable parting line, the die casting mold manufacturer must verify the designer’s purpose, welcome to die casting mold design page to know more about mold design for die casting.
For the casting to be made in accordance with the intended parameters, agreement on the ideal parting line location is crucial. When a part requires a cosmetic surface, the fixing half of the die is typically designed to provide that appearance surface, and the core side wil place ejector pings, inserts, and any engraving marks.
If the casting does not require an appearance surface, it can be changed to take advantage of the best casting situations. On cosmetic surface casting parts, the customer must explain this to the die casting mould manufacturer in advance so that the die casting tooling company can think about the location of the gate, overflows, and vents to ensure that there is no interference on the appearance surfaces or using secondary processes to meet the requirement.
Where cosmetic criteria exist and because regular, incremental die erosion is inherent in the die casting production process, the client will want to consider particular die maintenance measures to extend the die-casting mold’s ability to create casting components with the needed high-quality surface finish. Secondary operations on the mold cavity surface, such as polishing, should be negotiated in order to maintain cast part standards.
Figure 2 Step parting line “A,” have shut off parting line which is will make the die casting tooling more complex and not good result. The location of the parting line “B” will allow better casting fill and cleaner casting trim, offering longer die casting mold life and a less die casting mold manufacturing cost.
Ejector Pins
After the liquid metal alloy has been formed and the casting has been solidified in the die casting mold, ejector pins are used to push it out of the die. The ejector pins’ locati0n, quantity, and size are determined by the casting’s geometry design, size, and other specifications.
The die casting tooling supplier should design the ejector pins in the non function area of cating, and make sure that the cating can be demolded easily without any damge or crack. Die casting suppliers’s recommendations for ejector pin size, placement, and number are critical for successful casting part manufacture.
Each ejector pin has to be the right size and place for the casting in the die, and it will leave a small ejector mark on the surface of the casting. Because of this, they are not allowed to put the part’s appearance on the on the surface..
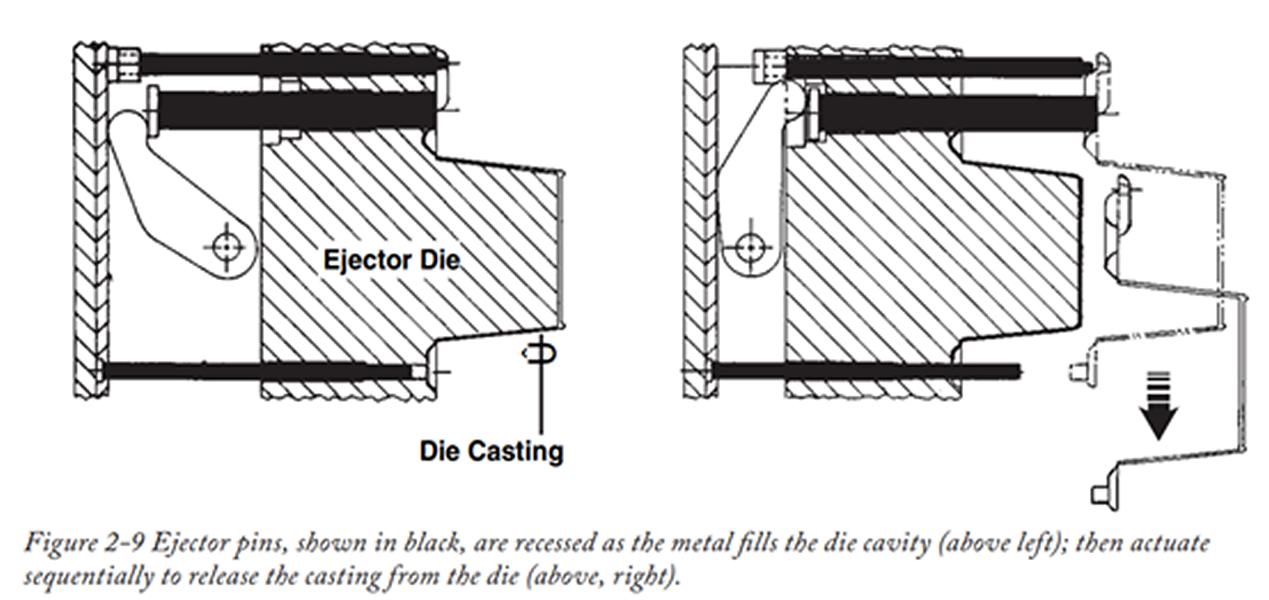
Cast-in Inserts
Each die casting tooling is different from others; an insert that is molded into the casting may be necessary to accommodate a bearing surface, internal thread, or other unique feature in certain castings. The die casting mold company can frequently satisfy this requirement as part of the standard casting process. This “insert molding” provides the benefit of securely embedding an insert into the casting, enabling it to be machined, pierced, and tapped. Nevertheless, this benefit is rarely sufficient to compensate for the additional expenses associated with the insert casting process.
The insert casting process will have The additional expenses are due to the longer casting process cycle time required to load the insert into the die casting mold, as well as the heating technique required to heat the inserts before placing them into the die half. But as long as this process works and solves your problem well, then it is worth it.
Guide pins
The alignment of the two die halves is guaranteed by guide pins and guide bushings (there are family components) that are located at the four corners of the die. Castings have critical dimensional alignment requirements for a feature in the stationary die half that is associated with a feature in the moving die half. This alignment is maintained by the guide bushings in one die half and the guide pins in the other. The guide pins may be designed in either die half.
When castings are removed from the die or the die is being sprayed with die release, the guide pins can become a snag hazard due to their protrusion from the parting line. Additionally, the guide pins operate at a high temperature and may pose a burn hazard.
In order to prevent the die from being incorrectly assembled, one of the four guide pins is typically offset. In certain exceptional circumstances, these pins may be rectangular in shape rather than round. We normally call this a mistake-proofing design.
Guide bushings
Round holes at the four corners of the die are called guide bushings, which are a family of guide pins. Guide pins are going through guide bushing when mold is closing and opening. Aligning the two die halves is the aim of the guide pins and guide bushings. If the die casting mold uses guide blocks, wear plates are used in place of bushings on two sides of the guide blocks.
Support pillars
Within the ejector box, columns are designed in the moving half mold base to produce a better casting part, through the ejector plates, to the machine plate or clamp plate. These round or square columns are situated in alignment with the die cavities and are intended to provide support for the mold base and withstand the force of injection.
The ejector system is located within the ejector chamber. This serves as one of the four critical die functions, which is to “enable the removal of the solidified metal.”
The ejector system is composed of ejector plates and pins as a minimum, and it may also include ejector guide pins and bushings and other sophisticated components to provide specialized ejection features.
Return pins
The ejector system is returned back to its “home” position using return pins before the next cycle. There are four return pins, which are designed on the ejector plate and extend to the parting line. The return pins do not have any force during the ejection stroke; rather, they travel along with the ejector pins. The return pins contact the fixing half-parting line and press the ejector plate back to the “home” position when the machine closes.
In some cases, the knockout rod (K.O.) is connected between the ejector plate and die casting machine so that the return pins become redundant and the ejector cylinder pulls the plate back to the home position prior to die casting mold closing. Return pins are still advised to ensure that the ejector plates are returned in the event of a failure, despite the redundancy.
When extended, return pins present both snag and fire hazards. In order to prevent snagging or contacting the return pins, the operator must be cognizant of their locations when reaching in to extract the shot.
Ejector plate
The heads of all ejector pins are fastened by the ejector plate and ejector retainer plate. As the ejector plate goes forward, it pulls on the pins, ejecting the casting out of the die. A machine motion pushes the ejector plate forward.
Ejector retainer plate
The bolted-on ejector plate holds the ejector pin heads in place. When the ejector system is put back into its “home” position, this plate is essential for keeping the ejector pins in place.
Guided ejection system
In some cases, ejector guide pings and guide bushings are added to the ejector plate and ejector retainer plate. This is similar to the parting line’s guide pins and bushings that used to guarantee that the ejector system functions uniformly and effortlessly.
Cooling lines
There should always have cooling channels in the cavity and core of dies; their function is to release heat from the molten metal to solidify casting.
The cooling channels may be configured to transport either oil or water as a cooling medium. cooling channels are equipped with specialized high-pressure and high-temperature hoses and connector fittings that must be kept in excellent repair. A fire hazard may arise as a consequence of a failure. In addition to the burn hazard, the fittings must be maintained to prevent leakage, and leaks should be promptly rectified due to the risk of a slip and fall.
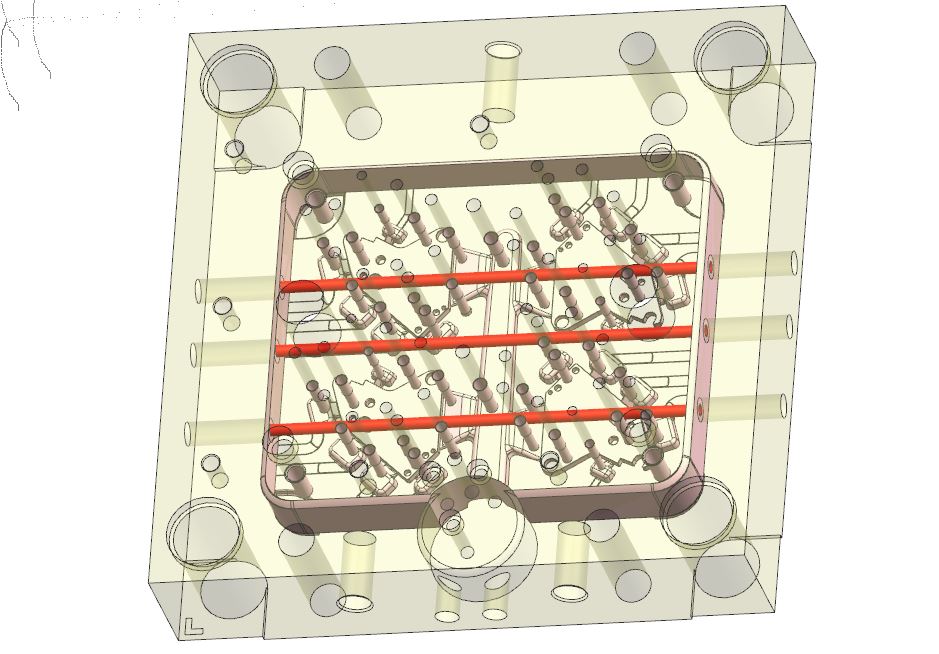
Biscuit block
Cold chamber die casting tooling typically includes a separate piece of AISI H-13 steel in the moving die half opposite the cold chamber. This block marks the start of the metal alloy distribution system (runner) for the casting cavities.
Sprue bushing
The sprue bushing serves an essential function in the hot chamber die casting mold as the interface between liquid alloy and solid alloy. At the confluence of the nozzle and sprue bushing, the metal in the nozzle must always stay liquid, while the metal in the sprue bushing must harden.
Sprue post.
The sprue post offers the same function as the biscuit block in the cold chamber die casting mold. For metal, the post is the first part of the system. For the die casting tool to work consistently, it is very important that the post is cooled properly.
Stop buttons (Travel limit column)
The stop buttons control how far the ejector plates can move forward and backward. The die ejector plates are pushed to the forward stop buttons by the ejection system during the ejection stroke. First, the ejection system or return pins push or pull the plate back to the rear stop. This gets the die ready for the next run.
Summary
There are many other small components in die casting mold, such as screws, slider cams, cavities, core pins, etc., but finally, we have summarized that die casting tooling contains five big parts, which are listed below:
- Mold base, including fixing half mold base and moving half mold base.
- Ejector system, ejecting the die casting part out from the mold cavity.
- Die cavities and cores, forming the casting features.
- Cooling systems, cool the cavity to solid the casting part.
- Feeding system, filling the die casting mold cavity.
By above information as you know making die casting mold is complex and costy, that is why we suggest you buy die cast tooling from China die casting mold factory, compare to Europe and America, working with a Chinese die casting tooling manufacturer will save you lots of time and cost.
Die Casting Mold Materials
When you plan to make die casting tooling, the tooling materials you use should be at least high quality, and preferably premium quality. These rules are based on the fact that die casting uses very high temperatures and pressures.
The grade of the tooling needed will depend on the part of the tooling that is being used, the alloy that is being die cast, how important the design of the cast part is, and how many casting parts will be made in the die casting tool. Before choosing tooling material, we normally ask the customer what the common quantity of parts required is.
Below are listed some die casting tooling materials:
Die Casting Mold and Cavity Materials
- Die Casting Molds for Zinc/Zamak Alloys: P-20, H13, DIN 1.2343, or other same-grade steel. Zinc alloys, which are cast at the lowest temperature in the nonferrous family, wear the least on their tooling, allowing the use of low-grade steel, such as P-20, in cases where part designs are relatively simple. Purchasers are cautioned; however, if the quantity requirement is very high (more than 100K), to avoid investing in new die casting tooling costs, high-grade steel should be used, such as H13.
- Die Casting Molds for Aluminum, Magnesium, and ZA Alloys: As previously mentioned, high-quality tool steel is necessary for die casting molds that are made of aluminum, magnesium, or ZA alloys. However, premium-grade tooling will always be the most prudent investment if part designs have highly critical features or if high production runs are being considered. In that case, H13, DIN1.2344, and DIN 1.2343 will be better options.
- Die Casting Molds for Brass Alloys: Copper alloy die castings are cast at the highest temperatures of the non-ferrous alloys; in that case, H13, 8407, and 1.2343 high-grade tool steel is a preferable option for brass die casting tooling.
High-quality steel will have an original metal certificate; this is provided by quality tooling material suppliers. There are some high-quality brands of steel for die casting tooling, such as LKM, ASSAB, FINKL, DAIDO, etc.
Die Cavity Insert Materials
The steel for the cavity insert is normally the same as the mold cavity, but for some small inserts or shut-off areas, it may need some special steel and have a 3-5-degree difference between the cavity and core. This will protect the cavity in case any crack or burn issue happens in the shut-off area.
Die Steel Heat Treatment
The quality of the heat treatment of the die steel is a critical step in the die casting tool manufacturing process. The use of high-quality rapid quenching heat treatment procedures is critical for normal die casting tool life. The heat treatment procedure must be carefully balanced to avoid distortion while maintaining the metallurgical properties that result from rapid quenching.
The professional heat treatment supplier should take care of this process. To ensure the quality of the heat treatment, a heat treatment report should also be provided. This is similar to the tool steel certificate; below is the heat treatment certificate.
Summarize for the mold steel
Die-steel materials are available in a variety of chemical compositions and mechanical properties. High-speed machining and wire EDM advancements have resulted in the utilization of a diverse array of tool steels, which are selected based on the complexity of the cavity and the material’s position in relation to the gate’s locati0n.
Specialty tool steels possess unique characteristics; however, when implemented correctly, they can extend the lifespan of die casting tools. It is advisable to consult with the die casting tooling manufacturer to determine the potential options for a specific casting design, as the increase in die life that can be achieved more than offsets this increased cost.
Controlling Die-Casting mold Performance
Porosity Control: Gating, Venting, and Vacuum
While high strength and integrity are expected from die castings, some product needs may necessitate extra procedures in the component design, die casting mold design, and online production phases. Porosity-conscious designers will be aware of strategies like removing thick wall sections from their designs. For broad guidelines, see Product Design for Die Casting. Before setting design parameters for a particular design, the engineer should always consult with a professional die casting supplier.
Given the final component design, the die caster will adhere to specified die design guidelines, including die gating, overflow, and venting slots, to appropriately remove air from the die cavity and minimize porosity to an acceptable level. Where pressure tightness is not a casting criterion, the process can be designed so that residual porosity only enters the casting’s non-functional internal portions. Porosity is tolerated in non-critical environments.
While not a replacement for appropriate product and die design, a vacuum system can help to optimize die fill, reduce gas porosity, and improve mechanical characteristics. A vacuum system is intended to expel ambient air from the die cavity during casting, resulting in negative pressure or a vacuum. The die casting mold must be particularly manufactured to accept a vacuum system; therefore, conversations about acceptable porosity levels should take place long before die casting tool design.
Thermal Balancing
The die casting tooling must operate at a specific, predetermined temperature in order to produce products of the highest quality. The size of the casting, the quantity of die cavities, the alloy being cast, and the machine cycle duration are some of the variables that will affect this temperature.
At this good temperature, the alloy is injected into the die cavity at a fast speed and quickly cooled to allow for ejection. The internal die casting mold cooling lines must be balanced in order to achieve this rapid and repeated cooling.
Properly balancing mold temperature through better cooling lines reduces die casting cycle time, improves casting quality, and lengthens the die casting tooling life.
Different sections of the die casting tooling can be heated or cooled to different temperatures; for example, the cavity and core will sometimes have different mold temperatures.
Oil Heating Lines
The use of hot oil channels in die casting tooling can sometimes be used to achieve differential heating of various sections of the mold in order to provide specific casting design elements. Hot oil systems heat a particular oil to a predetermined temperature before routing it through the die in the same way that water cooling lines do. Both water cooling and hot oil heating lines can be used.
Extended Die casting molds Life
Although high-quality tool steel is the first factor in optimum die casting tooling lifetime, there are a number of proprietary techniques that can be employed to increase a die casting tool’s lifespan. These procedures include chemically treating the mold, immersing it in specialized baths, and using shot-peening techniques.
When it comes to a particular casting part design, the die casting manufacturer might talk about the expected efficacy of such measures to prevent early die casting mold wear. Thermal fatigue cracking or heat checking is a common die failure mode. In that case, a DFM (Design for Manufacturing) report should be carried out before starting to manufacture the die casting tooling.
Crack Checking.
After some time in use (normally starting from 70K to 10K shots), die casting tools get small cracks and bigger cracks in some of the cavity areas. Both are important for the life of die-casting tools.
Below is a similar crack that happened to the die-casting mold. Check the cavity and casting part surface more carefully, and you will find if there are small or big cracks. Die casting mould companies should always keep an eye on part quality during casting production.
Secondary Machining Preplanning
Most die castings are made to be “almost ready to use,” and many die casting parts can be used directly as end products. The repeatability of the process and the close tolerances made possible by die casting make die casting parts suitable for cost-effective secondary machining operations.
By adding locating holes or a flush locating datum surface, a die casting can be made to precisely fit machining equipment. Die castings can be subjected to almost any kind of machining operation, including drilling, tapping, reamering, punching, and more.
The die casting company can perform machining operations such as measuring and other secondary processes as needed. Properly designing the part and die casting tool for optimum quality and economy in secondary machining will significantly reduce final casting part prices.
When you have a die casting project that requires tight tolerance, surface finish, and other special requirements, you need to discuss this with your die casting supplier in advance. If you have any questions, feel free to contact us.
Measuring Considerations
What gages will be used in die casting production and secondary machining, and what are critical components of the die casting program?
Gages can be used to inspect the casting in its as-cast state and again after machining.
The gage could be an attribute gauge, which is essentially a “go” or “no-go” check that returns either a good or bad part. A variable gage can also be used with a computer to document variables, collect data, and record CPKs. To check a casting, more than one gage may be required: one to check it in its as-cast condition, and another to check it fully machined.
Plug and thread gages may be required, as well as finished gages or standards for painted surfaces. The customer should consider gaging as part of their tooling package. Gaging requirements should be resolved as soon as possible by both the customer’s and die caster’s quality assurance managers to ensure that the part print requirements are met.
Inherited Tooling
Die casting mold transfer from one die casting mold to another may happen in your company, and this may cause some operational questions for the new die casting manufacturer. For example, the die casting molding needs to be put in a different type of die casting machine, and they may need to change the shot sleeve size or ejector system to suit their die casting machine.
In some instances, a customer may transfer a die casting mold from one die casting supplier to another. This generally will raise some operational questions for the new die casting manufacturer of which the customer should be aware. The die may need to be put into a different type of die-casting machine. This may require some modifications to the die’s ejector system as well as to the shot sleeve.
In that case, the die casting tooling must be reviewed by both the customer and the new die casting supplier to ensure that there are no visible issues with it. They should also check to see if the die casting mold has any appropriate limit switches and hydraulic cylinders. Following this analysis, an adaptation cost can be determined and agreed upon before the new die casting supplier invests a significant amount of time and money in preproduction.
Database Guidelines
When databases are used, casting quotations are frequently based on the premise that any CAD databases provided to build tooling and make components are comprehensive, functional, and do not require updates.
Databases can be considered incomplete and unusable if:
- The geometry of the cast part is not physically moldable.
- The draft angle and radius are not applied in the casting drawing.
- Line and surface geometry are not connected within 0.001”.
- The parting line is not clearly designed.
The database file format is important when you make your die casting tooling. STL files are typically used for the development of prototype parts. Stp or IGs format files are mostly working for all die casting manufacturers; we suggest you send those data to your supplier for a quote.
A 2D drawing is required to have a tight tolerance, secondary machine, and surface finish. 3D drawing is used for die casting tooling, but 2D drawing is used for quality casting production.
Die Casting Tooling Life
Die casting manufacturers are frequently asked, “How many shots the die casting tooling will last before making a new one?” or “How many shots will you guarantee the die casting tooling for?” A better question might be, “What can we do to maximize die casting tool life and how can we minimize replacement costs?” Aluminum and copper die casting molds wear out more quickly than zinc die casting molds due to the aggressive nature and high melting temperatures of the materials being die cast.
Part geometry, design, and shape also affect the die casting lifespan. In general, aluminum die casting tooling can run 50–70 thousand shots and may start to crack, while zinc die casting tooling can last 100 thousand shots, but this is not always the same result; some of them may be less and some of them may be more. There are many factors that affect the tool’s life. If you still have questions, then you are welcome to contact us.
GC Precision Mould is one of top 10 China die casting mold manufacturers, we can offer you high quality die casting mold with long life time more than 100 thousand shots, if you are looking for Chinese die casting mold company, we will be one of your best partner.
RFQ
1. What type of material should be used for die casting mold bases and cavity inserts?
An: For mold base, you can use S50C, 1.2311; for cavity and core, H13, 1.2344, and 8407 will be better options.
2. What is the proper heat treatment degree and procedure for die casting mold cavities?
An: For die casting mold cavities and cores, HRC48–52 degrees, and need to check the heat treatment report for quality control.
3. What is the difference between a prototype die casting mold and rapid die casting tooling?
An: Prototype die casting tooling is normally one-time tooling (1–10 pieces), while rapid die casting tooling is small quantity tooling (100–1000 pieces).
4. Why is trim die casting tooling used?
An: Trimming die casting tooling is used to trim the runner of the die casting part.
5. What should we send to the supplier to make high-quality die casting tooling and casting parts?
An: STP or IGS format file should be sent to the die casting manufacturer for die manufacture, and a 2D drawing should be sent for casting production. You need to specify if you have any tight tolerance, secondary machining, or surface finish.
6. where is the best place to buy die casting molds and proudcts.
An: to save your cost, we suggest you find a China die casting mold company to make your die casting molds and products.
7. How long does take to make a die casting mold?
An: Thise is mostly depending on the part size and the part geometry, normally the lead time for die casting mold manufacturing will be 5-10 weeks, and molstly Chinese die casting mold company will be able to make short lead time than other country. Send us your die casting project and we will inform you the detail lead time for your die casting mold.
Leave a Reply
You must be logged in to post a comment.